ブラスト仕上げとは?特徴や用途など徹底解説!
本日はブラスト仕上げについて解説していきます。
特徴や用途、メリット・デメリットなど解説しますので、是非ご覧ください♪
ブラスト仕上げとは
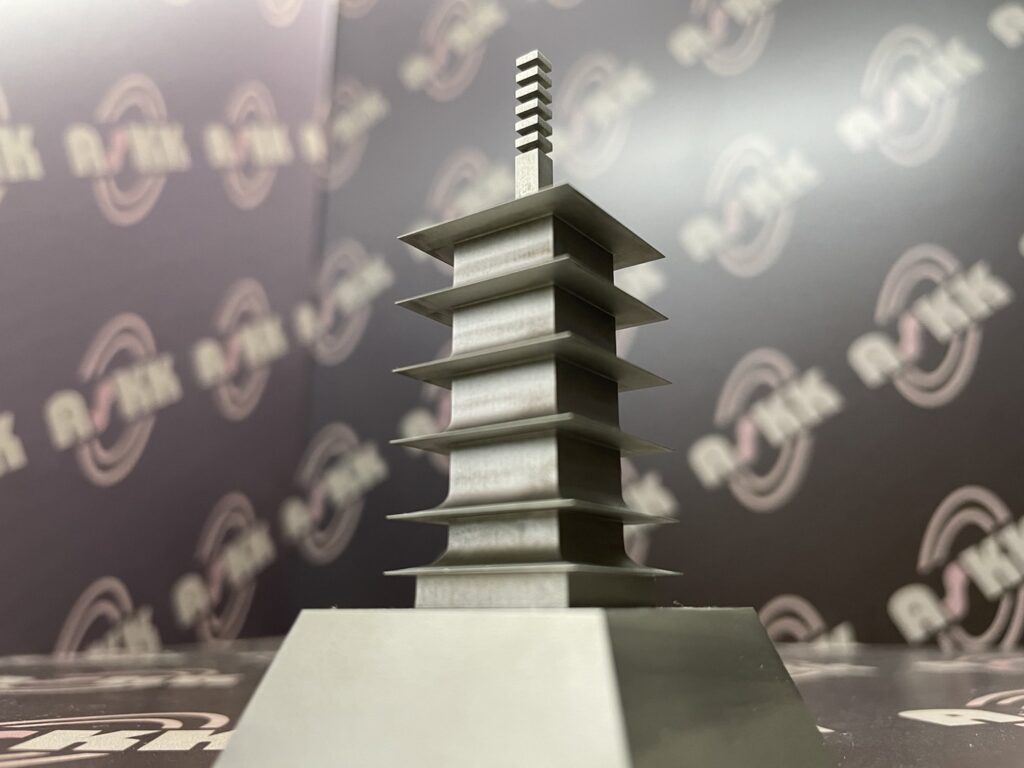
ブラスト仕上げとは、様々な種類の粒子を素材に衝突させることで、素材表面の状態や性質を変化または向上させる仕上げ方法のことです。
表面処理の一種で、その製作方法を指してブラスト加工やショットブラストと呼んだり、仕上げ後の表面性状を指して梨地仕上げと呼んだりします。
その目的は、表面を滑らかな鏡面にすることではなく、表面に硬質な素材を吹き付けることで凹凸を形成して、機能性や意匠性を付与したり、研磨剤を吹き付けて研磨やバリ取りを行ったり、軟質な粒子を吹き付けて清浄したりすることです。
対象となる素材は、金属をはじめ、プラスチックやガラスなどと幅広くなっています。
対象となる形状についても制限は少なく、その他の表面処理では加工が難しい複雑に入り組んだ形状や、狭い溝の奥などを加工することが可能です。
ブラスト加工の投射材
対象物に衝突させる粒子は、投射材(ブラスト材)と呼ばれますが、投射材に用いられる粒子と言っても、その材質は以下のように多種多様です。
・金属(鋳鉄、鋳鋼、ステンレス、銅、亜鉛、アルミ、アルミ合金、アルミナ[AI203]など)
・セラミック(ジルコン[ZrSiO4]、炭化ケイ素[SiC]など)
・ガラス
・樹脂(メラミン樹脂、ユリア樹脂、ナイロン樹脂、ポリカーボネートなど)
・植物(胡桃殻、トウモロコシ芯、桃の種など)
・その他(ドライアイス、重曹など)
金属やセラミックは粗い仕上がりとなりますが、セラミックは、投射対象を錆びつかせないという特徴があります。
ガラスや樹脂、植物は、投射対象を傷つけにくく、滑らかな仕上がりが期待できる投射材です。
ドライアイスは投射後に気化するため、投射対象の表面に残留することがなく、回収・廃棄も不要というメリットがあります。
投射材の形状も以下のように多様で、投射対象の材質や投射方法、用途に応じて使い分けられます。
・ショット・・・球状粒子
・グリット・・・多角形粒子
・カットワイヤー・・・線材を細かく切断したものやその角を丸めて粒子状としたもの
・ビーズ・・・穴のあいた球状粒子
・パウダー・・・粉状としたもの
ショットやグリットは、鉄鋼によく採用される形状で、鉄鋼製のショットやグリッドを「スチールショット」や「スチールグリット」と呼びます。
グリットの方が研削能力に優れますが、ショットの方が品質にばらつきがなく、仕上がりにムラがありません。
カットワイヤーは、ステンレスや非鉄金属に主に採用される形状で、ステンレスなどの硬質な材質であれば仕上がりは粗く、アルミなどの軟質な材質であれば仕上がりは滑らかになります。
ビーズは、主にガラスに採用される形状で、材質がガラスの場合はガラスビーズと呼びます。
ガラスビーズは、特に美しく滑らかな仕上がりが期待できる投射材で、投射対象を傷つけにくく、汚染することもありません。
パウダーも、ガラスによく採用される形状で、ガラスパウダーはガラスビーズを粉砕して作られます。
ガラスビーズよりも研削力があり、模様付けなどに適しています。
ブラスト加工の投射方法
投射材を対象物へ衝突させる方法には、以下のようなバリエーションがあります。
機械式ブラスト
扇風機の羽根車(インペラー)と同様の機構によって、インペラーに乗せた投射材を回転の遠心力で叩きつける方法です。
エネルギー効率が良く、重い投射材に対応しています。
広範囲に大量の粒子を投射できるため、対象物全体を均一に加工することが可能です。
ただし、投射範囲を制御することが難しく、特定の部位のみを加工することは難しくなっています。
エアー(乾式)ブラスト
投射材を圧縮空気で吹き付ける方法です。
機械式と比較してエネルギー効率が悪く、広範囲の投射には向いていません。
しかしながら、投射条件の細やかな設定が可能で、投射範囲や投射速度、投射材に使用する粒子の種類などの自由度が高くなっています。
ピンポイントに投射することも可能で、文字に沿って加工することもできます。
ウエット(湿式)ブラスト
水などの液体と投射材の混合液を圧縮空気で噴射する方法です。
乾式のように投射材が飛散しないことから、粉塵爆発の危険性がなく、粉塵を吸引・除去する集塵機が不要であるという利点があります。
微細な粒子から粗大な粒子までと、使用できる粒子サイズの幅が広く、小物・大物・広範囲などと多様な加工に対応可能です。
液体を含むため、投射材や汚れなども投射と共に流されます。
つまり、加工と洗浄を同時に実施することができます。
ただし、液体に浮かぶ投射材は使用できず、水気に弱い素材には使うことができません。
ブラスト仕上げの用途
装飾用
ブラスト仕上げの一つの用途に、素材表面の意匠性を高める装飾があります。
ブラスト仕上げは、素材表面に「梨地」と呼ばれる、梨の肌のように見える無数の凹凸を形成します。
梨地と言っても、その外観は多様で、凹凸が目立つものから、凹凸は目につかないが色合いが異なるもの、元の金属にマット感を出して高級感を持たせたもの、元の金属のツヤをわずかに消した半光沢のものまで存在します。
このような梨地のバリエーションは、投射材や投射方法、投射条件などを変えることで実現できます。
ブラスト仕上げは、装飾用として、建築や自動車、造船、鉄道、電子部材などの外観部材・部品に適用されています。
その適用品は、例えば、建築物の内装品として天井・階段周り・エントランス・家庭や店舗の様々な什器(器具や家具)、スマートフォンの筐体などに用いられています。
また、ブラスト仕上げは、投射方法によっては素材表面の限定された部分に適用することができるため、文字を描いたり、デザインに沿って模様を付けたりすることもできます。
この用法では、表札や看板などで採用されています。
バリ取り
ブラスト加工は、金属や樹脂などの加工時に発生するバリと呼ばれる意図しない突起物の除去にも用いられています。
バリは、加工品の固定や計測などに不備を招くとともに、作業者にケガや事故を引き起こします。
ブラスト加工であれば、細かなバリをまとめて取り除くことが可能であり、バリ取り工具が届かない部分のバリも除去できることがあります。
この用途では、ブラスト加工は、金属加工や樹脂加工などの成形加工後に用いられることが多くなっています。
サビ取り・塗装前処理・塗装はがし
ブラスト加工は、さび落としや塗装前処理、塗装はがしなどにもよく用いられています。
ブラスト加工は、素材表面に付着した錆びや汚れなどを物理的に除去することが可能です。
熱処理工程で素材表面に発生するスケールや黒皮といった酸化被膜の除去にも用いられます。
薬品などを使用しないため、対象物の材質に依ることなく除去することができます。
ブラスト加工は、塗装やメッキ、コーティングなどの前処理として実施される下地処理としても有用です。
それは、サビや汚れの除去効果のほか、塗料などの薬剤が素材表面の隙間に侵入して固まる「アンカー効果」が期待できるからです。
これらの効果によって、塗装やメッキ、コーティングなどの密着性が向上するとともに、外観も良くなります。
防錆効果も長続きするため、張替えや補修までの期間が延びて、結果的にコスト削減につながります。
ブラスト加工は、塗装やメッキ、コーティングの張替えの前に必要となる塗装はがしやメッキはがしなどにも利用することができます。
ただし、めっきは密着性が高いため、重く硬い投射材や強力に投射できる設備などが必要となります。
このような下地処理のためのブラスト加工は、建築や造船、自動車、家電、調理器具などの部材・部品に適用されています。
橋梁やビルの風雨にさらされる箇所の部材、船舶の骨材、デジタルカメラの筐体、テフロン加工前のフライパンなど、巨大な構造物から身近な製品まで、幅広く有効活用されています。
クリーニング
ブラスト加工は、製品・半製品の表面をクリーニングする用途でも用いられます。
上述したように、ブラスト加工は、対象物の表面に付着した錆びや汚れ、加工油、材料カスなどを取り除くことができます。
錆が浮いてきた塗装やめっき、機能が低下したコーティングなどもはがすことが可能で、そのまま下地処理を実施することができます。
クリーニングは薬品で行う事も可能ですが、清浄と剥離とで薬品が異なっていたり、薬品に漬け込む時間が必要だったりと、物理的かつ瞬時に清浄・剥離が可能なブラスト加工に比べると、使い勝手は良くありません。
また、近年では、投射材にドライアイスを使ったブラスト加工もよく用いられるようになっています。
その方法は、ドライアイス洗浄と呼ばれ、粉塵回収が不要となっています。
ブラスト加工のクリーニング対象としては、加工途中の半製品や完成品のほか、金型や鋳物、機械設備などと多様です。
使い古した自動車のエンジンやシャーシ、ポンプ、スクリューなどを再生することもできます。
機能の付与
ブラスト加工は、以下の機能を付与するために適用されることもあります。
・滑り止め・・・素材表面の凹凸が滑り止め効果を発揮します。
例:ドアノブなど。
・反射抑制・・・素材表面の凹凸によって光が乱反射するため、光沢(艶)は失われ、反射が抑制されます。
例:建築物の屋根や外壁、エクステリアなど。
特性の向上
また、ブラスト加工は、以下の特性向上を目的に適用されることもあります。
・美観の向上・・・素材表面に凹凸を形成することで、傷を消す効果があるほか、傷が目立たない表面性状とすることもできます。
例:食器や外観部品など。
・放熱性の向上・・・素材表面に形成した凹凸によって表面積が増大し、外気との接触面が増加して放熱性が向上します。
例:ボイラー管やバイクのシリンダーなど
・保油性の向上・・・素材表面に形成した凹凸によって表面積が増大し、油分を捉えやすくなります。
例:潤滑油を使用する摺動部品など。
・機械的性質の向上・・・金属の表面に高硬度の投射材を強くぶつけると、表面が加工硬化を起こすため、耐摩耗性や疲労強度が向上します。
例:刃具や工具、機械部品など
ブラスト仕上げの特徴
加工法が物理的
ブラスト加工は、対象物に投射材を物理的に当てることで、表面に荒らす・削る・磨くなどの加工を行ったり、表面の付着物を取り除いたりする表面処理方法です。
粉塵対策が必要となりますが、薬品や有機溶剤はもちろん、研削加工で必要となる研削油のような油剤も不要です。
加工力が一定
ブラスト加工の加工力は、投射材として選定した粒子の性質と形状、質量、速度で決まります。
また、ブラスト加工では、粒子が一回対象物に衝突すると、それ以上の加工力を発揮することはありません。
したがって、一つ一つの粒子が対象物に与える加工力は常に一定となります。
ただし、対象物の同一部品に多くの粒子が衝突すると、その部分に加工力が蓄積するので、粒子は対象物の全面に均一に当てるようにしなければなりません。
加工面に方向性がない
ブラスト加工では、対象物へ粒子が一定の加工力でランダムに衝突するため、表面に形成される構造は、方向性がないランダムな凹凸となります。
この点、研磨加工は、ブラスト加工と同じ物理的な表面処理ですが、加工面に筋目が形成されて方向性を持つため、異なる特徴を示すと言えるでしょう。
なお、化学的な表面処理であれば、対象物を溶液に浸漬して皮膜を張る化成処理など、加工面に方向性がないものがあります。
投射材や投射方法、投射条件によって仕上がりが変わる
ブラスト加工では、投射材として選定した粒子の性質や質量、形状、サイズ、速度などの違いによって、対象物の仕上がりは大きく変化します。
つまり、投射材や投射方法を選定し、投射条件を設定することで、対象物に現れる効果を制御できます。
材質に関係なく加工できる
ブラスト加工は、粒子を対象物に直接衝突させる加工法であるため、金属やセラミックス、ガラス、石材、樹脂、木材など、対象物の材質に関係なく加工することができます。
ただし、ブラスト加工による仕上がりは、対象物の硬度などといった機械的性質に依存するため、対象物の材質に合わせて投射材や投射条件などを調整する必要があります。
様々な形状の対象物を加工できる
ブラスト加工は、多様な形状の対象物に対応することが可能です。
例えば、研磨加工では加工が難しい溝の奥などでも、粒子が吹き出すノズル(投射口)との射線が通っていれば加工できます。
ブラスト加工には、自動加工用の装置と手動加工用の装置、双方の手段に対応している装置がありますが、手動加工用であれば、ノズルを自由に取り回し、ノズルを溝や穴などに差し込んで加工するといったことも可能です。
ブラスト仕上げのメリット
・材質に関係なく加工できる
・複雑な形状でも加工できる
・方向性のない加工面を形成できる
・多様な外観を実現できる
・様々な効果を付与できる
・様々な特性を向上させることができる
・薬品を使用しない表面処理法であるため、環境負荷が比較的小さい
なお、加工面が無方向性であれば、密着性能なども均一となるため、その加工面の上に張った塗膜が一定方向からのひっかきには弱いといったことも起こりません。
ただし、加工面が必ずしも無方向性となるわけではなく、粒子を一定方向から加工面に沿って投射するなどすれば、加工面に方向性をつけることができます。
ブラスト仕上げのデメリット
・全面に粒子を当てる必要があるため、表面積が大きくなるほど加工時間が増大する
・対象物の厚さや形状によっては、ブラスト加工による圧力で対象物が伸びてしまったり、曲がりや歪みが生じたりする場合がある
・投射材によっては、粒子の流路となるノズルなども加工してしまうため、部品の摩耗が早く、定期的な交換が必要となる
・投射方法が乾式の場合、加工時に粉塵が発生するため、集塵機が必要となる
・金属製の投射材は錆びることがあるため、管理やメンテナンスが必要となる
・投射材が錆びている場合、加工対象に錆がうつってしまうことがる
・投射物や削りくずなどが残留することがある
ブラスト加工が可能な素材
ブラスト加工は、投射材や投射方法、投射条件を適切に選ぶことで、以下に例示するような素材も含め、材質にかかわらず適用できる表面処理です。
スチール
鋼のことを指すスチールは、塗装やめっきの前に実行する下地処理としてブラスト加工がよく採用されます。
スチールは、強度や加工性に優れていますが、サビやすい素材でもあるため、防錆効果のある塗装やメッキ等を施して使用することがほとんどです。
そのため、塗装やメッキ等の防錆効果を向上させ、寿命を延ばす効果があるブラスト加工は、スチールに対する表面処理として有用です。
これらの効果に加えて、ブラスト加工は、バリ取りやクリーニングといった役割も同時に担うことができます。
ステンレス
鋼の一種であるステンレスは、美観の向上や反射抑制などを目的にブラスト加工が施されています。
強度と耐食性に優れたステンレスは、外観部材や外観部品によく用いられている素材です。
そこで、鏡面仕上げやヘアライン仕上げと並ぶ、表面装飾の一つのパターンとして、ブラスト加工による梨地仕上げが採用されることがあります。
ただし、ブラスト加工を適用すると、ステンレスの高耐食性を実現している不動態被膜が失われてしまうため、塗装やメッキ、不動態皮膜の再生処理などが必要となります。
アルミ
アルミニウムは、美観の向上や反射抑制、滑り止めなどを目的にブラスト加工が施されています。
アルミニウムは、軽量な割に耐久性が高く、加工性や耐食性にも優れるため、民生用や業務用にかかわらず様々な用途で用いられている素材です。
ブラスト加工は、アルミニウム製の外観部品や外観部材によく適用されており、建築物の天井・階段周り・エントランスといった内装品や、ノートパソコン・デジタルカメラといったデジタル家電の筐体などに見ることができます。
ただし、アルミニウムもまた、ステンレス同様、不動態皮膜が耐食性の要となっているため、ブラスト加工後は不動態被膜の再生が必要です。
アルミニウムでは、この不動態被膜を分厚く形成するアルマイト処理を施すことがありますが、ブラスト加工がまんべんなく適用されていないと、色むらが発生するので注意が必要です。
ブロンズ
青銅のことを指すブロンズには、主に装飾用途でブラスト加工が適用されています。
ブロンズは、十円玉や高級家具の金属部品、像やモニュメントなどによく用いられており、光沢がある高級感のある素材として知られています。
ブラスト加工は、このブロンズにさらなる高級感を出したり、デザインとして質感を変えたりすることを目的に施されます。
投射材などの選択によって色調を変えることもできるので、意匠性を重視するブロンズには有用な表面処理法となっています。
チタン
チタンは、装飾や美観の向上を目的にブラスト加工が適用されています。
チタンは、軽量かつ丈夫で耐食性も際立って高い、高品質な金属です。
しかし、素材自体が高価であるため、装飾品や費用対効果がある生体材料などに主に用いられています。
チタンに対するブラスト加工の適用例としては、装飾品のほかに、印鑑や高級感・意匠性が重要視されるホテルや美術館などの建築部材が挙げられます。
試作全国対応!
簡単・最短1時間お見積り
他、ブログ記事もご覧ください♪
動画の投稿もしておりますので良ければご覧ください♪