5軸加工?高精度・高効率の最先端加工技術とは
本日は5軸加工機について、記事を書いていきたいと思います!
製造業に携わっている方であれば当たり前のことかもしれないですが、本日もお付き合いください♪
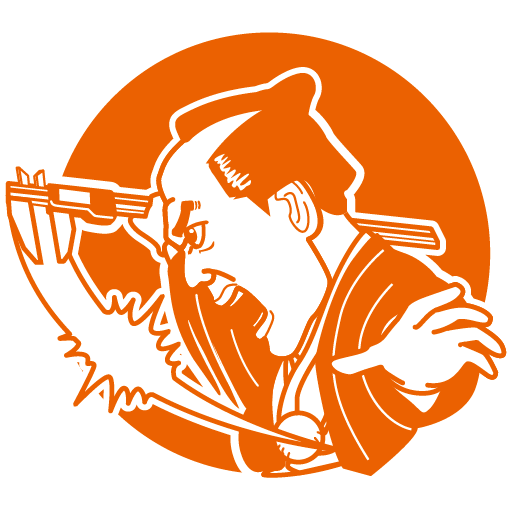
5軸加工機とは
5軸加工とは、工具や加工物が5つの方向に動く加工方法です。
通常の3軸加工は、X軸(左右)、Y軸(前後)、Z軸(上下)の3方向にしか動けませんが、5軸加工ではこれに加えて2つの回転軸(A軸・B軸またはC軸)が加わり、工具をいろいろな角度に傾けながら加工できます。
たとえば、A軸はX軸まわりに回転、B軸はY軸まわり、C軸はZ軸まわりの回転を指します。
これらを組み合わせることで、複雑な曲面や裏側の加工(アンダーカット)も可能になります。
例として、オークマの「MUシリーズ」やマキノの「Dシリーズ」などがあり、高精度な5軸加工が航空機部品や金型製作などで活用されています。
5軸加工には、「同時5軸加工」と「割出し5軸加工」の2種類があります。
同時5軸加工は5つの軸を同時に動かしながら加工するため、自由度が高く滑らかな形状を削るのに向いています。
一方で割出し5軸加工は、加工する前に角度を設定し、加工中はその角度で固定する方法です。
5軸加工機の種類
テーブル回転型
ワーク(加工物)を載せるテーブル自体が回転するタイプの5軸加工機です。
X軸・Y軸・Z軸の直線的な動きに加えて、テーブルがA軸(X軸まわりの回転)やC軸(Z軸まわりの回転)で動くことで、ワークの姿勢を変えながら多方向から加工できます。
特にテーブルが回転することで、加工対象を固定したまま複数の面にアクセスでき、段取り替えが最小限で済むため、加工精度の向上や作業時間の短縮に貢献します。
テーブル回転型は比較的小型の構造で、工作機械全体の剛性を確保しやすいという特徴があります。
そのため、精密部品や医療用部品、時計部品など、サイズが小さく高精度が求められる加工に向いています。
また、機械の構造が比較的シンプルで導入コストも抑えられる傾向があるため、5軸加工の入門機としても適しています。
一方で、大きなワークや重量のあるワークをテーブルで回転させるのは物理的に難しくなるため、サイズや重量に制限があるのがデメリットです。
ワークサイズが大きい場合は、後述するヘッド回転型や複合型が検討対象になります。
例として、DMG森精機の"CMX U"シリーズやファナックの"ROBODRILL 5軸仕様"などがテーブル回転型の代表格として知られており、小型高精度加工を支える現場で活用されています。
ヘッド回転型
ヘッド回転型の5軸加工機は、工具を保持するヘッド部分が回転する構造になっています。
これにより、工具がさまざまな角度に傾けられるため、複雑な形状や曲面の加工に対応しやすくなります。
特に、大型のワーク(加工物)や重量のあるワークの場合、テーブルを動かすのが難しいため、ヘッド側を動かすことで効率的に加工できます。
ヘッド回転型は、航空機や自動車の大きな部品、または産業用装置のフレームなど、大型で精度が求められる場面で活躍します。
また、テーブルに重いワークを固定したまま加工ができるため、段取りが安定しやすく、精度の確保にもつながります。
ただし、ヘッドが回転するためには、構造的に複雑になりやすく、機械自体の剛性をしっかり保つ必要があります。
そのため、機種によっては導入コストがやや高めになる場合もあります。
複合型
テーブルとヘッドの両方が回転する複合型の5軸加工機は、あらゆる方向から工具をアプローチさせることができるため、最も高い自由度を持っています。
これにより、極めて複雑な形状や深いアンダーカット、曲面形状なども高精度に加工することが可能です。
たとえば、航空宇宙産業におけるエンジン部品や翼の内部構造、あるいは医療用インプラントなど、複雑で精密な仕上がりが求められるワークには非常に有効です。
テーブルがワークの角度を調整し、同時にヘッドが最適な工具姿勢を保つことで、切削条件を常に最良の状態に保つことができ、加工時間の短縮や工具寿命の延長にもつながります。
ただし、この複合型は構造が非常に複雑であるため、工作機械としての設計・製造コストが高くなりがちです。
また、制御系も高度である必要があるため、専用のNC装置や高性能なソフトウェアが不可欠です。
メンテナンス面でも専門性が求められ、運用には十分な知識と経験が必要となります。
しかし、それらのハードルを超えてもなお、精度・効率・柔軟性を最大限に高められる点で、複合型5軸加工機は最先端の製造現場において欠かせない存在となっています。
3軸加工との違い
3軸加工では、工具の動きがX軸(左右)、Y軸(前後)、Z軸(上下)の3方向に限定されているため、加工できる形状に限界があります。
特に、部品の裏側を削るような「アンダーカット」や、斜めの角度がついた面、複雑な曲面、さらにはワークの深い位置にある穴など、工具がまっすぐに届かないような部分の加工は非常に困難になります。
例えば、金型の内部にある深く入り込んだ部分や、航空機の部品に多い流線型の構造などは、3軸加工では一方向からのアプローチしかできず、細部にアクセスするためには何度もワークの固定を変える必要があります。
この「段取り替え」は、加工の都度、ワークを取り外して新たな角度にセットし直す作業を意味し、加工の手間が大幅に増える要因となります。
また、段取り替えによって、元の位置と新しい位置のズレが生じやすく、微細な寸法誤差や工具の干渉、加工面の段差などの不具合が発生するリスクも高まります。
とくに精度が求められる医療機器や航空部品では、これが致命的な問題になることもあります。
加えて、工具の向きが限定されているため、切削面に対する接触角度が最適でない状態になりやすく、切削効率が下がったり、工具にかかる負荷が増えたりします。
その結果、工具の摩耗が早くなり、工具交換の頻度も上がってコストがかかるという悪循環に陥ることも。
このように、3軸加工では形状的・工程的に限界が多く、複雑形状や高精度が求められる製品の加工には向かない場面があるのです。
こうした課題を解消するために、より自由な角度からのアプローチが可能な5軸加工の必要性が高まっているのです。
5軸加工のメリット
角度の自由が利く
5軸加工では、通常のX・Y・Zの直線的な動きに加えて、回転軸(A軸・B軸・C軸)を利用して工具をあらゆる角度に傾けられます。
これにより、複雑な形状のワークでも一度の段取り(ワンチャック)で全体を加工できるのが大きな特徴です。
たとえば、3軸加工では工具が真上からしかアプローチできないため、ワークを何度も固定し直す必要があり、そのたびに誤差が出やすくなります。
しかし5軸加工では、工具を斜め方向や側面からも自由に当てられるため、アンダーカットや深い溝、傾斜面など、難しい形状でも高精度に加工することが可能です。
また、角度調整が柔軟にできることで、工具の先端だけでなく、側面を効果的に使った切削も実現できます。
これにより、切削条件を最適化しやすく、加工時間の短縮や工具摩耗の軽減にもつながります。
たとえば、航空機のタービンブレードのように、流体力学的に複雑な曲面を持つ部品では、5軸加工の自由な角度制御が不可欠です。
実際にオークマやマキノ、DMG森精機といったメーカーの高性能5軸マシニングセンタでは、航空・宇宙、自動車、医療などの現場でこうした複雑加工が日常的に行われています。
このように、回転軸を活用して工具の角度を自在に制御できることは、5軸加工の大きなメリットであり、生産性と精度の両立に大きく貢献しています。
高精度な加工と工具の負担軽減
5軸加工では、工具がワークに対して常に最適な角度で接触することが可能になります。
この「最適な角度」とは、切削に最も適した姿勢を保ちながら加工を行うという意味であり、工具の刃先や側面を効率よく使える状態です。
たとえば、3軸加工では工具が常に垂直にワークへ当たるため、角度によっては無理な力が加わってしまい、切削時に大きな抵抗が発生します。
これにより工具に負荷がかかり、早期の摩耗や破損の原因になります。
一方5軸加工では、工具をワークの曲面や傾斜面に対して斜め方向から接近させることができ、無理のない切削姿勢を保つことができます。
その結果、切削負荷が軽減されるだけでなく、刃先の摩耗が均一になり、工具寿命が延びるのです。
また、切削中の振動やびびり音が抑えられることで、加工面の仕上がりも滑らかになります。
さらに、摩耗が少ないということは、工具交換の頻度も少なくなるということです。
これにより機械の停止時間が減り、全体の生産効率が向上します。
加えて、工具の長寿命化は消耗品コストの削減にも直結します。
このように、工具が最適な姿勢でワークに接することが可能な5軸加工は、工具負担の軽減、加工品質の向上、そしてコスト削減に貢献する非常に効率的な技術なのです。
時間とコストを削減
5軸加工では、ワーク(加工物)を何度も固定し直す「段取り替え」の回数が大幅に減少します。
3軸加工では、ワークの各面を加工するために何度も位置を変えて固定し直す必要があり、そのたびに手間や時間がかかります。
固定するごとに位置ズレのリスクもあるため、精度管理にも苦労します。
一方、5軸加工では一度ワークを固定すれば、工具を様々な角度に傾けながら連続して加工できるため、1回の段取りで複数の面を一気に削ることが可能です。
この段取り作業の簡略化は、作業者の負担軽減にもつながり、熟練技術に依存しすぎずに安定した生産ができるというメリットもあります。
また、加工の時間短縮に直結するため、製品1個あたりの加工サイクルが短くなり、生産スピードが大きく向上します。
さらに、段取りや加工時間の短縮は、製造コストの削減にも大きな影響を与えます。
加工機が停止している時間が減るため、生産ラインの稼働率が高くなり、機械の効率的な運用が可能になります。
また、工具の摩耗も少ないため、工具交換や調整にかかるコストも抑えることができます。
結果として、5軸加工は工程全体の効率化とともに、製造にかかる無駄を最小限にし、時間とコストの両面で大きなメリットをもたらします。
ソフトと制御の力で5軸を使いこなす
5軸加工の性能を最大限に引き出すためには、機械そのものの性能だけでなく、「ソフトウェア」と「制御技術」の力が欠かせません。
ここでは、5軸加工を支える裏方の仕組みについて、解説していきます。
CAMソフトの役割
5軸加工では、CAD(設計データ)から実際に加工を行うためのプログラムを作る「CAMソフト」が重要な役割を果たします。
CAMとは「Computer Aided Manufacturing(コンピュータ支援製造)」の略で、複雑な形状や動きに対応した工具パス(加工ルート)を自動的に作成するソフトです。
特に5軸加工では、工具の傾け方や干渉回避など多くの要素を考慮する必要があるため、高性能なCAMソフトが必要になります。
代表的なソフトには「Mastercam」や「hyperMILL」、「NX CAM」などがあり、これらを使うことで効率的かつ正確な加工プログラムの作成が可能になります。
工具の姿勢制御
5軸加工では、工具の角度(姿勢)を自由に制御できるのが大きな特徴です。
しかし、その角度をどうやって決めるのか? それを自動的に計算してくれるのがCAMソフトや制御ソフトの力です。
たとえば、ある曲面を加工する場合、工具の刃先が常に最も効率よく、かつ安全な角度で接触するように姿勢を調整する必要があります。
これを「工具の姿勢制御」と呼び、5軸加工の品質や工具寿命に大きく関わってくるポイントです。
適切な姿勢制御ができれば、工具への負荷が減り、滑らかで美しい切削面が得られます。
また、干渉のリスクも減らせるため、トラブルの少ない加工が実現できます。
NC制御とポストプロセッサの役割
CAMソフトで作成した加工プログラムを、実際の機械が動かすためには、数値制御(NC)の命令形式に変換する必要があります。
これを担うのが「ポストプロセッサ」という仕組みです。
ポストプロセッサは、使用する機械や制御装置に合わせて加工データを最適な形に変換する翻訳機のような存在です。
5軸加工では特に、回転軸の動きや工具の姿勢など複雑な命令が多いため、機械ごとに細かな設定が必要になります。
この設定がしっかりしていないと、加工中に誤作動を起こしたり、仕上がりにズレが生じたりする可能性があるため、信頼性の高いポストプロセッサの構築が非常に重要です。
シミュレーションで安全・確実に!
5軸加工は自由度が高い分、動きが複雑になりがちです。
そのため、事前に「加工シミュレーション」を行うことで、安全かつスムーズに加工できるかどうかをチェックすることが大切です。
シミュレーションソフトでは、工具やワークの動きを画面上で再現し、衝突や干渉の可能性、加工ミスなどを事前に発見できます。
これにより、現場でのトラブルを未然に防ぎ、安全性と効率を両立した加工が実現できます。
特に高価なワークや高精度が求められる部品では、一度の失敗が大きな損失につながるため、シミュレーションはもはや必須のプロセスといえます。
5軸加工の未来
応用分野の広がり
航空機や医療、自動車、精密部品など、今後も高精度が求められる分野で活用が進みます。
スマート工場との連携
AIやIoTと組み合わせて、加工の状態をリアルタイムで管理し、より自動化・高品質な製造が可能になります。
5軸加工とAIの連携による革新
近年、AI技術の進化により、5軸加工の効率と精度がさらに向上しています。
AIは、過去の加工データやセンサーデータを分析し、最適な加工条件や工具の姿勢、送り速度、回転数などをリアルタイムで提案・制御することが可能です。
これにより、加工中の異常検知や工具摩耗の予測、さらには不良品の発生リスクの低減にもつながっています。
たとえば、AIが振動や音、温度といったセンサーデータを常時モニタリングし、「このままだと工具が摩耗して破損する可能性がある」と判断すれば、事前に工具交換を指示したり、加工条件を自動で調整したりします。
また、熟練技術者が行っていた工具の選定や加工条件の最適化をAIが支援することで、経験の浅い作業者でも高品質な加工が可能となります。
さらに、AIによる学習型最適化は、1つのワークだけでなく、複数の異なる形状に対しても柔軟に対応できます。
従来は人が都度プログラムを調整していた作業を、AIが自動化することで、段取り時間の短縮や少量多品種生産への対応力も大きく向上しています。
このように、AIと5軸加工の連携は、ものづくりの現場において「より速く、より正確に、より効率的に」加工を行うための重要な要素となっており、今後の製造業の競争力強化に不可欠な技術となっています。
ハイブリッド加工技術
切削と3Dプリントを組み合わせた新しい加工法が登場し、5軸加工と融合することで可能性がさらに広がっています。
人材育成の重要性
5軸加工には専門知識やスキルが必要です。教育や研修による人材育成がカギとなります。
持続可能な製造へ貢献
これからの製造業においては、環境への配慮も欠かせないテーマです。
5軸加工は、段取り回数の削減や工具寿命の延長によって無駄を減らし、エネルギーや資材の使用効率を高めることができます。
さらに、精密加工によって不良品の発生も抑えられ、資源のロスを最小限にとどめることができます。
今後は、こうした省エネ・省資源の視点からも、5軸加工の技術がますます注目されるようになるでしょう。
5軸加工の見積り依頼ならアスクへ
試作品や小ロットの加工も大歓迎!
特に手のひらサイズの部品製作を得意としています。
アスクなら、試作品のお見積もりが最短1時間で可能!!
お気軽にお問い合わせください。
試作全国対応!
簡単・最短1時間お見積り
他、ブログ記事もご覧ください♪
動画の投稿もしておりますので良ければご覧ください♪