仕上げ作業で行うバリ取りについて詳しく解説します!
こんにちわ!
本日は仕上げの工程で行うバリ取りについて、記事を書いていきたいと思います!
製造業に携わっている方であれば当たり前のことかもしれないですが、本日もお付き合いください♪
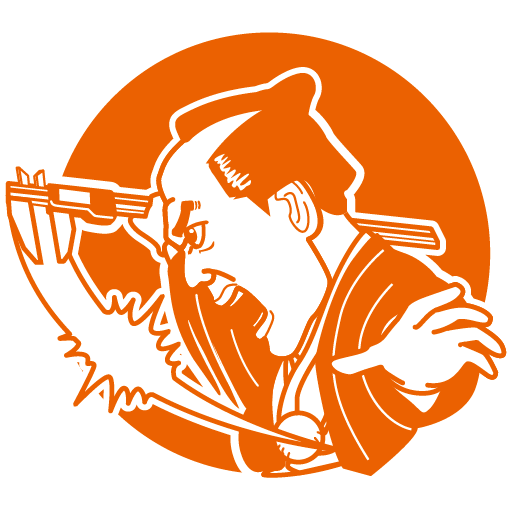
バリとは
製造加工の現場では「バリ」と呼ばれる不要な突起や切粉がしばしば発生します。
バリは、主に切削、プレス、鋳造、樹脂成形、研削などの加工工程で発生し、加工部品の端部に意図しない突起物として現れます。
たとえば、金属の切削加工では、工具が材料を削り終えた後の切り口にわずかな金属片が残ることでバリが発生します。
このバリを放置すると、組み立て精度の低下、製品の信頼性の低下、さらには作業者の手を傷つけるなどの安全面でも問題を引き起こします。
また、電子機器や精密部品などでは、バリがわずかに存在するだけでも動作不良やショートの原因となることがあります。
そのため、製品の品質管理や工程の安定性を維持するうえで、バリ取りは非常に重要な工程とされています。
バリの種類と見分け方
バリにはいくつかの種類があり、それぞれ発生メカニズムや対処法が異なります。
代表的なバリには「ロールオーバーバリ」「マイクロバリ」「フラクチャーバリ」「溶着バリ」などがあります。
たとえば、ロールオーバーバリは金属が加工中に変形して押し出されるようにしてできるバリで、切削加工や穴あけ加工後にしばしば見られます。
一方、フラクチャーバリは破断や亀裂によってできるもので、脆性材料の加工中に発生しやすい特徴があります。
マイクロバリは非常に小さなバリで、電子部品や精密機器の分野では無視できない存在です。
これらを見極めるには、拡大鏡や顕微鏡、あるいは画像処理システムを活用して観察します。
バリの種類を正確に把握することで、最適な除去方法や予防策を講じることが可能になります。
バリ取りの主な方法
手作業によるバリ取り
手作業によるバリ取りは、熟練工がヤスリやナイフ、スクレーパーなどの工具を用いて不要なバリを取り除く方法です。
最も古くから使われている方法で、特に少量生産や複雑形状、精密部品の加工後において重宝されます。
この方法の大きな利点は柔軟性です。
製品の形状やバリの位置に応じて作業者が即座に対応できるため、不良品の発生を最小限に抑えることができます。
一方で、作業者の技量に依存する点、作業時間がかかる点、人的コストが高い点などがデメリットとして挙げられます。
また、品質のバラつきが出やすいため、熟練した技術者の確保と教育が重要になります。
工具を使ったバリ取りの手法と選び方
工具を使ったバリ取りは、現場で最も一般的に行われている方法のひとつです。
手作業の延長ではありますが、専用の工具を使うことで効率や品質を向上させることができます。
使用される主な工具には、以下のようなものがあります。
・ハンドデバリングツール(手動バリ取りナイフ)
これは、バリ取り専用に設計された刃物付きのハンドツールで、手の動きに合わせて刃が自由に回転するタイプもあります。
穴の内外径や曲面など、さまざまな部位に対応する刃が用意されており、使い勝手の良さが特長です。
・リューター(電動回転工具)
小型の電動工具で、高速で回転するビットを使ってバリを削り取る方法です。
ビットの種類を替えることで金属、プラスチック、木材など様々な材質に対応でき、複雑形状や細部の仕上げにも有効です。
ただし、加工熱や削りすぎには注意が必要です。
・ヤスリや砥石
古典的な工具ですが、いまだに多くの現場で使われています。
手軽で汎用性が高く、特に小ロットの製品や複雑な形状の製品には欠かせない存在です。
平ヤスリ、丸ヤスリ、三角ヤスリなど形状も多彩です。
・バリ取り専用ドリル・カッター
穴加工の内径バリを除去するために設計された専用工具も存在します。
たとえば、カウンターシンクカッターやバリ取りリーマーなどがあり、切削機械に取り付けて使用することで、加工後すぐにバリ除去まで完了できます。
工具を用いたバリ取りの利点は、細部まで対応できる柔軟性と比較的安価な導入コストにあります。
一方、作業者の技量や選定する工具の適切さによって仕上がりが左右されるため、工具の選び方と正しい使い方が重要です。
さらに、近年ではエアモーター式や電動式の工具も普及しており、作業者の負担軽減や処理速度の向上にも寄与しています。
用途や素材に応じた工具の選定とメンテナンスを徹底することで、効率的かつ高品質なバリ取りが実現できます。
機械によるバリ取り
機械によるバリ取りは、自動化や省人化を進めるうえで有効な方法です。
バリ取り専用の装置やロボット、CNC機械などを用いて効率的に処理することができます。
主に大量生産品や同一形状の部品に適しており、生産性向上と品質の安定化に大きく寄与します。
ブラシ、バレル、ショットブラスト、研磨ベルトなどの装置を使うことで、手作業に比べて短時間かつ均一に処理できるのが特長です。
近年ではAIや画像認識を活用したバリ検出・除去装置も登場しており、より精密なバリ取りも可能となっています。
ただし、初期導入コストが高く、設備メンテナンスや段取り替えが必要な点は考慮する必要があります。
化学的・熱的処理によるバリ取り
バリ取りは物理的な方法だけでなく、化学反応や熱エネルギーを利用して行うことも可能です。
代表的な方法に「エレクトロポリッシング(電解研磨)」「熱的脱バリ(サーマルデバリング)」などがあります。
電解研磨は、電解液中で金属表面の微細な凸部を選択的に溶解させる方法で、特に微細部品や医療機器、半導体部品などに使用されます。
サーマルデバリングは、可燃性ガスを封入した密閉空間内でバリだけを燃焼・除去する方法で、内面や微細穴の処理にも対応できます。
これらの方法は物理的手段ではアクセスしづらい部分のバリも除去可能ですが、材料へのダメージリスクや高コスト、特殊設備の必要性などの課題もあります。
材質別に見るバリ取りの最適手法
バリ取りの方法は、対象となる素材によって大きく変わります。
材質ごとにバリの発生傾向や強度、脆性などが異なるため、適切な方法を選定することが、作業効率と品質の両面で非常に重要です。
ここでは代表的な3つの材質について解説します。
■ 金属(鉄・ステンレス・アルミなど)
金属は加工時の切削抵抗が高く、比較的硬いバリが発生します。
特に鉄やステンレスは、切れ味の鈍い工具を使用するとバリが大きくなりやすく、除去にも時間がかかります。
鉄系材料には、手工具(ヤスリ・ナイフ)やリューターのほか、ブラシ式のバリ取り装置やショットブラストなどの機械的方法が有効です。
一方でアルミは柔らかいため、軽い手作業でもバリを取りやすい反面、工具が食い込みやすく、削りすぎに注意が必要です。
電解研磨などで表面仕上げと同時にバリ除去を行う方法も選択肢です。
■ 樹脂(プラスチック類)
樹脂は加工熱によって溶けたり、引きちぎるような形でバリが出たりするため、バリが“糸状”や“薄片状”になることが多いです。
このようなバリには、ナイフやカッターによる手作業が向いており、ヒートガンで軽く熱して除去する方法もあります。
また、硬質樹脂であれば研磨ベルトや小型サンダーによる仕上げも有効です。
一方で、過剰な加熱や摩擦による“白化”や“焦げ”が発生するリスクがあるため、素材に合わせた温度管理と工具選定が必要です。
■ セラミックス・脆性材料
セラミックスやガラスなどの脆性材料は、力をかけすぎると割れてしまうため、物理的なバリ取りには非常に繊細なアプローチが求められます。
主に砥石やダイヤモンドビットを用いたリューター作業、または超音波バリ取りなどの非接触的な手法が有効です。
また、化学的エッチングやレーザー加工を応用することで、表面を傷めずに微細なバリを取り除くことも可能です。
これらは主に電子部品や医療用部品などの超精密領域で用いられます。
試作全国対応!
簡単・最短1時間お見積り
他、ブログ記事もご覧ください♪
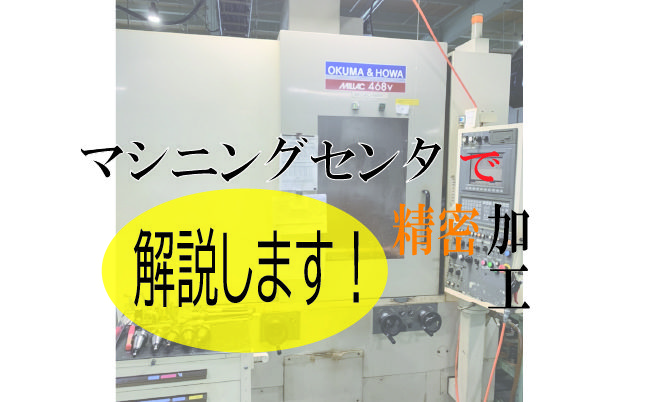
動画の投稿もしておりますので良ければご覧ください♪