A2017(ジュラルミン)の特徴や規格の違いなど、簡単解説します!!
おはようございます!本日はジュラルミンで知られているA2017について解説します!
特徴や規格の違いなど知っていただく機会になればと思いますので、是非ご覧ください♪
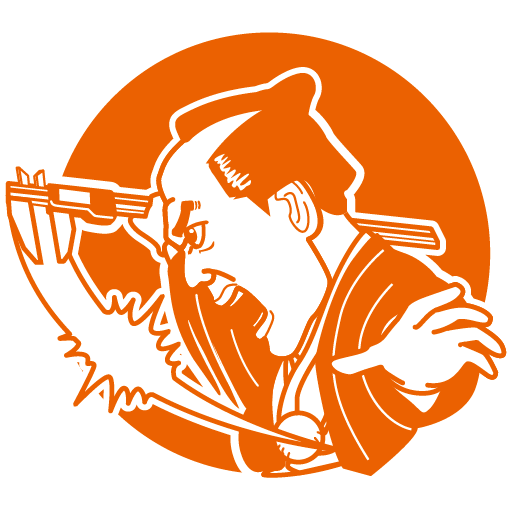
A2017とは
A2017は、JIS(日本工業規格)におけるアルミニウム合金の中でも、いわゆる「ジュラルミン系」に分類される代表的な材料であり、Al-Cu(アルミニウム・銅)系の合金です。
主成分であるアルミニウム(Al)に加え、2〜5%程度の銅(Cu)が添加されており、これによって高い強度が得られる点が大きな特徴です。
以下に代表的な化学成分を示します。
元素 | 含有量(%) |
---|---|
Al(アルミニウム) | 残部 |
Cu(銅) | 3.5〜4.5 |
Mn(マンガン) | 0.4〜1.0 |
Mg(マグネシウム) | 0.4〜0.8 |
Fe(鉄) | 0.7以下 |
Si(ケイ素) | 0.5以下 |
Zn(亜鉛) | 0.25以下 |
Cr(クロム) | 0.1以下 |
このように、Cuの含有量が非常に高いことがA2017の特徴であり、これによって「析出硬化処理」が可能となり、高い機械的強度を発揮します。
銅はアルミニウムに対して固溶強化の効果を持ち、さらに熱処理によって析出することで、材料内部に微細な析出物が生成され、それが結晶の滑りを妨げることで強度が向上します。
また、A2017は比較的古くから使用されている材料で、「ジュラルミン」と呼ばれる最初のアルミニウム合金の改良型に位置付けられています。
元祖ジュラルミン(A2000系)と比較して、A2017ではMnやMgを添加することで耐食性と加工性が向上しており、実用性が高まっています。
ただし、Cuを多く含むことはメリットばかりではありません。
代表的なデメリットとしては、耐食性が低下することが挙げられます。
銅は腐食の起点となりやすく、特に湿潤環境下では局部腐食(ピッティングや粒界腐食)の危険性が高まります。
そのため、A2017を使用する際には陽極酸化処理やアルマイト処理などの表面処理が重要となります。
さらに、Cuの多さは溶接性にも悪影響を与えます。
溶接熱による割れや、強度の低下が生じやすいため、溶接には不向きで、通常は接合にはリベットやボルトなどの機械的接合が選ばれます。
総じて、A2017は強度や切削性を求める用途に非常に優れており、機械部品や航空機構造部材、自転車フレームなど、加工精度と強度が重視される場面で活用されています。
一方で、耐食性や溶接性に制限があることから、設計・使用時には周囲環境や処理方法を考慮する必要がある、バランスの取れた高性能材料といえるでしょう。
機械的性質(引張強さ・硬さなど)
A2017は、アルミニウム合金の中でも機械的強度に優れる材料の一つとして知られており、特に引張強さや耐摩耗性の高さが評価されています。
これらの機械的性質は、Cuを主成分とした合金構成と、適切な熱処理によって得られる析出硬化によるものです。
引張強さと降伏点
A2017は、熱処理の状態によって性質が大きく異なります。
もっとも一般的に使用されるのは「T4(焼入れ+自然時効)」および「T6(焼入れ+人工時効)」の状態で、以下は代表的な数値です。
熱処理状態 | 引張強さ(MPa) | 降伏強さ(MPa) | 伸び(%) |
---|---|---|---|
T4 | 約 390 | 約 245 | 約 15 |
T6 | 約 440 | 約 355 | 約 8 |
T6処理では人工時効によりCuの析出が進み、非常に高い強度を得ることができます。
その反面、伸び(延性)は低下し、靭性がやや犠牲になります。
T4は強度と延性のバランスが良いため、加工を必要とする場面に適しています。
硬さと耐摩耗性
A2017は、硬度の面でも他のアルミ合金に比べて優れた性能を発揮します。
ビッカース硬さ(HV)で見ると、T6処理の場合で約120〜140HV程度に達します。
これは同じアルミ系の中でも高い水準にあり、耐摩耗性が求められる用途(ピストン、ギア、ジョイント部品など)に適しています。
また、鋼材に比べると軽量でありながら、このような高い硬度・強度を有することから、軽量化と高機能性を両立させたい設計に向いています。
疲労強度とクリープ特性
A2017は高強度材料である一方で、疲労強度や耐クリープ性はやや劣る傾向があります。
特に繰り返し応力がかかる構造体では、長期間の使用による金属疲労が問題になることがあります。
このため、設計時には応力集中を避ける形状設計が重要となります。
また、高温環境下では材料の強度が低下しやすく、クリープ(時間と共に変形が進行する現象)も発生しやすいため、A2017は常温から中温域(概ね150℃以下)での使用に適しています。
加工硬化と仕上げ性
A2017は加工硬化性を持ち、冷間加工を施すことで強度が一時的に向上しますが、これはあくまで補助的な効果であり、恒久的な強度向上には熱処理が不可欠です。
また、切削加工性が非常に良好であり、硬質であるため、仕上げ面が美しく、寸法精度の高い加工が可能です。
総じて、A2017は、強度と加工性、硬さを兼ね備えた優れた材料であり、機械部品や構造材として極めて有用です。
ただし、疲労や高温には注意が必要であり、用途に応じて他の材料との比較・検討が重要です。
耐食性と表面処理の必要性
A2017は強度や加工性に優れるアルミニウム合金ですが、その反面、大きな弱点として「耐食性の低さ」が挙げられます。
特に湿気や塩分を含む環境下では腐食の進行が速く、腐食対策が必須となる材料です。
この項では、A2017の耐食性の特性と、それを補うための表面処理について詳しく解説します。
耐食性のメカニズムと欠点
A2017はCu(銅)を3.5〜4.5%程度と高含有しているため、アルミニウム母材中に銅が固溶・析出することで腐食電位に差が生じ、ガルバニック腐食(異種金属間腐食)が発生しやすくなります。
これは、アルミニウムと銅の電位差によって、局部的に腐食が進行する現象で、ピッティング(点状腐食)や粒界腐食が生じやすい傾向にあります。
また、析出強化型の合金は、熱処理によって材料内部に不均一な組織が生じやすく、その影響で結晶粒の境界から腐食が進行する「粒界腐食」に特に注意が必要です。
このような腐食は見た目ではわかりにくく、進行すると材料の強度や寿命を大きく損なうため、構造部材として使用する際には設計段階から慎重な検討が求められます。
表面処理の必要性と種類
A2017を実用的に使用する際には、必ずと言っていいほど表面処理が施されます。
代表的な処理方法は以下のとおりです。
・陽極酸化処理(アルマイト処理)
A2017に対して最も一般的に施される表面処理が「陽極酸化処理(Anodizing)」です。
この処理により、表面に数μm〜数十μmの酸化皮膜(Al₂O₃)を形成し、耐食性と耐摩耗性を大幅に向上させます。
ただし、A2017は銅の影響で皮膜の均一性に欠けやすく、アルマイト処理時にやや濃い色味が出たり、処理ムラが起きることがあります。
・クロメート処理
化成皮膜処理の一種で、より簡易に耐食性を高めたい場合に用いられます。
皮膜は薄いものの、導電性を保ちつつ耐食性を向上させることができ、電装部品などに利用されることもあります。
六価クロムを使用したタイプは環境規制の対象となることから、現在は三価クロム系やクロムフリータイプの使用が進められています。
・塗装・電着塗装
耐候性が求められる場合には、表面に塗料を焼き付ける方法もあります。
塗膜は防食性を高めるだけでなく、意匠性や摩擦係数の調整にも役立ちます。
陽極酸化と組み合わせて使用することも多く、航空機や車両部品では標準的な処理です。
・複合処理(アルマイト+封孔処理など)
耐久性をさらに高めたい場合には、アルマイト後に封孔処理(染料や無機成分の注入)を施すことで、酸化皮膜内の微細な孔をふさぎ、腐食因子の侵入を防ぐことができます。
使用環境と設計上の注意点
A2017はそのまま使用すると、屋外や湿潤環境下で短期間に腐食が進むおそれがあります。
特に海浜地域や化学薬品を取り扱う現場では、使用に適しません。
よって、設計段階で以下の点を考慮する必要があります。
表面処理の選定と実施
・異種金属との接触を避ける(ステンレスや銅との接触による腐食)
・定期的なメンテナンスや洗浄を計画する
総じて、A2017は高性能なアルミ合金である一方、耐食性の低さが最大の弱点となるため、表面処理との組み合わせでその性能を最大限に引き出すことが重要です。
正しい処理を施せば、構造材としても長期間にわたり安心して使用できる材料となります。
A2017の加工性と熱処理
切削加工性と使用工具の選定
A2017は、アルミニウム合金の中でも非常に切削加工性に優れた材料として広く知られており、機械加工の分野で多く利用されています。
これは、高い硬度を持ちながらも被削性が良く、バリの発生が少なく、寸法精度や仕上げ面が美しく得られるためです。
ここでは、その切削特性の詳細や、使用する工具の種類・条件について説明します。
A2017の切削特性
A2017は、含有する銅やマグネシウムの影響で、純アルミニウムに比べて硬度が高く、しっかりとした切削反応を示します。
そのため、加工中にビビリやチャタリングが発生しにくく、安定した切削が可能です。
また、切りくずが細かく、絡みにくいため、自動旋盤やマシニングセンタでの連続加工に適しています。
さらに、材料自体にある程度の剛性があるため、薄肉加工や小径部品の仕上げ加工においても精度が出しやすく、切削加工の仕上げ面が非常に良好です。
公差要求の高い部品や美観が求められる製品にも適しており、外観品質を保ちつつ高能率加工が可能です。
適した切削工具の選定
A2017を切削する際には、工具選定が非常に重要です。
以下は、主な加工ごとの推奨工具です。
● 旋削加工
・工具材質:超硬合金(PVDコーティング付きが望ましい)
・切削条件:中〜高速度での切削が可能。一般に純アルミよりも低速で、高送り条件でも面粗度が安定。
・チップ形状:ポジティブすくい角、シャープな刃先を持つタイプが最適。切りくず排出性の良い設計が有効。
● フライス加工/マシニング加工
・エンドミル:アルミ用の2枚刃・3枚刃の超硬製エンドミルが適する。高送りに強い刃形がおすすめ。
・工具材質:超硬またはダイヤモンドコーティング(大量生産や高精度加工の場合)
・切削油:ドライ加工も可能だが、ミストやエアブローの併用で切りくず除去と刃持ちの向上が期待できる。
● ドリル加工
・ドリル種類:高精度加工には超硬ドリル、一般加工ではハイスドリル(HSS)も使用可能。
・下穴精度:位置精度が高く、加工変形が少ないため、精密穴あけにも適する。
注意点と最適条件
A2017の切削では、次のような点に注意すると加工性がより高まります。
・切削熱の管理:高速度での連続加工では、刃先温度の上昇による摩耗が起きやすくなるため、工具寿命の観点からも適度な冷却またはエアブローが有効です。
・チップの管理:鋭利な工具を保ち、摩耗した工具は早期に交換することで、加工面の品質維持と寸法精度の確保ができます。
・加工変形の防止:材料自体は高剛性ですが、薄板や細長い部品では加工時の振動や変形に注意が必要です。固定治具やクランプ位置を工夫することで、対策が可能です。
加工事例と実績
A2017は、その加工性の高さから、自動車部品や機械部品、航空機部品など、寸法精度や高品位な外観が求められる製品の切削に最適です。
特にNC旋盤や高速マシニングセンタを用いた大量生産ラインでは、効率と品質の両立が可能な材料として高く評価されています。
熱処理(T4・T6など)とその効果
A2017は「析出硬化型アルミニウム合金」に分類される材料であり、熱処理によって機械的性質を大きく向上させることができるのが大きな特徴です。
特に、T4処理(焼入れ+自然時効)やT6処理(焼入れ+人工時効)は、材料の用途や加工プロセスに応じて選択されます。
本項では、A2017における熱処理の基本と、その効果について詳しく解説します。
析出硬化とは?
A2017に含まれる主な強化元素はCu(銅)ですが、これが母材のAlに固溶した状態から熱処理によって析出することで、金属組織内に微細な粒子が形成されます。
これらの粒子が、結晶格子のすべりを阻害することで、材料の強度や硬度を飛躍的に高めることができます。
このプロセスが「析出硬化(時効硬化)」と呼ばれる現象です。
熱処理は、大きく3つの工程に分かれます。
・溶体化処理(Solution Heat Treatment)
銅をアルミ母材に均一に固溶させるため、約500°C程度で加熱し、急冷(焼入れ)する。
・焼入れ(Quenching)
急冷することで、銅が均一に溶け込んだ状態のまま、常温に戻す。
・時効処理(Age Hardening)
焼入れ後に、自然にまたは加熱により析出を進め、強度を高める。
この時効処理の方法により、T4やT6などの異なる性質が得られます。
T4処理(自然時効)
T4処理は、焼入れ後に常温で自然に時効させる方法です。
特に部品加工が多い場面では、このT4材が多く使われます。
・特徴:中程度の強度と高い延性を持ち、成形加工や曲げ加工に適する。
・用途例:リベット部品、曲げ部材、機械加工後に再熱処理を施す前段階など。
・利点:応力集中が起きにくく、加工歪みが少ない。
・欠点:T6に比べると強度はやや劣る。
数日から数週間かけてゆっくりと硬化が進行するため、加工後すぐに強度を要する用途には不向きですが、加工性と強度のバランスが良好な処理です。
T6処理(人工時効)
T6処理は、焼入れ後に160〜180°C程度の加熱を数時間行うことで人工的に析出を促進させる熱処理です。
これにより最大の強度が得られます。
・特徴:高い引張強さと硬度を有し、構造体や応力のかかる部品に適する。
・用途例:航空機構造材、自動車部品、高強度を求める産業部品。
・利点:高い機械的強度と耐摩耗性。
・欠点:延性はやや低下し、衝撃負荷や曲げには注意が必要。
特にT6処理後は、A2017が本来持つポテンシャルを最大限に引き出した状態となり、鋼材に迫るような強度をアルミで実現することが可能になります。
O処理(焼なまし)
T4やT6ほどではないものの、加工前の柔らかい状態が求められる場合には「O処理(焼なまし)」も使用されます。
これは溶体化処理を行わず、加熱後に徐冷することで、組織を安定化させ、延性や塑性を高めた状態です。
深絞りや曲げ、成形加工に使われますが、強度は最も低い状態になります。
状態ごとの選定ポイント
状態 | 強度 | 延性 | 加工性 | 用途例 |
---|---|---|---|---|
O | 低 | 高 | 非常に良好 | 深絞り部品、成形用素材 |
T4 | 中 | 中〜高 | 良好 | 機械加工用、曲げ部材 |
T6 | 高 | 中〜低 | 普通〜やや難 | 構造材、高強度部品 |
まとめ
A2017は、熱処理によって用途に応じた性質を自在に調整できる素材です。
特にT4とT6は強度と加工性のトレードオフを考慮して選択する必要があり、製品設計や製造工程に深く関わる要素となります。
正確な熱処理を施すことで、A2017は鋼材に劣らない強度と軽量性を兼ね備えた材料として、幅広い分野で信頼される存在です。
他材料との比較
A5052との比較(強度と耐食性)
A2017とA5052は、どちらもアルミニウム合金として多くの産業分野で用いられていますが、性質は大きく異なります。
両者を比較する際のポイントは、「強度」と「耐食性」にあります。
強度の比較
A2017はAl-Cu系の析出硬化型合金であり、熱処理によって高強度化される材料です。
特にT6処理では引張強さ400MPa以上が得られ、構造体や荷重のかかる部品に適しています。
一方のA5052はAl-Mg系の非熱処理合金で、T6などの時効硬化処理には対応していません。
引張強さは約250MPa前後で、A2017には及びません。
・A2017-T6:引張強さ 約440MPa
・A5052-H34:引張強さ 約265MPa
このように、高強度を求める場面ではA2017が圧倒的に有利です。
ただし、A5052は加工硬化によってある程度の強度向上が可能で、軽量なパネルや筐体などでは十分な性能を持ちます。
耐食性の比較
耐食性においては、A5052が大きく優れています。
A5052はMgを含有することで自己防錆性能が高く、特に海水や化学薬品に対する耐性が強いため、船舶・車両・配電盤など、腐食環境下での使用に最適です。
一方、A2017は銅を多く含むため、耐食性が著しく劣ります。
特に湿潤環境や塩害環境下では腐食が進行しやすく、表面処理が不可欠です。
陽極酸化やクロメート処理を施すことである程度改善されますが、長期間の屋外使用には注意が必要です。
まとめ
比較項目 | A2017 | A5052 |
---|---|---|
合金系統 | Al-Cu系(熱処理型) | Al-Mg系(非熱処理型) |
強度 | 非常に高い(T6) | 中程度(H34) |
耐食性 | 低い(処理必須) | 高い(無処理でも良好) |
溶接性 | 悪い | 良好 |
用途例 | 航空部品・機械部品 | 車体・船舶・タンク |
構造強度を最重視するならA2017、腐食環境や溶接加工を考慮するならA5052が適材適所です。
A6061との比較(汎用性と価格)
A2017とA6061は、いずれも高強度アルミ合金ですが、使用用途の幅広さ・価格面・加工性などに違いがあります。
特にA6061は、あらゆる性能をバランス良く持ち合わせた「汎用型アルミ合金」として知られ、対してA2017は強度や切削性に特化したやや高級材料といえます。
汎用性と使用範囲
A6061はAl-Mg-Si系合金で、耐食性、溶接性、加工性、強度などを高バランスで備えています。
建築、輸送、産業機械からDIYにまで使用される、最も汎用性の高いアルミ合金です。
一方のA2017はAl-Cu系で、航空機や精密機械など高精度・高強度を求める分野に適しており、使用シーンは限定的です。
耐食性や溶接性が劣るため、屋外構造や建材用途には不向きです。
価格の違い
A6061は流通量が多く、価格も安定しており、一般材料として扱いやすいのが特徴です。
一方、A2017は流通量が少なく、原料コストも高いため、価格がやや高めになります。
また、T6材など特定の熱処理状態での入手性に差がある点にも注意が必要です。
性能比較
比較項目 | A2017-T6 | A6061-T6 |
---|---|---|
引張強さ | 約440MPa | 約310MPa |
降伏強さ | 約355MPa | 約275MPa |
耐食性 | 低 | 高 |
溶接性 | 不可 | 良好 |
加工性 | 優秀(切削) | 良好(万能) |
コスト | 高 | 中~低 |
まとめ
A6061は「万能型」、A2017は「高精度・高強度型」として住み分けがされています。
コストと汎用性重視ならA6061、強度と加工精度を重視するならA2017という選定基準が有効です。
A2024との比較(高強度系合金同士の違い)
A2024とA2017は、どちらもAl-Cu系の高強度アルミ合金であり、いわゆる「ジュラルミン系」の代表格です。
両者の違いは細かく、用途の重なりもありますが、性能面と用途の特化性に差があります。
機械的性質の比較
両者ともT4やT6処理によって高強度化されますが、A2024はマグネシウム(Mg)含有量が高く、さらに高い強度と疲労特性を持ちます。
特に疲労強度においてA2024は航空機用途において長く採用されており、A2017より優位です。
性能比較 | A2017-T6 | A2024-T4 |
---|---|---|
引張強さ | 約440MPa | 約470MPa |
降伏強さ | 約355MPa | 約325MPa |
伸び | 約8% | 約10–15% |
疲労強度 | 普通 | 優秀 |
加工性・切削性の違い
A2017は切削性に優れ、バリが出にくく寸法精度が出しやすい点で優れています。
一方、A2024はやや硬質で工具摩耗が早く、切削には若干の工夫が必要です。
そのため、高精度機械加工にはA2017が好まれます。
耐食性の比較
どちらもCu含有量が高く耐食性は低めですが、A2024の方がやや劣る傾向にあります。
そのため、A2024を使用する場合には耐食性アルミ合金とのクラッド材(2024-T3 Clad)として使用されることが一般的です。
A2017は単材で使用されることが多く、必要に応じてアルマイト処理が施されます。
用途の違い
・A2024:航空機構造材(主翼、胴体フレーム、リベット材など)
・A2017:精密部品、航空機小物部品、自動車のハブやギアなど
まとめ
A2024は「構造材に求められる総合性能(高強度・疲労強度)」に優れ、A2017は「高精度加工と汎用性」に適しています。
どちらも高性能ですが、「部材の重要性」や「加工精度」に応じた選定が必要です。
アルミ製品の見積り依頼ならアスクへ
試作品や小ロットの加工も大歓迎!
特に手のひらサイズの部品製作を得意としています。
アスクなら、試作品のお見積もりが最短1時間で可能!!
お気軽にお問い合わせください。
試作全国対応!
簡単・最短1時間お見積り
他、ブログ記事もご覧ください♪
動画の投稿もしておりますので良ければご覧ください♪