表面粗さについての基本知識を解説します!
本日は表面粗さについて解説していきます!
基本知識となることを順に紹介していきますので、是非ご覧ください♪
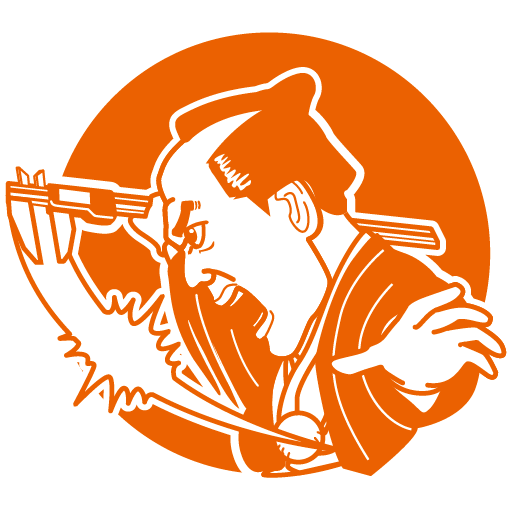
表面粗さとは
表面粗さとは、物体の表面に存在する微小な凹凸の程度を数値的に表したものです。
これらの凹凸は、製造工程や使用環境によって生じるものであり、製品の性能や耐久性に大きな影響を及ぼすことがあります。
表面粗さは、一般的に数ミクロン(μm)単位の非常に微細なレベルで測定され、見た目には滑らかに見える表面でも、拡大すると凹凸が存在していることがわかります。
表面粗さの評価は、単なる「見た目のきれいさ」を超えて、部品の機能や信頼性と密接に関係しています。
たとえば、摺動部品では、粗すぎると摩耗が激しくなり、逆に滑らかすぎても潤滑油が保持できずに性能が低下することがあります。
また、接着や溶接のように他部材との密着性が必要な場合にも、適切な粗さが重要です。
表面粗さは、表面の高さ変化を一定の方法で測定して評価されます。
通常、基準線(平均線や基準面)からの高さのずれを統計的に処理して数値化します。
代表的な指標には「Ra(算術平均粗さ)」や「Rz(最大高さ)」などがあります。
これらの数値によって、表面がどれくらい滑らかであるか、またどれほどの微細な凹凸を持っているかがわかります。
ただし、表面の状態は粗さだけで決まるわけではなく、波形の周期や形状、さらには方向性(例えば加工痕の筋目の方向)なども重要です。
そのため、「表面性状(surface texture)」という言葉が用いられることもあり、これは粗さだけでなく、うねりや形状誤差なども含んだ広い概念です。
表面性状の中で最も基本的な評価項目が表面粗さであると理解しておくとよいでしょう。
製造業においては、表面粗さは図面に明示される重要な仕様項目の一つであり、加工技術者や品質管理担当者にとって避けて通れない知識です。
表面粗さを適切に管理することは、製品の長寿命化、信頼性向上、品質向上につながります。
表面性状との違いと関係
表面性状(ひょうめんせいじょう)とは、物体表面の微細な形状の総体を指す用語であり、「表面粗さ」を含むより広い概念です。
多くの現場では「表面粗さ=表面の状態」と単純に理解されることもありますが、正確には、表面性状は以下の3つの要素で構成されており、それぞれ異なる意味と役割を持ちます。
1つ目は表面粗さ(surface roughness)で、これは表面上の微細な凹凸を表します。
数μm単位での凹凸を測定対象とし、短い測定長さの中で発生するランダムな起伏を指します。
たとえば、切削や研磨などによって発生する微小な加工痕やざらつきなどが該当します。
表面粗さは、Ra(算術平均粗さ)やRz(最大高さ)などのパラメータによって評価され、部品の機械的な機能や外観品質に直接関係します。
2つ目はうねり(waviness)で、粗さよりも長い周期で現れる緩やかな起伏を指します。
うねりは、工具の振動、加工機のたわみ、材料の内部応力などに起因することが多く、ミリメートル単位の起伏となる場合もあります。
うねりが大きいと、接触面での密着性が低下したり、光の反射が乱れて見た目にムラが生じることもあります。
3つ目は形状誤差(form error)です。
これは、設計上の理想的な幾何形状(直線、円、平面など)からのズレを指します。
たとえば、本来フラットであるべき面が凸に膨らんでいたり、真っ直ぐなはずのエッジがわずかに曲がっていたりする状態です。
形状誤差は、測定範囲全体にわたる大きなズレであるため、測定や評価には三次元測定機やプロファイラなどの高精度機器が用いられます。
これら3つの要素は互いに独立しているわけではなく、実際の表面では同時に存在し、重なり合っています。
たとえば、粗さが小さくても、うねりが大きければ部品の機能に悪影響を与える可能性がありますし、逆もまた然りです。
そのため、表面の総合的な状態を評価するためには、「表面性状」という包括的な視点が欠かせません。
図面で表面性状を指定する際には、一般的に粗さパラメータ(RaやRz)が中心ですが、高精度な製品ではうねりや形状誤差も設計条件として明示されることがあります。
特に精密機器や光学部品、自動車部品などでは、表面性状の管理が製品性能に直結するため、測定・評価の精度も非常に重要になります。
製造現場においては、「粗さだけでは不十分である」という認識が徐々に浸透してきています。
今後、より高性能・高信頼性が求められる分野では、「表面性状のトータルマネジメント」がますます重要となるでしょう。
表面粗さが与える機能的影響(摩擦・密着性・疲労強度など)
表面粗さは、製品の外観だけでなく、機能性にも大きな影響を与えます。
特に重要なのが、摩擦係数、密着性、疲労強度、腐食耐性といった性能への影響です。
これらの特性は、機械部品の寿命や動作の信頼性、安全性に直結するため、製品設計や加工の際に十分な配慮が必要です。
■ 摩擦と摩耗への影響
摩擦係数は、表面同士が接触して滑る際の抵抗を示しますが、表面粗さが粗いと、接触面積が不均一になり、局所的な圧力が高くなります。
これにより、摩耗が激しくなったり、異音が発生したりする可能性があります。
たとえば、摺動部品(シャフト、スライド、ベアリングなど)では、粗すぎる表面は摩擦を増大させ、発熱やエネルギーロスの原因になります。
一方で、滑らかすぎる表面では、潤滑油が保持されにくくなる「油膜切れ」の問題も起こり得ます。
そのため、用途に応じて最適な粗さを選定することが必要です。
■ 密着性・接着性への影響
接着や塗装、溶接といった「表面に別の材料を密着させる処理」では、適切な表面粗さが重要です。
粗すぎると、気泡や隙間が入り込んでしまい密着不良を起こすことがありますが、逆に滑らかすぎると、接着剤や塗料がしっかりと食い込まず、剥がれやすくなる場合があります。
適度な粗さがあることで「機械的結合」が形成され、密着力が高まるのです。
この効果を意図的に利用するために、接着前にサンドブラストやショットピーニングで表面を粗くする工程が設けられることもあります。
■ 疲労強度への影響
表面粗さは、金属材料の疲労強度にも密接に関わります。
表面に凹凸があると、その谷部が「応力集中」の起点となり、繰り返し荷重がかかることで微小な亀裂が発生しやすくなります。
この亀裂は徐々に成長し、最終的には破断に至ることもあります。
たとえば、自動車や航空機の構造部材、回転軸などの部品では、疲労破壊のリスクを避けるため、表面を鏡面に近いレベルまで仕上げる場合もあります。
■ 腐食のリスクにも関係
表面が粗いと、微細な凹みに水分や薬品、塩分などが残留しやすくなり、腐食が局所的に進行する「点腐食(ピッティング)」の原因となることもあります。
特に、ステンレスなどの耐食性材料でも、表面が粗いと保護皮膜が不均一になり、腐食が始まりやすくなるため注意が必要です。
医療機器や食品機械のように衛生環境が求められる分野では、表面粗さの管理は極めて重要です。
このように、表面粗さは見た目の滑らかさ以上に、製品の機能性、耐久性、安全性に直結する重要な要素です。
設計段階から使用条件に応じた粗さを指定し、それを確実に実現・管理することが、信頼性の高い製品づくりに欠かせません。
表面粗さの測定方法
接触式測定器と非接触式測定器の違い
表面粗さを正確に評価するためには、適切な測定器の選定が欠かせません。
表面粗さの測定方法は大きく分けて「接触式測定器」と「非接触式測定器」の2種類があり、それぞれに特徴と適用シーンがあります。
ここでは、その違いについて詳しく解説します。
■ 接触式測定器とは
接触式測定器(Contact-type Surface Roughness Tester)は、ダイヤモンドなどの硬質なスタイラス(触針)をワークの表面に接触させ、一定の速度でスライドさせながら、表面の凹凸を機械的にトレースして測定します。
代表的な機器には「表面粗さ計(サーフテスト)」があります。
測定原理としては、触針の上下動を高精度な変位センサで検出し、Ra(算術平均粗さ)やRz(最大高さ)などの粗さパラメータを算出します。
機器によっては、結果を数値だけでなくプロファイル(断面図)として可視化することも可能です。
利点:
・高精度で安定した測定が可能
・多くの規格(JIS、ISO、DINなど)に準拠した評価ができる
・表面の形状を実線で可視化できる
欠点:
・接触により微細な傷がつく可能性がある
・測定に時間がかかる
・凹凸が複雑な部品や柔らかい素材の測定には不向き
■ 非接触式測定器とは
非接触式測定器(Non-contact Surface Roughness Tester)は、レーザーや白色干渉、共焦点顕微鏡などの光学技術を用いて、物理的な接触なしに表面の凹凸を測定する方法です。
3D測定器や白色干渉計、レーザー顕微鏡などが代表例です。
測定原理は機器によって異なりますが、表面からの反射光の位相差や反射強度を利用して、高速かつ高解像度で表面形状をデジタル的に再現します。
結果は数値だけでなく、3次元画像やカラー断面図として表示されるため、視覚的にも理解しやすい特徴があります。
利点:
・ワークに傷をつけることなく測定可能
・測定が高速かつ広範囲で可能
・微細加工やナノレベルの凹凸評価に適している
欠点:
・材質や表面の反射特性に測定結果が影響されやすい
・機器の価格が高くなりがち
・測定結果が接触式と一致しない場合がある(評価基準の違い)
■ 選定のポイント
どちらの測定方式を使うかは、ワークの材質や形状、求められる精度、用途により判断されます。
たとえば、一般的な金属部品の量産検査では、信頼性が高くコスト効率に優れる接触式測定器が好まれます。
一方、超精密加工部品、光学部品、樹脂などの微細・柔らかい素材には、非接触式測定器が適しています。
また、近年では両方式を併用することで、より総合的かつ信頼性の高い測定を行う企業も増えています。
このように、接触式と非接触式の測定器にはそれぞれ明確な特性と利点があります。
目的やコスト、精度要件をふまえて、最適な測定方法を選定することが、正確な品質評価と安定した製品づくりにつながります。
主な測定パラメータ(Ra, Rz, Ryなど)とその意味
表面粗さを定量的に評価する際には、さまざまなパラメータが用いられます。
代表的な粗さ指標には「Ra」「Rz」「Ry」などがあり、それぞれの数値が示す意味を正しく理解することが重要です。
ここでは主なパラメータの定義と用途、注意点について解説します。
■ Ra(算術平均粗さ)
Raは、最も一般的に使われる表面粗さの指標です。
正式には「算術平均粗さ」といい、測定範囲内のプロファイルの中心線からの絶対偏差の平均値を表します。
言い換えると、表面の凸凹の高さを平均的に評価する数値です。
数式的には、測定長さLにおけるプロファイルの高さy(x)の絶対値の積分平均で表されます。
Raの値が小さいほど表面が滑らかであることを意味し、一般的に部品の外観や摩擦性能の評価に用いられます。
ただし、Raは凸部と凹部の振れ幅を平均化してしまうため、鋭いピークや深い谷を表現しきれない欠点もあります。
■ Rz(最大高さ)
Rzは「10点平均粗さ」とも呼ばれ、プロファイル上の最大の5つの凸部の高さと最大の5つの凹部の深さの平均値を足したものです。
つまり、粗さのピークと谷の最大振れ幅を重視した指標です。
Raに比べて表面の極端な凹凸を反映しやすいため、工具の刃先の摩耗や加工不良などによる局所的な荒れを把握するのに適しています。
一般的に、RaとRzはセットで評価されることが多いです。
■ Ry(最大高さ)
Ryは測定範囲内のプロファイルで観察される最大の凸部と凹部の高さの合計を示します。
言い換えれば、その区間で一番高い山の頂点と一番低い谷底の差を表しています。
Ryは表面の極端な欠陥や傷の有無をチェックするのに用いられますが、部分的な凹凸の影響を大きく受けやすいため、製品の一般的な粗さを評価する目的ではあまり単独で用いられません。
■ その他のパラメータ
・Rq(2乗平均粗さ):Raの二乗平均で、凸凹の振幅が大きい部分をより強調する。
・Rsk(歪度):プロファイルの形状の左右対称性を示し、凹凸の偏りを評価。
・Rku(尖度):プロファイルのピークの鋭さや尖り具合を示す。
これらのパラメータは、特殊な用途や高精度の品質管理で利用されます。
■ パラメータ選定のポイント
製品の用途や求められる機能によって、適切な粗さパラメータは異なります。
たとえば、軸受けなど滑らかな摺動面ではRaが主に使われ、鋳造品や切削加工の粗さ管理ではRzも併用されることが多いです。
また、複数のパラメータを組み合わせて評価することで、表面状態の全体像をより正確に把握できるため、単一の数値だけで判断せず、目的に応じて最適な指標を選ぶことが重要です。
表面粗さのパラメータは単なる数値ではなく、加工方法の評価や製品性能の予測、品質保証に欠かせない指標です。
正しい理解と活用が、製造工程の改善や製品の信頼性向上につながります。
表面粗さ測定の注意点と測定環境
表面粗さの測定は、製品の品質管理や工程改善に欠かせない工程ですが、測定を正確かつ安定して行うためにはいくつかの注意点と適切な測定環境が必要です。
この項目では、測定時に気を付けるポイントや環境条件について詳しく解説します。
■ 測定の再現性と安定性
表面粗さ測定は非常に微細な凹凸を計測するため、測定者の操作や機器の設定によって結果がばらつくことがあります。
再現性を確保するためには、測定条件の統一が重要です。
例えば、測定位置の選定は同一箇所を狙うことが望ましく、複数回測定して平均値を取ることも効果的です。
機器のキャリブレーション(校正)も定期的に行い、信頼性を保ちましょう。
■ 測定環境の影響
温度や湿度、振動などの外部環境が測定精度に影響を与えます。
特に接触式測定器は微細な力でスタイラスを表面に接触させるため、周囲の振動がノイズとなりやすいです。
測定はできるだけ振動の少ない専用の測定台や環境で実施し、温度変動が少ない安定した環境下で行うことが推奨されます。
また、埃や汚れの付着も測定結果に影響を与えるため、ワーク表面は清掃してから測定しましょう。
■ 測定範囲と走査長さの選定
表面粗さ測定は「測定範囲(走査長さ)」によって結果が変わる場合があります。
走査長さが短すぎると、局所的な凸凹のみを捉えてしまい、全体の粗さを代表しない結果となります。
逆に長すぎると、表面の波状や形状の影響が大きくなり、純粋な粗さ評価からずれることがあります。
一般的にはJISやISOなどの規格で推奨される走査長さを守ることが重要です。
例えばJIS B0601では、粗さ測定に対し複数の標準的走査長さが設定されています。
■ ワークの固定と取り扱い
測定対象物はしっかりと固定し、測定時に動かないようにします。
動くと測定精度が大幅に低下し、データの信頼性が損なわれます。
接触式の場合は特にスタイラスの押し込み量(測定力)も一定に保つ必要があります。
柔らかいワークや曲面の測定では、スタイラスの損傷やワークの変形に注意しましょう。
■ 表面処理や加工の影響
塗装、メッキ、研磨などの表面処理が施された部品は、素地の粗さだけでなく処理層の状態が測定に影響します。
表面処理層が薄い場合は素地の粗さが反映されますが、厚い場合は処理層の粗さが測定値に大きく影響するため、測定目的を明確にしておくことが重要です。
表面粗さ測定は単なる数値取得だけでなく、測定環境や条件の管理、適切な測定手順の徹底が製品の品質管理に直結します。
日常的な測定の中でこれらのポイントを意識することで、安定した高精度な評価を実現できます。
表面粗さの改善方法
加工条件の最適化による改善
表面粗さは、加工条件の調整によって大きく改善できる要素の一つです。
加工方法に関わらず、切削速度や送り速度、工具材質や刃先形状、クーラントの使用条件などが表面状態に直接影響します。
ここでは、加工条件を見直すことで表面粗さを向上させる具体的なポイントを紹介します。
■ 切削速度(切削条件)の調整
切削速度(回転数や送り速度)は、表面粗さに大きな影響を与えるパラメータです。
一般的に、切削速度を上げすぎると工具の摩耗が早まり、表面に傷が入りやすくなります。
一方、速度が遅すぎると切りくずが滑らかに排出されず、むしろ表面に悪影響を及ぼす場合もあります。
適正な切削速度は、被削材の材質、工具の材質・形状、加工方法などにより変動します。
例えば、アルミニウムのような軟質材料は比較的高い切削速度で仕上げることで、滑らかな表面を得られます。
逆に、硬質材では切削速度を抑えて安定した加工を行うことが重要です。
■ 送り速度と切込み量
表面粗さを良くするには、送り速度(1回転当たりの移動量)を小さくすることが効果的です。
送り速度が大きいと、工具の刃跡が荒くなり、うねりが生じやすくなります。
反対に、送りを小さく設定することで、より平滑な表面が得られます。
切込み量も同様で、深すぎると工具に負荷がかかって振動が生じやすくなり、表面粗さが悪化します。
特に仕上げ加工では、浅く、安定した切込みで加工するのが基本です。
■ 工具の材質・形状の選定
工具の摩耗や損傷は、直接的に表面粗さを悪化させる要因です。
仕上げ加工においては、耐摩耗性の高い超硬工具やコーティング工具を選ぶことで、工具寿命の延長とともに良好な仕上げ面を維持しやすくなります。
また、刃先のR(丸み)を持たせた工具を使うことで、滑らかな仕上げ面が得られることもあります。
逆に尖った刃先では、バリや傷が発生しやすくなるため、粗加工と仕上げ加工で工具を使い分けることも表面品質向上のポイントです。
■ クーラントと潤滑の活用
切削時の発熱は、加工面の酸化や変質、工具摩耗の促進などにつながり、結果として表面粗さの悪化を招きます。
クーラントを適切に使用することで、切削熱の抑制と切りくずの排出を助け、滑らかな表面を実現できます。
特にアルミ材などは切りくずの付着による「ビルドアップエッジ(刃先への凝着)」が起こりやすいため、潤滑性の高いクーラントを選定し、適切な流量で供給することが重要です。
加工条件の最適化は、比較的コストをかけずに表面粗さを改善できる手段です。
ただし、他の要素とのバランスを考慮し、トライアンドエラーで最適値を探る姿勢も重要です。
量産現場では、工程内でのバラつきを抑えるためにも、安定した加工条件の管理と記録が求められます。
工具選定や摩耗管理による改善
表面粗さの品質を安定して向上させるには、加工条件の最適化に加えて、使用する工具の選定とその管理が極めて重要です。
工具はワークと直接接触して加工を行うため、その性能や状態が表面の仕上がりを大きく左右します。
この項目では、表面粗さ改善のために考慮すべき工具の選定ポイントや摩耗管理の手法について解説します。
■ 表面粗さと工具の関係
工具の刃先がワーク表面に直接作用するため、刃の状態が表面粗さに直結します。
新しい、または適切に管理された工具は切れ味が良く、安定した切削が可能であるため、滑らかでムラの少ない加工面を得られます。
しかし、摩耗が進行した工具を使用すると、切削時に微細なバリやビビリ(振動)が発生しやすくなり、表面に微小な凹凸が残る原因となります。
したがって、工具の摩耗度合いを適切に管理することは、加工品質の維持に不可欠です。
■ 工具選定のポイント
表面粗さを重視する加工では、使用する工具の種類や材質も重要です。
以下にいくつかの選定ポイントを挙げます。
・工具材質:超硬工具は高い硬度と耐摩耗性を備え、仕上げ加工に適しています。また、ダイヤモンドコーティング工具やCBN(立方晶窒化ホウ素)工具は、アルミや硬質合金などの高精度加工において有効です。
・刃先形状:R付きの刃先や多刃工具を使用することで、切削時の仕上がりが均一になり、表面の凹凸が抑えられます。特に仕上げ専用の工具は、滑らかな面を得るために最適化された設計が施されています。
・コーティング:TiAlNやDLC(ダイヤモンドライクカーボン)などのコーティングは、工具の表面に潤滑性や耐摩耗性を持たせ、長寿命化と加工面の滑らかさ向上に貢献します。
■ 工具摩耗の兆候と影響
工具の摩耗は次第に進行しますが、ある閾値を超えると急激に加工精度が悪化します。
以下は、摩耗によって現れる代表的な兆候です。
・切削音の変化(ビビリ音や異音)
・加工面に光沢がなくなる
・工具先端の丸まりや欠け
・寸法精度や公差の外れ
摩耗した工具を使い続けると、表面粗さの悪化に加え、ワークの焼き付きや加工不良のリスクも増します。
さらに、加工機への負荷が増大し、機械の寿命を縮める原因にもなります。
■ 摩耗管理と予防保全
工具の寿命管理は、加工工程の安定にとって非常に重要です。
以下の方法で、摩耗によるトラブルを未然に防ぐことが可能です。
・使用時間の記録:切削時間や加工数を記録し、一定期間で工具を交換する「予防交換」の考え方を取り入れる。
・定期点検と顕微鏡検査:特に高精度加工では、工具の刃先を定期的に顕微鏡で確認することで、摩耗や欠損を早期に発見できます。
・摩耗予測システムの導入:近年では、切削音や主軸負荷などのデータをリアルタイムでモニタリングし、工具摩耗をAIで予測するシステムも登場しています。
表面粗さを高精度に管理するには、工具の性能を最大限に引き出すことが重要です。
適切な工具選定と摩耗管理を徹底することで、加工の安定性が向上し、製品の品質向上と歩留まりの改善にもつながります。
仕上げ加工・二次加工による改善
表面粗さの改善は、加工条件や工具選定だけでなく、仕上げ加工や二次加工を取り入れることで大きく向上させることが可能です。
特に高精度部品や意匠性を求められる部品では、初期加工のままでは所定の表面粗さを満たせないことが多く、追加の工程が必要となります。
本項では、代表的な仕上げ加工や二次加工法とその効果について詳しく解説します。
■ 研削加工による仕上げ
研削加工は、砥石を用いて材料表面を微細に削る加工法であり、非常に滑らかな表面仕上げが可能です。
切削加工でRa6.3程度であった面を、研削によってRa0.8以下にまで改善することも可能です。
特に、焼入れ鋼や硬質金属の最終仕上げに多く用いられます。
平面研削盤、円筒研削盤、センタレス研削盤など、目的に応じた機種を選ぶことで、精密かつ均一な仕上げが実現できます。
また、研削加工は寸法精度や幾何精度にも優れており、公差管理が厳しい部品に有効です。
■ バフ研磨・鏡面仕上げ
さらに表面光沢を追求する場合には、バフ研磨や鏡面仕上げが採用されます。
これは布やフェルトに研磨剤をつけて、摩擦により表面を研磨する加工です。
Ra0.1以下の極めて滑らかな仕上がりを実現でき、装飾部品や食品・医療機器のような高清浄性を必要とする部品に適しています。
ただし、寸法精度のコントロールが難しいため、寸法管理が重要な部品では研削と併用することが多いです。
また、手作業による仕上げも多く、量産向きではない場合もあります。
■ ラップ加工(ラッピング)
ラップ加工は、微細な研磨粒を含むスラリーを用いて、ワークとラップ板の間に挟んで加圧・摺動させることで高精度な表面を得る加工方法です。
Ra0.05以下の非常に高精度な面粗度が求められる用途(例:光学部品、シール面など)に使用されます。
ラッピングは、加工熱が少なく、熱による変形の影響が小さい点も特長です。
工程時間は長くなりがちですが、最終工程として非常に高い品質を得ることができます。
■ ショットピーニングや化学研磨
表面改質や微細凹凸の除去には、ショットピーニング(微粒子衝突による表面硬化)や、化学薬品によって表面を溶かす化学研磨といった特殊な方法も有効です。
特に複雑形状や内部の表面粗さを均一に整えたい場合に適しています。
ただし、化学研磨や電解研磨などは素材ごとに適合性があり、処理条件の管理も重要です。
樹脂やアルミなどの非鉄金属でも、表面粗さ改善の手段として導入されるケースが増えています。
■ 工程全体での考慮
仕上げ加工は単独で考えるのではなく、前工程(切削・成形など)とのつながりを意識することが重要です。
前段階での工具摩耗やバリ、焼けなどの不具合を放置すると、後工程で修正するための工数が増し、コスト・納期両面で不利になります。
そのため、設計段階で所定の表面粗さに応じた加工フローを設定し、必要であれば仕上げ加工の実施を前提に工程設計を行うことが、品質向上と効率的な生産の鍵となります。
このように、仕上げ加工や二次加工の選択は、表面粗さの最終品質に直結します。
目的に応じた加工法を選び、工程全体で最適化することで、製品の完成度を大きく高めることが可能です。
試作全国対応!
簡単・最短1時間お見積り
他、ブログ記事もご覧ください♪
動画の投稿もしておりますので良ければご覧ください♪