エンドミル加工の基礎知識:多刃工具で切削する精密加工技術
エンドミル加工は、金属や樹脂などの材料に対して、回転する多刃の工具(エンドミル)を用いて切削する加工方法の一つです。
この加工法は、特に複雑形状や三次元的な加工が求められる部品の製作において重要な技術とされています。
例えば、機械部品、金型、航空機や自動車の部品など、多くの製造現場で不可欠な加工方法です。
エンドミル加工は、工具が回転しながら移動することで、立体的な形状を削り出すことができます。
この特性により、設計通りの精密な部品を効率よく製造することが可能となります。
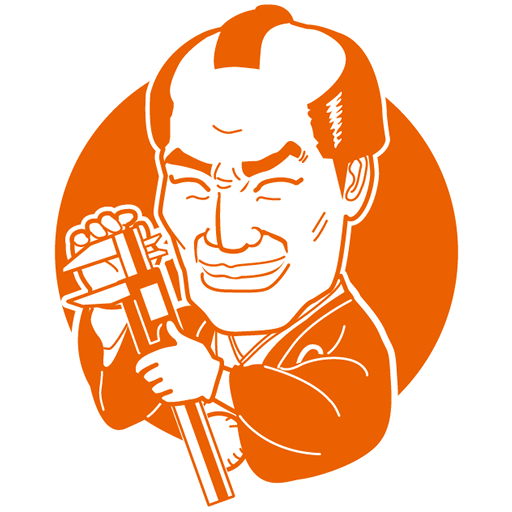
エンドミル加工とは
エンドミル加工とは、主に金属や樹脂などの材料に対して、回転する多刃の工具(エンドミル)を用いて切削する加工方法の一つです。
エンドミルはフライス工具の一種であり、主にマシニングセンタやフライス盤などに取り付けられて使用されます。
エンドミルの刃は側面および底面に付いており、工具が回転しながら移動することで、立体的な形状を削り出すことができます。
この加工方法は、特に複雑形状や三次元的な加工が求められる部品の製作において重要な技術です。
例えば、機械部品、金型、航空機や自動車の部品など、多くの製造現場で不可欠な加工方法とされています。
旋盤加工のようにワーク(加工対象物)自体が回転するのではなく、固定されたワークに対して工具が移動・回転しながら削る点がエンドミル加工の特徴です。
エンドミル加工は「切削加工」に分類され、除去加工とも呼ばれます。これは、不要な材料を切り取って目的の形状を作るという加工の考え方です。
切削には摩擦と熱が伴い、適切な切削条件(回転数、送り速度、切り込み量など)の設定が必要となります。
また、エンドミルの材質や形状の選定も、加工の仕上がりや効率に大きく影響します。
エンドミル加工の大きな利点の一つは、その加工自由度の高さにあります。
ポケット加工(くぼみ加工)、スロット加工(溝加工)、輪郭加工(外形加工)、曲面加工など、さまざまな加工が1本の工具で行える場合もあり、非常に汎用性が高い技術です。
また、NC(数値制御)やCNC(コンピュータ数値制御)の普及により、自動化されたエンドミル加工が一般化しており、精密な部品の量産にも対応可能です。
一方で、加工条件や工具の選定を誤ると、加工面が粗くなったり、工具が破損するなどの不具合も発生しやすいため、基礎知識と実践的なノウハウの習得が重要です。
とくに工具寿命の管理や切りくずの排出、熱対策など、現場での工夫も求められます。
総じて、エンドミル加工は、ものづくりの現場において極めて重要な役割を果たす技術です。
その基本を理解することは、金属加工や機械加工の全体像をつかむうえでも有効であり、初心者から上級者まで、広く学ぶ価値があります。
他の切削加工との違い
エンドミル加工は、多くの切削加工法の中でも非常に汎用性が高く、多軸で複雑な形状にも対応できる加工方法です。
ここでは、旋盤加工、フライス加工、ボーリング加工、ドリル加工などの他の切削加工と比較しながら、エンドミル加工の特性と独自の強みを解説します。
まず、旋盤加工との違いから見てみましょう。
旋盤加工は「ワーク(素材)が回転」し、固定されたバイト(工具)で外径や内径を削る加工法です。
一方、エンドミル加工では「工具が回転」し、「ワークは固定」されている点が大きな違いです。
旋盤は円柱形状の外径加工に向いていますが、平面加工や角形状には不向きです。
対してエンドミルは、平面・曲面・ポケット・溝・穴など多彩な加工に対応できるため、複雑形状の部品加工に適しています。
次に、ドリル加工との比較です。
ドリルは円筒形の穴を開ける専用工具で、穴あけ専用の加工法と言えます。
一方エンドミルも、底刃を持つことで穴あけに使えるものもありますが、その後に穴の拡大や溝の加工など、複合的な形状に対応できる点がドリルと大きく異なります。
ドリルは単純な直線方向の穴あけに優れ、エンドミルは横方向や斜め方向への進行も可能で、自由度の高い切削が実現できます。
また、ボーリング加工(中ぐり加工)は、すでに開けた穴を広げたり、内径の寸法精度を高めたりする加工方法です。
これは高精度が求められる穴の仕上げに特化しており、専用のボーリング工具が用いられます。
エンドミルも内径加工に用いることはできますが、精度面では専用工具にやや劣ります。
そのため、最終仕上げにはボーリング工具を使い、エンドミルは中間工程や荒加工に使用されるケースもあります。
フライス加工はエンドミル加工のルーツともいえる加工法です。
実際、エンドミルもフライス加工に使われる工具の一種です。
フライス盤での加工は、ワークを動かしながら工具を回転させ、面や溝を削るという点で、エンドミル加工と非常に似ています。
違いは、汎用フライス加工では直線的な加工が中心であるのに対し、エンドミル加工ではCNC技術と組み合わせることで曲線、斜面、三次元形状の自由な加工が可能となる点です。
さらに、放電加工やレーザー加工などの非接触加工と比べた場合、エンドミル加工は機械的に工具が材料に接触して削る「機械加工」に分類されます。
そのため、導電性が必要な放電加工と異なり、非金属や樹脂などの幅広い材料に対応できる点が強みです。
また、切削速度や工具材質、クーラントの使用などを調整することで、高い加工精度と表面仕上げも実現可能です。
総じて言えるのは、エンドミル加工はその自由度の高さ、多軸制御との親和性、工具バリエーションの豊富さにより、他の加工法と比べても非常に柔軟で応用範囲の広い加工法であるということです。
1台のマシニングセンタと多様なエンドミル工具を揃えることで、穴あけから溝加工、曲面仕上げまで一貫して行える点は、製造現場における大きな強みと言えるでしょう。
エンドミルの種類と用途
スクエアエンドミルの特徴と用途
スクエアエンドミル(Square End Mill)は、先端が平らな形状を持つ最も基本的なエンドミルです。
その先端が直角にカットされており、底面や側面の切削に向いているため、エンドミル加工における汎用工具として広く使われています。
特に、溝加工、ポケット加工、平面削りなどにおいて優れた性能を発揮します。
スクエアエンドミルの最大の特長は「直角のエッジ」です。
これにより、角のあるポケットやシャープな形状を作ることができ、設計図面通りのエッジを加工しやすくなります。
機械加工の現場では、部品の寸法精度や角形状を保つことが求められるため、このような工具は非常に重宝されます。
スクエアエンドミルはフルカットにも対応できるため、ワーク(被削材)の側面を深く削る加工や、部材の外形をなぞって仕上げる「輪郭加工」などにも適しています。
さらに、2枚刃・4枚刃・6枚刃などのバリエーションがあり、加工内容に応じて選定されます。
例えば、2枚刃は切りくず排出性が良いため荒削りに向いており、4枚刃以上になると切削面が滑らかになり、仕上げ加工に適します。
素材に関しても、多くの被削材(鉄、アルミ、銅、ステンレス、樹脂など)に対応しており、工具コーティング(TiAlN、DLCなど)を施すことで耐久性や熱耐性も向上します。
特に量産加工や一般機械部品の製造において、コストパフォーマンスに優れた選択肢といえるでしょう。
ただし、先端が完全に平らであるため、ポケット底部のコーナーには“R(アール)”が残らないため応力集中が生じやすい点には注意が必要です。
また、シャープなエッジは欠けやすいため、切削条件の調整や工具の定期的な交換が重要になります。
総じて、スクエアエンドミルはエンドミル加工の基本となる工具であり、機械加工における「万能選手」ともいえる存在です。
初めてエンドミルを選定する場合には、まずこのタイプから導入するのが一般的であり、その後の加工内容に応じて他のタイプへと使い分けていくのが理想的です。
ボールエンドミルの特徴と用途
ボールエンドミル(Ball End Mill)は、先端が半球状になっているエンドミルです。
この形状により、三次元の曲面加工や滑らかな輪郭加工、微細なR形状の成形に非常に適しています。
金型加工や航空宇宙・医療機器分野のような高精度かつ複雑形状を求められる製品において、ボールエンドミルは欠かせない工具です。
最も大きな特徴は、曲面形状を滑らかに加工できるという点です。
スクエアエンドミルでは、エッジの直線的な移動によって角ばった仕上がりになりがちですが、ボールエンドミルは球状の先端が材料表面をなめるように削るため、曲面を高精度で仕上げることができます。
この特性は特に、CAM(コンピュータ支援製造)による「等高線加工」や「スキャロップ加工」などの三次元輪郭の仕上げ工程で真価を発揮します。
また、工具の中心部(球の最下点)は切れ刃の送り速度がゼロに近くなるため、加工中の切削抵抗は高くなりがちです。
そのため、ボールエンドミルは基本的に側面を使って加工することが多く、Z軸方向への深掘りではなく、X-Y方向への等高線的な動きが主流となります。
このため、送り速度や回転数の設定には注意が必要であり、切削条件を適切に制御しなければ、加工面に「スジ」や「バリ」が出る原因にもなります。
素材選定においては、超硬ボールエンドミルが一般的で、耐摩耗性や剛性に優れています。
高硬度鋼や難削材の加工にも対応するため、特に金型加工では標準工具として用いられます。
また、微細加工用として「マイクロボールエンドミル」も存在し、ミクロン単位の微細部品や医療用インプラントなどの加工にも対応できます。
さらに、ボールエンドミルは底部にRを残す設計となるため、応力集中の回避にも役立ちます。
たとえば、構造部品における角部の疲労強度向上を目的とした設計では、わざとRを残して加工することがあります。
このようなケースではスクエアエンドミルではなく、ボールエンドミルを選定することで設計意図に沿った加工が可能になります。
一方、欠点としては、工具先端が点接触になるため、中心部の切削能力が弱く、加工能率が低いという側面もあります。
特に、荒加工に用いるには不向きで、主に中仕上げ〜仕上げ加工で使用されることが一般的です。
荒加工にはスクエアエンドミルやラジアスエンドミルなどを使い、最後にボールエンドミルで仕上げるという流れが主流です。
総じて、ボールエンドミルは高精度な3D曲面を求められる加工や、設計上Rが必要な部品の仕上げ加工に欠かせない工具です。
マシニングセンタとの相性も良く、CAD/CAM技術との連携により、その性能を最大限に引き出すことができます。
設計段階で3次元形状が多い場合には、必ずと言っていいほど活用される重要なエンドミルです。
ラジアスエンドミルの特徴と用途
ラジアスエンドミル(Radius End Mill)は、先端のコーナー部に半径(R形状)を持たせたエンドミルです。
一見するとスクエアエンドミルに似ていますが、刃先の角が鋭角ではなく丸く加工されている点に大きな違いがあります。
このR部は「コーナーR」とも呼ばれ、加工時のエッジ強度を高めるとともに、仕上げ面の耐久性向上や応力集中の緩和に貢献します。
ラジアスエンドミルの最大の特長は、工具の寿命を延ばしながら高品位な切削を実現できる点です。
スクエアエンドミルでは、角部に大きな負荷が集中しやすく、特に高硬度材や加工条件が厳しいケースでは、エッジが欠けたり摩耗しやすくなります。
対して、ラジアスエンドミルではR部が切削抵抗を分散させるため、刃先のチッピング(小さな欠け)を抑え、安定した加工を継続できます。
用途としては、金型加工・航空機部品・精密機械部品の外周加工や溝加工、ポケット加工などに広く用いられています。
特に、コーナー部に意図的にRを残す必要がある設計では、ラジアスエンドミルの使用が必須となります。
製品設計の段階で応力集中を避ける目的で角部にRを設けることが多いため、その加工にはこの工具が適しています。
また、スクエアエンドミルと比較すると、ラジアスエンドミルはより高速で切削できるケースも多く、生産性向上に寄与します。
これは刃先の形状が滑らかなため、切削時の振動やビビりを抑えられるためです。
そのため、CNCマシニングセンタとの相性もよく、安定した加工面を得たい際には積極的に選定されます。
さらに、ボールエンドミルとは異なり、底面を平らに加工できる点も特徴です。
これは、スクエアエンドミルのように平面を仕上げつつ、刃先にはRがあるという“中間的な性質”を持つためで、仕上げ面の美しさと工具の耐久性を両立したいときに非常に有効です。
つまり、スクエアエンドミルとボールエンドミルの利点をバランスよく備えた工具といえます。
なお、ラジアス部のサイズは、一般的に「R0.2」から「R2.0」など用途に応じて様々なバリエーションがあります。
Rが大きければ加工面の角はより丸くなりますが、自由度が下がる場合もあるため、設計意図や加工形状に応じた選定が重要です。
一方で注意点としては、意図せず角を立てたい場合には不向きということです。
スクエアなエッジが必要な設計にラジアスエンドミルを使ってしまうと、コーナーにRが残ってしまい、寸法公差や形状精度を損ねるおそれがあります。
そのため、使用前には必ず図面の設計仕様や要求公差を確認し、工具選定を慎重に行う必要があります。
総じて、ラジアスエンドミルは耐久性と仕上がり品質を両立させたい加工現場において重宝される工具です。
スクエアエンドミルと比較して少し高価な傾向はあるものの、トータルのコストパフォーマンスや工具寿命の面で見ると、非常に優れた選択肢といえるでしょう。
ロングネック・ロングシャンクエンドミルの使いどころ
ロングネックエンドミルおよびロングシャンクエンドミルは、その名の通り通常のエンドミルに比べて、首下やシャンク(工具を保持具に固定する部分)が長く設計された工具です。
この特徴により、深いポケット加工や側壁の深い箇所の切削、段差のある形状へのアクセスが可能になります。
特に金型加工や航空機部品など、複雑かつ奥行きのある形状を削る場面では、これらのロングタイプのエンドミルが必須の選択肢となります。
ロングネックエンドミルは、刃長(切削部分)は比較的短いまま、首下を細く長くすることで、干渉を避けながら深い場所まで刃を届かせられるのが特徴です。
例えば、深さ30mmのポケット形状に加工を行う場合、通常のスクエアエンドミルではシャンク部分がワークに干渉してしまう恐れがありますが、ロングネックタイプであればこの問題を回避し、工具の逃げを確保しながら切削が行えます。
こうした構造は、金型のコーナーR仕上げや、深いリブ形状、三次元形状の最終仕上げにおいて重宝されます。
一方、ロングシャンクエンドミルは、首下だけでなくシャンク自体も長くなっており、工具全体の突出し量が大きくなるため、マシニングセンタでの治具構造や取り回しの自由度が高まります。
ただし、その分、剛性が低下しやすく、ビビり(工具の微細振動)やたわみ、切削面の荒れが起きやすくなるというリスクも伴います。
このような加工不安定性を回避するためには、以下のような対策が必要です。
・切削条件の最適化(切込み量や送り速度を控えめに)
・工具の突出し量を最小限に抑える
・高剛性のツーリングを使用する
・ビビり抑制用の工具形状(不等分割・不等リード)の採用
さらに、ロングネックやロングシャンクタイプのエンドミルは、微細加工や小径工具での使用が多いのも特徴です。
たとえば、深い溝の底に微小なRをつけるような加工、微小部品の隅部処理など、細やかな加工精度が求められる場面では、首下の長さと工具径の小ささが加工精度を大きく左右します。
加えて、被削材との関係も考慮が必要です。
ロングタイプのエンドミルは、アルミや樹脂など比較的切削抵抗の少ない材料には適していますが、難削材や高硬度鋼に使用する場合は、さらに剛性のある超硬工具やコーティング付き製品を選定することで、ビビりや工具折損を防ぎます。
総じて、ロングネックおよびロングシャンクエンドミルは、「届かない場所に刃先を届かせる」という目的に特化した、非常に戦略的な工具です。
ただし、突出し量が長いことで加工の安定性が損なわれやすいため、使用にあたっては工具設計だけでなく、加工条件や工作機械の剛性、保持具の適切な選定など、周辺環境も含めて慎重に対応することが求められます。
粗加工用エンドミルと仕上げ加工用エンドミルの違い
エンドミル加工においては、目的に応じて「粗加工(ラフカット)」と「仕上げ加工(フィニッシュカット)」を使い分けるのが基本です。
これに対応する工具として、「粗加工用エンドミル」と「仕上げ加工用エンドミル」がそれぞれ存在し、それぞれが持つ形状・特性・使用目的は大きく異なります。
この理解が、加工の効率・精度・工具寿命を大きく左右します。
■ 粗加工用エンドミルの特徴
粗加工用エンドミル(ラフィングエンドミルとも呼ばれます)は、大きな切り込みと高い送り速度で効率よく大量の材料を除去するための工具です。
特徴的なのは、刃の形状に「波状刃」や「セレーション刃(ギザギザの刃)」が設けられていること。
これにより切りくずが細かく分断され、切削抵抗を低減しながら高能率な加工が可能になります。
また、工具全体の剛性も高く設計されており、重切削にも耐えられる構造となっています。
特に、鉄・ステンレス・鋳鉄などの金属を荒削りする際には、切削熱や振動にも強く、安定した切削が期待できます。
ただし、粗加工用エンドミルで得られる加工面は、仕上げ品質には劣ります。
あくまで大量除去が目的であるため、寸法精度や表面粗さは仕上げ加工に委ねられる前提で使われます。
実際の加工現場では、「粗取り→仕上げ」という工程分離がごく一般的です。
■ 仕上げ加工用エンドミルの特徴
一方、仕上げ加工用エンドミルは、高い寸法精度と表面仕上げ品質を求める場面で使用される工具です。
刃先形状は鋭利かつ滑らかで、波刃などは用いられず、切削痕がきれいに残るよう設計されています。
刃数も多く(4枚刃以上)、低切込み・高回転での使用に適しており、最終的な形状を決定する仕上げ工程に使用されます。
また、ボールエンドミルやラジアスエンドミルも仕上げ加工に適したタイプとして使われることが多く、特に三次元曲面やコーナー部などではこれらが必須になります。
表面粗さの指示がある図面や、公差が厳しい部品などでは、仕上げ専用工具の導入が精度確保のカギとなります。
■ 両者の使い分けの重要性
粗加工用と仕上げ加工用のエンドミルを使い分けることで、加工時間の短縮と品質の向上を両立できます。
例えば、最初から仕上げ用エンドミルで重切削を行おうとすると、刃が欠けたり、工具寿命が著しく低下してしまう可能性が高くなります。
また、粗加工用のエンドミルで仕上げまで行ってしまうと、寸法精度や表面仕上げが不十分になり、再加工が必要になるおそれもあります。
加工プログラムの設計においても、「粗加工ツールパス」と「仕上げツールパス」を別々に設け、工具も最適化して選定することで、効率・精度・コストのバランスをとることが可能です。
■ 加工例と選定のポイント
たとえば、40mm角のアルミブロックから金型の一部を削り出す場合、まずは12mmの粗加工用エンドミルで大部分を除去し、その後6mmのラジアスエンドミルで細部を仕上げる、というように段階的に工具を使い分けます。
この際、被削材や形状の複雑さに応じて、刃径、刃数、コーティングの有無なども考慮に入れて選定します。
試作全国対応!
簡単・最短1時間お見積り
他、ブログ記事もご覧ください♪
動画の投稿もしておりますので良ければご覧ください♪