研磨加工とは?加工の種類や手順を簡単解説します。
こんにちは!本日は研磨加工についての記事を書きました! 製造業に携わっている方はご存じのことかもしれませんが、ぜひご覧ください♪
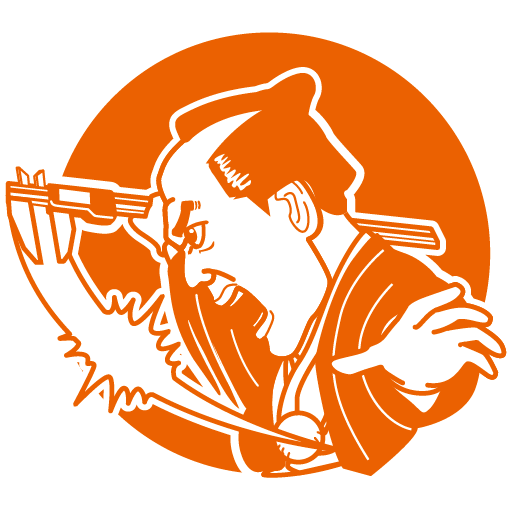
研磨加工とは
研磨加工は、主に部品や材料の表面を滑らかにすることを目的とした加工方法です。
具体的には、粗い表面を細かい粒子で削ることによって、材料の表面を平滑にし、一定の寸法精度を達成します。
研磨加工は、材料表面の粗さ(Ra値)を減少させるため、主に仕上げ工程や精密加工で使用されます。
研磨加工の主な目的は以下の通りです。
・表面仕上げ: 表面の凹凸をなくすことで、見た目や触感を向上させる。
・寸法精度の向上: 他の加工方法で得られた粗い仕上がりを精密に仕上げるために使用される。
・摩擦抵抗の低減: 機械部品の摩擦を減らすことで、耐久性や性能を向上させる。
・部品の機能性向上: 一部の製品では、表面の滑らかさが機能性に直結するため、精密な研磨が必要。
たとえば、金属部品や自動車のエンジン部品、さらには光学機器のレンズなど、非常に精密な表面仕上げが要求される分野では、研磨加工が重要な役割を果たします。
研磨により、表面に微細な傷がなくなり、部品の性能が向上します。
研磨加工の種類
研磨加工には多くの種類があり、使用する機械や道具、研磨材によってその方法は大きく異なります。
目的や加工物の特性に合わせて適切な研磨方法を選択することが重要です。
以下に、代表的な研磨方法をさらに詳しく説明します。
機械研磨
機械研磨は、専用の研磨機を用いて行う自動化された研磨方法です。
通常、研磨材(研磨パッドや研磨盤)を高速で回転させ、これを対象物に当てて表面を削ります。
主に大量生産の現場で使用され、高い精度と一貫した仕上がりが特徴です。
以下のような種類があります
平面研磨
平面研磨は、平坦な面を滑らかに仕上げるための研磨方法です。
研磨盤が回転し、加工物がその上を移動して研磨されます。
この方法は、特に金属部品や機械の基盤部分、プレートなどで使用されます。
精度の高い平面が要求される場合には、非常に重要な加工手段です。
円筒研磨
円筒研磨は、円形のワークピースを研磨するための方法で、回転するワークを研磨機で研磨します。
例えば、シャフトやスリーブなど、円筒形の部品に多く使用されます。
精密な外径や内径の加工が可能で、円筒形状の部品で求められる精度を確保するために広く用いられています。
ベルト研磨
ベルト研磨は、研磨ベルトを使って広い範囲を均一に研磨する方法です。
この方法は、曲面の研磨や大きな面積を短時間で仕上げるのに適しています。
主に金属やプラスチックの表面処理に使用されます。
手動研磨
手動研磨は、機械を使用せずに手作業で行う研磨方法です。
この方法は、非常に精密な仕上がりや微細な調整が求められる場合に適しています。
手動で行うため、柔軟に対応でき、独自の微調整を加えることが可能です。
以下の方法があります。
手持ち研磨機による研磨
手持ちの電動研磨機を使用し、手作業で表面を削る方法です。
この方法は比較的自由度が高く、狭い場所や特殊な形状の部品でも加工が可能です。
主に少量生産や修正作業に使用されます。
ラッピング研磨
ラッピングは、手作業で研磨材を使用して非常に精密な仕上げを行う方法です。
特に、精密部品や高光沢を求める部品に適しています。
例えば、光学機器のレンズや工具、ダイカスト製品の仕上げに使用されます。
超精密研磨
超精密研磨は、非常に高精度な仕上がりを求められる部品や材料に使用される研磨方法です。
高精度な研磨を行うために、極めて細かい粒度の研磨材や専用の研磨機が使用されます。
超精密研磨は、通常、以下の用途で使用されます。
光学機器や精密機械部品
光学機器や精密機械部品は、非常に滑らかで精密な表面を必要とします。
これらの部品の表面は、研磨によって非常に精密に仕上げられる必要があります。
光学レンズやミラー、半導体チップなどが代表的な例です。
超硬素材やセラミックス
超硬合金やセラミックスなどの硬い材料の表面を研磨するためには、特別な機械と研磨技術が必要です。
これらの材料は非常に硬く、普通の研磨方法ではうまく処理できないため、超精密研磨を行います。
超硬工具や硬質部品の精密加工には欠かせない技術です。
ダイヤモンド研磨
ダイヤモンドを研磨材として使用することで、非常に硬い材料の表面も精密に研磨できます。
ダイヤモンド研磨は、主に宝石や精密工具の製造、さらには半導体製造で使われることがあります。
その他の研磨方法
水研磨
水研磨は、研磨材を水と一緒に使用することで冷却効果を得つつ研磨を行う方法です。
この方法は、熱による変形や焼き付きが発生しやすい素材に適しています。
金属の加工や、特に鋳物などの素材に使われます。
磁気研磨
磁気研磨は、強い磁場を利用して微細な研磨粒子を使い、ワークの表面を研磨する方法です。
この方法は、形状が複雑な部品や細かい部分の研磨に効果的です。
研磨加工の技術と方法
研磨剤と研磨機の選定
研磨加工の品質と効率を大きく左右するのが「研磨剤」と「研磨機」の選定です。
適切な組み合わせを選ぶことで、目的とする表面粗さや寸法精度に到達しやすくなります。
まず、研磨剤は、「砥粒(とりゅう)」と呼ばれる微細な粒子を含んだ材料で、素材表面を物理的に削り取る役割を果たします。
砥粒には主に以下の種類があります。
・アルミナ(酸化アルミニウム):硬度が高く、鉄鋼系の材料に広く使われます。
・炭化ケイ素(SiC):アルミナよりも硬く、非鉄金属やセラミックスの加工に適しています。
・ダイヤモンド砥粒:非常に高硬度で、超硬合金やセラミックなどの硬質材料に最適。
・CBN(立方晶窒化ホウ素):鉄系材料に強く、特に高精度研磨に向いています。
砥粒は「粒度」(番手)で細かさを示します。
粒度が大きいほど粗く、大量に削るのに適しています。
一方、粒度が小さい(番手が高い)ほど仕上がりは滑らかになります。
次に、研磨機には多種多様な種類が存在し、以下のような分類があります。
・平面研削盤:平らな面を研磨するために使用。加工物を磁気チャックなどで固定し、砥石が水平方向に動きながら加工します。
・円筒研削盤:円筒形状の外周または内径を研磨するための装置。主にシャフトや軸などの加工に使われます。
・ベルトグラインダー:研磨ベルトを使用し、柔軟性のある加工が可能。手軽に曲面や大きな面を加工できます。
・ラッピングマシン:平坦度・鏡面仕上げが必要な場合に使用され、非常に高精度な表面処理が可能です。
研磨機の選定では、加工物の形状や寸法精度、表面粗さの要求に加え、加工時間や量産性、コストなども考慮する必要があります。
また、冷却水や研磨液(スラリー)を使用することも多く、これにより摩擦熱の発生を抑え、加工物の熱変形を防止します。
特に高精度な研磨では、これらの補助剤も重要な要素になります。
まとめると、目的とする仕上がりに対し、
「どの素材を削るのか?」「どの程度の粗さや寸法公差が必要か?」「加工時間やコストの制約はあるか?」といった観点から、適切な研磨剤と研磨機を組み合わせて選定することが、研磨加工の成功に直結します。
研磨工程の流れ
研磨加工は単なる表面の仕上げにとどまらず、製品の性能や寿命に直結する重要な工程です。
そのため、研磨は段階を踏んで計画的に進める必要があります。
以下に、一般的な研磨加工の流れを紹介します。
【STEP1】加工前の準備
研磨加工を始める前に、まずは加工対象物(ワーク)の状態確認と前処理を行います。
例えば、鋳肌が粗い状態であれば、粗研磨の前にバリ取りや切削加工を済ませておくことが必要です。
また、寸法公差や表面粗さの要求を確認し、どの程度まで仕上げるかを明確にしておきます。
この段階では、以下のような項目をチェックします。
・加工物の材質と硬度
・寸法公差、面粗度の要求値
・形状の複雑さ、取付方法
・加工後の用途(機能性や見た目)
【STEP2】粗研磨(あらけんま)
粗研磨は、削る量が多い段階で、切削加工の跡を取り除いたり、全体の形状を整えたりする目的で行います。
このとき使用する砥粒は粗い粒度(#80〜#220程度)が一般的で、効率良く削ることを重視します。
この工程では、
・平面を大まかに整える
・寸法を目標値よりやや大きめに仕上げる
・面の凹凸やゆがみを均す
などの作業が行われ、次の中研磨・仕上げ研磨の精度に影響するため、丁寧に行う必要があります。
【STEP3】中研磨(ちゅうけんま)
中研磨では、粗研磨でできたスクラッチ(傷)や不陸(ふりく:平らでない状態)をさらに細かく修正し、最終寸法に近づけます。
ここで使用する研磨剤の粒度は#240〜#600程度が主流です。
また、この段階では、
・平面度や直角度などの形状精度を追い込む
・表面粗さを要求値に近づける
・最終仕上げでの負荷を減らす
といった目的があります。
研磨時間や荷重、回転数の調整によって、仕上がり品質に大きな差が出るため、経験やノウハウが重要となります。
【STEP4】仕上げ研磨(精密研磨)
仕上げ研磨では、表面を鏡面に近いレベルまで滑らかに仕上げます。
この工程では、粒度#800〜#2000以上の非常に細かい研磨材を使用し、加工面の傷やムラを完全になくします。
この工程の目的は以下の通りです。
・表面粗さRa0.1μm以下などの高精度要求に対応
・摩擦を減らし、機械部品の性能を向上させる
・外観品質の向上(光沢・均一性)
ここでは、ラッピングやバフ研磨などの手法も使われることがあります。
特にバフ研磨は、化粧仕上げや装飾品、医療機器のような外観に敏感な製品に多く用いられます。
【STEP5】洗浄・検査・後処理
研磨後は、加工中に付着した砥粒や油、水分を超音波洗浄機や脱脂処理などで除去します。
洗浄を怠ると、汚れや異物が残り、部品の機能性や組立精度に影響するため非常に重要です。
その後、以下のような検査・評価を実施します。
・表面粗さ計によるRa値測定
・投影機やマイクロメーターによる寸法検査
・視覚によるキズ・打痕の確認
必要に応じて、防錆処理や表面コーティングなどの後処理を施すこともあります。
このように、研磨加工はただ単に「削ってきれいにする」だけでなく、工程ごとに明確な目的があり、段階を追って行うことで初めて高品質な仕上がりが得られます。
研磨加工で使われる設備・工具
研磨加工に使われる機械は、対象物の形状や加工目的に応じてさまざまです。
以下に主要な研磨機を紹介します。
平面研削盤
平面研削盤は、主に平らな表面を研磨するための装置です。
加工物をテーブルに固定し、上部に取り付けられた砥石が回転しながら前後・左右に動くことで、表面を均一に研削します。
高精度な平坦度が求められる金型部品や機械のベース面などの仕上げに使われます。
円筒研削盤
円筒研削盤は、円筒形状の外周部や内径を研磨する装置です。
加工物自体が回転しながら、外周または内側を砥石が削っていきます。
シャフトやベアリングなど、寸法精度が重要な部品の研磨に適しています。
内面研削盤
内面研削盤は、円筒形状の内径を研磨する専用機です。
内径の真円度や表面粗さを精密に仕上げる必要がある場合に使用され、例えばエンジンのシリンダー内径の仕上げなどに用いられます。
センタレス研削盤
センタレス研削盤は、ワークの中心を固定せず、左右から支えながら研磨する方式です。
主に大量生産に向いており、シャフトなどの連続加工に適しています。
自動供給による連続処理が可能で、生産性が高いのが特徴です。
バフ研磨機
バフ研磨機は、布製やフェルト製の研磨ホイールを高速で回転させ、表面を摩擦で磨く機械です。
光沢仕上げや装飾目的の部品、または金属の最終仕上げに使われます。
柔らかい圧力で磨くため、複雑形状にも対応できます。
ラッピングマシン
ラッピングマシンは、微粒子を含むスラリーを使い、非常に高精度な表面仕上げを行う装置です。
ガラスやセラミックス、光学部品などでナノレベルの面精度が求められる場合に使用されます。
研磨工具とその用途
研磨に使われる工具は、用途や材質に応じて多様です。
以下に代表的な工具を紹介します。
砥石
砥石は研磨の基本的な工具で、粒状の砥粒を固めたものです。
形状や材質、粒度によって多くの種類があり、硬い材料の加工には高硬度の砥石が使われます。
平面・円筒研削など幅広い用途で使用されます。
バフ
バフは、柔らかい布やフェルトでできた円盤状の工具です。
金属表面を滑らかにし、光沢を出す仕上げ研磨に使用されます。
研磨剤を塗布して使用し、見た目の美しさを重視する製品に向いています。
研磨ベルト
研磨ベルトは、紙や布に研磨粒子を接着した帯状の工具で、ベルトサンダーやベルトグラインダーで使われます。
広い面積を短時間で研磨でき、曲面や平面加工に適しています。
ダイヤモンドホイール
ダイヤモンドホイールは、ダイヤモンド粒子を焼き固めた高硬度の研磨工具です。
超硬合金、セラミック、ガラスなどの非常に硬い材料に対応し、精密加工に欠かせない存在です。
CBNホイール
CBN(立方晶窒化ホウ素)ホイールは、鉄系材料に対して強く、熱にも強いため、高精度・高能率な研磨に向いています。
ダイヤモンドホイールでは対応しにくい鋼材に適しています。
補助装置と消耗品
研磨加工では、機械本体だけでなく以下のような補助装置や消耗品も重要です。
・冷却装置/切削液供給装置:加工中の温度上昇を抑え、焼き付きや熱変形を防止します。
・集塵機・防塵設備:研磨時に発生する粉塵を吸引し、作業環境をクリーンに保ちます。
・ワーク固定治具:加工物を安定して保持し、寸法や形状の精度を確保します。
・スラリー(研磨液):微細な砥粒を含んだ液体で、ラッピングや超精密研磨に使用されます。
このように、研磨加工には多くの種類の設備・工具が存在し、それぞれが特定の役割を担っています。
加工目的やワークの特性に応じて、適切な機器・工具を選ぶことが、高品質な仕上がりと加工効率の向上につながります。
研磨加工の活用例と業界別のニーズ
金属加工業界における研磨加工の役割
金属加工業界では、研磨加工はほぼすべての工程に関与すると言っても過言ではありません。
機械部品や金型の仕上げに欠かせず、「表面粗さ」「寸法精度」「真円度」「平坦度」など、厳しい要求に応えるために高精度な研磨が求められます。
具体的な用途例としては以下の通りです。
・金型部品の精密仕上げ:プラスチック射出成形金型やプレス金型では、型の面精度が製品の仕上がりに直結します。鏡面仕上げや高精度の角出しには手仕上げやバフ研磨、ラッピングなどを駆使します。
・回転部品の軸受部研磨:シャフトやベアリング部では、摩擦低減と耐久性の向上のため、表面粗さをRa0.2μm以下に仕上げることも珍しくありません。
・組立用部品の嵌合調整:嵌め合い精度が必要なスリーブやブッシュ部では、μm単位での研磨仕上げが求められ、気密性や静音性に直結します。
また、量産を目的とした製造現場では、自動化された研磨機と専用治具を組み合わせて、研磨の均一性と加工時間の短縮を両立しています。
自動車・航空機業界での精密研磨
自動車や航空機などの輸送機器産業では、「安全性」「耐久性」「省エネ性能」が重要視されるため、研磨による微細な表面仕上げが不可欠です。
以下のような部品で研磨加工が活躍しています。
・エンジン部品(クランクシャフト、カムシャフト):高速回転や高圧力下で動作するため、摩擦を減らし、潤滑性を向上させるためにミクロン単位での研磨が施されます。
・ブレーキ・足回り部品:平滑な面を保つことで、ブレーキ性能や振動の抑制に寄与します。ローターの研磨加工などが該当します。
・航空機のジェットエンジン部品:高温・高圧に耐える特殊合金が使われるため、ダイヤモンド砥粒やCBN砥石による精密研磨が必須です。
また、航空機分野では「品質保証」が最も重視されるため、研磨後の検査記録やトレーサビリティの確保が義務付けられている場合もあります。
医療・精密機器分野での要求と応用
医療機器や精密機器においては、「安全性」や「衛生面」、「微細な構造への対応力」が求められるため、研磨加工は極めて重要です。
・外科用メスやハサミ:切れ味の良さと安全性の両立のため、刃先部分は極限まで研磨されます。また、光沢のある鏡面仕上げで汚れが付きにくく、洗浄性も高めます。
・人工関節やインプラント:生体適合性の高い金属(チタン、コバルトクロム合金など)を使用し、摩耗しにくいよう滑らかな表面に研磨されます。摩擦係数の低減により、長期耐久性が実現します。
・顕微鏡部品や測定機器:研磨によって光学面の精度を上げ、計測精度の信頼性を担保します。ラッピングや超精密バフ加工が多用されます。
このような用途では、最終的な使用環境や安全性に配慮した研磨が不可欠であり、高度な制御技術とクリーンな加工環境が求められます。
研磨加工における課題と今後の展望
研磨加工は多くの産業で不可欠な仕上げ技術ですが、高精度であるがゆえに課題も多く、今後の進化が期待されている分野でもあります。
ここでは、現在の主な課題と、それを踏まえた技術革新や将来の展望について解説します。
現在の研磨加工が抱える課題
研磨加工は「精密」「高品位」を求められる一方で、次のような課題が挙げられます。
1.加工時間と生産性のバランス
研磨加工は他の加工に比べて非常に時間がかかるケースが多く、生産効率を落とす要因にもなっています。
特に手仕上げ工程を含む場合、作業者の熟練度に依存し、品質のバラつきや生産リードタイムの長期化につながることがあります。
2.作業者の技能依存
高精度な研磨には熟練した技術者の感覚が必要不可欠であり、若手技術者の育成が進まないと技術の継承が難しくなります。
人手不足や高齢化が進む中で、技能の属人化が大きな問題となっています。
3.工具・砥石の摩耗と管理
研磨に使われる工具は摩耗が激しく、定期的な交換や補修が必要です。
特に高硬度材料の加工では、工具の寿命やコストが課題になります。
また、砥石のドレッシング(再成形)も品質管理上重要なプロセスです。
4.表面品質の安定性
ミクロン単位、ナノレベルの面粗さを要求される現場では、環境(温度・湿度)や設備の微細な振動も仕上がりに影響を与えるため、高度な管理体制が必要です。
均一な品質を維持するには、測定機器やフィードバック制御の導入も求められます。
技術革新と自動化の進展
近年、上記の課題を克服するために、以下のような技術革新が進んでいます。
1.CNC研磨機・ロボット研磨の導入
従来は人手に頼っていた研磨作業も、CNC(数値制御)によって自動化が進んでいます。
特に、同じ形状を大量に研磨する工程では、ロボットによる研磨アームが活躍し、安定した品質と作業時間の短縮を実現しています。
2.AI・IoTを活用した品質管理
砥石の摩耗具合や研磨面の仕上がりをリアルタイムでモニタリングし、AIが最適な加工条件を自動で調整するシステムが登場しています。
また、クラウドによる作業ログの蓄積と分析により、不良品の予測やメンテナンスの最適化も可能になりつつあります。
3.新素材に対応する研磨技術
カーボンやセラミックスなど、従来の金属よりも硬く・脆い素材に対応するため、ダイヤモンドやCBN砥粒、さらには超音波振動研磨といった先端技術の採用が進んでいます。
こうした技術は、電子部品や医療デバイスなどの精密分野で特に重宝されています。
未来に向けた研磨加工の可能性
研磨加工は、技術の進化によってさらに幅広い分野への展開が期待されています。
・スマートファクトリーとの連携:生産全体をIoTでつなぎ、研磨機もその一環として自律的に動作・補正・報告する「スマート化」が進んでいます。
・環境対応型加工:排水や粉塵の発生を抑えるエコ研磨技術や、研磨液の再利用装置の導入など、SDGsに配慮した持続可能な加工法も注目されています。
・微細・ナノ研磨の拡大:今後さらに進む半導体、光学、医療分野の精密部品製造において、ナノメートルレベルの超精密研磨が求められるようになります。
研磨加工は、決して過去の技術ではなく、今も進化を続ける「ものづくりの最終砦」と言えます。
高精度な加工が求められる時代において、いかに自動化・高効率・高品質を両立するかが、今後の研磨技術のカギとなるでしょう。
研磨加工のある部品の見積り依頼ならアスクへ
試作品や小ロットの加工も大歓迎!
特に手のひらサイズの部品製作を得意としています。
アスクなら、試作品のお見積もりが最短1時間で可能!!
お気軽にお問い合わせください。
試作全国対応!
簡単・最短1時間お見積り
他、ブログ記事もご覧ください♪
動画の投稿もしておりますので良ければご覧ください♪