マシニング加工とは?精密加工の中核を担う技術について
今年は124年ぶりに2月2日が節分だったそうですね!ちなみに暦の関係でしばらくは4年ごとに2月2日が節分になるそうです。
さて、本日はマシニング加工について、記事を書いていきたいと思います!
製造業に携わっている方であれば当たり前のことかもしれないですが、お付き合いください♪
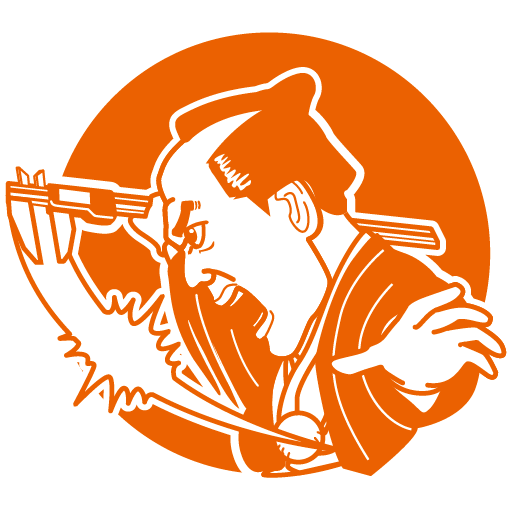
マシニング加工とは
マシニングセンタの基本構造
マシニング加工は、フライス盤をベースに発展した高機能工作機械「マシニングセンタ」を使って行う切削加工です。
マシニングセンタは、自動工具交換装置(ATC)や数値制御装置(NC)を備えており、多工程の加工を1台で連続的にこなせるのが特徴です。
主な構成要素としては、主軸、テーブル、工具マガジン、ATC、制御装置が挙げられます。
主軸は高速回転し、エンドミルやドリルなどの工具を回転させてワーク(加工対象)を削ります。
テーブルはXYZの3軸方向に動き、ワークを的確に移動させることで高精度な加工が可能になります。
また、近年では4軸・5軸といった多軸制御も一般的になっており、複雑な立体形状も一度の段取りで加工できるようになりました。
工具の自動交換により、生産性が飛躍的に向上し、省人化・無人化にも大きく貢献しています。
NC加工との違いと関係性
マシニング加工とよく混同される言葉に「NC加工」があります。
NC加工とは「Numerical Control(数値制御)」によって機械の動きを制御する加工全般を指し、旋盤やフライス盤などにNC装置がついていればそれもNC加工となります。
一方、マシニング加工は、NC装置を備えたフライス加工機で行う高度な切削加工を指し、特に「マシニングセンタ」を使うケースが一般的です。
つまり、マシニング加工はNC加工の一種でありながら、より高機能で自動化された装置を使う点で、NC旋盤などとは区別されます。
NC加工はプログラム制御で高精度な繰り返し作業が可能ですが、マシニングセンタはさらに複雑な加工や自動工具交換が可能で、生産ラインの中でも重要なポジションを担っています。
マシニングセンタの種類
立形マシニングセンタ(VMC:Vertical Machining Center)
主軸が垂直方向に取り付けられているタイプで、最も一般的に使用されています。
ワークをテーブルに固定し、上から工具で加工する構造のため、操作性が良く、見た目でも加工状況が確認しやすいというメリットがあります。
主に平面加工や形状加工、穴あけなどに使われ、機械構造が比較的コンパクトで、設備導入のハードルが低いのも魅力です。
少量多品種の加工や、比較的軽量なワークに適しています。
横形マシニングセンタ(HMC:Horizontal Machining Center)
主軸が水平方向に配置されたタイプで、重力を利用して切粉(チップ)を自然に排出できる構造になっています。
ワークの側面や深い穴の加工に適しており、テーブルが回転(B軸)することで複数面の加工を一度に行えるメリットもあります。
また、パレットチェンジャーと組み合わせることで、無人化・連続加工に優れた運用が可能です。
自動車や重機などの量産部品加工に多く採用されています。
5軸マシニングセンタ
従来のXYZの3軸に加え、工具やテーブルが回転する2軸(A軸・B軸)を持つタイプです。
複雑形状や多面加工、深いアンダーカットの加工など、3軸では対応できない領域にも対応できるのが最大の強みです。
航空宇宙部品、医療機器、金型など、高い精度と加工自由度が求められる分野で活躍しています。
プログラム作成が高度であり、装置価格も高価なため、導入には専門知識と投資が必要ですが、1回の段取りで多面加工が可能な点は大きな魅力です。
これらのマシニングセンタを使い分けることで、製品形状や生産ロット、加工精度のニーズに応じた最適な生産が可能になります。
近年では、立形と5軸のハイブリッド機や、コンパクトな卓上5軸機なども登場しており、選択肢はますます広がっています。
門型マシニングセンタ
門型マシニングセンタは、その名の通り「門(ゲート)」のような構造をした大型の工作機械です。
通常、主軸が門の中央にぶら下がっており、ワークテーブルの上を主軸が前後左右、上下に移動することで加工を行います。
構造が大きく剛性も高いため、非常に大きなワークや重たい部品の加工に適しており、特に金型加工や大型機械のベース部品の製作によく使われます。
このタイプの大きなメリットは、広い加工エリアと高い加工剛性にあります。
一度に大きなプレートを複数面加工したり、深い溝や穴を正確に加工できる点から、精密性とパワーの両立が求められる業種には非常に重宝されます。
ただし、設備が非常に大きいため、設置スペースの確保や床の耐荷重、搬入の手間なども考慮する必要があります。
また、導入コストも高額な部類に入るため、主に大手メーカーや金型専門工場で採用されています。
ガントリタイプマシニングセンタ
ガントリタイプは、門型に似た構造ながら、より自由度が高く、さらに大型のワークに対応するために設計された機種です。
門型との違いは、ワークテーブルではなく「ガントリ(門構造)」自体が前後左右に動く点にあります。
これにより、超大型ワークを固定したまま、マシン側が動いて加工するスタイルとなり、航空機部品や鉄道車両、風力発電部品など、極めて大きな構造物の加工に最適です。
特にアルミ合金や複合材などの軽量・大型素材を扱う際に威力を発揮し、ワークを動かす必要がないため、寸法の狂いを最小限に抑えることができます。
高精度なガントリタイプは、スケールが大きいだけでなく、5軸加工や多主軸仕様などにも対応可能なものが増えており、超高精度・高剛性・高効率を兼ね備えた先端加工設備として注目されています。
マシニング加工の種類
フライス加工
フライス加工は、回転する工具(フライス)でワークの表面を削っていく加工方法です。
マシニング加工における基本であり、平面加工、溝加工、段差加工など多くの用途に使われます。
フライスにはエンドミル、フェイスミル、ラフィングミルなどさまざまな種類があり、加工内容や精度によって使い分けられます。
エンドミルは、特に複雑な形状を削るのに適しており、工具径や刃数、形状も多岐にわたります。
フェイスミルは広い面を一度に削るのに向いており、主に仕上げ面を平滑にする用途で使われます。
フライス加工では、切削条件の最適化が非常に重要であり、送り速度や回転数、切り込み量などを適切に設定することで、工具の寿命と加工品質が大きく変わります。
穴あけ・リーマ加工
穴あけ加工は、ドリルを使ってワークに穴をあける加工方法で、下穴を開けた後にさらに精密な内径仕上げを行うリーマ加工と組み合わせて使われることが多いです。
マシニングセンタでは、ドリルとリーマをATCで自動交換することができるため、一連の穴加工を連続して行うことが可能です。
リーマ加工はドリルで開けた穴の内径をさらに滑らかにし、寸法精度を高めるための加工です。
例えば、M6のボルト用の穴を開ける際には、下穴ドリルで5.0mmの穴を開けた後、リーマで6.0mmまで仕上げるといった工程が一般的です。
リーマ加工では特に同心度や真円度が重要となり、工具の精度だけでなく、機械の剛性や振動の少なさも重要な要素となります。
タッピング・ネジ切り加工
ネジ穴を作る工程として重要なのがタッピング加工です。
タップという専用工具を使い、穴の内側にネジ山を切っていきます。
マシニングセンタでは、下穴を開けた後に自動でタップを装着し、そのままネジ切り加工を行うことができます。
また、最近では「リジッドタッピング」という制御方式も主流となっており、主軸と送り軸の同期制御により、高速かつ高精度でのネジ切りが可能になっています。
タッピング加工では、タップの折損リスクを低減するために、切削油の使用や加工条件の最適化が求められます。
特に硬質材の場合には、成形タップや超硬タップなどの高性能工具を使用することが推奨されます。
マシニング加工のメリットとデメリット
高精度と量産性の両立
マシニング加工の最大のメリットは、高精度と量産性の両立が可能である点です。
CAD/CAMによって設計した形状をそのままNCプログラムとして読み込み、同一品質の製品を短時間で多数生産することができます。
機械精度が高く、繰り返し加工にもブレがないため、自動車部品や航空機部品など、高い品質が求められる分野に広く使われています。
また、自動工具交換機能やパレットチェンジャーによって無人化運転も可能となっており、夜間でも加工が進められる「夜間無人加工」は中小製造業にとって大きな武器となっています。
さらに、測定プローブを使えば、加工中に寸法チェックも自動で行えるため、品質管理の精度も向上します。
加工コストと設備投資の課題
一方で、マシニング加工には初期導入コストが高いという課題もあります。
マシニングセンタ本体だけで数百万円から数千万円、さらにCAD/CAMソフトや治具、工具などの周辺機器をそろえると、相当な投資が必要です。
また、NCプログラムの作成には専門知識が必要であり、熟練したオペレーターの育成にも時間とコストがかかります。
さらに、複雑な加工になればなるほど工具摩耗や工具破損のリスクも高まるため、定期的なメンテナンスと在庫管理が不可欠です。
特に少量多品種の生産では、段取り替えの頻度が増え、1ロットあたりのコストが高くなる可能性もあります。
そのため、マシニング加工を有効に活用するには、生産計画と工程設計の最適化が重要になります。
加工に使われる工具と素材
主な切削工具の種類
マシニング加工で使用される切削工具は非常に多岐にわたります。
代表的なものとしては、エンドミル、ボールエンドミル、ドリル、リーマ、タップなどがあり、それぞれ用途や加工対象によって最適な選択が必要です。
たとえば、エンドミルは平面や溝加工に適しており、ボールエンドミルは曲面や3D形状の加工に使われます。
工具は超硬合金や高速度鋼(HSS)で作られており、被削材や加工条件に応じてコーティング(TiAlN, DLCなど)を施したものも多く存在します。
最近では、工具メーカー各社が独自の形状や刃先処理を施した高性能工具を開発しており、工具選定の良し悪しが生産性に直結する時代となっています。
加工に適した金属素材
マシニング加工で扱われる素材も多種多様です。
アルミニウムは切削性が高く、軽量で精密部品に多く使われます。
鉄・炭素鋼は一般的で安価な素材ですが、加工硬化しやすいため条件設定に注意が必要です。
ステンレス鋼は耐食性が高い反面、粘性があり工具に負担がかかるため、高剛性な設備と工具が求められます。
また、チタン合金やインコネルなどの難削材も、航空・医療分野ではよく使用されますが、これらは加工熱が高く工具摩耗が激しいため、切削条件の最適化やクーラントの工夫が欠かせません。
素材の特性を十分に理解し、それに合わせた工具と条件を選ぶことで、より高精度かつ安定した加工が可能になります。
今後の展望と最新技術
5軸加工やハイブリッド加工
近年、マシニング加工の進化として注目されているのが「5軸加工」です。
従来の3軸に加え、回転軸(A軸、B軸)を加えることで、より自由度の高い加工が可能となります。
これにより、複雑な曲面やアンダーカットなど、通常では難しい形状も一度の段取りで加工でき、生産効率と精度が飛躍的に向上します。
さらに、切削と積層造形(3Dプリンティング)を組み合わせた「ハイブリッド加工機」も登場しており、加工の幅がますます広がっています。
例えば、金属粉末を溶融・積層した後、同一機内で切削加工を行うことで、高精度な最終製品が得られます。
これにより、試作や部品の補修にも大きな可能性が生まれています。
AI・IoTとの連携によるスマート工場
マシニング加工の現場にも、IoTやAI技術の波が押し寄せています。
加工機の稼働状況や工具寿命、振動・温度といったデータをリアルタイムで収集・分析し、予防保全や加工品質の向上に役立てる「スマートファクトリー化」が進行中です。
AIは、加工条件の最適化や異常検知にも使われており、従来なら熟練者に頼っていた判断も自動化が可能になりつつあります。
これにより、少人数でも高効率な生産が可能になり、人手不足の解消にも貢献しています。
今後はクラウドとの連携により、遠隔地からでも工場の状態を把握・制御できるようになり、グローバルな製造業の形も大きく変わっていくことでしょう。
マシニング形状の加工の見積り依頼ならアスクへ
試作品や小ロットの加工も大歓迎!
特に手のひらサイズの部品製作を得意としています。
アスクなら、試作品のお見積もりが最短1時間で可能!!
お気軽にお問い合わせください。
所有設備:5軸加工機・立型マシニングセンタ・CNCフライス盤・立型汎用フライス盤
対応可能サイズ:□10mm~□400mm ※横手最大1,000mm可能
対応数量:単品から小ロットが得意です。
対応材質:鉄、SUS、アルミ、銅、真ちゅうなどの一般的な金属から、チタン、インコネル、など一部の難削材、樹脂などもお任せください。※詳しくはお問い合わせください
試作全国対応!
簡単・最短1時間お見積り
他、ブログ記事もご覧ください♪
動画の投稿もしておりますので良ければご覧ください♪