めっき処理とは!?その目的や種類などについて徹底解説します!
製造業におけるめっき処理とは、製品を加工した後に様々な特性を付与することができる、とても重要な表面処理方法の一種といえます。
そんなめっき処理について目的や種類についてご紹介します♪
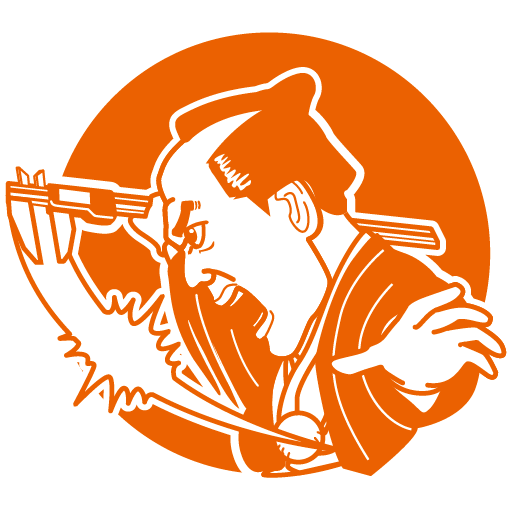
めっき処理とは
メッキ処理とは、金属やプラスチックなどの素材表面に、薄い金属の被膜を形成する表面処理技術です。
この処理は主に「防錆」「装飾」「導電性付加」「耐摩耗性向上」などの目的で行われ、古くから工業製品に広く用いられてきました。
特に金属部品においては、基材の性能だけでは補いきれない機能を被膜によって補完するという役割を担っています。
メッキ処理には、電気の力で金属を析出させる「電気メッキ」、化学反応により自発的に金属を析出させる「無電解メッキ」、金属を高温で溶かしてコーティングする「溶融メッキ」など、さまざまな種類があります。
それぞれに得意とする分野があり、対象物の材質や使用環境に応じて使い分けられています。
例えば、ニッケルメッキは防錆性と装飾性に優れ、日用品から工業部品まで幅広く使用されます。
クロムメッキは高い硬度と耐摩耗性を持ち、自動車部品や機械部品に多用されます。
また、電子部品では金メッキが導電性や耐酸化性の観点から重宝されています。
メッキの歴史は古く、紀元前から金や銀の装飾メッキが行われていた記録があります。
近代的なメッキ処理は19世紀に電気メッキ技術が確立されたことで発展し、20世紀には自動車、航空機、電子機器などの分野に広がりました。
21世紀に入ってからは、環境規制への対応やナノテクノロジーを活用した高機能メッキなど、技術革新が加速しています。
メッキ処理は一見、単純な「表面のコーティング」のように見えますが、その裏には高度な材料工学と化学の知識が求められます。
素材の選定から、被膜の厚さや均一性の管理、下地処理、環境への配慮まで、非常に奥深い技術分野といえるでしょう。
現代の製造業において、メッキは品質・信頼性の基盤を支える重要な工程の一つとなっています。
メッキ処理の工程フロー
メッキ処理は、単に金属をコーティングするだけの工程ではありません。
被膜の品質や密着性、外観などを左右するため、前処理から後処理まで一連の厳密な工程管理が求められます。
ここでは、一般的な電気メッキ処理の工程フローを中心に、その概要を解説します。
① 脱脂・洗浄
まず最初に行うのが、素材表面の油分や汚れの除去です。
これは脱脂剤(アルカリ系洗浄剤など)を用いて行われます。
素材の表面に油やホコリが残っていると、メッキが均一に付着せず、はがれやムラの原因となるため、非常に重要な工程です。
脱脂後には純水や水道水による十分なすすぎが行われます。
② 酸洗い(スケール除去)
続いて、金属表面の酸化皮膜やサビを除去する「酸洗い(ピクルス処理)」を行います。
通常は希硫酸や塩酸を使用し、酸化物を溶解させて素地金属を露出させます。
これにより、メッキの密着性が高まります。
素材や用途に応じて薬品の種類や濃度、処理時間が調整されます。
③ 活性化処理
酸洗い後、一部の金属(特に不動態皮膜を形成するステンレスやアルミなど)では、メッキが付着しにくい状態になります。
そこで、表面を一時的に活性化させる処理(例えばフッ化物処理や電解脱脂)が施され、メッキの乗りを良くします。
④ メッキ処理
前処理を経て、いよいよ本格的なメッキ処理に入ります。
処理液に対象物を浸漬し、電気を流して金属イオンを基材表面に還元させて被膜を形成します。
メッキ液の種類、電流密度、温度、時間などは目的や素材によって最適化されます。
自動メッキラインではこれらの工程が自動で制御されています。
⑤ 水洗
メッキ直後には、処理液に含まれる薬品を洗い流すために水洗を行います。
水洗が不十分だと、次の工程で化学反応が起きたり、被膜表面にシミや腐食を招く恐れがあるため、複数回の水洗を行う場合もあります。
⑥ 後処理(パッシベーション・乾燥など)
最後に、必要に応じて後処理が施されます。
たとえば、亜鉛メッキではクロメート処理(パッシベーション)を施し、白サビ(酸化亜鉛)の発生を抑えます。
また、ニッケルや銅などのメッキでは乾燥炉での乾燥処理が行われることもあります。
装飾メッキでは、光沢剤の使用やバフ研磨による仕上げ処理も含まれることがあります。
このように、メッキ処理は多段階の工程で構成されており、どのステップも品質に直結します。
特に、前処理の出来栄えが最終的な被膜品質に大きな影響を与えるため、熟練した作業管理が欠かせません。
メッキの主な種類と特徴
メッキ処理にはさまざまな種類があり、それぞれの方式や使用される金属によって目的や特性が大きく異なります。
ここでは代表的なメッキの種類とその特徴について解説します。
まず最も一般的な「電気メッキ」は、電解液中で金属イオンを電気の力で還元させて、対象物の表面に金属被膜を形成する方法です。
この方式は被膜の厚さを比較的コントロールしやすく、ニッケル、クロム、銅、金、銀などさまざまな金属に適用されます。
用途としては、装飾性、耐食性、導電性、耐摩耗性などの機能が求められる分野に広く使われています。
たとえば、自動車部品に施されるクロムメッキは、美観と耐久性を両立させる代表的な例です。
次に、「無電解メッキ」は、電気を使わず化学的な還元反応により金属イオンを基材表面に析出させる技術です。
電気を必要としないため、形状が複雑な部品や非導電性素材(例:プラスチック)にも均一なメッキが可能です。
代表的なものに「無電解ニッケルメッキ」があり、耐摩耗性や耐食性に優れているため、電子部品や精密機械部品に多く採用されています。
さらに、「溶融メッキ(ホットディップメッキ)」は、金属を高温で溶かした状態で基材を浸漬する方法です。
特に「溶融亜鉛メッキ」は、鋼材の耐食性を大幅に向上させることから、橋梁、建築構造物、電柱などの屋外環境で使用される構造材に多用されます。
この方法は比較的分厚い被膜を形成できる点も特徴です。
また、「真空蒸着メッキ」や「イオンプレーティング」など、真空中で行う物理的な蒸着法やプラズマ技術を用いたメッキもあります。
これらは半導体や光学機器など、高精度・高機能が要求される分野で使用されます。
メッキに使われる金属ごとの特徴も重要です。
たとえば、「ニッケル」は防錆性・耐摩耗性・はんだ付け性に優れており、さまざまな基礎メッキとして使われます。
「金」は高い導電性と耐酸化性を持ち、電子部品や高級装飾品で用いられます。
「銀」も導電性が高く、電気接点などに使用されますが、硫化による変色には注意が必要です。
このように、メッキは処理方法と使用する金属の選定によって、その性能や用途が大きく異なります。
製品の目的や使用環境に応じて、最適なメッキを選択することが重要です。
メッキの種類と用途別解説
電気メッキの原理と特徴
電気メッキ(Electroplating)は、最も広く利用されているメッキ処理方法のひとつです。
電解質中に浸した被処理物(製品)に電流を流し、金属イオンを電極表面に還元・析出させることで、金属の薄膜を形成する技術です。
このプロセスは電気分解の原理を応用しており、制御性が高く、さまざまな用途に応じた被膜形成が可能です。
電気メッキでは、主に以下の構成要素が使用されます。
・陽極(プラス極):一般的にはメッキする金属自体が使われます(例:ニッケルメッキではニッケル陽極)。
・陰極(マイナス極):被メッキ物、つまり製品本体です。
・電解液:メッキ対象となる金属の塩(例:硫酸ニッケル)を含んだ溶液で、イオン状態の金属を供給します。
通電を開始すると、陽極から金属イオンが溶け出し、陰極の表面で還元されて金属として析出します。
つまり、電解液内を通る電流によって、金属が陰極(製品)に移動してコーティングされるという仕組みです。
陽極が溶解型(供給型)でない場合、外部から金属イオンを供給する補充管理が必要になります。
電気メッキの最大の特徴は、「膜厚や性質を精密にコントロールできる点」にあります。
電流密度、処理時間、電解液の成分や温度、pHなどを調整することで、厚さ数ミクロンから数十ミクロンの被膜を均一に形成することが可能です。
さらに、光沢の有無や硬度、導電性、防錆性など、必要な機能性に合わせたカスタマイズもできます。
用途も極めて多岐にわたります。
たとえば、電子部品に使われる金メッキや銀メッキは、優れた導電性と接触抵抗の低減を実現します。
また、自動車や家電の装飾パーツではクロムメッキが高級感と耐久性を与えています。
工業部品向けには、耐摩耗性・耐食性の向上を目的としたニッケルや亜鉛メッキなどが採用されています。
ただし、電気メッキは製品が導電性素材であることが前提であり、プラスチックやセラミックスなど非導電性材料への直接メッキはできません(※ただし下地導電処理を施すことで対応可能)。
また、形状が複雑な製品では、電流分布のムラによって膜厚が不均一になりやすく、治具の工夫や整流補助剤の使用が求められます。
電気メッキは高い自由度と大量生産性を両立した表面処理技術であり、あらゆる工業製品において不可欠な存在です。
近年では、環境負荷の低い薬品の開発や、排水処理技術の向上など、持続可能な電気メッキ技術の実現も進んでいます。
無電解メッキの仕組みと利点
無電解メッキ(Electroless Plating)は、電気を一切使用せず、化学反応によって金属被膜を形成するメッキ技術です。
電気メッキとは異なり、外部からの電力供給を必要とせず、還元剤を用いて金属イオンを被処理物の表面に還元・析出させます。
主にニッケルや銅のメッキで用いられ、電子部品や複雑形状部品、非導電性材料への処理に活躍しています。
無電解メッキの原理
無電解メッキは、メッキ液中に含まれる金属イオンと還元剤が、触媒作用を受けて被処理物の表面で化学反応を起こし、金属を析出させる仕組みです。
たとえば、無電解ニッケルメッキでは、次のような反応が起きます。
Ni²⁺ + 還元剤(ホルムアルデヒドなど) → Ni(金属) + 副生成物
この反応は、被処理物の表面が触媒活性を持っている場合にのみ進行します。
そのため、非導電性素材(プラスチックなど)に無電解メッキを施す場合は、事前にパラジウムなどの触媒処理(アクティベーション)が必要です。 主な利点
1.均一な被膜形成が可能
無電解メッキの大きな特長のひとつは、形状にかかわらず均一な膜厚が得られることです。
電気メッキでは電流分布の影響でエッジやコーナー部に膜厚ムラが生じやすいのに対し、無電解メッキでは溶液の拡散と反応だけで被膜が形成されるため、複雑形状部品や内径、穴の内部にも安定した被膜が得られます。
2.非導電性材料へのメッキが可能
プラスチックやセラミックなど、電気を通さない素材にもメッキが可能です。
これは、電子部品の樹脂筐体や3Dプリント部品の導電性付与、装飾用途で非常に有効です。
3.優れた耐食性・硬度
特に無電解ニッケルメッキは、リンやホウ素などを含む合金被膜を形成することで、高硬度・高耐食性を実現します。
化学装置や航空機部品など、過酷な環境下での使用にも適しています。
さらに、熱処理を施すことで表面硬度をさらに高めることも可能です。
4.電力不要な省エネプロセス
電気を使わないため、電力設備が不要であり、省エネ・設備簡素化が可能です。
バッチ式処理にも向いており、小ロットや試作など柔軟な生産対応も可能です。
注意点・課題
無電解メッキにはいくつかの課題も存在します。
まず、メッキ液の管理が非常に繊細で、金属イオン濃度や還元剤のバランス、温度・pHなどの管理が不適切だと被膜品質が劣化します。
また、薬品コストが比較的高く、液の寿命が短いため、廃液処理にも注意が必要です。
その他のメッキ方法(溶融、真空など)
電気メッキや無電解メッキ以外にも、目的や材料に応じてさまざまなメッキ方法が存在します。
ここでは、特に工業用途で注目される「溶融メッキ」「真空メッキ」「乾式メッキ」などの代表的な方式について、その概要と特徴を解説します。
溶融メッキ(溶融亜鉛メッキなど)
溶融メッキ(Hot-Dip Galvanizing)は、金属を高温で溶融させた浴の中に被処理物を浸漬することで、表面に金属層を形成する方法です。
最も一般的なのが「溶融亜鉛メッキ」で、鉄鋼部品に耐食性を持たせるために広く使用されます。
処理工程は以下の通りです。
・被処理物の脱脂・酸洗い
・フラックス処理による酸化防止
・溶融亜鉛浴(約450℃)への浸漬
・冷却・仕上げ
この方式では、被膜の厚さが電気メッキよりも厚く、耐食性に優れるため、屋外構造物(ガードレール、鉄塔、ボルトなど)に多用されます。
一方で、膜厚が大きいため、寸法精度が要求される精密部品には不向きな場合があります。
真空メッキ(PVD、CVD)
真空メッキは、真空環境下で金属や化合物を蒸着・堆積させる技術です。
代表的なものには以下の2方式があります。
・PVD(物理蒸着):金属を蒸発・スパッタリングなどで原子レベルにして対象物に付着させる。
・CVD(化学蒸着):気体反応によって対象表面に薄膜を形成する。
真空メッキは極めて薄く高密度な被膜を形成できるため、半導体部品、光学部品、工具コーティングなどに活用されています。
たとえば、チタンやクロムを使ったPVD処理は、装飾性・耐摩耗性・耐熱性に優れ、切削工具や金型の寿命を延ばします。
また、真空メッキは環境負荷が少なく、六価クロムなど有害物質を使わない点でも注目されています。
その他の乾式メッキ法
乾式メッキには他にも以下のような方法があります。
・イオンプレーティング:PVDの一種で、金属蒸気に高電圧をかけてイオン化し、被処理物に強く密着させる方式。密着性と耐久性に優れる。
・アーク放電メッキ:真空中でアーク放電を用いて金属を蒸発させ、被膜を形成する。高硬度被膜に用いられる。
比較と適用選定のポイント
メッキ方法 | 被膜特性 | 適用例 |
---|---|---|
溶融メッキ | 厚膜・高耐食性 | 建材、配管、鉄鋼構造物など |
真空メッキ(PVD) | 高密着・高硬度 | 切削工具、装飾部品、半導体部品 |
CVD | 耐熱性・化学安定性 | 電子部品、セラミックコート |
これらのメッキ技術は、用途やコスト、精度、環境負荷などの観点から適切に選定される必要があります。
特に真空系技術は、今後の高性能・高機能材料加工において重要な選択肢となっています。
メッキの材料別分類と特性
ニッケルメッキの特徴と用途
ニッケルメッキは、工業分野から日用品、電子機器に至るまで幅広く使用されている代表的なメッキのひとつです。
耐食性、耐摩耗性、光沢性などに優れており、機能性と装飾性の両面で高く評価されています。
また、電気メッキと無電解メッキの両方式で広く利用され、用途や目的に応じた被膜設計が可能です。
ニッケルメッキの主な種類
ニッケルメッキには大きく分けて以下の種類があります。
・電気ニッケルメッキ:電流を使ってニッケルを析出させる方式で、光沢ニッケルや半光沢ニッケルなどに分類されます。
・無電解ニッケルメッキ:化学反応によって均一に析出させる方式で、リン含有率の違いによって高リン・中リン・低リンタイプに分かれます。
これらはそれぞれに特徴があり、例えば光沢ニッケルは装飾性に優れ、無電解ニッケルは複雑な形状でも均一な被膜を得られるため、精密部品や電子機器に適しています。
主な特長
1.優れた耐食性
ニッケルは自然環境中で酸化しにくく、鉄や銅などの母材を腐食から守ります。
特に無電解ニッケルメッキ(高リンタイプ)は、化学薬品や海水環境においても高い耐食性を発揮し、化学装置や海洋機器などに採用されています。
2.美しい光沢と均一性
光沢ニッケルメッキは、装飾用としての美しい外観を持つため、自動車部品、バス金具、家具金物などに多用されます。
また、表面の均一性が高く、下地としてクロムメッキを施す前処理層としても使用されます。
3.高硬度・耐摩耗性
ニッケルは硬度が高く、耐摩耗性にも優れます。
特に無電解ニッケルメッキは、熱処理を加えることで表面硬度を大幅に向上させることができ、金型や機械部品、軸受けなどに用いられます。
4.はんだ付け性や磁性制御
電子部品においては、ニッケルメッキのはんだ付け性や磁性特性の調整が重要です。
例えばプリント基板のスルーホール部やIC端子には、Ni/Au(二層メッキ)が使われることが一般的です。
主な用途
分野 | 用途例 |
---|---|
自動車産業 | バンパー、グリル、ドアハンドル、エンブレムなど |
家電製品 | 洗濯機・冷蔵庫の部品、内装装飾部品 |
電子機器 | 端子、コネクタ、プリント基板、ハードディスク |
機械部品 | 軸、ギア、シリンダ、ピストン部など |
医療・精密機器 | 小型バルブ、センサー部品、試験機部品 |
ニッケルメッキは、機能性と装飾性を兼ね備えており、コストパフォーマンスにも優れているため、非常に汎用性の高いメッキです。
ただし、ニッケルに対してアレルギーを持つ人が一定数いることから、装身具や皮膚に触れる製品では注意が必要です。
クロムメッキの特徴と用途
クロムメッキは、金属表面にクロム(Cr)を被覆するメッキ処理で、装飾性と耐久性に非常に優れた仕上がりを提供します。
自動車や機械部品、工具など、あらゆる産業分野で広く使われており、光沢のある美しい外観とともに、耐摩耗性・耐食性・耐熱性を実現できることが最大の魅力です。
クロムメッキは大きく分けて「装飾クロムメッキ」と「硬質クロムメッキ」の2種類があります。
それぞれの特徴と用途を詳しく見ていきましょう。
装飾クロムメッキ
装飾クロムメッキは、下地としてニッケルメッキや銅メッキを施した上に、薄いクロム層(0.1〜0.3μm程度)を形成することで、鏡のような光沢と耐食性を実現します。
この処理は美観を目的としつつも、日常的な摩耗や腐食から保護する機能も兼ね備えています。
主な用途:
・自動車部品(ドアハンドル、グリル、バンパーなど)
・家電製品(水栓金具、調理器具)
・家具・装飾品(金物、取っ手、時計のフレームなど)
装飾クロムメッキの特徴は「見た目の美しさ」に加え、「耐久性」と「表面の滑らかさ」にもあります。
日常的に触れる製品において、表面の質感や光沢感はユーザーの満足度を高める要因となります。
硬質クロムメッキ
硬質クロムメッキ(インダストリアルクロム)は、厚さ数μm~数百μmに及ぶクロム層を形成し、極めて高い硬度と耐摩耗性を付与します。
Hv800〜1000にも達する硬さを持ち、さらに熱に強く、摩擦や腐食の厳しい環境でも性能を保ちます。
主な用途:
・金型、プレス金型、射出成形金型
・油圧シリンダー、ピストンロッド、軸受け
・ロール部品、計測機器、産業機械部品
また、硬質クロムは潤滑性もあり、接触部品間の摩擦係数を下げる効果があります。
例えば、繰り返し摺動する部品や高速回転する部品において、寿命の延長や性能安定に寄与します。
クロムメッキのメリット・注意点
メリット | 注意点 |
---|---|
高光沢で美しい外観 | 有害な六価クロムを使用(環境・健康問題) |
優れた耐摩耗性と耐食性 | メッキ浴の管理が高度でコストが高い場合も |
熱・摩擦・薬品に対する耐性が高い | 厚膜では割れやすい性質がある |
現在では環境規制の強化により、六価クロムを使用しない「三価クロムメッキ」や「代替皮膜処理」も開発されており、より安全で環境に配慮した処理方法への転換も進められています。
クロムメッキは、外観美と機能性を高いレベルで両立させたいときに最適な処理です。
特に摩耗・腐食への強さや、表面処理としての品位の高さが求められる場面において、他のメッキと比較しても非常に優れた選択肢となります。
亜鉛メッキの特徴と用途
亜鉛メッキは、主に鉄鋼材料の防錆処理として広く用いられている金属表面処理技術の一つです。
鉄や鋼の表面に亜鉛の被膜を形成することで、腐食から母材を保護し、製品の耐久性を大幅に向上させます。
建設資材、自動車部品、家電製品など、多様な分野で採用されており、コストパフォーマンスに優れるため産業界で非常に人気のあるメッキ処理です。
亜鉛メッキの主な方法
亜鉛メッキには主に「溶融亜鉛めっき」と「電気亜鉛めっき」の2種類があります。
溶融亜鉛めっき(ホットディップメッキ)
鋼材を高温の亜鉛溶湯に浸す方法で、厚くて丈夫な亜鉛被膜が形成されます。
被膜の厚さは一般的に50μm以上で、耐食性が非常に高いのが特徴です。
橋梁や鉄塔、屋外構造物など、厳しい環境下での使用に適しています。
電気亜鉛めっき
電解法で亜鉛を析出させる方法で、薄い被膜が得られます。
溶融亜鉛メッキに比べ被膜は薄い(数μm~10μm程度)ですが、均一で美しい外観を得られ、自動車部品や精密機械部品など、表面の仕上げが求められる用途に適しています。
亜鉛メッキの特長
1.優れた防錆効果
亜鉛は鉄よりも腐食されやすいため、亜鉛メッキの被膜が鉄を犠牲にして腐食から守る「犠牲防食効果」を発揮します。
傷や割れがあっても亜鉛が先に腐食されるため、鉄の腐食進行を大幅に抑制可能です。
2.耐久性が高い
特に溶融亜鉛メッキは厚い被膜を形成するため、屋外の過酷な環境下でも長期間にわたり鉄鋼材料の腐食を防ぎます。
これによりメンテナンスコストの削減にもつながります。
3.加工性の良さ
亜鉛メッキは被膜が比較的柔軟であり、メッキ後の曲げ加工や溶接加工も可能です。
ただし溶融亜鉛メッキの場合、溶接時に亜鉛が蒸発しやすいため換気や防護措置が必要です。
コスト効率が高い
亜鉛メッキは材料費や処理コストが比較的低いため、大量生産品や構造物の防錆対策に適しています。
主な用途例
分野 | 用途例 |
---|---|
建設・土木 | 鋼構造物、橋梁、フェンス、手すり |
自動車部品 | ボディパーツ、シャーシ、ブラケット |
電気・電子機器 | 電気接点、端子、ケース |
家電製品 | 洗濯機フレーム、冷蔵庫外装 |
注意点と対策
亜鉛メッキの弱点としては、被膜が薄い電気亜鉛メッキは耐久性が溶融亜鉛に比べ低いこと、そして塩害や酸性雨の影響を受けやすいことが挙げられます。
これを補うため、亜鉛-ニッケル合金メッキや亜鉛-鉄合金メッキといった複合メッキや、クリア塗装を施すことで耐久性を向上させる方法もあります。
亜鉛メッキは「コストを抑えつつ確実に防錆したい」場合に最も効果的な選択肢です。
長期的な耐食性を求められる構造物や自動車部品に不可欠な技術として、今後もその需要は高まり続けるでしょう。
銅メッキの特徴と用途
銅メッキは、金属表面に銅の薄膜を析出させるメッキ方法で、その優れた導電性、導熱性、密着性から多岐にわたる分野で重要な役割を果たしています。
特に電子・電気機器分野においては基盤や配線の材料として欠かせない処理として活用されていますが、装飾用途や耐食性向上のためにも利用されます。
銅メッキの主な特徴
1.優れた導電性・導熱性
銅は鉄やニッケルなどの金属に比べて非常に高い導電性を持ち、電気回路や配線のメッキとして最適です。
また、熱を効率よく伝える性質があるため、放熱性が求められる部品にも適用されます。
2.密着性の高さ
銅は多くの金属に対して密着性が良く、他のメッキ層の下地としてよく使われます。
例えばニッケルメッキやクロムメッキを施す前の中間層として銅メッキを施すことで、メッキ層全体の剥がれや割れを防止します。
3.加工のしやすさ
銅メッキは柔軟性があり、被膜が割れにくい特徴を持つため、メッキ後の曲げ加工や成形が比較的容易です。
4.耐食性の補助的効果
純銅自体は腐食に弱いものの、適切な処理を施すことで一定の耐食性が得られます。
また、銅メッキ層の上にニッケルやクロムを重ねることで耐食性を大幅に向上させることが可能です。
銅メッキの主な用途
分野 | 用途例 |
---|---|
電子・電気機器 | プリント基板の配線、電気接点、コネクタ |
自動車部品 | 電気系部品の端子、配線、接点 |
装飾・工芸品 | 金属家具の下地処理、装飾品の下地 |
電気機械部品 | モーター部品、変圧器コアのシールド層 |
銅メッキの方法
・電解銅メッキ
最も一般的な方法で、銅イオンを含む電解液に被処理物を浸し電流を流すことで銅を析出させます。
均一で密着性の高い銅膜が得られます。
・無電解銅メッキ
化学反応によって銅を析出させる方法で、複雑形状や凹凸の多い部品に均一に銅被膜を形成できるため、基板の多層配線などに利用されます。
注意点
銅メッキはそのままでは耐食性が低いため、屋外や腐食性の強い環境で使う場合は必ず耐食性のある上位メッキ(ニッケルやクロムなど)や塗装と組み合わせる必要があります。
また、銅は硫化による変色も起こりやすいため、見た目の維持には保護処理が重要です。
銅メッキは、電気的な性能を重視した用途において特に有効なメッキ技術です。加工のしやすさと密着性の良さから多層メッキの中間層としても重宝され、機能的かつ経済的な面で幅広い産業分野で利用されています。
めっき処理のある加工品の見積り依頼ならアスクへ
試作品や小ロットの加工も大歓迎!
特に手のひらサイズの部品製作を得意としています。
アスクなら、試作品のお見積もりが最短1時間で可能!!
お気軽にお問い合わせください。
試作全国対応!
簡単・最短1時間お見積り
ブログ記事も投稿しておりますので是非ご覧ください♪
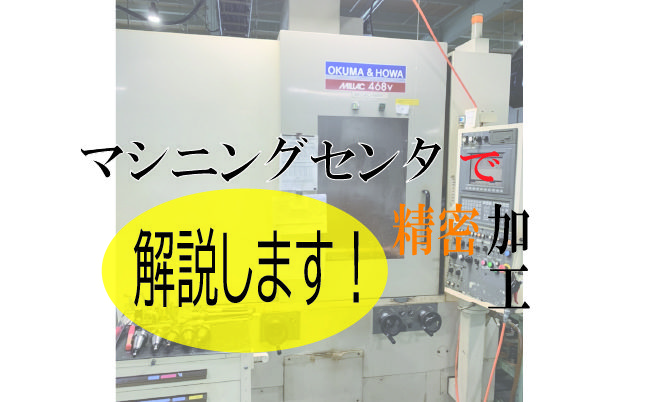
他の動画ご覧ください♪