TIG溶接の特徴や加工方法お伝えします!
本日はTIG溶接について解説していきます!
特徴や加工方法などお伝えしていきますので、是非ご覧ください♪
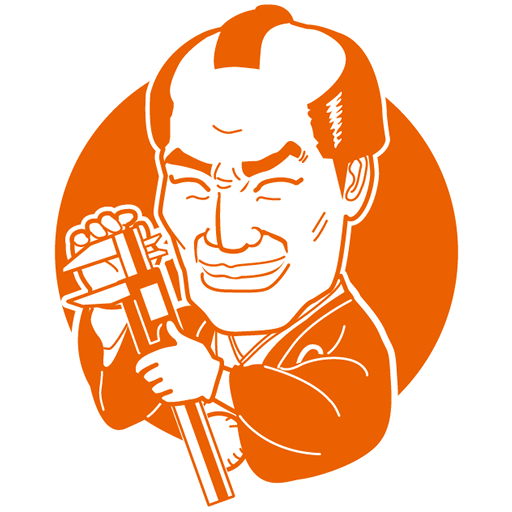
TIG溶接とは
TIG溶接(Tungsten Inert Gas Welding)は、アーク溶接の一種であり、不活性ガス(Inert Gas)を使って電極と母材間にアークを発生させ、その熱で金属を溶かして接合する溶接方法です。
日本語では「タングステン不活性ガス溶接」と呼ばれ、「ティグ溶接」と発音されます。
アメリカでは「GTAW(Gas Tungsten Arc Welding)」という名称でも知られています。
この溶接法の大きな特徴は、タングステン電極を使用する点です。
タングステンは融点が高く、アーク熱で溶けにくいため、消耗しにくい電極材料として適しています。
TIG溶接ではこのタングステン電極と母材の間に高温のアークを発生させ、母材を溶融して接合します。
電極自体は溶け込まず、溶接ワイヤ(フィラー材)を必要に応じて手動で供給することにより、接合部の肉盛りが行われます。
また、アーク部分や溶融金属が酸化しないよう、アルゴンやヘリウムといった不活性ガスをトーチの先端から吹き付けて保護します。
これにより、大気中の酸素や窒素との反応が抑えられ、酸化・窒化による劣化やピット(孔)などの欠陥を防ぐことができるのです。
アルゴンは特に扱いやすく、TIG溶接では最も一般的に用いられています。
TIG溶接は、他の溶接法と比べて非常に美しく、高精度な溶接が可能であり、溶接ビード(接合部の盛り上がり)の見た目が重要な製品や、耐食性・気密性が求められる製品に多く用いられます。
例えば、ステンレス製のパイプやタンク、アルミ部品、医療・航空機器などが代表的です。
一方で、アークの制御やトーチの取り回し、溶加棒のタイミングなどに高度な技術が必要とされるため、初心者には難易度の高い溶接法でもあります。
特に薄板や小径パイプなどでは、熱のかけ方ひとつで溶け落ちたり、穴が空いたりするリスクがあるため、熟練者による作業が求められます。
このように、TIG溶接は高品質な溶接を可能にする反面、高度な技術力と正確な設定が要求されるプロフェッショナル向けの溶接法と言えるでしょう。
精密さと仕上がりの美しさを両立できる点が、TIG溶接の大きな魅力です。
使用される主な材料と適用分野
TIG溶接は、その高い精度と美しい仕上がりにより、幅広い金属材料と分野で利用されています。
特に、酸化や窒化による劣化を防ぎながら、精密な溶接を必要とする材料や製品に適しており、他の溶接法では難しい薄板や非鉄金属にも対応可能です。
ここでは、TIG溶接でよく用いられる金属材料と、代表的な適用分野について解説します。
● TIG溶接に適した金属材料
ステンレス鋼(SUS304、SUS316 など)
TIG溶接と相性のよい代表的な材料がステンレス鋼です。
ステンレスは耐食性に優れ、医療機器、食品機器、化学プラント、建築装飾など幅広い分野で使用されていますが、その性質上、酸化を嫌います。
TIG溶接は不活性ガスによってアークや溶融池を保護するため、酸化の少ない美しい仕上がりが得られます。
特にSUS304(オーステナイト系)やSUS316(耐薬品性に優れる)が多用されます。
アルミニウムおよびアルミ合金(A5052、A6061 など)
アルミは軽量で加工性がよいものの、表面に酸化被膜ができやすく、溶接が難しい金属です。
TIG溶接では交流(AC)モードを使用することで酸化膜を除去しながら溶接ができるため、アルミ溶接に適しています。
特にA5052(耐食性・成形性が良好)やA6061(強度と加工性のバランスに優れる)などが多く利用され、自動車部品や航空機部品、アルミ構造物などで活用されます。
チタンおよびチタン合金
チタンは高強度で軽量、かつ耐食性にも優れるため、航空宇宙、医療機器、化学装置などのハイエンド分野で用いられます。
ただし、大気中の酸素・窒素との反応性が非常に高いため、溶接時に高レベルのシールド(保護)が求められます。
TIG溶接では高純度アルゴンによるガスシールドが可能なため、チタンの溶接においても高品質な結果が得られると評価されています。
銅および銅合金(真鍮など)
銅は熱伝導性が高く、アーク熱がすぐに拡散してしまうため、溶接が難しい素材ですが、TIG溶接による細かな熱制御で対応可能です。
銅配管や電気接点部品、熱交換器などの接合に使われることがあります。
真鍮などの銅合金も、母材とフィラー材のマッチングによって良好な溶接結果が得られます。
● TIG溶接が活用される主な分野
医療機器・精密機器
TIG溶接はスパッタやスラグの発生が少なく、溶接部分が清浄で仕上がりが美しいため、医療機器のような高衛生性と気密性が求められる製品に適しています。
手術用具や人工関節、滅菌器具などの製造にも使用されています。
航空宇宙産業
航空機部品は軽量・高強度・耐熱性などの特性が要求されるため、アルミ合金やチタンなどが用いられます。
これらの材料に対してもTIG溶接は高い品質を確保できるため、機体のフレーム、タンク、配管など多岐にわたり使用されます。
食品・飲料機器
ステンレス製のタンクや配管は、溶接部に汚れが溜まりにくく、滑らかな内面を保つ必要があります。
TIG溶接はビードを最小限に抑えられ、さらに電解研磨などとの併用で衛生的な仕上げが可能です。
化学プラント・エネルギー設備
耐腐食性が求められる機器に使用されるニッケル合金やステンレス鋼、チタンなどの溶接にもTIG溶接が用いられます。
特に配管の溶接ではリークを防ぐため、TIG溶接による気密性の高い接合が重視されます。
モータースポーツ・カスタムバイク・アート作品
TIG溶接は、美しいビード模様が形成されることから、カスタムバイクのフレーム、エキゾーストパイプ、アート作品など、「見せる溶接」としての要素も評価されています。
他の溶接法との違い
TIG溶接は、多くの溶接法の中でも特に「精密性」「美観」「制御性」に優れる工法ですが、その特徴をより深く理解するためには、他の代表的な溶接法と比較することが重要です。
ここでは主に「被覆アーク溶接(手溶接)」「MIG/MAG溶接」「レーザー溶接」などと比較し、TIG溶接の位置づけを明確にしていきます。
● 被覆アーク溶接(SMAW)との比較
被覆アーク溶接は、手溶接として広く使われており、電極自体が溶接棒(被覆された金属棒)となるタイプです。
溶接棒が消耗しながらアークを発生し、同時に溶加材としても働きます。
比較的安価で、装置も簡便なため建設現場などで多用されていますが、スパッタ(飛び散り)やスラグ(溶けたフラックスのカス)などが発生しやすく、仕上がりが粗くなる傾向があります。
一方、TIG溶接では非消耗電極(タングステン)を使用し、必要に応じて別途溶加棒を手で供給します。
そのため、作業の自由度が高く、スラグやスパッタの発生もほとんどなく、よりクリーンで美しい仕上がりを実現できます。
● MIG/MAG溶接との比較
MIG(Metal Inert Gas)溶接およびMAG(Metal Active Gas)溶接は、半自動溶接とも呼ばれ、ワイヤを自動供給しながらガスでシールドする方式です。
これらは作業スピードが速く、量産性にも優れるため、自動車や重機、製缶業界などの量産分野でよく使われています。
特にMAGは炭酸ガスなどのアクティブガスを使用し、コストパフォーマンスも良好です。
対してTIG溶接は、操作が手動かつ溶加材も手作業で供給するため、スピードは劣るものの、高精度な制御が可能で、薄板や小径部品などにも対応できる点が大きな利点です。
スパッタの少なさや仕上がりの美しさはMIG/MAGにはない魅力です。
● レーザー溶接との比較
近年注目されているレーザー溶接は、レーザー光を高エネルギー密度の熱源として利用する精密な溶接法です。
非常に高速かつ低歪みでの加工が可能であり、自動化にも優れていますが、設備コストが高く、加工対象の形状や材料に制約がある場合もあります。
これに対しTIG溶接は、設備投資がレーザーよりは抑えられ、複雑形状の手加工や多様な材質に対して柔軟に対応できる点で優れています。
特に、熟練した職人による手作業が強みとなる場面では、レーザーでは代替できない価値があります。
● TIG溶接の立ち位置
総じて言えば、TIG溶接は「スピードよりも品質・精度・美観を重視する」溶接法です。
自動車部品の大量生産にはMIG溶接、建設現場では被覆アーク溶接、超精密部品や重要な構造体の接合にはTIG溶接、というように、用途によって最適な溶接法は異なります。
TIG溶接は、「見せる溶接」や「精密性が求められる溶接」に特化して選ばれる技術であり、他の溶接法との違いを理解することで、その活用価値がより明確になります。
TIG溶接のメリットとデメリット
TIG溶接のメリット
TIG溶接は他のアーク溶接法と比較して、いくつかの明確な利点を持っています。
特に「高品質・高精度な溶接が求められる場面」では重宝される工法です。
以下にその主なメリットを紹介します。
1. 高品質な仕上がり
TIG溶接の最大の特徴は、「溶接ビードが美しく、欠陥が少ない」という点です。
溶接中にスラグ(溶けたフラックス)やスパッタ(金属の飛び散り)が発生しないため、仕上がりが非常にクリーンで、追加の後処理が最小限で済みます。
また、溶接熱が比較的集中しており、母材への熱影響(HAZ: Heat Affected Zone)が小さいため、寸法変化や歪みが少なく抑えられます。
これにより、精密部品の溶接や装飾部品の接合にも適しています。
2. 薄板の溶接に最適
TIG溶接は、電流調整の幅が広く、繊細なアーク制御が可能なため、0.3mm前後の極薄板にも対応できます。
これは他のアーク溶接(MIG、被覆アークなど)では困難な領域です。
たとえば、医療機器・電子機器の筐体や、精密なパイプの接合などにおいて、TIG溶接の微細制御は非常に有効です。
3. 多くの金属に対応可能
TIG溶接は、鉄・ステンレス・アルミニウム・チタン・銅・ニッケル合金など、多様な金属に対応しています。
特に酸化しやすい金属(アルミやチタンなど)では、不活性ガスによる保護効果が非常に大きく、安定した溶接が可能です。
また、異種金属の接合(例:ステンレスと銅)など、条件に応じて工夫することで実現可能な点も評価されています。
4. 精密な溶接操作が可能
トーチとフィラー(溶加棒)を手動で分けて操作できるため、熟練すればアーク熱と材料供給のバランスを自在にコントロールできます。
これにより、複雑形状の継手や微細部の補修にも柔軟に対応できます。
また、電流の上昇や下降をフットスイッチで制御できる機種も多く、工程ごとの加熱条件を精密に制御できます。
5. 清潔な作業環境
TIG溶接はスパッタが少なく、煙や臭いも他の溶接法に比べて少なめです。
これにより、作業者のストレス軽減や、工場内の清掃・メンテナンスの効率向上にもつながります。
特にクリーンルームや室内作業が求められる分野(医療・食品・半導体など)においては、TIG溶接が選ばれる大きな理由の一つです。
まとめ
TIG溶接のメリットは、「高精度」「高品質」「多用途」といった特性に集約されます。
自動化装置とも組み合わせやすく、手動作業でも丁寧な管理が可能なため、信頼性の高い接合を実現できるのが大きな魅力です。
TIG溶接のデメリット
TIG溶接は高品質な溶接が可能な反面、いくつかのデメリットも抱えています。
これらの要因により、TIG溶接が最適とは言えない加工現場も存在します。
ここでは代表的なデメリットを詳しく解説します。
1. 作業効率が低い
TIG溶接は他のアーク溶接に比べて作業スピードが遅いという欠点があります。
MIG溶接や被覆アーク溶接では、比較的早い速度で接合が可能ですが、TIGは溶接トーチと溶加棒を別々に操作する必要があり、常に丁寧な手作業が求められます。
また、スタートや終了時のアーク制御も慎重に行う必要があるため、特に熟練していない作業者にとっては時間がかかりやすくなります。
大量生産や長尺構造物の溶接では、非効率になりやすい点は大きなマイナスです。
2. 熟練した技術が必要
TIG溶接はその品質の高さゆえに、高い技能が要求される溶接法です。
溶接トーチの角度、距離、溶加棒の供給タイミング、アーク長の維持、ガスシールド範囲の確保など、複数の要素を同時に管理する必要があります。
初心者が扱うとアークが不安定になりやすく、溶け込み不足やブローホール(気泡欠陥)、酸化、ピット(小穴)などの不具合が発生しやすくなります。
そのため、多くの現場ではTIG溶接専門の溶接士が必要になります。
3. 装置が高価で設置にも制限
TIG溶接機は一般的にMIG溶接機よりも高価です。
また、アルミニウムやマグネシウムなどの材料をTIG溶接する際には、AC(交流)機能を持つ高機能モデルが必要となり、さらに設備コストが増します。
加えて、溶接中はアルゴンガスなどの不活性ガスを絶えず供給する必要があるため、ガスのコストも継続的に発生します。
屋外での作業では風によってガスシールドが乱れることもあり、屋内に限って使われるケースが多いのも制限のひとつです。
4. 厚板の溶接には不向き
TIG溶接は、熱源が集中しておりコントロール性に優れる反面、入熱量が少ないため厚板の溶接には向いていません。
厚みが5mmを超えるような鋼板や構造部材などでは、溶け込みが浅く、複数回の溶接が必要になるか、他の工法と組み合わせる必要が出てきます。
このような場合、深い溶け込みが得られるMIG溶接やサブマージアーク溶接(SAW)が採用されることが多く、TIGはあくまで精密用途や薄板向けの工法としての位置付けになります。
5. 屋外使用に制限がある
TIG溶接はアルゴンなどの不活性ガスによる保護が必須です。
風が強い屋外ではガスが流されてしまい、シールド効果が失われてしまうため、溶接部が酸化しやすくなります。
これにより溶接不良が起こる可能性が高まります。
そのため、現場溶接や建設現場などでは使いにくく、風防や溶接テントを設けるなどの対策が必要です。
この点では、フラックスを使用する被覆アーク溶接のほうが安定して使用できます。
まとめ
TIG溶接は確かに高品質な溶接が可能ですが、それには高コスト・高技能・作業環境の制約といった条件が伴います。
効率や量産性を重視する現場には向かず、精密さや外観品質を重視する場面に特化した溶接法といえるでしょう。
TIG溶接に適した材料と用途
TIG溶接に適した材料の種類
TIG溶接は、アーク溶接の中でも特に幅広い金属材料に対応できる溶接方法です。
これは、溶接中にアルゴンやヘリウムなどの不活性ガスでアークと溶接部を保護するため、酸化や窒化などの不良を抑えることができるためです。
ここでは、TIG溶接に適している主な金属材料を紹介します。
ステンレス鋼
TIG溶接と特に相性が良いのがステンレス鋼です。
SUS304やSUS316といったオーステナイト系ステンレスをはじめ、フェライト系、マルテンサイト系、二相系なども適用可能です。
ステンレスは酸化しやすい金属ですが、不活性ガスによる保護が強いTIG溶接では酸化を最小限に抑えられ、高品質な溶接が実現できます。
特に食品機械、医療機器、化学装置など、衛生面や耐腐食性が求められる分野では、TIG溶接で仕上げたクリーンな接合部が評価されます。
アルミニウムおよびアルミ合金
アルミニウムは酸化被膜が非常に強いため、溶接が難しい材料のひとつですが、TIG溶接では交流(AC)モードを使用することで酸化被膜を破壊しながら溶接することが可能です。
代表的なアルミ合金であるA5052、A6061なども問題なく溶接でき、航空機部品、自動車部品、アルミフレームなどに広く利用されています。
溶接ビードが美しく、溶接後の外観性も高いため、アルミ加工においてはTIGが選ばれることが多くあります。
チタンおよびチタン合金
チタンは非常に酸化しやすく、一般的なアーク溶接では酸化による溶接不良が問題になります。
しかしTIG溶接であれば、不活性ガスによる強力なシールド効果で酸化を防ぎながら溶接可能です。
航空宇宙分野、医療用インプラント、耐食性が必要な装置などでチタンはよく使われます。
チタン溶接では、溶接後の冷却時まで酸化を防ぐため、トーチからの後追いガス(トレーリングシールド)や裏面保護ガスの供給も必要になる点が特徴です。
銅および銅合金
銅は熱伝導率が非常に高く、アーク熱が拡散してしまうため、他の溶接法では溶け込み不足になりがちです。
TIG溶接では細かな電流制御とアーク集中性により、局所的な加熱がしやすく、銅の溶接に向いています。
特にヒートシンクや電気部品の接合において効果を発揮します。
ただし、熱伝導の影響で母材が冷えやすく、電流を大きめに設定したり、プレヒート(予熱)を行ったりするなどの工夫が必要です。
その他(ニッケル合金・モネル・インコネル等)
高温下での耐食性が求められるニッケル系合金(インコネル、モネル、ハステロイなど)も、TIG溶接で対応可能です。
これらの材料は高価ですが、化学装置、原子力機器、耐熱部品などで多用されており、安定した溶接品質が求められる場面でTIG溶接が活躍します。
TIGに不向きな材料は?
一方で、鋳鉄や高炭素鋼など、割れが起きやすい材料や熱影響で硬化しやすい材料は、TIG溶接にはあまり適していません。
溶接前後に予熱や後熱、パルス制御などの高度な管理が必要になるため、技術的なハードルが高くなります。
まとめ
TIG溶接は、ステンレス、アルミ、チタン、銅、ニッケル合金など、酸化や変質に弱い金属の溶接に非常に適した方法です。
これらの材料を対象とした高精度な製品製造や構造体の接合において、TIG溶接はその力を最大限に発揮します。
TIG溶接が活用される具体的な用途
TIG溶接は、美しい仕上がりと高品質な接合が求められる現場で、多くの業界から支持を受けています。
特に外観が重要な製品や溶接強度・耐食性が問われる部品などで選ばれることが多く、手作業での精密な制御が可能である点からも、職人技が活きる加工法といえます。
以下では、具体的な活用事例を業界別に紹介します。
【1】食品・医療機器分野
食品機械や医療機器は、衛生性と耐食性が非常に重視される分野です。
そのため、溶接部にスラグやスパッタなどの異物が残らず、酸化スケールも発生しにくいTIG溶接が多用されます。
特にSUS304やSUS316といったオーステナイト系ステンレスを素材とする配管やタンク、ケーシング部品などでは、TIG溶接による「クリーンな接合」が必須です。
また、医療器具や分析装置では、溶接ビードが極めて狭く目立たないことが重要視されるため、熟練のTIG溶接技術者による細密な溶接が求められます。
【2】航空宇宙産業
航空機やロケットといった構造体には、軽量で高強度な材料(例:チタン合金、アルミニウム合金)が数多く使われています。
これらは酸化しやすく、溶接に細心の注意が必要なため、高い品質と精度を確保できるTIG溶接が選ばれます。
エンジン部品や燃料タンクのような高温・高圧環境で使用される部品では、溶接部の微細な欠陥が致命的な事故につながる恐れがあるため、品質保証の観点からもTIG溶接が不可欠です。
高真空や無重力環境を想定した接合部の信頼性確保にも一役買っています。
【3】自動車・バイク関連
車両関連では、主にマフラーやエキゾーストパイプ、アルミ製のタンクやフレームなどの製造にTIG溶接が使われています。
特にスポーツカーやバイクのカスタムパーツでは、見た目の美しさも重要な評価ポイントとなるため、TIG溶接の美しいビードライン(魚のうろこのような模様)が高く評価されます。
また、レースカーなどの特殊車両では、軽量化と強度の両立が求められ、アルミやチタンの使用が主流です。
TIG溶接は、これらの難加工材に対しても対応可能なため、プロフェッショナルな製造現場では必須の技術となっています。
【4】精密機械・産業機器
精密部品や計測機器などの製造では、寸法精度と耐久性、外観品質がバランスよく求められます。
そのため、最小限の熱影響で繊細な部品を溶接できるTIG溶接が最適です。
溶接部が目立たず、仕上げも容易なことから、微細部品の接合にも活用されています。
たとえば、真空装置のチャンバーや、電子顕微鏡の外装筐体などは、気密性の高い溶接が必要であり、TIG溶接の強力なシールド効果が重宝されます。
【5】建築・装飾用途
建築分野でも、意匠性の高いステンレス手すりやアルミ製パネル、屋外モニュメントなどの製作にTIG溶接が使われています。
外観重視のデザイン構造物では、TIG溶接によって得られる滑らかで整った溶接ビードが、製品の印象を大きく左右します。
また、ステンレス製の厨房機器や店舗什器などもTIG溶接で仕上げられることが多く、美観と耐久性を両立した仕上がりが求められる分野での採用が目立ちます。
まとめ
TIG溶接は、ただ「接合」するだけでなく、「美しさ」や「高精度」「耐食性」といった付加価値を求められる溶接現場に特に適していることがわかります。
自動化が難しい反面、職人による繊細な作業が活かされる現場で、その真価を発揮します。
TIG溶接の見積り依頼ならアスクへ
試作品や小ロットの加工も大歓迎!
特に手のひらサイズの部品製作を得意としています。
アスクなら、試作品のお見積もりが最短1時間で可能!!
お気軽にお問い合わせください。
試作全国対応!
簡単・最短1時間お見積り
他、ブログ記事もご覧ください♪
動画の投稿もしておりますので良ければご覧ください♪