切削加工とは?加工のプロが基礎から実践のポイントまでをご紹介!
本日は精密な加工も可能な切削加工について記事を書いていきたいと思います。
製造業の方には当たり前の内容かもしれませんが、是非ご覧ください♪
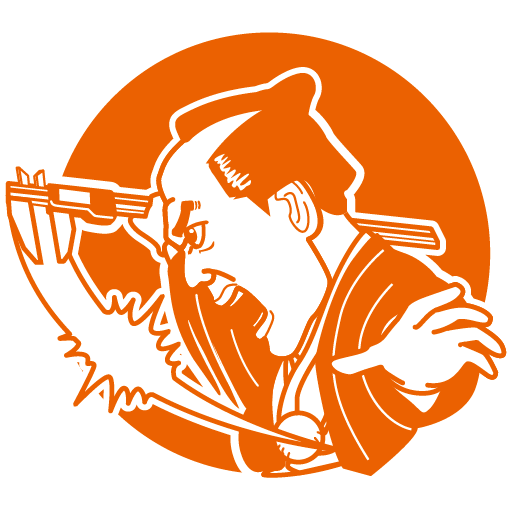
切削加工とは
切削加工とは、金属や樹脂などの素材から、回転する刃物や工具を用いて不要な部分を物理的に除去し、目的の形状や寸法に仕上げる加工方法です。
工作機械にワーク(素材)や工具を取り付け、工具が素材に食い込むことで切りくず(切粉)を発生させながら、目的の形に近づけていきます。
この加工法は「除去加工」や「機械加工」とも呼ばれ、主に寸法精度や表面粗さが求められる部品製造に用いられます。
切削加工の代表的な種類には、以下のようなものがあります。
・旋盤加工(Turning):回転する素材に対して固定されたバイトで外径や内径を削る加工。
・フライス加工(Milling):固定された素材に対し、回転するカッターで平面や溝を削る加工。
・穴あけ加工(Drilling):ドリルなどで素材に円形の穴を開ける加工。
・中ぐり加工(Boring):既存の穴を拡大・仕上げする加工。
これらの加工は、単一の工具だけで行うのではなく、工程ごとに工具や機械を使い分けて精度を追求します。
例えば、荒加工では大きく材料を削り取り、仕上げ加工で高精度な寸法や滑らかな表面を実現します。
また、切削加工の対象となる素材は多岐にわたり、鉄鋼、アルミニウム、真鍮、ステンレス、樹脂、チタンなどが挙げられます。
それぞれの材料に応じて、工具の材質や形状、切削条件(切削速度や送り速度、切り込み量など)を適切に設定することが求められます。
切削加工の用途は幅広く、自動車や航空機の部品、医療機器、半導体装置、電子部品、金型など、精密さと堅牢性が求められるあらゆる分野に及びます。
特に、最終製品に関わる高精度な部品加工には、他の加工法では実現が難しい寸法公差や表面性状が求められるため、切削加工が最適とされます。
さらに、現代の切削加工はCNC(コンピュータ数値制御)技術によって自動化されており、繰り返し精度が高く、安定した品質を維持できます。
設計図面をもとにCAD/CAMソフトを使用してNCプログラムを作成し、それを加工機に入力することで、熟練者でなくとも高精度な加工が可能になっています。
このように、切削加工は「素材を削る」というシンプルな原理に基づきながらも、非常に奥が深く、製造業の根幹を支える技術の一つとして位置づけられています。
切削加工のメリットとデメリット
切削加工には多くの利点がありますが、一方で制約や欠点も存在します。
以下では、それぞれを具体的に解説します。
■ メリット
1.高精度な寸法制御が可能
切削加工は、他の加工法と比べて圧倒的に高い寸法精度が実現できます。
ミクロン(μm)単位での加工が可能なため、部品同士の嵌合や機能性を重視する製品には最適です。
例えば、シャフトとベアリングのはめ合い、モーター部品の芯ブレ管理などに活用されます。
2.多様な形状に対応可能
平面、曲面、溝、ねじ、穴など、さまざまな形状を一つの工作機械で加工できます。
特に、複雑な三次元形状や高精度のねじ切りなどは、切削加工でしか対応できないケースもあります。
マシニングセンタや複合加工機の導入により、一度の段取りで複雑な形状加工も可能です。
3.加工後の仕上げ精度が高い
切削加工は滑らかな表面を得やすく、光沢のある仕上げ面を作ることもできます。
表面粗さ(Ra)が1μm未満といった超仕上げも、適切な条件と工具を用いれば十分に可能です。
4.少量多品種の製造に対応
金型を必要としないため、試作や少量生産にも適しています。
設計変更にも柔軟に対応でき、リードタイムの短縮が可能です。
■ デメリット
1.材料歩留まりが悪い
切削加工は素材を削って形を作るため、切りくずとして材料の一部が廃棄されます。
そのため、材料の使用効率(歩留まり)は他の加工法(鍛造や鋳造など)と比較して低くなります。
高価な材料を使用する場合、このロスがコストに直結します。
2.工具摩耗によるコスト増
加工には硬質な工具を使用しますが、特に硬い材料(ステンレスやチタンなど)を切削すると工具の摩耗が早く進みます。
これにより、工具交換や補充、調整の頻度が高まり、運用コストがかさむ可能性があります。
3.加工時間が長くなることがある
複雑な形状や高精度の要求がある場合、1つの製品に対して長時間の加工が必要になることがあります。
また、荒加工→仕上げ加工と段階を分けるため、工程が増えてしまうこともあります。
4.条件設定に技術が求められる
切削速度や送り速度、切り込み量などの条件設定を誤ると、加工面の荒れや寸法不良、工具破損につながります。
そのため、経験やノウハウが求められる作業でもあります。
このように、切削加工は高い柔軟性と精度を持つ一方で、材料ロスや工具管理といった運用面の課題も存在します。
実際の加工現場では、これらのメリットとデメリットを理解し、最適な加工法として選定することが重要です。
切削加工の種類
旋盤加工(Turning)
旋盤加工は、円柱状の素材(ワーク)を主軸に取り付けて高速回転させ、そこに固定された単刃工具「バイト」を当てて削る切削加工です。
主に丸物の外径や内径、端面などを高精度で加工できるのが特徴で、古くからある代表的な切削技術の一つです。
旋盤加工では以下のような多様な工程を一台でこなすことができます。
・外径削り:円柱の外側を直径方向に削り、所定の外径寸法に仕上げる。 内径削り:中ぐりバイトを使って、内側の穴を拡大・精密化する。
・端面削り:ワークの端面を削って平らに整える。
・突っ切り:ワークの一部を切り離す。
・ねじ切り:バイトを使って外ねじ・内ねじを加工する。
加工対象としては、シャフト、パイプ、ピン、軸受(ベアリング)部品、ボルト、ナットなどの回転対象物が主です。
工作機械としては、汎用旋盤、NC旋盤、CNC旋盤があり、近年は自動化されたCNC旋盤が主流となっています。
さらに、高度な旋盤加工には複合加工機(複数の回転軸や工具搭載が可能なCNC旋盤)が使用されることもあり、これによりフライス加工や穴あけ加工まで1台で行う「ワンチャック・フル加工」も可能です。
これは加工時間の短縮、精度向上、工数削減に寄与します。
旋盤加工の特長は以下の通りです。
・回転対称形状の精密加工に最適
・表面仕上げが美しく、同軸精度も高い
・段取りが比較的簡単で、加工効率が高い
・工具の形状と位置決めにより、複雑な加工も可能
ただし、回転対象外の角材などは原則として加工できないため、対象素材に制限があります。
また、工具の摩耗やワークの芯ブレにより精度が影響されることもあるため、慎重な段取りやメンテナンスが重要です。
フライス加工(Milling)
フライス加工は、固定された素材に対して回転する多刃の切削工具(フライスカッター)を当てて削る加工方法です。
工具が回転し、ワークがX軸・Y軸・Z軸方向に移動することで、さまざまな形状に加工することができます。
主に以下のような加工に対応します。
・平面加工:広い面を削って滑らかに仕上げる。
・溝加工:溝や段差などを形成する。
・側面加工:素材の側面を垂直または斜めに削る。
・穴あけやポケット加工:中空部分を掘り込む。
・3次元曲面加工:金型や機構部品などに見られる自由曲面形状の加工。
対象となるワークは角材やプレートが中心で、自動車部品、機械部品、金型、治具などに広く用いられます。
フライス加工に使用される機械には、以下のような種類があります。
・汎用フライス盤:手動操作で加工。試作や教育用など。
・NCフライス盤:数値制御によって自動化されたタイプ。
・マシニングセンタ(MC):自動工具交換機構を備えた多機能な加工機で、連続加工が可能。
特にマシニングセンタでは、3軸、4軸、5軸などの構成があり、同時に複数軸で加工を行えるため、複雑形状の加工も一度の段取りで対応可能です。
フライス加工の特徴
・角物や複雑形状に対応可能な汎用性
・高い加工精度と表面品質
・工具の種類が豊富で、細かなニーズに対応
・自動化が進み、生産性が高い ただし、切削抵抗が大きくなりやすく、振動による加工面の荒れや工具摩耗が発生する可能性があります。
加工条件(切削速度・送り速度・工具径・切り込み深さなど)の最適化が求められます。
穴あけ加工(Drilling)
穴あけ加工とは、ドリルなどの工具を用いてワークに穴を開ける加工方法で、切削加工の中でも非常に基本的かつ重要な工程です。
穴あけ加工は単に丸穴を開けるだけでなく、次の加工工程(ねじ切り、嵌合、リーマ仕上げなど)の基準となるため、穴の位置精度、直径精度、深さ精度が非常に重要です。
基本的な穴あけ工程は以下の通りです。
・センタードリル加工:ドリルのブレ防止のため、中心位置を確保。
・ドリル加工:目的の直径まで穴を開ける。
・リーマ加工:仕上げ用の工具で穴の精度と面粗さを向上させる。
・タップ加工:ねじ穴を加工する。
・中ぐり加工:穴を拡張・精密化する。
工具には以下のような種類があります。
・ツイストドリル:最も一般的な円筒状の穴あけ用工具。
・ステップドリル:段階的に穴径を広げる。
・ガンドリル:深穴加工に適した高精度ドリル。
・リーマ:仕上げ用工具で、穴の公差や表面品質を向上。
穴あけ加工の難しさは「まっすぐ、正確に、目的の深さ・直径で穴をあけること」にあります。
特に深穴加工では、切りくずの排出不良やドリルの曲がりが問題になりやすく、切削油の供給や工具冷却が重要です。
また、CNC機やマシニングセンタを用いれば、複数の穴加工を自動で連続して行うことが可能で、リピート性と作業効率が格段に向上します。
穴あけ加工の特徴
・最も基本的で汎用的な加工
・あらゆる製品・部品に不可欠
・工具と条件の選定が精度に直結
・深穴・高硬度材加工には専用工具が必要
トラブルとしては、バリの発生、穴の真円度不良、位置ズレ、工具破損などがあり、対策として切削条件の最適化や専用冶具の使用が重要です。
中ぐり加工(Boring)
中ぐり加工とは、すでに開けられた下穴をさらに削って内径を拡大・仕上げる加工方法です。
ドリルで開けた穴は、工具のブレや切りくずの影響で内径の精度が出にくいため、最終仕上げとして中ぐり加工を行うことで、高精度な穴径・真円度・同軸度・表面粗さを確保します。
主な加工内容は以下の通りです。
・内径仕上げ:穴径の寸法精度をミクロン単位で調整。
・段付き穴加工:異なる直径を持つ複数の内径を形成。
・座ぐり加工:ボルト頭などが収まる平坦面を内側に作る。
中ぐり加工に使用される工具は「ボーリングバー」と呼ばれ、切れ刃を持つ一方向突き出し形状が一般的です。
NC旋盤やマシニングセンタに取り付けて使用され、工具の突き出し長さが長くなるほど工具剛性が下がるため、ビビリ振動対策が重要です。
特に中ぐり加工では以下のようなポイントが求められます。
・穴の真円度・円筒度の確保
・既存穴の芯ずれや傾きの修正
・寸法精度(H7などの公差対応)
・内面の仕上げ面粗さの向上(Ra1.6以下など)
たとえば、エンジンブロックや油圧シリンダー、ベアリングホルダーなどでは、高い内径精度と表面品質が要求され、中ぐり加工が不可欠です。
CNC機による加工では、事前に開けた穴の位置情報を基に自動補正を行い、高精度な位置制御・切削制御が可能です。
中ぐり加工のメリット
・仕上げ精度が高く、内径の微調整が可能
・段付き・テーパ穴の加工にも対応
・ドリルでは難しい長穴や深穴の高精度化が可能
一方、工具の突き出し量や加工条件によってビビリ振動が起きやすく、加工面が荒れたり寸法が狂ったりすることがあります。
これを防ぐために、剛性の高いボーリングバーの選定、切削条件の最適化、内部給油による切りくず除去が重要です。
タップ加工(Tapping)
タップ加工は、穴の内側にねじ山(メネジ)を形成する加工方法で、主にボルトやねじで部品同士を締結するための機械要素加工の一つです。
タップという専用の工具を用いて、下穴に対して規定のねじ形状を削り出します。
タップ加工には以下のような種類があります。
・ハンドタップ:手作業で使用。試作や小ロットに最適。
・機械用タップ(スパイラルタップ、ポイントタップ):旋盤やマシニングセンタでの自動加工用。
・ロールタップ(転造タップ):切削ではなく塑性変形でねじを成形する方式。切りくずが出ず、高強度なねじを形成。
加工の流れは次の通りです。
・下穴加工:ドリルで適切な直径の下穴を開ける(呼び径より小さい)。
・タップ加工:専用のタップ工具で下穴内にねじ山を形成する。
・仕上げ確認:ねじゲージやボルトで嵌合を確認。
タップ加工は特に小径ねじや深穴ねじにおいて難易度が高くなるため、切削油の供給や適切な回転速度、送り速度の設定が必要です。 切りくずの排出が不十分だと、タップの折損やネジ不良の原因となるため、内部給油式タップやスパイラルタップがよく使われます。
タップ加工の代表的な用途
・アルミ・鉄・ステンレスなどの部品のねじ穴形成
・精密機器や筐体のねじ固定部
・自動車部品や機械フレームのボルト締結部
タップ加工の特徴
・ねじ締結のための不可欠な工程
・専用タップで高い再現性が得られる
・自動化により量産も可能
・ロールタップを使えば強度向上も図れる
注意点として、ねじ精度(メートルねじM、ユニファイねじUNC/UNFなど)や等級(6H、6gなど)に対応した工具と加工条件が必要です。
また、タップが折れると除去が困難なため、加工時の監視や工具寿命の管理も重要です。
リーマ加工(Reaming)
リーマ加工とは、すでに開けられた下穴の内径を高精度かつ高品質に仕上げる加工方法です。
専用の切削工具である「リーマ(reamer)」を使い、わずかな切込みで内面を仕上げることで、寸法精度・真円度・表面粗さの向上を図る工程です。
加工の目的と特徴
リーマ加工の主な目的は、次のような「仕上げ精度」を得ることです。
・寸法公差(例:H7、H8)への対応
・真円度や円筒度の向上
・表面粗さの改善(Ra1.6以下など)
ドリル加工では、わずかな芯ぶれや振動によって寸法のばらつきが出やすく、また内面も荒れがちです。
そこで、リーマを使用してわずか数十μm単位の切込みで仕上げることで、精度と表面性の両立を実現します。
リーマの種類
用途や材質、加工環境に応じて、以下のようなリーマが使われます。
・ハンドリーマ:手作業で使う。精密機器や現場修正に用いられる。
・マシンリーマ:工作機械用。高い繰り返し精度を確保。
・ストレートリーマ・スパイラルリーマ:切れ刃の形状によって異なる。スパイラルリーマは切りくず排出性が良好。
・調整式リーマ:刃径を微調整できる。試作や多品種対応に便利。
リーマ加工の流れ
・下穴をドリルや中ぐりで開ける(リーマの仕上がり寸法より0.2〜0.5mm小さく)
・リーマをゆっくり回転させながら挿入・加工
・再研磨や再使用ができるものもある
注意点とメリット
・回転数は低速、送りは一定が基本。無理な送りで工具が破損しやすい。
・切削油の使用は必須。焼き付き防止と面粗さ改善に効果あり。
・芯ずれや下穴精度が悪いと効果が得られないため、前工程が非常に重要。
リーマ加工は、特にベアリングの圧入穴やシャフト貫通穴、ピン挿入部などに使用され、高精度な嵌合を求められる場面で不可欠な加工方法です。
キー溝加工(Keyway Cutting)
キー溝加工は、回転部品(シャフト)と動力伝達部品(歯車・プーリーなど)との間にトルクを伝えるための“キー”を挿入するための溝を掘る加工です。
このキー溝にキーをはめ込むことで、部品同士の相対回転を防ぎ、動力が確実に伝達されます。
キー溝の構造と用途 キー溝には一般的に以下のような種類があります。
・平行キー溝:最も一般的。キー断面が長方形で、軸方向に平行。
・くさびキー溝:一部テーパーが付いており、打ち込み式。
・半月キー(ウッドラフキー)溝:円弧状のキーを使用し、主に小径シャフトに用いられる。
使用例としては、モーターシャフトとギヤ、ポンプ軸とカップリング、フライホイールとクランク軸など、トルク伝達を伴うあらゆる機械要素部で見られます。
キー溝加工の方法 キー溝は以下のような加工法で作られます。
ブローチ盤による加工:専用のブローチ工具で一発加工。量産向き。
・スロッター(形削り盤)による加工:1ストロークごとに削る。小ロットや特殊形状に適応。
・ワイヤー放電加工やエンドミルによる加工:マシニングセンタでも対応可能で、多様な形状に対応。
・CNCマシンによる自動加工:同時加工や位置決めが精密に行える。
加工時のポイントと注意点
・軸と穴のキー溝は芯合わせ(同芯性)が重要。ずれがあると振動やトルク伝達不良が発生。
・嵌合公差に注意(キーの厚みと溝の幅、深さ)。
・仕上げ精度が低いと、キーの抜けやがたつきの原因になる。
キー溝加工は比較的単純な形状に見えますが、実際には位置精度、溝深さ、軸方向の長さ管理など、要求精度が高い加工です。
特に、高速回転する機械では、わずかな偏心やバランス不良でも性能に大きな影響を与えます。
面取り加工(Chamfering)
面取り加工とは、部品の角やエッジ部を斜めに削る加工方法です。
図面上では「C面取り(例:C0.5)」などと表記され、角のエッジを0.5mmの45°で削ることを意味します。
丸みをつける「R面取り」と区別される場合もありますが、ここでは「C面」に焦点を当てて解説します。
面取り加工の目的
面取りには以下のような目的があります。
・バリの除去:切削や穴あけ後にできる鋭いバリを除去し、安全性を確保。
・組立性の向上:部品の嵌合や組み立てがスムーズになる。
・見た目の改善:美観を保つことで、製品品質が向上。
応力集中の緩和:シャープエッジによる応力集中を回避し、疲労破壊を防止。
つまり面取りは単なる「仕上げ」ではなく、機能的にも非常に重要な加工です。
加工方法と使用工具
面取り加工は以下のような方法で行われます。
・専用の面取りカッター:フライスやマシニングセンタで使用される。
・ドリルやエンドミルの傾斜使い:簡易的な面取りに利用。
・バリ取り工具やリューター:手作業で行う場合。
・CNCプログラムでの自動化:角部や穴のエッジを連続して加工可能。
複雑な三次元形状でも、CAMで指令すれば自動で正確な面取りが可能です。
注意点と品質管理
面取り加工で重要なのは、以下の要素です。
・寸法管理:C0.5やC1.0など指定された寸法を確実に守る。
・エッジの傷や面粗さ:加工後の滑らかさやバリ残りに注意。
・加工順序:バリの発生しやすい工程の後に実施することで、再発を防ぐ。
また、外周だけでなく穴の開口部や内角にも面取りを指示される場合があり、その際には「裏面取り」や「逆面取り」と呼ばれる加工を行います。
面取り加工は、機能性・安全性・審美性を高めるために欠かせない仕上げ工程であり、部品製造の最終品質を左右する重要な役割を果たします。
突っ切り加工(Parting Off)
突っ切り加工とは、旋盤などで回転する素材に対して、工具を横方向に送り、部品を素材から切り離す加工です。
英語では「パーティングオフ(Parting Off)」と呼ばれ、最終工程として多くの加工現場で使われます。
加工の特徴と目的
突っ切り加工の主な目的は以下の通りです。
・加工済みの部品を素材から切り離す
・シャフトやパイプなどを所定の長さに分割する
・溝やスリット加工に応用される場合もある
加工対象は丸物が多く、旋盤や複合加工機での自動化が一般的です。
自動旋盤では突っ切りが終わると同時に次の材料が送り出されるため、量産工程の中核的な役割を担っています。
使用工具と加工方法
突っ切りには専用の突っ切りバイトを使用します。
形状は薄く、先端が鋭く設計されており、切削抵抗を小さくする工夫がされています。
最近ではインサート式突っ切り工具が主流で、交換性や切りくず処理性に優れています。
加工の流れは以下の通りです。
・ワークをチャックで固定し、回転開始
・突っ切りバイトを横方向に進める
・部品が母材から切り離される
・落下防止の工夫(キャッチャーなど)を実施
加工上の注意点
突っ切り加工は、非常にシンプルに見える反面、次のような課題が伴います。
・切削抵抗が高くなりやすい:工具が細いため、ビビリやたわみに注意。
・切りくずの巻き付き:断続切削になると切りくず処理が難しくなる。
・切断時のバリや段差:最後の瞬間で部品が崩れて段差がつくことがある。
これらを防ぐために、適切な送り速度と切削条件、クーラントの使用が重要です。
特にステンレス鋼などの粘りのある材料では、切りくずが巻き付きやすく、工具寿命にも影響します。
突っ切りは、加工工程の“締め”に当たる重要なフェーズであり、失敗すればそれまでの加工が無駄になります。
安定性と再現性が求められる、一見地味だが非常に奥が深い加工方法です。
使用される機械と工具
工作機械の種類
切削加工において使用される工作機械は、加工対象物(ワーク)の形状、求められる精度、ロット数、生産性などに応じて最適なものが選定されます。
ここでは、代表的な工作機械とその特徴について紹介します。
● 旋盤(Lathe)
旋盤は、ワークを回転させて固定工具で削る機械です。
主に丸棒や円筒形の加工に用いられ、外径削り、内径削り、端面削り、ねじ切り、突っ切りなど、さまざまな工程を一台でこなすことができます。
手動操作の汎用旋盤のほか、NC旋盤(数値制御)やCNC旋盤(コンピュータ制御)も一般的で、量産や高精度な加工に対応します。
● フライス盤(Milling Machine)
フライス盤は、固定されたワークに対して回転する刃物(フライス)を当てて削る機械です。
平面加工、溝加工、段差加工などに対応し、角形状や複雑な外形を削るのに適しています。
縦型・横型・万能型などがあり、加工内容に応じて選択されます。
現在はNC制御のNCフライス盤も広く使われています。
● ボール盤(Drilling Machine)
ボール盤は、ドリルを回転させて穴をあけるための専用機械です。
構造がシンプルで、穴あけ、皿もみ、タップ加工、リーマ加工といった基本的な穴加工に用いられます。
卓上型から自動送り付きのものまで多様な種類があり、穴の位置精度や深さ管理が求められる加工に向いています。
● マシニングセンタ(Machining Center)
マシニングセンタは、フライス盤に工具自動交換装置(ATC)とNC機能を組み合わせた高機能な工作機械です。
複数の工具を自動で切り替えながら、穴あけ、タップ、フライス、彫り込みなどを連続で行えます。
縦型(VMC)と横型(HMC)があり、加工形状やワークの配置に応じて選ばれます。
自動化・高効率加工に欠かせない存在です。
● CNC旋盤(CNC Lathe)
CNC旋盤は、汎用旋盤に数値制御(NC)を組み込んだ旋盤です。
自動で工具を動かして加工を行うため、精度の高い連続加工や量産に適しています。
近年では、ミーリング機能やY軸を搭載した複合型CNC旋盤も登場し、1台で複数工程を完結できる複合加工機としての役割も担っています。
切削工具の材質と種類
切削加工の品質や効率は、使用する切削工具の材質や構造によって大きく左右されます。
工具の性能は「耐摩耗性」「耐熱性」「靱性」などに依存し、加工対象の材質や条件に応じて最適な工具材が選ばれます。
● 主な工具材質
材質名 | 特徴 | 主な用途 |
---|---|---|
ハイス(HSS) | 靱性が高く、安価。手仕上げや小ロット加工向き。 | 鉄、アルミ、樹脂など |
超硬合金 | 高硬度・高耐熱。高速度・高精度加工に適する。 | 鋼、ステンレス、アルミ等 |
セラミック | 耐摩耗性と耐熱性に優れるが脆い。高速切削用。 | 鋳鉄、焼結材など |
CBN(立方晶窒化ホウ素) | 超硬より硬く、耐摩耗性抜群。高硬度材向き。 | 焼入鋼、工具鋼など |
ダイヤモンド(PCD) | 最硬材。摩耗しにくく、非鉄金属や樹脂に最適。 | アルミ、銅、CFRP等 |
● 工具の種類と形状
・バイト(旋削用工具):旋盤で使用。外径・内径・端面・ねじ切りなど各種形状がある。
・エンドミル:フライス加工用。形状はラフィング、ボールエンド、スクエアなど。
・ドリル:穴あけ加工用。ねじれ形状(ツイストドリル)が基本。
・タップ・リーマ:ねじ切りや仕上げ穴用。
・インサート(チップ)式工具:超硬などの刃先を交換できる工具。コストと効率のバランスに優れる。
● コーティングの役割
近年では、切削工具の表面にコーティング処理を施すことで、耐久性と加工性能を向上させています。
代表的なコーティングは以下の通りです。
・TiN(窒化チタン):金色の光沢。耐摩耗性を向上。
・TiAlN(窒化チタンアルミ):高温耐性に優れ、高速加工に向く。
・DLC(ダイヤモンドライクカーボン):低摩擦。非鉄金属や樹脂に有効。
コーティングの選定も、被削材や切削条件に応じて調整する必要があります。
切削加工品の見積り依頼ならアスクへ
試作品や小ロットの加工も大歓迎!
特に手のひらサイズの部品製作を得意としています。
アスクなら、試作品のお見積もりが最短1時間で可能!!
お気軽にお問い合わせください。
試作全国対応!
簡単・最短1時間お見積り
他、ブログ記事もご覧ください♪
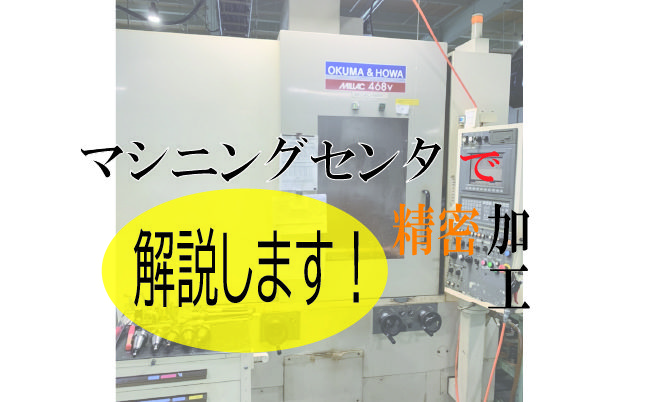
動画の投稿もしておりますので良ければご覧ください♪