ヘリサートの種類や形状など解説します!
本日はヘリサートについて解説します!
ヘリサートの種類や形状、用途など解説していきますので、是非ご覧ください♪
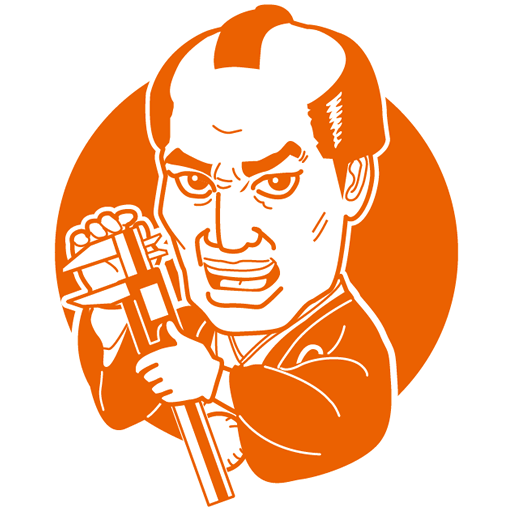
ヘリサートとは
ヘリサート(Heli-Coil)は、ねじ山の補修や補強に使われる金属製のスプリング状インサートです。
正式には「スプリュー(Screw thread insert)」とも呼ばれますが、日本では「ヘリサート」という商品名が一般的に定着しており、通称として広く使われています。
ヘリサートは、母材のねじ穴に挿入することで、新たなねじ山を形成し、強度や耐久性を向上させる役割を果たします。
特にアルミニウムやマグネシウムなどの軟質材料において、ねじの締結力を高めたり、ねじ山の損傷を修復したりするために活用されます。
ヘリサートは、断面が菱形のステンレス製ワイヤーを螺旋状に巻いた構造になっており、この構造がねじ穴に高い保持力と耐久性をもたらします。
インサートの外周が母材側のねじ山に、内周が挿入されるボルト側のねじ山に対応しており、まるで元からその場所にねじ山があったかのような状態を再現することができます。
これにより、何度もボルトを着脱するような場面でも、母材のねじ山を傷めることなく長期間使用することが可能です。
また、ヘリサートはJISやISO、UNC/UNFなど、さまざまなねじ規格に対応しており、規格に応じた製品がラインナップされています。
そのため、用途に合わせて最適なタイプを選定することができます。
さらに、通常のねじ穴加工よりも軽量でコンパクトな補修が可能なため、自動車、航空機、精密機器、電子機器、医療機器など、幅広い分野で使用されています。
ヘリサートの利用により、ねじの抜けや緩みを防止し、機械部品の信頼性を高めることができます。
特に、振動や温度変化の激しい環境では、ねじ部のトラブルが製品全体の不具合につながることもあります。
ヘリサートはそうしたリスクを低減する効果的な手段として、多くの製造業や整備現場で重宝されているのです。
ヘリサートの構造と材質
ヘリサートは、シンプルながら非常に機能的な構造を持つねじ補修・補強用のインサートです。
その基本構造は、菱形断面を持つ金属ワイヤーを螺旋状に巻いたもので、見た目はスプリングのようですが、機械的特性に優れた精密な部品です。
この構造により、母材側のねじ山と、ボルト側のねじ山の両方と確実に噛み合い、しっかりとした締結力を実現します。
ヘリサートの断面形状は「ダイヤモンド形(ひし形)」をしており、この断面形により、ねじ締結時にはワイヤーのエッジ部分がボルトと母材のねじ山に確実に密着します。
このような構造により、締結力が均等に分散され、ねじの緩みや抜けを防止できるのが特長です。
また、螺旋のピッチや径も非常に高い精度で管理されており、挿入後のボルトの締め心地や精度は通常のねじ穴と遜色ありません。
材質については、標準的なヘリサートはSUS304などのオーステナイト系ステンレス鋼で作られています。
SUS304は耐食性や加工性に優れており、多くの環境で安定した性能を発揮します。
この材質は、腐食に強く、屋内外問わず使用可能で、しかも柔軟性と強度のバランスに優れているため、インサート材として理想的です。
一方で、使用環境によっては特殊な材質が求められることもあります。
たとえば、高温環境ではインコネル(耐熱ニッケル合金)、電気接点用途ではリン青銅、腐食性ガスが発生する環境ではハステロイやチタン合金など、過酷な条件下でも性能を維持できる材料が選ばれます。
これらの特殊材質のヘリサートは、航空宇宙分野や半導体製造装置、医療機器などの高信頼性が求められる分野で使用されています。
また、ヘリサートには「コーティング」や「潤滑処理」が施されることもあります。
たとえば、乾式潤滑剤を表面に施して挿入性を向上させたり、ねじ込みトルクを安定させるための潤滑コートを加えたりすることがあります。
こうした処理は、自動組立ラインでの安定した作業や、繰り返し使用されるメンテナンス部品での耐久性向上に効果的です。
このように、ヘリサートの構造は非常にシンプルでありながら、その材質や設計には高度な技術が詰め込まれており、多様な使用環境に対応できるように工夫されています。
正しい構造理解と材質選定を行うことで、ねじ締結部の信頼性を大きく向上させることができるのです。
ヘリサートの用途とメリット
ヘリサートが最も効果を発揮する用途の一つが、「軟質金属におけるねじ補強」です。
特に、アルミニウムやマグネシウムといった軽金属は、軽量性や加工性に優れている反面、ねじ山の強度が低く、繰り返しの着脱や過大なトルクにより簡単にねじ山がつぶれてしまうという欠点があります。
こうした問題を解消するために、ヘリサートを使ってねじ部を補強することが一般的です。
たとえば、アルミ製の部品に直接ねじを切った場合、ボルトの着脱を数回繰り返しただけで、ねじ山が摩耗してしまい、十分な保持力を失ってしまうことがあります。
とくに、自動車や航空機、家電などのように定期的なメンテナンスが必要な製品では、ねじの耐久性が信頼性に直結します。
そこで、初めからヘリサートを挿入しておくことで、鋼製のねじ山を形成し、耐摩耗性や強度を格段に高めることができるのです。
さらに、ヘリサートの使用により、ねじ山の強度だけでなく、ボルトの締結トルクに対する耐性も向上します。
たとえば、アルミだけではトルクをかけすぎるとねじ山がバカになってしまいますが、ヘリサートを挿入することで、締付けトルクを適切に管理しやすくなり、安定した締結力を維持できます。
また、ねじのゆるみにも強く、長期使用時の信頼性も確保されます。
また、軟質金属へのねじ補強では、挿入工程自体も簡便で、特別な加工機械を必要とせず、下穴をあけて専用のタップを使い、挿入工具でヘリサートをねじ込むだけです。
この手軽さもあって、小規模な工場やメンテナンス現場でも導入が進んでいます。
近年では、EV(電気自動車)やドローン、ポータブル電子機器など、軽量かつ高耐久が求められる製品が増えており、アルミやマグネシウムの採用がますます増加しています。
それに伴い、ヘリサートの重要性もさらに高まっており、設計段階からインサートを前提としたねじ設計が行われることも増えてきました。
総じて言えるのは、軟質金属におけるねじ補強においてヘリサートは非常に有効であり、製品の耐久性・信頼性を飛躍的に高めるキーコンポーネントであるということです。
設計者や技術者にとっては、素材特性と締結技術を理解し、最適なヘリサート活用を行うことが、製品寿命の向上や品質トラブルの低減につながるのです。
損傷ねじ山の修復
機械や装置のメンテナンスにおいて、ねじ山の損傷はよくあるトラブルのひとつです。
長年使用された機械部品や、不適切なトルクで締め付けられたボルト穴などでは、ねじ山が摩耗したり、つぶれたりして、ボルトが正しく固定できなくなることがあります。
こうした損傷は一見小さな問題に思えますが、締結力の低下や部品脱落など重大なトラブルに発展しかねません。
このようなケースで有効なのが、ヘリサートを使ったねじ山の修復です。
損傷したねじ穴をそのまま放置すると、再度の締め付けができず、機能不全や安全性の低下につながるため、何らかの対処が必要です。
新品の部品に交換するという方法もありますが、それはコストがかさみ、場合によっては不可能なケースもあります。
特に、大型機械のフレームや鋳物部品など、交換が容易でない部材には、現地で修復できる手段としてヘリサートが最適です。
修復手順はシンプルで、以下のような工程で行います。
1.下穴の拡大
損傷したねじ穴をドリルで広げて、ヘリサート挿入に必要なサイズの下穴をあけます。
2.専用タップで新しいねじ山を加工
次に、ヘリサート専用のタップを使って、拡大した下穴にインサート用のねじ山を切ります。
3.ヘリサートの挿入
専用工具を使用して、ヘリサートをねじ込むことで、元のねじ径・ピッチと同じねじ山が再生されます。
4.挿入爪の折り取り
最後に、挿入爪を折り取れば、通常通りのボルトが使用可能になります。
このように、比較的短時間かつ低コストでねじ穴の修復が完了するため、メンテナンス現場では非常に重宝されています。
修復後のねじ山は、元の母材よりも強度が高い場合が多く、耐久性や耐トルク性に優れるという副次的な利点もあります。
また、修復対象は金属に限らず、プラスチック樹脂製品に対しても応用可能です。
たとえば、ノートパソコンやカメラの筐体など、繰り返しネジを脱着する箇所はねじ山が摩耗しやすく、ヘリサートを使って修復・補強することで製品寿命を延ばすことができます。
このように、損傷ねじ山の修復においてヘリサートは非常に有効な手段であり、「壊れたから交換する」から「修理して再使用する」へと、サステナブルな製品運用にも貢献しています。
現場での即時対応が求められる中、誰でも扱いやすい修復手段として今後も重要な役割を果たし続けるでしょう。
振動やゆるみに対する効果
機械や構造物において、ねじの「ゆるみ」は大きな問題を引き起こす原因となります。
とくに自動車、航空機、鉄道、産業用機械など、絶えず振動や衝撃にさらされる装置では、ボルトやねじが緩むことで構造的な不具合が生じ、最悪の場合は事故につながることもあります。
そうしたリスクを低減するための対策として、ヘリサートの使用は非常に有効です。
まず理解しておきたいのは、ボルトのゆるみの主な原因が「振動・熱膨張・繰り返し荷重による応力変動」であるということです。
通常のねじ山は、こうした変動によって徐々にクリアランスが生じ、初期の締結トルクを維持できなくなってしまいます。
特に、母材がアルミなどの軟質金属の場合はねじ山が変形しやすく、ゆるみが顕著になります。
ここで登場するのがヘリサートです。
ヘリサートはステンレス製などの高強度ワイヤーでできた螺旋状のインサートで、これを母材に挿入することで、ねじ山の耐久性を飛躍的に高めます。
母材とヘリサートの間には非常に強固なはめ合いが生じるため、ねじ込み式のボルトは本体に強固に固定され、微小な揺れや変位に対してもしっかりとした保持力を発揮します。
さらに、ヘリサートには「ロックタイプ」と呼ばれる製品があります。
これはインサート内部の一部に「変形コイル」が組み込まれており、ボルトが締め込まれるとこの変形部分がボルトに圧力をかけて摩擦を発生させ、セルフロック機能を持つ構造です。
この機構により、外部からの振動や衝撃による緩みを抑制でき、ナイロンナットやスプリングワッシャーのような緩み止め部品を使わなくても、高い締結信頼性を実現できます。
たとえば、エンジン回りやトランスミッション、振動を伴う装置などでは、ロックタイプのヘリサートが多く使用されています。
航空業界や軍用機器など、過酷な環境下での運用が前提となる分野では、振動や衝撃によるゆるみ防止が設計上の重要ポイントとなっており、ヘリサートの活用が非常に進んでいます。
このように、ヘリサートは単にねじの修復・補強という役割だけでなく、「振動対策」としての性能にも優れており、信頼性が求められる現場において不可欠な存在となっています。
特にゆるみによる不具合が品質問題や安全リスクに直結する分野では、設計段階からの積極的な採用が望まれています。
耐摩耗性の向上
ねじ締結部は、機械構造において繰り返し使用されることが多く、取り外しや再締結のたびにねじ山が摩耗していきます。
特にアルミニウムやマグネシウム、樹脂などの軟質材料を母材とする場合、ねじ山の耐摩耗性は構造強度や長期信頼性に直結する重要な課題です。
こうした問題を解決する手段のひとつが、ヘリサート(ねじインサート)を用いたねじ山の補強です。
ヘリサートは主にSUS304(ステンレス鋼)などの耐摩耗性に優れた材質で構成されており、これを母材に挿入することで、繰り返しのボルト着脱による摩耗を大幅に軽減できます。
たとえば、アルミ製の部品に直接ボルトを締めた場合、数回の使用でねじ山が変形・削れ・摩耗してしまう可能性があります。
一方で、ヘリサートをあらかじめ挿入しておけば、ねじ山自体は硬質金属によって形成されるため、摩耗しにくくなり、繰り返しのメンテナンスにも耐える構造となります。
この特性は、特に以下のような用途で効果を発揮します。
・航空機や自動車のエンジンカバーなど、定期的に取り外す部品
→ メンテナンス頻度が高いため、摩耗によるネジ抜けを防ぐ必要があります。
・精密機器の筐体、電子機器の樹脂ケース
→ ねじ穴の摩耗によるがたつきや締結不良を防止。
・組立治具や検査装置など、頻繁にボルトを締めたり緩めたりする構造物
→ 使用頻度が高くても長寿命な締結性能が維持されます。
また、ヘリサートは摩耗だけでなく、「かじり」や「焼き付き」といった金属同士の摩擦によるトラブルも抑制します。
たとえば、ステンレス製のボルトをステンレス製の部材に直接ねじ込むと、固着して外れなくなる「焼き付き」が発生しやすいのですが、間にヘリサートを介在させることで潤滑性と離脱性が改善され、こうした問題も防げます。
さらに、ヘリサートは一度挿入すれば長期的に使用でき、交換の必要もほとんどありません。
万が一、ねじ山が破損した場合でも、ヘリサートを取り除いて再挿入するだけで済みます。
この「再利用可能性の高さ」も、耐摩耗性とあわせて大きな利点といえるでしょう。
結果として、ヘリサートの使用は部品の寿命延長と保守コストの削減にもつながります。
ねじ部の摩耗は見落とされがちですが、実は製品信頼性に深く関わるポイントです。
初期設計段階でヘリサートを採用することで、トラブルを未然に防ぐとともに、耐久性の高い構造が実現できるのです。
異種金属の接触防止(電食対策)
金属部品同士を組み合わせる際に注意が必要なのが、「異種金属接触による腐食」、いわゆる電食(電気化学的腐食)の問題です。
これは、異なる金属が電解質(水分や湿気など)を介して接触した場合に、電位差により電流が流れ、腐食が促進される現象です。
たとえば、アルミ母材にステンレスボルトを直接ねじ込むと、アルミ側が腐食しやすくなるという問題が生じます。
このような場面で役立つのがヘリサートの使用です。
ヘリサートは、母材とボルトの間に中間層として機能する金属インサートであり、電気的接触の条件をコントロールすることができます。
特に、母材が腐食に弱いアルミニウムやマグネシウムなどの場合、ステンレス製のヘリサートを挿入することで、直接的な金属接触を避け、電食リスクを大幅に低減することが可能です。
ヘリサートの材質にはSUS304やSUS316などがあり、これらは耐食性が高く安定した金属です。
適切な材料を選ぶことで、異種金属間の電位差を小さくし、腐食電流の発生を抑えることができます。
さらに、特定の用途ではニッケルメッキや亜鉛メッキ処理されたヘリサートも使用され、耐環境性を高めています。
電食による腐食は、見た目にはわかりづらく、内部から劣化が進行することが多いため、設計段階での予防が非常に重要です。
ボルトが脱落したり、ねじ山がもろくなったりすることによって、機械全体の性能や安全性が損なわれるおそれがあります。
とくに海洋機器、航空機、車載部品、屋外設備などでは、湿気や塩分が多い環境下での使用が前提となるため、電食対策は欠かせません。
また、樹脂や塗装で防食を試みるケースもありますが、ねじの締結部はトルクが集中しやすく、表面処理が破壊されることもあるため、構造的に防ぐ方法としてヘリサートの使用は理にかなっています。
実際、航空宇宙産業や医療機器分野など、信頼性が要求される分野では、電食防止の観点からもヘリサートの採用が一般的です。
まとめると、ヘリサートは単にねじ山の補強にとどまらず、異種金属接触による腐食を防ぐインターフェースとして機能する重要な要素です。
これにより、構造の信頼性を高め、長期にわたる製品寿命を支える役割を果たしています。
ヘリサートの種類と特徴
ヘリサートの種類と構造(フリータイプとロックタイプ)
ヘリサート(ねじインサート)は、ねじ山の補強や修復に使用される便利な機械要素ですが、その種類は使用目的に応じていくつかに分類されます。
代表的なのが「フリータイプ」と「ロックタイプ」という2つのタイプです。
どちらも母材に挿入することで高強度なねじ山を形成する役割を持ちますが、それぞれ構造と機能が異なります。
フリータイプ(Free Type)
フリータイプは、最も標準的なヘリサートの形態で、ばね状に成形されたステンレス製のコイルが、タップ加工された下穴に挿入され、ねじ山を形成します。ボルトを締め込むと、このコイルが内側に力を分散し、ねじ部にしっかりとした締結力を生み出します。
特徴は以下の通りです。
・一般的な締結用途に最適
・挿入や取り外しが比較的容易
・繰り返しの着脱にも耐える構造
・軟質金属(アルミやマグネシウムなど)への補強に効果的
フリータイプは、電気機器、自動車部品、精密機械、医療機器など、さまざまな産業分野で広く使用されています。
特に、母材の強度が低い場合に、そのねじ部を補強する目的で導入されることが多く、トラブル防止や長寿命化に貢献します。
ロックタイプ(Screw Lock Type)
ロックタイプのヘリサートは、フリータイプに追加機能を加えたもので、ボルトのゆるみ止め効果を持つのが最大の特徴です。
構造的には、内側の一部に変形したコイル部分(ポリゴン形状や押しつぶされたコイル)があり、ここがボルトのねじ部に機械的な抵抗を加えます。
この抵抗力によって、振動や衝撃が加わってもボルトが自動的に緩まないようになります。
ロック剤や座金を使わずにゆるみ止めが実現できるため、組立工程の省略や信頼性の向上が図れるのです。
特徴は以下の通りです。
・ボルトのゆるみを防止(セルフロック機能)
・高振動環境(エンジン周りや航空機)に適する
・ネジゆるみ対策の部品点数削減に貢献
・挿入はやや難易度が高く、専用の工具が必要なこともある
ただし、ロックタイプは抵抗が強くなるため、繰り返しの着脱に制限がある点には注意が必要です。
締め直しの頻度が高い部分にはフリータイプを使用し、確実なロックが求められる部分にはロックタイプを選ぶ、という使い分けが重要です。
まとめ
ヘリサートの選定においては、「どのような機能をねじ部に求めるか」が大切です。
一般的な補強・修復にはフリータイプ、振動や衝撃にさらされる環境ではロックタイプといったように、使用条件や目的に応じた選定が、ねじ締結部の信頼性と安全性を大きく左右します。
特に産業用途においては、設計段階からこれらの違いを理解し、適切なインサートを選ぶことが重要です。
使用する材質とその選び方
ヘリサート(ねじインサート)を選定する際、見逃せない重要なポイントが「材質」です。
用途や使用環境によって適切な材質を選ぶことで、ねじ部の信頼性や製品寿命、安全性が大きく左右されます。
材質は主に使用環境(腐食、温度、絶縁性など)と母材との相性を踏まえて選ぶ必要があります。
ステンレス鋼(SUS304、SUS316など)
もっとも一般的で広く使用されているのがステンレス製のヘリサートです。
標準タイプにはSUS304が、耐食性をより重視する場合にはモリブデンを含むSUS316が使われることがあります。以下のような特徴があります。
・耐食性が高く、屋外や湿気の多い環境でも使用可
・高強度・高耐久性を備え、機械的負荷にも強い
・電気伝導性があるため、導電性が必要な機器にも対応
とくに自動車部品、航空機、医療機器、電子機器の筐体など、信頼性が重視される製品においてはステンレスが最適です。
ただし、母材との電位差による電食(電気化学的腐食)に注意する必要があります。
銅合金(ブロンズ)
銅系の合金製ヘリサートは、絶縁性や磁性の問題を避けたいときに選ばれることがあります。
たとえば、電子機器や磁気センサー付近の構造において、磁性を嫌う場合などです。
・磁性がないため磁場の影響を受けにくい
・導電性が高く、静電気対策にも有効
・やや柔らかいため、繰り返し使用には不向きな場合もある
また、銅は柔らかいため挿入時に注意が必要ですが、ねじ込みトルクの精度を上げやすい利点もあります。
表面処理付きタイプ(ニッケルメッキ、潤滑コーティングなど)
標準のステンレス製ヘリサートに、追加の表面処理を施したものも多く存在します。
たとえば、ニッケルメッキ仕上げは耐食性の向上に役立ちますし、潤滑コーティングがされているタイプは挿入時の抵抗を下げる効果があります。
・ニッケルメッキ:耐食性や耐熱性を強化
・ドライフィルム潤滑:工具負荷を軽減し、作業性向上
・酸化処理(黒染め):反射防止や外観改良に使われることも
これらは特殊用途向けですが、作業効率やメンテナンス性を考慮する設計においては非常に有効です。
樹脂対応タイプ(樹脂母材専用設計)
プラスチック材料に使う場合は、特殊なヘリサートが必要です。
通常の金属母材用とは異なり、外径部分に突起やアンカー構造を持たせたタイプが多く、母材への食いつきを強化しています。
・樹脂の変形を抑えながら高い保持力を確保
・溶着や圧入などの挿入方法が選べる
・小型機器、筐体部品、家電などに最適
注意点として、一般の金属用ヘリサートを樹脂に使うと保持力不足や破損の原因となるため、材質と形状が専用のものを選ぶことが重要です。
選定のポイント
材質選定においては、以下の観点を押さえておくとよいでしょう。
・使用環境(湿度、温度、腐食要因)
・締結トルクや負荷の大きさ
・母材の材質(アルミ、樹脂、マグネシウムなど)
・繰り返しの脱着があるか
・導電性や磁性の有無
たとえば、海辺や湿気の多い場所ではSUS316やニッケルメッキ品、磁場が影響するような医療機器では非磁性合金が選ばれることが多いです。
対応ねじ規格(メートルねじ・ユニファイねじなど)
ヘリサートを使用するうえで見落としがちですが非常に重要なポイントが、「対応するねじ規格」です。
ねじは世界各地でさまざまな規格が採用されており、それぞれ寸法や角度、ピッチに違いがあります。
これに合わせて、ヘリサートも適切な規格に対応した製品を選定する必要があります。
メートルねじ(Mねじ)
日本国内をはじめ、ヨーロッパなどでも広く使用されているのがメートルねじ(Metric Thread)です。
ねじの呼び径(M3、M5など)とピッチ(ねじ山の間隔)がミリ単位で表記されており、ISO規格(ISO 68-1, ISO 261)にもとづいて設計されています。
例:M6×1.0 → 外径6mm、ピッチ1.0mm
・標準ピッチと細目ピッチ(細かいねじ山)両方に対応する製品あり
・日本国内では圧倒的に使用頻度が高く、調達も容易
ヘリサートの多くはこのメートルねじ用であり、製品ラインナップも豊富です。
M2からM30を超える大型まで用意されているため、一般機械・電子機器・車両まで幅広く対応可能です。
ユニファイねじ(UNC・UNF)
アメリカやカナダなどで主流なのが、ユニファイねじ(Unified Thread)です。
インチ単位で寸法が表記され、ねじ山の数(TPI=Threads Per Inch)でピッチを表します。
ユニファイねじはさらに、以下の2種類に分類されます。
・UNC(Unified National Coarse):並目ねじ。荒めのピッチで組立性が高い。
・UNF(Unified National Fine):細目ねじ。精密性とゆるみ止め性能が高い。
例:
#10-24UNC → 呼び径0.19インチ(約4.8mm)、TPI=24
1/4-28UNF → 呼び径1/4インチ(約6.35mm)、TPI=28
これらの規格に対応するヘリサートも販売されており、米国規格製品や外資系製品の補修や設計において必須となります。
国際取引やグローバル製造ラインでは、メートルねじとの混在も多いため、設計段階から明確に規格を区別することが重要です。
その他の規格
特定の用途では、以下のような特殊ねじ規格も使われることがあります。
・BSP(British Standard Pipe):配管用ねじ
・NPT(National Pipe Thread):テーパーねじ(流体機器など)
・MJねじ:航空宇宙用、厳格な規格でトルクや強度が求められる
こうした特殊規格にも対応するヘリサートは存在しますが、基本的には設計や製造上で規格が必要になる特殊分野での使用が中心です。
規格選定のポイント
ねじ規格の誤りは、製品の不具合やトラブルの原因となります。
特に以下の点を意識して選定・管理する必要があります。
・機器や製品の原産国に合わせて規格を確認
・メートル・インチ規格の混在を避ける
・修理・補修の場合、既存のねじ規格に合わせる
・社内・設計図面で規格を明記し統一する
ヘリサートの寸法や専用工具も規格によって異なるため、互換性のない部品を混在させないよう注意が必要です。
ヘリサートの施工方法
下穴加工と専用タップ
ヘリサートを使用する際の第一工程は、下穴加工とタップ立てです。
このステップは、インサートを正確に挿入するために不可欠であり、全体の精度や耐久性にも大きく関わります。
以下では、具体的な手順や注意点について詳しく解説します。
下穴の加工
まず、母材に対してヘリサート挿入用の下穴をあけます。
この下穴の径は、使用するインサートのサイズとピッチに応じて厳密に決められており、メーカーの技術資料に記載されています。
たとえば、M6×1.0ピッチのヘリサートを使用する場合、推奨される下穴径は6.3mm程度です。
一般のタップ下穴(M6なら5mm)よりもやや大きくなっている点が特徴です。
この下穴の精度が悪いと、タップが正しく立たなかったり、インサートが傾いて入ってしまう原因となります。
そのため、できる限り真円度の高いドリルやリーマ加工を用いることが望ましいです。
また、深さについてもインサートの長さ+タングの余裕分を確保する必要があります。
専用のヘリサートタップ
下穴を加工した後は、専用のヘリサートタップ(HST:Heli-Coil Screw Thread Tap)を使ってねじ山を切削します。
このタップは、通常のメートルねじ用タップとは形状やピッチが異なるため、代用はできません。
ヘリサートタップの特徴:
・インサートがしっかり嵌まるように、特殊なねじ形状
・先端が滑らかで、下穴への入りがスムーズ
・インサートの直径に合わせて設計されており、確実なねじ保持力を実現
手作業でタップ立てを行う場合は、必ずタップガイドなどを使用し、垂直に加工するようにしましょう。
また、切削油を適切に使用してタップへの負荷や摩耗を減らすことも大切です。
量産現場では、タッピングマシンやCNC加工によるタップ立てが主流です。
注意点
・下穴径とタップサイズを必ず確認:規格ミスがトラブルの原因になります。
・母材が軟質材(樹脂やアルミなど)の場合、より高精度な加工が必要。
・一度切ったヘリサート用ねじ山は再利用できないため、やり直しが効きにくい工程です。
このように、ヘリサート施工における「下穴加工と専用タップ」は非常に重要な工程であり、精度・工具選定・手順の遵守が成功の鍵となります。
インサート挿入と工具の使い方
ヘリサート施工において、ねじ山を切った後に行うのが「インサート挿入」の工程です。
この作業は一見シンプルに見えますが、適切な工具の使用と、正確な操作が求められる工程です。
ここでは、挿入方法や専用工具の種類、作業時の注意点について詳しく解説します。
インサートの構造と挿入方向
ヘリサート(スプリュー)は、コイル状に巻かれたステンレスワイヤー製のインサートで、片端に「タング」と呼ばれる突起がついています。
このタングは挿入時に工具が引っかかるように設計されており、これを利用して右ねじ方向に回しながら挿入します。
注意点としては、ヘリサートには挿入方向が決まっており、逆方向から入れてしまうと使用できません。コイルの巻き方向を確認し、タング側から工具にセットする必要があります。
挿入工具の種類
ヘリサートの挿入には、専用の工具を使うことが推奨されています。
代表的なものは以下のとおりです。
・手動式挿入工具(ドライバー型)
小型サイズのヘリサート(M2〜M8程度)では、手動の専用ドライバーを使用することが一般的です。
工具の先端にタングを引っかけて回転させ、コイルを押し込むようにねじ込んでいきます。
・ラチェット式工具
繰り返し作業に便利で、特に量産現場で使用されます。
回転トルクが安定し、一定の押し込み力で挿入可能です。
・自動装填式工具
インサートを複数本マガジンにセットし、自動で挿入していく装置です。
高速化が可能で、生産ライン向けに導入されます。
いずれの場合も、工具とヘリサートのサイズが一致していることが重要です。
サイズ不一致や劣化した工具の使用は、インサートの変形や挿入不良の原因になります。
正しい挿入方法
・ヘリサートを工具にセットする(タングがしっかり引っかかるように)
・母材のねじ穴に対して、垂直に工具をあてがう
・回転させながらゆっくりとインサートをねじ込む(無理に押し込まない)
・インサートが1/4~1/2ピッチ程度穴の内側に収まるまで挿入する
・最後に工具を逆回転させて取り外す
重要なのは、ねじ込みすぎず、足りなすぎない適正な挿入深さを確保することです。
飛び出してしまうとボルトと干渉し、締結不良やガタつきの原因になります。
よくあるトラブルと対策
・インサートが斜めに入ってしまう
→工具を垂直に保ち、下穴の面取りやバリ取りをしっかり行いましょう。
・途中で硬くなり、挿入できない
→タップの切りくず残りやねじ精度不良が原因。エアブローや再タップで対処。
・工具から外れない/タングが変形する
→サイズミスや摩耗した工具が原因。新品の適正サイズを使用しましょう。
このように、インサート挿入は見た目以上に繊細な作業です。
正しい工具と手順を守ることで、長期にわたって信頼性の高いねじ締結が可能となります。
タングの折り取りと仕上げ
ヘリサートの挿入が完了した後の最終工程が「タングの折り取り」です。
タングとは、ヘリサートの一端に設けられた突起部分で、挿入時に工具が引っかかるように設計されています。
このタングは、挿入後も残ったままだとボルトの通りを妨げてしまうため、必ず切り取る必要があります。
とくに貫通穴で使用する場合、タングの折り取りは避けて通れない重要な工程です。
タングの役割と存在意義
ヘリサートはコイル状のインサートであり、その先端に「タング」と呼ばれる小さな突起がついています。
これがあることで、挿入工具はタングに噛み合い、ねじ込む力をしっかり伝えることができます。
つまり、施工時の操作性を高めるための構造ということです。
しかし、インサートの挿入が完了した後、このタングは役割を終えます。
特に貫通穴では、ボルトを奥まで通す際に干渉してしまうため、タングを取り除かなければなりません。
一方、止まり穴の場合、奥にタングが残っていても問題ないこともありますが、異物混入や精密性の観点から折るのが一般的です。
折り取り工具と方法
タングを折り取るためには、専用のタング折り取り工具(ブレーカー)を使用します。
この工具は、細いピンのような形状をしており、タングの位置に合わせて差し込み、軽くハンマーなどで叩いて折ります。
手順は以下の通りです。
・インサート挿入後、工具を外し、タングがしっかり見えることを確認
・折り取り工具をタングの真上に垂直にセットする
・軽く一打、ハンマーで工具を叩く
・「カチッ」と音がしてタングが折れ、穴の奥に落ちる
ヘリサートのタングは意図的に折れやすい構造になっているため、力をかけすぎる必要はありません。
無理に押し込んだり斜めに衝撃を加えると、母材やインサート自体が傷むおそれがあります。
折った後の仕上げ処理
折り取ったタングは、基本的には穴の底にそのまま残ることが多いですが、重要な機構部品や精密機器のねじ穴などでは、マグネットやエアブローで取り除くことが推奨されます。
残骸が機械内部に落ちてしまうと、不具合や異音の原因となることもあるためです。
また、インサートの挿入後は、上面が母材の穴より0.25~0.5ピッチほど内側にあることが理想的です。
飛び出している場合は、再調整するか、場合によっては取り外してやり直すことも検討します。
注意点とトラブル例
・工具を斜めに当ててしまい、インサートごと変形させた
→常に垂直な方向から衝撃を加えるように意識し、工具も適正サイズを使う。
・タングが完全に折れず、ねじ部に干渉してしまった
→不完全な折り取りは非常に危険。タングが完全に取れたことを必ず確認する。
・折ったタングが機器内部に落ちてしまった
→貫通穴の場合、タング回収の工夫(マグネットピックなど)を事前に検討しておく。
このように、タングの折り取りと仕上げは、地味ながら品質に大きく影響する工程です。
わずかな残骸や位置ズレが、製品全体の機能不良につながることもあるため、丁寧な作業と最終確認が求められます。
ヘリサート加工の見積り依頼ならアスクへ
試作品や小ロットの加工も大歓迎!
特に手のひらサイズの部品製作を得意としています。
アスクなら、試作品のお見積もりが最短1時間で可能!!
お気軽にお問い合わせください。
試作全国対応!
簡単・最短1時間お見積り
他、ブログ記事もご覧ください♪
動画の投稿もしておりますので良ければご覧ください♪