POM(ポリアセタール)とは?その特性と活用
やってまいりました、材料解説シリーズ!!!!
本日はPOM(ポリアセタール)のご紹介です♪
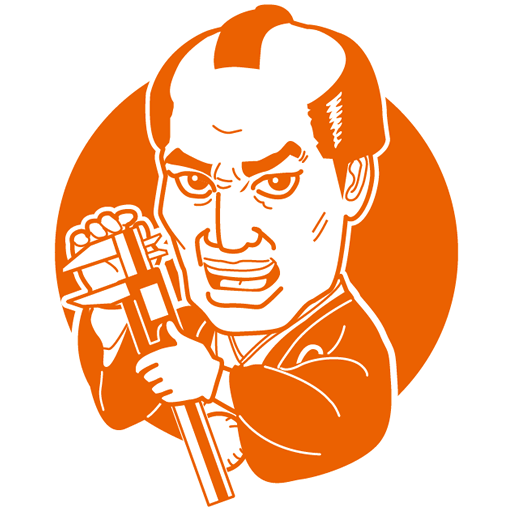
POM(ポリアセタール)とは
POM(Polyoxymethylene、ポリアセタール)は、エンジニアリングプラスチックの一種で、優れた機械的強度、耐摩耗性、寸法安定性を持つことから、金属部品の代替として広く利用されています。
結晶性の熱可塑性樹脂であり、分子構造により「ホモポリマー」と「コポリマー」の2種類に大別されます。
まず、ホモポリマー型POMは、単一のモノマーで構成された直鎖状の分子構造を持ち、高結晶性で剛性や耐摩耗性が非常に高いことが特徴です。
これにより、精密な加工が必要な部品や高負荷がかかる機械部品に適しています。
一方で、熱安定性や耐加水分解性にはやや難があり、高温多湿な環境では劣化しやすいという欠点も持ち合わせています。
これに対して、コポリマー型POMは、ホルムアルデヒドと他の共重合成分(一般的には1,3-ジオキサン)を組み合わせた構造をしています。
これにより、ホモポリマーよりも熱安定性が高く、加水分解に対する耐性にも優れています。
また、成形時の寸法安定性にも優れており、一般的な産業用途ではこちらのタイプがよく用いられます。
加工性や成形性も良好なため、量産性が重視される部品に適しています。
POMは、通常、白色または乳白色のペレット状で流通し、射出成形、押出成形、切削加工など、さまざまな加工方法に対応できます。
ホモポリマーはデュポン社の「Delrin(デルリン)」というブランド名で知られ、コポリマーは各種メーカーから多様な製品名で展開されています。
選定においては、使用環境や目的に応じてホモポリマーとコポリマーを使い分けることが重要です。
たとえば、高精度かつ剛性が求められる歯車やスライド部品にはホモポリマーが適しており、逆に湿気の多い環境や寸法安定性が求められる部品にはコポリマーが選ばれる傾向にあります。
このように、POMはその分子構造の違いによって性質が大きく変わり、それぞれの特性を活かした用途で幅広く活躍しています。
次の小項目では、こうした特性をさらに詳しく掘り下げていきます。
POMの物理的・化学的特性
POM(ポリアセタール)は、エンジニアリングプラスチックの中でも特に優れた物性バランスを有する材料として知られています。
その特性は金属に匹敵するとも言われ、多くの機械部品や精密パーツに利用されています。
この項目では、POMの代表的な物理的・化学的特性について詳しく解説します。
まず注目すべきは、高い機械的強度と剛性です。
POMは結晶性樹脂であり、その高い結晶性によって優れた引張強度や曲げ強度を持っています。
特に初期剛性が高く、荷重が加わった際のたわみが小さいため、ギア、軸受、カムなどの機械構成部品に適しています。
こうした機械特性は、熱可塑性樹脂の中でもトップクラスです。
また、優れた耐摩耗性と自己潤滑性もPOMの特長です。
摺動部品として使用されることが多く、潤滑油なしでも長期間にわたり安定した動作を維持することができます。
このため、潤滑が難しい環境や、メンテナンスを最小限にしたい設計において重宝されます。
さらに、POMは寸法安定性に優れており、吸水率が低く、湿度や温度の変化による膨張や収縮が少ないという利点があります。
これにより、高精度が求められる部品でも安心して使用することができます。
コポリマータイプのPOMは特にこの特性が顕著です。
耐熱性については、連続使用温度が約100〜120℃と比較的高く、一時的な熱にもある程度耐えることができます。
ただし、150℃以上では熱劣化が進みやすくなるため、高温環境下では他素材との比較検討が必要です。
耐薬品性についても良好で、多くの油類、アルコール、有機溶剤に対して安定しています。
酸やアルカリにはやや弱い傾向がありますが、日常的な使用環境では問題にならないレベルです。
ただし、ホモポリマータイプはコポリマーよりも加水分解に対する耐性が低いため、水分を含む環境では注意が必要です。
また、電気的特性も良く、絶縁体としての性能が高いため、電子部品や絶縁部材としての用途にも適しています。
耐アーク性や絶縁破壊電圧などの面でも信頼性があり、家電製品の内部部品などでも活用されています。
以上のように、POMは強度・剛性・摺動性・耐薬品性・寸法安定性など、非常にバランスの取れた性能を持つ素材です。
その結果、金属代替の樹脂として、また、量産可能な高性能素材として、さまざまな分野で使用されているのです。
他の樹脂との違いと比較
POM(ポリアセタール)は、数あるエンジニアリングプラスチックの中でも、バランスの取れた物性を持つ高性能樹脂として知られています。
この項目では、POMと他の代表的なエンプラ(エンジニアリングプラスチック)との違いや、それぞれの特徴を比較し、用途に応じた選定のポイントを明らかにします。
まず、POMとナイロン(PA)との比較です。
ナイロンはPOMと同様に機械的強度や耐摩耗性が高い材料として知られていますが、吸水性が高いという弱点があります。
吸水によって寸法が変化しやすく、寸法精度が求められる部品には不向きなことがあります。
その点、POMは吸水率が非常に低く、湿度の高い環境でも寸法安定性に優れています。
また、ナイロンは柔軟性があり衝撃に強い一方で、POMはより硬く、初期剛性に優れています。
用途としては、ナイロンは軟らかく耐衝撃性が求められる部品、POMは高精度なギアや摺動部品などに適しています。
次に、POMとポリカーボネート(PC)との比較です。
ポリカーボネートは耐衝撃性と透明性に優れた材料で、光学部品や透明カバーなどに用いられます。
一方で、耐摩耗性や摺動性はPOMに劣ります。
また、ポリカーボネートはPOMよりも耐熱温度が高い傾向がありますが、耐薬品性ではPOMの方が優れています。
したがって、化学薬品と接する可能性がある機構部品にはPOMが適し、光を通す部品や高い衝撃強度が必要な場合にはPCが選ばれます。
また、POMとポリプロピレン(PP)を比較すると、PPは非常に軽量で耐薬品性に優れており、コストも低いのが特長です。
ただし、機械的強度や耐摩耗性はPOMほど高くありません。
POMは高負荷がかかる可動部品などにも耐えられる剛性を持つ一方で、PPは主に耐薬品性を活かしたタンクや容器類、家庭用品に使われます。
POMとABS樹脂も比較されることがあります。
ABSは加工性や意匠性に優れ、家電製品の筐体などに多用されますが、機械的強度や耐摩耗性ではPOMに及びません。
POMはABSに比べて硬く、摺動性が求められる部品により適しています。
最後に、POMとPTFE(テフロン)の違いにも触れておきます。
PTFEは非常に優れた耐薬品性と滑り性を持ち、極端な環境でも安定した性能を発揮します。
ただし、加工が難しくコストが高いため、一般的な摺動用途にはPOMが選ばれるケースが多くなります。
POMは「手頃な摺動材」としてPTFEの代替となることもあります。
以上のように、POMは「剛性」「寸法安定性」「摺動性」「耐摩耗性」といった特性において非常に優れており、他の樹脂と比較しても、汎用性とバランスの高さが際立ちます。
用途に応じて、これらの比較を踏まえた材料選定が重要です。
POMの加工性と成形技術
射出成形におけるPOMの扱い
POM(ポリアセタール)は、射出成形によって大量生産されることが多いエンジニアリングプラスチックのひとつです。
加工性が良好で寸法精度も高いため、工業用部品から精密機構部品まで幅広い分野で採用されています。
本項では、POMを射出成形する際の注意点や加工条件、成形特性について詳しく解説します。
1. 加熱と分解の管理
POMは熱分解しやすい特性を持っています。
特にホモポリマー型は200℃を超えると急速に分解が進み、ホルムアルデヒドを発生させるため、安全管理と温度制御が非常に重要です。
一般的な成形温度の目安は、ホモポリマーで170~190℃、コポリマーで190~210℃程度とされており、加熱筒の温度や滞留時間には細心の注意を払う必要があります。
また、樹脂がホッパーから加熱シリンダー内に滞留する時間が長くなると、分解ガスの発生や焦げの原因となり、製品の品質低下や金型の汚染につながります。
成形機のパージ処理や定期的な清掃も品質維持に不可欠です。
2. 成形性と収縮率
POMは結晶性樹脂であるため、冷却時の収縮率が大きい(一般に1.5~2.5%)という特徴があります。
このため、精密成形品においては金型設計段階から適切な収縮補正を行う必要があります。
特に肉厚部や金型の冷却バランスが悪いと、寸法精度や変形に影響を与えるため注意が必要です。
また、POMは流動性が良いため、複雑な形状や薄肉の製品でも比較的容易に成形できます。
しかし、ゲート位置やランナー設計が不適切だとウェルドラインやヒケの原因になることがあり、成形不良のリスクもあるため、CAE解析や試作による事前検証が有効です。
3. 金型設計と離型性
POMは離型性に優れており、型離れが良いため、複雑な形状でもスムーズに取り出すことが可能です。
反面、金型内でのスライド部分などに摺動が生じるため、金型の摩耗に対してはある程度の対策が求められます。
また、成形時のガス抜き構造も重要で、分解ガスや空気が金型内に残留すると、焼けや欠けといった不良の原因になります。
冷却系の設計もPOM成形では重要です。
均一かつ効率的な冷却により、寸法安定性と成形サイクルの短縮を両立できます。
特に高精度な部品を成形する場合は、金型温度を一定に保つ温調機の導入も有効です。
4. 加工後の処理と注意点
POMは成形直後でも高い物性を発揮しますが、さらに寸法精度や機械的強度を求める場合には、アニール処理(応力除去焼鈍)が施されることがあります。
これは、成形時に内部に蓄積された応力を除去する目的で行われ、長期的な変形防止に寄与します。
また、POMは成形品のエッジ部分が鋭くなる傾向があるため、バリ取りや面取りなどの仕上げ加工も場合によっては必要となります。
とはいえ、POMは比較的バリが出にくい素材であり、量産に適した良好な成形性を持つ点も大きなメリットです。
切削加工におけるPOMの特性
POM(ポリアセタール)は射出成形による大量生産だけでなく、少量生産や試作、精密部品の加工にも対応できる「切削加工性の高い樹脂」としても広く利用されています。
特に、精密さが求められる機構部品や試作品の製作では、POMの切削特性が大きな強みとなります。
この項目では、POMの切削加工における特徴や、加工上の注意点、適した工具などについて詳しく解説します。
1. 加工性の良さと適用範囲
POMは硬さと剛性を兼ね備えた樹脂でありながら、切削抵抗が比較的小さいため、NC旋盤やマシニングセンタなどの一般的な工作機械で容易に加工できます。
また、切削時に溶けにくく、バリや溶着が少ない点も特長です。
このため、微細加工やネジ切り、溝加工、ドリル加工など、金属と同等の加工が可能であり、汎用的な材料として重宝されています。
また、POMは寸法安定性が高く、加工後の反りや変形が少ないため、精密な公差管理が求められる用途にも対応できます。
たとえば、スライド部品やギア、カムなど、機械的に繰り返し動作するパーツにも切削加工で高精度に仕上げることが可能です。
2. 使用工具と切削条件
POMの切削には、超硬工具やハイス鋼のエンドミル、バイト、ドリルなどが用いられます。
金属に比べると加工負荷が低いため、工具寿命も長くなる傾向にあります。
切削速度(Vc)は、ドリル加工で約30〜60m/min、旋盤加工では100〜250m/min程度が目安です。
送り速度(f)や切込み量(ap)は工具や加工内容により異なりますが、POMは熱により軟化しやすいため、切削熱がこもらないように加工条件を調整することが重要です。
とくに連続切削や深穴加工では、切削油やエアブローによる冷却が有効です。
乾式加工も可能ですが、精度や表面仕上げが求められる場合には湿式加工が推奨されます。
3. バリ・表面仕上げと後加工
POMはバリの発生が少ない素材ではありますが、加工条件や工具の摩耗状態によっては細かいバリが出ることもあります。
特に、薄肉部や端面部では工具の切れ味が影響しやすいため、定期的な刃先のチェックや仕上げ加工が求められます。
発生したバリに対しては、面取りやバフ研磨、ディバリングツールなどで処理を行うのが一般的です。
また、POMは表面の滑り性が高く、美しい光沢仕上げが得られやすい素材です。
そのため、高精度の刃物と適切な切削条件を用いれば、加工後すぐに使用可能なレベルの仕上がり面が得られます。
これは他の樹脂にはない大きな利点のひとつです。
4. 切削加工に向くPOMの種類
POMにはホモポリマーとコポリマーの2種類が存在し、切削加工においてはコポリマーの方が一般的に扱いやすいとされています。
ホモポリマーはより剛性が高い反面、加工時に割れやすく、刃物への攻撃性もやや強いためです。
また、着色されたPOMやグレードによっては、切削性に差が出ることもあります。
例えば、炭素繊維強化タイプのPOMは強度こそ高いものの、工具摩耗が激しい傾向にあるため、工具の材質選定や加工条件の最適化がより重要になります。
加工時の注意点とトラブル対策
POM(ポリアセタール)は、射出成形・切削加工の両方に優れた特性を持ち、工業用の多くの部品に活用されている高機能樹脂です。
しかし、その性能を最大限に引き出すには、加工中の特性やリスクに対する理解が不可欠です。
この項目では、POMの加工時に注意すべき点と、実際によくあるトラブル、そしてその対策について詳しく解説します。
1. 熱分解とガス発生への注意
POMの最大の注意点のひとつが、熱による分解リスクです。
特にホモポリマー型は熱分解しやすく、200℃を超えるとホルムアルデヒドなどの刺激性ガスを発生させます。
成形機のノズルやシリンダー内に樹脂が長時間滞留した場合にも分解が進行するため、成形停止時のパージ処理や温度管理が非常に重要です。
また、加工現場では換気設備の整備も必須であり、局所排気装置(局排)を設置してガスの拡散を防止する必要があります。
特に連続成形を行う場合や、ホモポリマーPOMを使用する場合は、作業者の安全を確保するための環境整備が求められます。
2. 静電気・粉じんの発生と対策
POMは他のプラスチックと比べると静電気を帯びにくい特性を持っていますが、切削加工やサンダー仕上げなどで微粉が発生する場合には、静電気によって加工機内部や製品表面に粉じんが付着することがあります。
これにより製品の表面品質が低下したり、加工機のトラブルを引き起こす場合もあります。
このため、加工現場には静電気除去装置の導入やエアブローによる除塵処理を行うのが有効です。
また、吸引装置付きの加工機を使用すれば、クリーンな環境を保ちつつ効率的に作業が進められます。
3. クラック(亀裂)の発生リスク
POMは機械的強度に優れる一方、局所的な応力集中や化学薬品との接触によって亀裂が生じる場合があります。
例えば、タップ加工やプレス嵌合などで部品に過大な力を加えると、内部応力によって微細なクラックが発生し、長期的な使用により破損に至ることもあります。
これを防ぐためには、設計段階での応力分散構造の工夫や、加工後のアニール処理(応力除去)が有効です。
また、POMは耐薬品性に優れる一方で、酸化剤や強酸には弱いため、使用する洗浄液や接着剤などにも注意が必要です。
4. バリやヒケ、歪みの対策
射出成形では、POMの流動性が高いため、金型合わせ面からバリが発生しやすいという特性があります。
これは型締力の不足や金型の摩耗、樹脂の過充填が原因であることが多く、適正な保守と成形条件の管理が重要です。
また、収縮率が高いため、製品にヒケ(表面のへこみ)や歪みが生じるケースもあります。
これらを防ぐためには、ゲート位置や冷却バランスの最適化が必要です。
また、金型の温度コントロールと、冷却時間の適正化により、製品の寸法安定性が向上します。
切削加工時においても、長尺物や薄肉部の反りを防止するために、段階的な仕上げ加工や支持治具の工夫が有効です。
5. 環境要因による寸法変化
POMは吸水率が低いため、寸法安定性には優れていますが、それでも温度変化や湿度の影響を受けてわずかな寸法変化が生じることがあります。
特に精密部品や嵌合部などでは、その影響が機能に直結するため、保管・使用環境に配慮する必要があります。
これに対しては、加工後のアニール処理や、使用環境に応じたPOMグレードの選定が有効です。
また、最終製品の使用条件に合わせた試験・検証を行い、長期使用時の変化を見越した設計も重要です。
POMの用途と応用分野
機械部品・工業製品での活用例
POM(ポリアセタール)は、その優れた機械的特性や耐摩耗性、自己潤滑性などにより、多くの工業製品に使用されています。
特に、繰り返しの動作や摺動を伴う部品においては、金属の代替材料として採用されるケースも多く、コストダウンや軽量化、メンテナンス性の向上に大きく貢献しています。
以下では、代表的な機械部品や工業製品でのPOMの活用例を具体的に紹介します。
歯車(ギア)
POMは、高い寸法安定性と耐摩耗性、自己潤滑性を兼ね備えているため、小型モーターや精密機械に使われる歯車に多く採用されています。
特に金属歯車と比べて軽量で、潤滑油が不要な点から、騒音低減やメンテナンスフリーを実現できます。
また、POM製歯車は射出成形により量産性が高く、コストを抑えつつ精密な加工が可能なため、プリンターや複写機、自動車内部のアクチュエータなどにも幅広く使われています。
スライダー・ブッシュ・ベアリング
POMは自己潤滑性に優れ、摺動性が高いため、スライド機構や軸受部品にも適しています。
金属部品では潤滑剤が必要な箇所でも、POMであれば無潤滑でも十分な性能を発揮するため、給油作業の省力化やメンテナンス周期の延長に寄与します。
搬送機器や自動装置、医療機器の内部構造においても、静音性と耐久性の両立を求められる部品としてPOM製スライダーが選ばれています。
カム・ローラー
機械の動作タイミングを制御するカム部品や、回転を支えるローラー部にもPOMは多用されています。
POMは衝撃強度が高く、繰り返し荷重にも強いため、これらの部品が長期間使用されても変形や摩耗が少なく、安定した性能を保ちます。
特にOA機器や食品加工機械などの分野では、金属摩耗粉の混入を嫌うケースも多く、非金属であるPOMが選ばれる理由の一つです。
ファスナー・クリップ・ジョイント
POMは弾性回復性(復元性)にも優れているため、ファスナーやバネのような役割を持つ部品にも適しています。
例えば、自動車の内装に使われるクリップやスナップフィット構造の部品、簡易脱着可能なジョイント部品などに使われることが多く、繰り返しの脱着に対しても変形や破損が少ないのが特徴です。
ポンプ部品・バルブ
POMは耐薬品性にも優れており、水や油に強いため、ポンプのインペラ(羽根車)やバルブ、流路部品などにも採用されています。
水回りの機器や給水装置、洗浄機などでは、金属部品では腐食の恐れがあるため、POMを使用することで長期的な耐久性と安定稼働が確保されます。
自動車分野での使用事例
POM(ポリアセタール)は、自動車業界においても非常に重要なエンジニアリングプラスチックの一つです。
優れた耐摩耗性、自己潤滑性、寸法安定性を活かし、さまざまな内部機構部品に使用されています。
軽量化、静音化、耐久性向上といった自動車の性能向上ニーズに応える素材として、金属部品の代替材料としても注目されています。
ドアロック・パワーウィンドウ機構
自動車のドアロックやパワーウィンドウの機構部品には、高い寸法精度と繰り返し動作に耐える耐摩耗性が要求されます。
POMはこれらの要求に応える素材として、ギア、スライダー、アームなどに採用されています。
金属に比べ軽量で、潤滑油なしでもスムーズに動作するため、メンテナンス性や静音性にも優れています。
また、温度や湿度の変化にも強く、屋外での長期間使用にも安定した性能を発揮します。
燃料系・冷却系の部品
POMの耐薬品性や寸法安定性を活かし、燃料タンク周辺のバルブ部品や、エンジン冷却システムの継手、コネクターなどに広く利用されています。
特に、ホースコネクターやフュエルラインのジョイント部品では、軽量で加工しやすく、高い密閉性を維持できることから採用が進んでいます。
また、吸水率が低いため、樹脂膨張によるリークリスクも小さく、信頼性の高い部品設計が可能です。
内装部品:スイッチ、ノブ、クリップなど
POMの良好な成形性と剛性、そして表面仕上がりの美しさは、自動車内装部品にも最適です。
スイッチ類の可動部、シートのリクライニング部、インパネ周辺の機構部品などに多く採用されています。
特に、クリップや嵌合部品には、POMの弾性回復性(スナップ性)が活かされており、脱着を繰り返しても破損しにくいという特長があります。
駆動系の補助部品
POMはエンジンやトランスミッションなどの直接的な高負荷部分には用いられないものの、それらの補助機構としての使用が広がっています。
たとえば、タイミングベルトテンショナーのガイド部、ウォーターポンプの補助ギア、あるいは電動モーターの内部構成部品など、繰り返し摺動と静音性が求められる補助構造においてPOMは高い評価を受けています。
EV(電気自動車)・次世代車両における需要拡大
近年では、EV(電気自動車)の普及により、軽量で絶縁性のある樹脂材料の需要が増加しています。
POMは高い耐熱性と電気絶縁性を備えていることから、モーター周辺部品、バッテリー冷却系部品、電装品の可動部などに採用が広がっています。
金属と異なり腐食の心配がないため、車両の寿命延長にも貢献しています。
電子機器・OA機器への展開
POM(ポリアセタール)は、その高い寸法精度、耐摩耗性、自己潤滑性を活かし、電子機器やOA(オフィスオートメーション)機器の内部部品としても幅広く利用されています。
これらの分野では、特に小型・高精度で、繰り返しの動作や摺動が伴う機構部品において、POMの特性が非常に有効です。
また、成形性に優れており、複雑な形状の部品を一体成形できるため、コスト面や設計自由度の高さからも重宝されています。
プリンター・コピー機の可動部品
プリンターやコピー機などのOA機器では、紙送り機構、トナーカートリッジの駆動部、カム、ローラー、ギアなどの多くの部品にPOMが使用されています。
これらの部品には、高精度でスムーズな摺動性と耐久性が求められます。
POMは潤滑性が高く、潤滑油なしでも長期間の動作が可能なため、機器の信頼性向上とメンテナンスコストの削減に貢献します。
また、金属部品と比較して軽量で静音性にも優れており、製品全体の静音化にもつながります。
ファクシミリ・スキャナーの搬送系部品
ファクシミリやスキャナーでは、原稿や紙を送り込むローラーやガイドレールにPOMが用いられています。
ここでは、安定した摩擦係数と耐摩耗性、かつ紙やフィルムに対して傷を付けない柔軟な摺動性が求められます。
POMは表面性状も滑らかで、精密な紙搬送を必要とする機器にとって理想的な素材のひとつです。
また、湿度や温度の変化にも強いため、設置環境を問わず安定したパフォーマンスを発揮します。
パソコン周辺機器の内部部品
パソコンや周辺機器(マウス、キーボード、CD/DVDドライブなど)では、POMがガイド機構やギア、軸受け、バネ部品として使用されています。
クリック機構や押下構造では、弾性回復性と耐疲労性が活かされ、長寿命化に貢献します。
キーボードのパンタグラフ構造や、スプリング機構の支持部材などにも活用されており、軽快な操作感と耐久性の両立が求められる領域で特に重宝されています。
家庭用電化製品(家電)での使用
家電製品においても、POMは内部の可動部品、ジョイント部、ギア部品などに利用されています。
例えば、炊飯器のフタ開閉機構、掃除機の回転ブラシの軸受け、扇風機の首振り部など、軽量かつ高強度が求められる部位において、金属の代替材料として導入されており、設計自由度の向上にも貢献しています。
さらに、POMは食品衛生法に適合するグレードも存在するため、一部の調理家電や給水機器にも使われています。
精密機器のモジュール部品
カメラや医療機器、分析機器などの精密機器では、ミクロ単位の精度が求められる小型モジュール部品にPOMが利用されます。
温度変化に対しての寸法変化が小さく、かつ長期的に安定した形状を維持するため、精密な動作を必要とする構造に適しています。
たとえば、カメラのズーム機構のギアや、可動レンズ部のスライドガイドなどにも採用されており、微細な動きを支える要として機能しています。
このように、POMは電子機器やOA機器分野においても、その特性を活かして多数の応用実績を持つ素材です。
特に、「小型・高精度・繰り返し動作が求められる分野」において、今後も需要の拡大が見込まれます。
医療・食品業界での利用可能性
POM(ポリアセタール)は、一般的に産業機械や自動車部品に多く使用される素材ですが、その中でも特定のグレードは医療機器や食品関連機器にも応用されています。
医療・食品業界においては、素材に対して高い安全性・衛生性・耐薬品性・寸法安定性などの特性が求められます。
POMはこれらの要件の一部を満たす材料として、適切な条件下での使用が可能です。
食品衛生法・FDA適合グレードの存在
POMの中には、日本の食品衛生法や米国FDA(食品医薬品局)の規格に適合した食品接触可能なグレードが存在します。
これにより、食品の加工機械や充填装置、搬送ラインの部品などにおいて、金属や他の樹脂に代わる材料としてPOMが選ばれることがあります。
たとえば、ローラー、スライド部品、ギア、ピン、ベアリングなどがPOMで製造されることがあります。
これらの部品には、摩耗や衝撃に強く、滑らかな動作が必要とされる場面が多く、POMの自己潤滑性や耐摩耗性、加工精度の高さがそのまま品質維持に直結します。
また、POMは比較的吸水率が低いため、湿気による寸法変化が小さく、衛生面の管理が重要な環境にも適しています。
医療用デバイスの機構部品
医療分野においては、POMは薬液の注入機器や外科手術器具の一部、分析装置の構成部品などに使用されています。
これらの用途では、精密な動作、耐薬品性、耐久性が要求されるため、POMは非常に適した素材です。
とくに、POMはホルムアルデヒドが含まれていない医療用グレードを選定することで、患者や医療従事者への安全性にも配慮することが可能です。
また、手術用機器や診断装置に用いられる小型ギア、軸受け、カム部品などでは、高い加工精度と長寿命が両立できる点が評価されています。
特にPOMは、反復動作の多い用途でも摺動面が劣化しにくく、精度を長期間維持できるという特徴があります。
滅菌対応や薬品耐性についての注意点
ただし、医療・食品分野でのPOM使用には注意点もあります。
POMは、高温・高圧の蒸気滅菌(オートクレーブ)には弱く、熱による変形や劣化のリスクがあります。
そのため、滅菌が前提となる部品には、POM以外のエンジニアリングプラスチック(例:PEEKやPPSUなど)が使われることもあります。
また、強酸や強アルカリには劣化する可能性があるため、使用環境の薬品との相性を事前に確認することが重要です。
アルコールや中性洗剤への耐性は比較的良好ですが、長時間の接触や高濃度条件では材質劣化のリスクがあるため、仕様書やメーカー推奨値の確認が必須です。
メンテナンス性と安全性のバランス
POMは金属に比べて軽量で加工がしやすく、静音性にも優れるため、装置の軽量化や静音化に貢献します。
さらに、POMは摩擦による発塵が比較的少ないため、クリーンルームなどの衛生管理が求められる環境にも適しています。
ただし、磨耗粉や素材そのものがコンタミネーション源にならないよう、適切な設計や保守体制の整備が求められます。
以上のように、POMは医療・食品業界においても、安全性や機能性を満たした適切なグレードを選定することで、多様な用途に応用可能な素材です。
特に高精度・高耐久性が求められる動作部品では、今後も需要が期待されます。
POMのメリットとデメリット
POM(ポリアセタール)は、エンジニアリングプラスチックの中でもバランスの取れた性能を有し、工業製品に幅広く用いられています。
しかし、どんな素材にも長所と短所があり、POMにも注意すべき特性があります。
ここでは、POMの特性を「摺動性」「耐薬品性・耐熱性」「加工や使用時の注意点」から整理し、メリットとデメリットを具体的に解説します。
優れた摺動性と耐摩耗性
POMの最大の特長のひとつが、優れた摺動性(すべりやすさ)と耐摩耗性です。
これはギアやスライド機構、ベアリングなど、他の部材と接触しながら動く用途において特に重宝されます。
POMの分子構造は結晶性が高く、分子間の結合が強固なため、摩擦による表面の劣化が起こりにくいという利点があります。
この摺動性は、潤滑油が不要な“ドライ環境”でも性能を維持できることを意味しており、潤滑剤による汚染が許されない機器(医療機器や食品機器など)においても活用可能です。
また、耐摩耗性に優れることで、長期間の使用でも性能を維持しやすく、部品の交換頻度を減らせる点は、メンテナンス性の観点でもメリットとなります。
さらに、金属と比べて軽量で音鳴りが少ないこともあり、静音性を求められる装置にも適しています。
たとえば、OA機器や自動車内装部品では、金属ギアに代わってPOM製ギアが使われることが多く、機器全体の静音化に寄与しています。
ただし、摩擦相手の材質や潤滑条件によっては、摩耗量が変化するため、用途に応じた材料選定と設計が重要です。
とくに、POM同士の接触や、粗い金属面との接触では摩耗が進行することがあるため、摺動ペアの工夫が求められます。
耐薬品性・耐熱性の観点からの評価
POMは化学的安定性が高く、さまざまな薬品や溶剤に対して耐性を持つため、耐薬品性が重要な用途にも対応できます。
特にアルコール類、ガソリン、油類、グリコール、希酸・希アルカリに対しては安定しており、薬品の飛沫や洗浄時の化学接触が想定される機器でも長寿命を維持できます。
一方で、強酸(硝酸・塩酸など)や強アルカリ(苛性ソーダなど)には耐性が低く、分解や劣化を引き起こすため、これらの薬品を使用する環境では不向きです。
また、POMにはホルムアルデヒドの残留があるため、分解時にガスが発生することもあり、密閉空間や高温下では取り扱いに注意が必要です。
耐熱性については、POMの連続使用温度はおよそ80〜100℃程度であり、耐熱性は中程度といえます。
短時間であれば120℃程度にも耐えられますが、長時間の加熱やオートクレーブ滅菌のような高温高湿の条件下では、寸法変化や物性低下が起こる可能性があります。
また、POMは自己消火性は持たないため、耐燃性を必要とする用途では難燃グレードを使用するか、他の樹脂との比較検討が必要です。
UL規格(UL94)でV-0グレードをクリアするには、添加剤入りの特殊グレードが選定されます。
このように、POMは幅広い薬品に対して優れた耐性を示しますが、極端な温度や特定の薬品には制約があるため、使用環境の詳細に応じた材料評価が求められます。
加工時や使用時の注意点
POMは加工性に優れた樹脂であり、射出成形や切削加工で精密な製品を製造できる一方で、加工時・使用時に特有の注意点もいくつか存在します。
まず、POMの射出成形において注意すべきは熱分解によるホルムアルデヒドガスの発生です。
成形温度が高すぎたり、滞留時間が長くなると、材料が劣化しホルムアルデヒドが発生します。
これは刺激臭があり有害なガスのため、成形設備には適切な換気や排気システムが必要です。
また、樹脂の乾燥は不要とされることが多いPOMですが、加工前に含水率や保存状態をチェックすることでトラブルを回避できます。
切削加工においては、POMは切削性が良くバリが少ないという利点がありますが、逆に加工温度が上がると溶けたり変形したりしやすいという性質もあります。
高回転・高送り条件では発熱により切削面が荒れたり、ワークが膨張して寸法精度に影響が出ることがあります。
低速・多刃工具を使うことで熱の発生を抑える工夫が必要です。
さらに、POMは吸水性が非常に低いとはいえ、長期間の湿潤環境下ではわずかに寸法変化が起こることもあり、高精度用途では温湿度変化に配慮した設計が求められます。
使用中においても、紫外線に弱い(屋外劣化しやすい)という性質があるため、長期間の屋外使用には適しません。
紫外線安定剤を含有したグレードや、塗装・コーティングでの保護が必要になります。
また、POM同士のすべり接触では静電気の発生も問題となることがあり、静電気除去対策や帯電防止グレードの採用も検討ポイントになります。
POMの部品加工の見積り依頼ならアスクへ
試作品や小ロットの加工も大歓迎!
特に手のひらサイズの部品製作を得意としています。
アスクなら、試作品のお見積もりが最短1時間で可能!!
お気軽にお問い合わせください。
試作全国対応!
簡単・最短1時間お見積り
他、ブログ記事もご覧ください♪
動画の投稿もしておりますので良ければご覧ください♪