アルミとステンレスの違いについて徹底比較!!
本日はアルミとステンレスについての比較記事を書いていきます!
是非ご覧ください♪
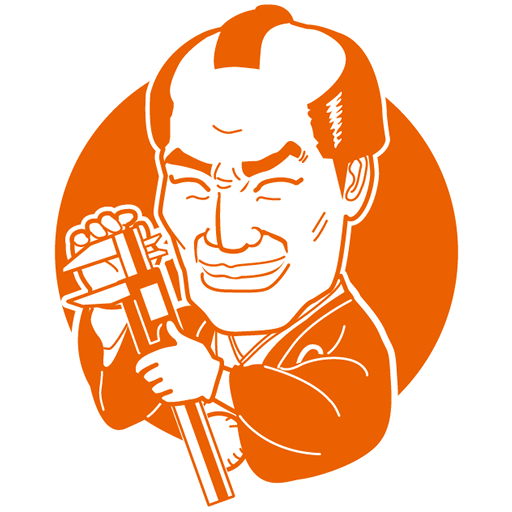
基本的な性質の違い
アルミニウムの特性
アルミニウム(Al)は、地殻中に豊富に存在する軽金属の一つで、優れた物理的・化学的性質を持ち、幅広い分野で活用されています。
まず最大の特徴は「軽さ」です。
比重は約2.7と非常に軽量で、鉄やステンレスの約3分の1程度しかありません。
これにより、軽量化が求められる航空機や自動車、建築資材などに広く利用されています。
次に挙げられるのが「高い耐食性」です。
アルミニウムは空気中にさらされると、表面に非常に薄い酸化皮膜(酸化アルミニウム)を自然に形成します。
この皮膜は非常に安定しており、内部の金属を腐食から守るバリアとして働きます。
特に、塩害や湿気がある環境においても比較的耐久性が高いため、屋外用途にも適しています。
また、「熱伝導性・電気伝導性の良さ」も重要な特性です。
銅には及ばないものの、アルミニウムは高い熱伝導性と電気伝導性を持ち、放熱部品や電線、電子機器の筐体などに用いられます。
これらの特性に加え、加工性にも優れており、押出、圧延、切削、溶接、曲げ加工などの工程に適しているため、製造プロセスの自由度が高い点も強みです。
一方、機械的強度はステンレスなどの鉄系金属に比べて劣ることが多いため、強度が求められる用途では、アルミニウム合金(たとえばA6061やA7075など)として使用されるのが一般的です。
これらの合金は、マグネシウムやシリコン、銅、亜鉛などを添加することで強度や硬さを高めています。
アルミはまた非磁性体であり、磁場の影響を受けにくいという性質があります。
電子機器や磁場環境での使用にも適しており、MRI装置周辺などでも活用されます。
さらに、表面処理による見た目の美しさの向上も可能で、アルマイト処理を施すことで耐食性・硬度をさらに向上させつつ、さまざまな色に着色することもできます。
このように、アルミニウムは軽量性、耐食性、熱・電気伝導性、加工性といった多くのメリットを持つ万能素材ですが、強度や耐摩耗性に関しては限界があるため、使用環境や目的に応じた合金設計や処理が重要となります。
ステンレス鋼の特性
ステンレス鋼(Stainless Steel)は、鉄を主成分としながらクロム(Cr)を10.5%以上含有することで、優れた耐食性を実現した合金鋼です。
その名の通り「ステイン(汚れや錆)レス(少ない)」という特徴を持ち、サビに強く、見た目の美しさを長期間保てることから、幅広い産業で使用されています。
ステンレス鋼の最大の特徴は、その「自己修復性を持つ耐食性」です。
これは、表面に形成される非常に薄いクロム酸化皮膜によるもので、傷がついても自然に空気中の酸素と反応して再生されるため、錆が進行しにくい性質を持ちます。
この耐食皮膜は塩素環境や酸性環境にも比較的強く、キッチン器具や食品機械、医療機器、化学プラントなどの分野で重宝されています。
また、ステンレス鋼は「高い強度と耐摩耗性」も兼ね備えています。
一般的なオーステナイト系(例:SUS304)やマルテンサイト系(例:SUS420)などのステンレス鋼は、機械的強度や硬さが高く、外部からの衝撃や摩耗に対して優れた耐久性を発揮します。
特にマルテンサイト系や析出硬化系ステンレス(例:SUS630)は熱処理によって高硬度化が可能で、構造材や刃物、バルブ部品などにも用いられています。
さらに、「高温下での耐酸化性」も特筆すべきポイントです。
多くのステンレス鋼は800℃程度までの高温環境でも酸化しにくく、熱交換器や排気システムなど熱の影響を受けやすい用途にも対応可能です。
逆に、アルミニウムは高温での強度が急激に低下するため、ステンレスが優位になります。
ステンレス鋼の欠点としては、「比重が重い」ことが挙げられます。
一般的なステンレスの比重は7.9程度で、アルミニウムの約3倍あり、軽量化が求められる用途には不向きです。
また、「加工性において難易度が高い」点も考慮が必要です。
切削や曲げ加工においては工具の摩耗が激しく、特別な加工条件や機械が必要になることがあります。
ステンレスは基本的に磁性を持たないオーステナイト系と、磁性を持つフェライト系・マルテンサイト系に分けられます。
用途や磁場の影響を考慮して、適切な系統の選定が重要です。
総じて、ステンレス鋼はその高い耐食性・強度・耐熱性により、信頼性と長寿命を求める用途で活躍します。
アルミニウムと比べると重く加工が難しい一方、過酷な環境下や衛生性が求められる現場では不可欠な材料です。
密度と重量の違い
アルミニウムとステンレスの大きな違いの一つが、密度、すなわち「重量の違い」です。
これは材料の選定や設計において非常に重要なポイントであり、特に軽量化が重視される分野では最初に検討される要素でもあります。
まず、密度の数値から比較すると、アルミニウムの密度は約2.7g/cm³です。
一方、ステンレス鋼(代表的なSUS304など)の密度は約7.9g/cm³です。
つまり、ステンレスはアルミニウムの約3倍の重さがあることになります。
これは、同じ体積の部品を作った場合、ステンレスの方が明らかに重くなるということを意味します。
この重量差は、実際の用途や構造物の設計に大きな影響を与えます。
たとえば、航空機や自動車など、移動体にとって「軽さ」は燃費や運動性能、積載力に直結します。
そのため、これらの分野ではアルミニウムが積極的に採用されています。
たとえば航空機の外板や骨格部材、自動車のボンネットやホイール、エンジンブロックの一部にまでアルミ素材が使用されています。
逆に、重量が重要ではない、もしくはある程度の「質量」が求められる場面ではステンレスの優位性が発揮されます。
たとえば、調理器具や実験機器などでは、ある程度の重みが安定性を生むため、ステンレスが好まれます。
また、建築資材などでも重厚感や堅牢性を出すために、あえてステンレスを選定するケースもあります。
ただし、密度の違いは単純に「重さの優劣」ではなく、「用途に応じた最適化」の観点から判断すべきです。
たとえば、ステンレスは密度が高いため、同じ重量でもアルミよりも体積が小さくなります。
結果として、剛性が高くなり、狭いスペースで高強度を実現しやすいという利点もあります。
また、重量が製造コストや輸送費に与える影響も見逃せません。
アルミニウムは軽量であるため、輸送中の燃料コストが抑えられるメリットがあり、特に大量輸送が求められる製品やグローバル輸出入が前提のビジネスにおいては、有利に働くことが多いです。
まとめると、密度の違いは以下のように分類されます。
材料 | 密度(g/cm³) | 特徴 |
---|---|---|
アルミ | 約2.7 | 非常に軽量、輸送や移動体に有利 |
ステンレス | 約7.9 | 重厚で剛性が高く、安定性に優れる |
このように、アルミとステンレスの密度・重量差は非常に大きな特性の違いであり、設計段階での材料選定において必ず考慮すべき重要な要素です。
機械的性質の違い
強度と硬さの比較
アルミニウムとステンレス鋼は、機械的特性において明確な違いがあります。
特に「強度」と「硬さ」の面では、両者の性質は用途を大きく左右するため、慎重な材料選定が求められます。
まず「引張強さ」から比較すると、一般的な純アルミニウムはおおよそ90~150MPa程度の引張強さしかなく、機械構造用としてはかなり低い部類に入ります。
これに対して、オーステナイト系ステンレス鋼(SUS304など)は約520MPa前後、マルテンサイト系や析出硬化系(SUS630など)では1000MPaを超えるものも存在し、非常に高強度な材料として知られています。
つまり、構造体として大きな荷重を支える必要がある場合には、ステンレスが圧倒的に有利です。
ただし、アルミニウムにも高強度タイプの合金があります。
例えばA7075やA2024といったジュラルミン系のアルミ合金は、熱処理と合金元素によって強化されており、引張強さは500~600MPa程度にまで達することがあります。
これにより、軽さとある程度の強度を両立した設計が可能になります。
特に航空宇宙分野ではこのような高強度アルミ合金が好んで使用されます。
次に「硬さ」の観点では、アルミニウムは相対的に柔らかい金属です。
ビッカース硬さ(HV)で言えば、純アルミは20~30HV程度しかありません。
これに対し、SUS304で150~200HV、SUS420のような焼入れ可能なマルテンサイト系ステンレスでは500HVを超えることもあります。
つまり、表面が傷つきにくく、摩耗に対しても強いのがステンレス鋼の大きなメリットです。
この硬さの差は、部品の寿命やメンテナンス頻度に直結します。
たとえば、摺動部や摩擦が生じやすい部品、あるいは衝撃が繰り返し加わるような部位には、ステンレスの方が優れた耐久性を示します。
逆に、アルミは柔らかいため、傷や変形が起きやすく、繰り返しの摩耗に弱いという欠点があります。
一方で、アルミは柔らかいからこそ、「靭性(じんせい)」や「変形しやすさ」においてはメリットとなる場合もあります。
衝撃を受けた際に割れにくく、変形することでエネルギーを吸収する性質があるため、軽量衝撃吸収材やクラッシャブル構造などに適しています。
総合的に見ると、強度と硬さを求めるならステンレス、軽さと一定の強度のバランスを重視するなら高強度アルミ合金が選ばれる傾向にあります。
最終的な用途や要求性能に応じて、両者の物性値を正しく把握し、最適な材料を選定することが、品質とコストの両立につながります。
加工性と成形のしやすさ
アルミニウムとステンレス鋼は、それぞれ異なる機械的特性を持ち、加工時の難易度や適した工程が大きく異なります。
製品の設計や製造コスト、製造時間に直結する「加工性と成形のしやすさ」は、素材選定の上で非常に重要な要素です。
まず、アルミニウムの加工性は非常に優れています。
アルミは柔らかく、延性が高いため、切削・曲げ・絞り・押出・鍛造といった多様な加工方法に対応しやすい素材です。
工具の摩耗が少なく、加工機械への負荷も軽いため、生産効率が良く、比較的低コストで加工が可能です。
また、熱伝導性が高いため、切削中の熱が分散しやすく、工具への局所的な熱集中も抑えられます。
これにより、アルミはCNC加工やプレス加工、薄板加工、建築材の押出成形など、多くの分野で重宝されています。
さらに、アルミは溶接も比較的容易です。
特にTIG溶接やMIG溶接との相性が良く、薄板でも割れにくいため、美観が要求される製品にも適しています。
ただし、酸化皮膜が自然発生しやすく、そのままでは溶接性を損なうため、事前の皮膜除去などの前処理は重要になります。
一方、ステンレス鋼の加工性は、アルミと比較するとやや劣る点が多いです。
ステンレスは硬く粘りがあり、切削加工時には工具の摩耗が早く進みます。
特にSUS304などのオーステナイト系ステンレスは、加工硬化しやすい特性を持つため、切削の際に切りくずが伸びて工具とワークの間に噛み込み、加工面が荒れることがあります。
そのため、切削条件や工具材質、潤滑剤などの選定が非常に重要です。
曲げ加工や絞り加工においても、ステンレスは弾性が強いため、スプリングバック(元に戻る力)が大きく、寸法精度を確保するのが難しいことがあります。
さらに、熱伝導率が低く、加工中に局所的な発熱が起こりやすいため、溶接や切断の際にも技術的な工夫が求められます。
溶接についても、ステンレスは高温での酸化による変色や腐食のリスクがあるため、適切なガスシールドや後処理(酸洗い・電解研磨など)が不可欠です。
とくに高品質な外観が求められる食品機器や医療機器では、こうした仕上げ処理が製品品質に直結します。
まとめると、「加工のしやすさ」ではアルミに軍配が上がり、「精度と仕上げ品質を高めるにはステンレスにはより高い加工技術が求められる」という構図です。
量産や軽作業向けであればアルミが適し、強度や耐久性が重視される部品ではステンレスが選ばれる傾向にあります。
摩耗性・耐衝撃性の違い
アルミニウムとステンレス鋼は、その物理的特性により、摩耗や衝撃への耐性において大きく異なる反応を示します。
製品の使用環境が過酷であるほど、これらの性能差が設計・選定の重要な判断材料となります。
まず、「摩耗性(耐摩耗性)」について比較します。
アルミニウムは、素材自体が柔らかく、表面硬度が低いため、摺動や繰り返しの摩擦によって摩耗しやすいという特性があります。
特に純アルミや比較的軟らかい合金では、摩擦部に使用すると短期間で傷や摩耗痕が生じやすく、寸法精度が維持しにくくなります。
そのため、摺動部などでは、表面にアルマイト処理(陽極酸化処理)を施すことで硬度と耐摩耗性を補強するのが一般的です。
ただし、アルマイト層は薄くて硬く割れやすいため、強い衝撃や繰り返し応力には注意が必要です。
一方、ステンレス鋼は、その種類にもよりますが、一般的に高い硬度と強靭性を備えており、摩耗に強い材料です。
とくにマルテンサイト系(SUS420など)や析出硬化系(SUS630など)は熱処理によって高硬度化が可能で、500HV以上の表面硬度を持つものもあります。
これにより、回転軸やベアリング部品、工具、摺動面などで高い耐摩耗性能を発揮します。
さらに、ステンレスは腐食と摩耗が同時に進行する「摩耗腐食」にも比較的強く、食品機械や薬品装置など衛生性が求められる現場でも長寿命を実現します。
次に、「耐衝撃性(衝撃荷重への耐性)」を比較します。
アルミニウムは硬度が低いため、ある程度の「靱性(じんせい)」を持っており、衝撃を受けても割れずに塑性変形する傾向があります。
たとえば、車両のクラッシャブルゾーン(衝突時に変形してエネルギーを吸収する部分)にはアルミが好んで使われる理由の一つです。
軽量であるがゆえに慣性力も小さく、衝撃そのものの影響も低減されやすいという副次的効果もあります。
これに対して、ステンレスは高強度かつ硬質な材料であるため、瞬間的な衝撃荷重に対しては非常に強く、変形しにくいという特長があります。
特に厚肉部材や高硬度ステンレスでは、衝撃に耐える強固な構造が求められる用途、例えば産業用機械部品、圧力容器、構造部材などに使用されています。
ただし、マルテンサイト系など一部のステンレスは脆性破壊を起こしやすいこともあるため、使用温度や応力条件には注意が必要です。
総合的に見ると、
・アルミ:衝撃を受けた際に「変形」でエネルギーを吸収。柔らかく、摩耗には弱い。
・ステンレス:高い表面硬度で摩耗に強く、衝撃にも強いが場合によっては割れやすい。
というように、軽さと靭性を重視するならアルミ、高硬度・耐摩耗・高強度を重視するならステンレスが適しているといえます。
使用目的に応じて、どちらの特性が優先されるべきかを明確にしたうえで素材を選定することが重要です。
耐食性と環境耐性の違い
アルミの耐食メカニズム
アルミニウムが幅広い用途で使用されている大きな理由の一つに、「耐食性の高さ」が挙げられます。
一見、柔らかく腐食に弱そうな印象を持たれることもありますが、実はアルミニウムは非常に優れた耐食特性を備えており、その仕組みは「自己修復性のある酸化皮膜の形成」にあります。
アルミニウムは空気中に露出すると、表面に「酸化アルミニウム(Al₂O₃)」の極めて薄い皮膜が自然に形成されます。
この皮膜はわずか数ナノメートルの厚さしかありませんが、非常に緻密で安定しており、内部の金属を外部の酸素や水分から保護する役割を果たします。
しかもこの皮膜は自己修復機能を持ち、物理的に傷がついても、再び酸素に触れることで速やかに再形成され、腐食の進行を抑えるのです。
この酸化皮膜によって、アルミニウムは水や湿気にさらされる環境でも比較的安定して使用できます。
特に大気中の酸素濃度が高い日本のような気候では、この皮膜の形成と再生が活発に行われるため、アルミは腐食に強い素材として認識されています。
ただし、耐食性は「環境条件によって大きく変化」します。
たとえば、アルミニウムは中性や弱酸性の環境では安定していますが、強酸・強アルカリ、または塩化物イオン(Cl⁻)が存在する環境下では皮膜が破壊されやすく、局所腐食(ピッティングやすきま腐食)を引き起こすリスクがあります。
特に、海水や塩化カルシウムなどの塩分が存在する場所では、アルミの耐食性は著しく低下する可能性があるため注意が必要です。
また、異種金属と接触することで起こる「ガルバニック腐食(異種金属腐食)」にも弱い傾向があります。
アルミニウムは電位的に比較的卑な金属であるため、たとえば鉄やステンレスと直接接触し、電解質(湿気や水)が存在する状況では、アルミの方が優先的に腐食してしまう現象が起こります。
これを防ぐためには、異種金属間に絶縁材を挟んだり、防食処理を施すことが一般的です。
このようなリスクを抑えつつ耐食性をさらに高める方法として有効なのが、「アルマイト処理(陽極酸化処理)」です。
この処理では人工的に厚くて硬い酸化皮膜を形成し、耐食性・耐摩耗性を格段に向上させることができます。
また、着色も可能なため、外観的な美しさを求める建材やインテリア用途にも適しています。
総合的に見て、アルミニウムは「自然に形成される酸化皮膜」と「軽量・非鉄金属であること」が相まって、優れた耐食性を実現している素材です。
しかし、その耐食性能を最大限に活かすためには、使用環境や組み合わせる他素材との相性、表面処理などを十分に考慮することが欠かせません。
ステンレスの耐食メカニズム
ステンレス鋼の最大の特徴の一つが、その非常に優れた耐食性です。
この耐食性を支えているのが、表面に自然に形成される「不働態皮膜(ふどうたいひまく)」と呼ばれる、クロムを主成分とする酸化被膜です。
この被膜こそが、ステンレスが他の鋼材に比べて著しく錆びにくい理由です。
ステンレス鋼には最低でもクロム(Cr)が10.5%以上含まれており、これが空気中の酸素と反応して、表面に極めて薄く緻密な酸化クロム(Cr₂O₃)の皮膜を形成します。
この皮膜は「不働態(passive)」という状態にあり、金属表面を外部からの酸素や水分、化学物質の侵入から守る役割を果たします。
さらに、この不働態皮膜は「自己修復性」を持っています。表面が物理的に傷ついた場合でも、周囲に酸素が存在すれば再び皮膜が形成されるため、腐食の進行を防ぐことができます。
これはアルミニウムの酸化皮膜と同様のメカニズムですが、ステンレスの不働態皮膜はより耐薬品性・耐久性に優れ、酸性・アルカリ性を含む広範な環境で使用が可能です。
また、クロムに加えてモリブデン(Mo)やニッケル(Ni)などを添加することで、さらに高い耐食性能を持たせたグレードも存在します。
たとえばSUS316は、モリブデンを含むことで、塩化物イオン(Cl⁻)に対する耐性が向上し、海水や塩素系薬品を扱う環境でも使用可能となっています。
一方で、ステンレスも万能ではありません。特定の条件下では腐食が進行することがあります。
代表的なのが以下の3つです。
・孔食(ピッティング):塩化物が皮膜を局部的に破壊することで、点状に深く腐食が進む現象。
・すきま腐食:ボルトやガスケットの下など、酸素の供給が不十分なすきま部分で局所的に皮膜が壊れ腐食が進む現象。
・応力腐食割れ(SCC):引張応力と腐食環境が重なった場合に亀裂が発生し、破断に至る現象。
これらの腐食現象は、環境条件(温度、湿度、化学物質の存在など)やステンレスの種類によって発生しやすさが異なります。
したがって、用途に応じたステンレス材の選定が極めて重要です。
たとえば、厨房機器ではSUS304が広く使われますが、海水が関与する設備ではSUS316が選ばれるといった使い分けがなされています。
さらに、ステンレスの耐食性を維持するためには、表面仕上げの質も大きく影響します。
鏡面研磨やバフ研磨により表面を滑らかにすると、汚れがつきにくく、腐食因子が滞留しにくくなります。
逆に、粗い表面や加工キズがあると、そこが腐食の起点となることがあります。
総じて、ステンレスの耐食性は、素材の成分、表面状態、使用環境の3要素のバランスによって最適化されるものです。
不働態皮膜による高耐久性と自己修復能力は、他の金属では得られない大きな特長であり、厳しい環境での長寿命化・メンテナンス性の向上に貢献しています。
屋外使用や腐食環境での使い分け
屋外や腐食性の高い環境において、アルミニウムとステンレスのどちらを選定するべきかは、単に「耐食性が高いか否か」ではなく、使用環境の特性・コスト・メンテナンス性・美観維持の難易度など、さまざまな要素を総合的に判断する必要があります。
以下、それぞれの素材の特徴をふまえて、使い分けの考え方を解説します。
■ 一般的な屋外環境
たとえば住宅の外装材、雨どい、フェンスなどにおいては、アルミニウムもステンレスも高い耐候性を発揮します。
アルミは自己酸化皮膜により風雨や紫外線にさらされても錆びにくく、表面にアルマイト処理を施すことでさらなる保護と美観の両立が可能です。
軽量で施工性も高いため、大量使用や高所での取り付けにも適しています。
一方、ステンレス(特にSUS304)は、長期にわたって外観を保ちつつ高い耐食性を維持できるため、高級感を求めるエクステリア製品や公共施設などでも多用されます。
ただし、塩分や工業排気が多い場所では、SUS304でも表面にもらい錆(他の鉄成分が付着して発生する錆)が出ることがあり、定期的な清掃が必要です。
■ 海沿い・高塩分環境
海沿いの地域や冬季に融雪剤(塩化カルシウム)が散布されるような場所では、アルミニウムよりもモリブデンを含有するSUS316などの高耐食ステンレスが推奨されます。
アルミは塩化物イオンに弱く、ピッティング(孔食)が起こりやすくなるため、未処理では数年で腐食が進行するリスクがあります。
アルミを使用する場合は、耐塩害アルマイトやフッ素樹脂系の表面処理を施すことで対応できますが、完全な耐久性を求めるにはステンレスの方が有利です。
ただし、SUS316は価格が高いため、予算や使用年数とのバランスを考えることが重要です。
■ 工場・薬品を扱う環境
酸性・アルカリ性ガス、化学薬品が存在する環境では、素材の耐薬品性が鍵となります。
一般的なアルミはアルカリに極端に弱く、また酸にも影響されやすいため、化学的な耐性には限界があります。
一方、ステンレス鋼はグレードによって薬品耐性が異なり、SUS316LやSUS317L、二相ステンレスなど、用途に応じた選択肢が用意されています。
このため、食品工場・医薬品製造設備・下水処理場などでは、ステンレスが主に採用されます。
耐食性に加えて洗浄性や衛生性も求められるため、ステンレス表面にはバフ研磨や電解研磨などの仕上げ処理が施されるのが一般的です。
■ 美観やデザイン性が重要な場面
建築意匠やインテリア、デザイン性を重視した什器などでは、どちらの素材も使用されます。
アルミは軽量で光沢があり、アルマイトによるカラーバリエーションが豊富です。
一方、ステンレスは重厚感があり、鏡面仕上げからヘアライン加工まで多彩な表面仕上げが可能で、高級感や清潔感を演出できます。
美観を長期に保ちたい場合は、環境に応じて仕上げ処理の選定が重要です。
たとえば、ステンレスはヘアラインよりも鏡面の方が汚れが付きにくく、またアルミも硬質アルマイト処理で耐傷性が向上します。
総合的に言えば、
環境 | 推奨素材 | 補足 |
---|---|---|
一般的な屋外 | アルミ or SUS304 | 軽さとコストならアルミ、高級感と耐久性ならSUS |
海沿い・高塩分 | SUS316 | アルミは劣化しやすい。SUS316は高コストでも高耐久 |
工場・薬品環境 | ステンレス(SUS316L等) | 耐薬品性と洗浄性で圧倒的優位 |
美観重視の建築 | 両方可 | アルマイトと鏡面・ヘアライン仕上げの使い分け |
といったように、使用目的や設置場所に応じて、アルミとステンレスを最適に使い分けることが、長期的な製品価値や維持コストの最小化に繋がります。
熱と電気に対する特性
熱伝導性と放熱性の違い
アルミニウムとステンレス鋼は、熱伝導性において大きな違いがあり、これが材料選択の際に重要なポイントとなります。
特に電子機器の放熱部品やヒートシンク、熱交換器など、熱の伝達や放散が求められる用途では、両者の熱特性を正しく理解することが不可欠です。
アルミニウムの熱伝導性
アルミニウムは金属の中でも熱伝導率が非常に高く、約200~240 W/m·K(ワット毎メートル・ケルビン)という数値を持っています。
これは銅に次ぐ良好な熱伝導率であり、熱を効率よく拡散・伝達できるため、熱管理が重要な製品に広く用いられています。
軽量で加工しやすいという特性に加え、この高い熱伝導性が相まって、パソコンのCPUクーラーやLED照明の放熱フィン、電子機器の筐体などに最適です。
アルミは熱を素早く伝え、放熱面積を増やすことで効果的に熱を逃がすことができるため、熱膨張に伴うトラブルを減らす役割も果たします。
ステンレス鋼の熱伝導性
一方で、ステンレス鋼の熱伝導率は約15~25 W/m·Kと、アルミの約10分の1以下に留まります。
これはステンレスが鉄を主成分としており、合金元素や不純物の影響で電子の移動が制限されるためです。
この低い熱伝導率は、逆に言えば熱が伝わりにくく局所的に熱がこもりやすいということです。
そのため、放熱性が要求される用途では不利になります。
熱交換器のパイプ材や電子機器の冷却部材として使われることは少なく、熱の局所過熱を防ぐためには設計上の工夫や冷却システムの併用が必要です。
しかし、ステンレスは高温に強く、800℃を超えるような過酷な熱環境でも耐酸化性を保つため、熱伝導性よりも耐熱性や耐久性が重視される場面では選ばれます。
たとえば排気管や高温炉の部材などが代表例です。
放熱性能の実用面での差異
実際の放熱性能は、熱伝導率だけでなく、形状や表面積、設置環境、空気の流れなど複数の要因に左右されます。
しかし、素材の熱伝導率が低いと、放熱設計で効率的な熱拡散が難しくなり、熱が滞留する可能性が高まります。
そのため、電子機器や精密機械の冷却部品には、熱伝導率の高いアルミニウム合金が主に使われています。
軽量かつ加工性が良いため、複雑な放熱フィンの成形も可能で、高性能の放熱設計が実現できます。
まとめると、
材料 | 熱伝導率 (W/m·K) | 放熱性の特徴 |
---|---|---|
アルミニウム | 約200~240 | 高熱伝導率で効率良く熱を拡散・放熱可能 |
ステンレス鋼 | 約15~25 | 低熱伝導率で熱がこもりやすいが耐熱性に優れる |
このように、放熱性能を重視する設計にはアルミニウムが適しており、高温耐久性が重要な用途にはステンレスが選ばれる傾向があります。
耐熱性と高温特性の比較
アルミニウムとステンレス鋼は、耐熱性や高温環境での特性においても大きな違いがあります。
これらの違いは、材料の選定において、特に熱負荷の大きい機器や構造物の設計で非常に重要な要素となります。
アルミニウムの耐熱性
アルミニウムは軽量で加工性が良い一方で、熱に対する耐性は比較的低い金属です。
アルミの融点は約660℃ですが、実際には200~300℃程度の高温になると機械的強度が急激に低下し、変形や強度低下を引き起こします。
このため、熱を多く発生するエンジン周辺部品や高温環境での構造材には、アルミは基本的に適しません。
加えて、熱膨張率が高いため、高温から冷却時の収縮が大きく、設計上の寸法管理や応力管理に注意が必要です。
ただし、一部の特殊アルミ合金は耐熱性を高めるために合金元素が添加されており、短時間の高温使用に耐えられるものもあります。
しかし、長時間の高温環境では、アルミニウムは避けられることが多いです。
ステンレス鋼の耐熱性
一方、ステンレス鋼は優れた耐熱性を持ち、特にクロム含有により表面に形成される不働態皮膜が高温でも酸化や腐食を防ぎます。
多くのステンレス鋼は約800℃程度までの連続使用に耐えることが可能で、フェライト系、オーステナイト系などグレードによってさらに耐熱特性が異なります。
たとえば、オーステナイト系ステンレス(SUS304やSUS316)は約900℃まで耐熱性を示し、一時的には1000℃以上でも使用可能なことがあります。
これにより、ボイラー部品、排気管、化学プラントの高温配管、耐熱容器などに広く用いられています。
また、析出硬化系ステンレスは高温強度に優れ、航空機部品やタービン部品など、過酷な温度条件下で高強度を維持するために使われます。
熱膨張と機械的安定性
熱膨張率については、アルミニウムの方が高く(約23×10⁻⁶ /℃)、ステンレス鋼(約10~17×10⁻⁶ /℃)よりも熱による寸法変化が大きいです。
これは、高温での寸法安定性が求められる構造物では、アルミの使用が難しい理由の一つです。
機械的な安定性もステンレスの方が優れており、高温環境下でも強度を比較的よく保持します。
アルミは高温で軟化・変形しやすいため、高温負荷がかかる用途には不向きです。
まとめ
特性 | アルミニウム | ステンレス鋼 |
---|---|---|
融点 | 約660℃ | 約1400~1450℃ |
実用耐熱温度 | 200~300℃(強度低下が顕著) | 800℃前後(グレードにより異なる) |
熱膨張率 | 約23×10⁻⁶ /℃ | 約10~17×10⁻⁶ /℃ |
高温強度 | 低い(軟化しやすい) | 高い(強度維持が良好) |
用途例 | 一般的な構造材以外は限定的 | 高温配管、排気系、耐熱容器など |
以上のように、耐熱性や高温での強度維持が求められる場合はステンレス鋼が圧倒的に有利であり、アルミニウムは低温~中温環境に適しているといえます。
熱膨張率と寸法安定性の比較
材料の熱膨張率とは、温度変化に伴う材料の長さや体積の変化率を示す重要な物理的特性です。
アルミニウムとステンレス鋼では、この熱膨張率に大きな違いがあり、特に寸法精度や機械部品の組み合わせ、熱サイクルを繰り返す環境での使用に影響を及ぼします。
アルミニウムの熱膨張率
アルミニウムは比較的熱膨張率が高く、平均して約23×10⁻⁶ /℃(23ppm/℃)程度です。
これは、温度が1℃上昇すると、1メートルの長さの材料が約23マイクロメートル伸びる計算になります。
高い熱膨張率は、温度変化が激しい環境では材料の寸法が大きく変動することを意味し、機械的なクリアランスや組み立て部品の隙間に影響を与えます。
例えば、電子機器の筐体や精密機械にアルミ部品を用いる場合、温度上昇による寸法変化を考慮しないと、熱膨張によって接触不良や機械的応力が発生することがあります。
また、異なる材料と組み合わせた際の熱膨張率の差異による「熱応力」が発生し、材料間の剥離や亀裂、ゆがみの原因となることもあります。
ステンレス鋼の熱膨張率
一方、ステンレス鋼の熱膨張率は合金の種類によりやや異なりますが、一般的には約10~17×10⁻⁶ /℃(10~17ppm/℃)の範囲です。
これはアルミの約半分から3分の2程度の値であり、同じ温度変化でもアルミより寸法変化が小さいことを意味します。
熱膨張率が低いことは、温度変化による寸法変動が小さく、機械部品の精度や組み合わせの安定性に寄与します。
特に高温環境下や繰り返しの熱サイクルが加わる場合、寸法変化を抑制できることは耐久性や信頼性の向上につながります。
寸法安定性と設計上の影響
寸法安定性が高いほど、製品の動作精度や寿命が長くなる傾向があります。
アルミの場合は熱膨張率が高いため、設計段階で熱変形を見越したクリアランス調整や熱膨張を抑制する構造設計が必要です。
たとえば、アルミ部品同士を組み合わせる場合、温度変化による膨張を考慮しないと部品が干渉し、変形や破損の原因になることがあります。
また、異素材(例:ステンレス、銅、樹脂など)との接合部では、熱膨張率の差異が大きく応力集中や剥離を引き起こすリスクがあるため、熱膨張差に耐えられる設計や接合方法の工夫が不可欠です。
一方ステンレスは、熱膨張率が比較的低く、熱による寸法変動が抑えられるため、精密機械や高温設備での使用に適しています。
また、熱応力が小さいことから異種材料との組み合わせでもトラブルが起きにくいというメリットがあります。
まとめ
特性 | アルミニウム | ステンレス鋼 |
---|---|---|
熱膨張率 (ppm/℃) | 約23 | 約10~17 |
寸法変化量 | 大きい | 小さい |
寸法安定性 | 低め(熱膨張による影響大) | 高め(温度変化に強い) |
設計上の配慮 | 熱膨張を考慮したクリアランス設計が必要 | 熱応力対策は比較的容易 |
以上のように、温度変化がある環境での寸法精度や耐久性を重視する場合はステンレス鋼が有利ですが、軽量性や加工性を優先する場合はアルミニウムの使用も十分に検討されます。
両者の特性を理解し、設計段階で適切に対処することが重要です。
アルミやステンレスの試作品の見積り依頼ならアスクへ
試作品や小ロットの加工も大歓迎!
特に手のひらサイズの部品製作を得意としています。
アスクなら、試作品のお見積もりが最短1時間で可能!!
お気軽にお問い合わせください。
試作全国対応!
簡単・最短1時間お見積り
他、ブログ記事もご覧ください♪
動画の投稿もしておりますので良ければご覧ください♪