蒸着のメリットや特徴などを徹底解説!!
本日は蒸着について解説していきます!
メリットや特徴、種類などを徹底解説しますので、是非ご覧ください♪
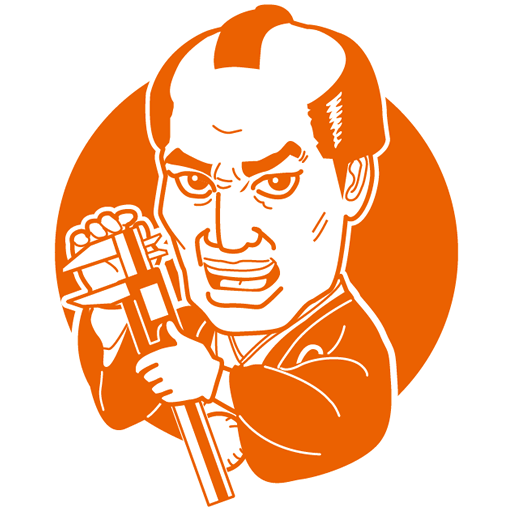
蒸着とは
蒸着(じょうちゃく)とは、真空中または低圧環境下で材料を加熱・蒸発させ、その蒸気を基材(対象となる物体)の表面に凝縮させて薄膜を形成する表面処理技術の一種です。
英語では「Vapor Deposition」と呼ばれ、「Physical Vapor Deposition(PVD)」や「Chemical Vapor Deposition(CVD)」などがその代表例です。
主に金属や無機材料、または機能性を持つ材料を基材の表面に薄く均一に付着させ、目的に応じた特性(耐摩耗性、反射性、導電性、装飾性など)を付加することを目的とします。
蒸着の基本的なメカニズムは「材料の蒸発と凝縮」です。
処理対象の材料(たとえばアルミニウムやチタンなど)を高温で加熱すると、その材料が気化します。
この蒸気が真空中で飛び出し、周囲に存在する冷たい基材表面に到達すると、そこで再び固体として凝縮し、薄い膜となって表面に堆積します。
この膜は極めて薄く、数nm〜数μm程度が一般的で、目的に応じて膜厚の調整も可能です。
蒸着の主な目的は、以下のように多岐にわたります。
・保護膜の形成:基材の耐摩耗性、耐食性、耐熱性を向上させ、長寿命化を図る。
・機能性の付与:導電性、絶縁性、反射性、光透過性、ガスバリア性など、特定の機能を与える。
・装飾性の向上:金属光沢や色彩を持つ薄膜を形成することで、外観を美しくする。
・微細構造の制御:半導体分野ではナノレベルでの微細パターン形成が可能であり、回路やデバイス性能に大きく寄与する。
蒸着処理は、他の表面処理(メッキや塗装など)に比べて「より薄く、より均一で、より純度の高い膜を形成できる」という点で優れています。
また、真空中で行うため、不純物の混入が少なく、精密な制御が可能であることも大きな特長です。
特に電子部品、光学機器、精密機械などの分野では、極めて高い信頼性が求められるため、蒸着技術の利用が不可欠となっています。
このように、蒸着は単なる表面コーティングを超えた、機能設計のための先進的な加工技術であり、現代の製造業において重要な役割を果たしています。
蒸着の歴史と発展
蒸着技術の起源は19世紀後半にまで遡ります。最も初期の例は、1852年に英国の化学者マイケル・ファラデーが金属の蒸気を使ってガラスに薄膜を形成する実験を行ったことに由来すると言われています。
この頃は、科学実験の延長線上にある技術でしたが、20世紀に入るとともに、蒸着は科学研究から実用技術へと発展し始めました。
蒸着技術の大きな転機となったのは、真空技術の進歩です。
1930年代から1940年代にかけて、高真空環境を生成・維持できる装置が開発され、これにより蒸着処理の精度と再現性が大きく向上しました。
当初は金属鏡や光学レンズへの反射防止膜の形成など、光学分野での応用が先行しました。
たとえば、アルミニウムを蒸着させて鏡面反射性を高めたり、マグネシウムフッ化物を使って反射防止コーティングを施すといった用途がその代表です。
1950年代から1960年代には、トランジスタや半導体の登場とともに、蒸着技術はエレクトロニクス分野へ急速に広がりました。
特に、真空蒸着法による金属配線や薄膜トランジスタの製造が可能となり、集積回路(IC)の発展に大きく貢献しました。
また、この頃には「スパッタリング」や「CVD(化学気相成長)」といった蒸着に関連する新技術も並行して登場し、より多様な材料や構造に対応できるようになります。
1980年代には、装飾用途や工業用途にも蒸着技術が浸透しました。
たとえば、自動車の内装部品や化粧品容器、腕時計などへのメタリックな外観仕上げとしての利用が広がり、真空蒸着による「装飾メッキ」として市場を拡大させました。
この時期には、イオンプレーティングやアーク蒸着などの応用技術も実用化され、膜の密着性や硬度をさらに高めることが可能となっています。
21世紀に入り、蒸着技術はナノテクノロジーやバイオテクノロジー分野へも応用が拡がっています。
原子レベルで膜厚を制御できる「原子層堆積(ALD)」や、機能性を付与する複合材料の蒸着などが進展し、現在では薄膜トランジスタ、透明導電膜、有機ELディスプレイ、太陽電池、MEMS(微小電気機械システム)などの分野において不可欠な技術となっています。
このように、蒸着処理は真空技術、材料工学、電子工学などと密接に連携しながら、産業の進化に合わせて発展してきました。
今後も新たな材料や機能のニーズに対応する形で、その応用範囲はさらに拡大していくと見られています。
表面処理との違いと蒸着の特徴
蒸着処理は、表面処理の一種に分類される技術ですが、一般的な表面処理と比べてその性質や用途には明確な違いがあります。
ここでは、蒸着が他の表面処理(たとえばメッキ、塗装、熱処理など)とどのように異なるのかを明確にし、その特徴を整理します。
まず、「表面処理」とは、素材の表面に物理的・化学的な処理を加えることで、外観や性能を改善・強化する技術全般を指します。
主な目的は、耐食性の向上、摩耗防止、美観の向上、密着性の向上、電気的特性の付与などです。
代表的な方法として、亜鉛メッキ、クロムメッキ、粉体塗装、アルマイト処理、焼入れなどが挙げられます。
一方、「蒸着処理」は、真空または低圧環境下で材料を蒸発させ、その蒸気を対象の表面に凝縮させることで薄膜を形成する技術です。
そのため、処理方式としては「真空下での材料蒸散と堆積」という極めて特殊な条件を必要とし、以下のような独自の特徴を備えています。
● 高純度・高精度の薄膜形成
蒸着によって形成される膜は、数ナノメートルから数マイクロメートルの厚さまで制御可能で、非常に薄く均一であることが特徴です。
真空環境で行うため不純物の混入が少なく、純度の高い膜を得ることができます。
これにより、半導体や光学部品など、極めて高い精度とクリーンさが求められる分野で広く利用されています。
● 物理的付着による膜構造
蒸着膜は、基材表面に物理的に堆積する「付着膜」であり、化学反応を伴うものではありません(※PVDの場合)。
そのため、基材自体の化学組成や特性を大きく変化させず、元の素材の特性を維持したまま、表面だけに新しい機能を持たせることが可能です。
● 表面の平滑性・透明性への適性
蒸着処理は非常に緻密で平滑な表面を形成できるため、レンズやディスプレイなど光学用途に適しています。
また、酸化インジウムスズ(ITO)などを使えば、透明導電膜としても機能します。
塗装やメッキでは難しいこのような微細制御が、蒸着では実現可能です。
● 処理コストと設備の違い
蒸着処理は専用の真空装置が必要であり、設備コスト・運用コストが高くなる傾向があります。
一方、メッキや塗装は比較的低コストで大量処理が可能なため、コスト重視の量産用途ではそちらが選ばれることもあります。
蒸着は「高機能・高精度」を求める用途に特化しているといえるでしょう。
● 密着性と耐久性の課題
蒸着膜は、基材との間に強固な化学結合を持たないため、密着性がやや弱い傾向があります。
そのため、プライマー層やバッファ層を設けたり、基材表面の前処理(洗浄やイオンエッチングなど)を行ったりして、密着力を高める工夫が必要となります。
このように、蒸着処理は一般的な表面処理とは異なり、「精密性」「純度」「機能性」に特化した高度な技術です。
その分、要求される技術水準やコストも高くなりますが、得られる成果も非常に大きいため、特定の高付加価値製品に不可欠な処理法となっています。
蒸着の種類と原理
真空蒸着(PVD)の仕組み
真空蒸着とは、「Physical Vapor Deposition(物理的気相成長)」の一種であり、加熱により材料を蒸発させ、真空中でその蒸気を基材に凝縮させることで薄膜を形成する技術です。
一般に「PVD」と略され、他のPVD技術(スパッタリング、アーク蒸着、イオンプレーティングなど)と区別する場合には「熱蒸着」あるいは「真空蒸着」と呼ばれます。
最も古く、かつ基本的な蒸着技術の一つです。
● プロセスの概要
・真空引き
処理チャンバー(蒸着装置の内部)を高真空状態にします。
通常、10⁻³〜10⁻⁶ Pa 程度の真空にまで減圧され、不純物のない状態が作られます。
これにより、蒸発した材料の分子が空気中の分子と衝突することなく基材に到達できるようになります。
・材料の加熱・蒸発
蒸着材料(ターゲット)は、電気抵抗加熱(ボート式やコイル式)、電子ビーム加熱(EB蒸着)、レーザー加熱などで昇温されます。
金属であれば約1000〜2000℃、酸化物であればそれ以上の温度が必要になることもあります。
加熱により、材料が気化して真空中に蒸気が広がります。
・膜の形成
蒸気状になった材料は、チャンバー内に設置された冷却された基材表面に達し、凝縮して固体膜となります。
このプロセスによって、原子レベルで均一な薄膜が形成されます。
膜厚は数nm(ナノメートル)〜数μm(マイクロメートル)で調整可能です。
● 使用される装置構成
主な構成は以下の通りです。
・真空チャンバー
・真空ポンプ(ロータリーポンプ+ターボ分子ポンプ等)
・蒸発源(抵抗加熱、電子ビーム等)
・基材ホルダー(加熱回転機構を備えることも)
・膜厚モニタ(石英振動子など)
近年では、自動制御によるプロセスの安定化が進み、膜厚や蒸着速度をリアルタイムで制御できるシステムも一般化しています。
● 特徴と利点
・高純度な膜形成:真空中で処理するため、酸化や不純物の混入が少なく、極めて純度の高い膜を形成できます。
・低温処理が可能:材料の蒸発と凝縮という物理的プロセスであるため、基材を高温に晒さずに済み、樹脂やフィルムなどの熱に弱い素材にも適用できます。
・機械的応力の少ない膜:PVDの中でも熱蒸着は、膜内部にストレスがかかりにくく、光学特性や電気特性が安定しやすい傾向があります。
● 課題と制限
・密着性の問題:蒸着膜は物理的に付着しているだけなので、下地処理が不十分だと剥離しやすくなる可能性があります。表面洗浄やバッファ層の設置が重要です。
・形状依存性:蒸気は直進性が高いため、凹凸のある基材や複雑形状には膜が均一に付きにくく、シャドーイング現象が発生することがあります。
・材料制限:揮発性が低い材料(タングステン、グラファイトなど)は加熱が難しく、蒸着に適さないことがあります。
真空蒸着は、単層の金属膜から多層の光学膜まで幅広い応用に対応しており、特に光学機器、半導体部品、装飾用途においてその性能が発揮されます。
シンプルながらも精密性と再現性に優れる技術であり、現在でも重要な表面処理手段として多用されています。
化学的蒸着(CVD)のプロセス
化学的蒸着(Chemical Vapor Deposition:CVD)は、気体状の原料(前駆体)を反応性雰囲気中で基材表面に導入し、そこで化学反応を起こさせて薄膜を形成する技術です。
蒸着といっても、物理的な蒸発・凝縮を主とするPVDとは異なり、CVDでは化学反応によって新たな物質を合成し、堆積させることが最大の特徴です。
このため、膜材料の自由度が高く、複雑な構造の基材にも均一な膜を形成できるという利点があります。
● CVDの基本プロセス
・原料ガスの導入
主に金属または非金属のハロゲン化物、アルコキシド、炭化物、有機金属化合物などの揮発性物質が原料となります。
これらをキャリアガス(例:水素、窒素、アルゴン)とともに反応チャンバー内に供給します。
・基材への吸着と反応
基材は適切な温度に加熱されており、到達したガス成分が基材表面に吸着します。
吸着された化合物が表面で化学反応を起こし、目的とする薄膜物質が堆積されます。
この際、副生成物(たとえばHCl、COなど)は気体として排出されます。
・膜の成長と排気
反応により形成された膜が徐々に厚みを増していきます。
反応ガスや副生成物は連続的に排気され、チャンバー内の雰囲気を一定に保ちます。
成膜条件(温度、圧力、ガス流量など)を調整することで、膜質や厚さを精密にコントロール可能です。
● CVDの分類
CVDにはいくつかの方式があり、用途や膜材料に応じて使い分けられます
・熱CVD(Hot-Wall CVD)
基材を高温(通常500〜1000℃)に加熱して反応を促進する方式。結晶性の高い膜を得やすい。
・低圧CVD(LPCVD)
減圧下で行うことで、膜の均一性と純度を向上。半導体製造に多用される。
プラズマCVD(PECVD) プラズマを用いて低温下でも化学反応を進行させる技術。
熱に弱い材料にも適用できる。
・金属有機CVD(MOCVD)
金属有機化合物を原料とするCVD。
LEDやパワーデバイス材料(GaN、InPなど)の成膜に重要。
● 特徴と利点
・高い被覆性
反応ガスが基材の隅々まで拡散するため、複雑な3D形状や微細構造の内部にも膜を形成できる。
・材料の自由度が高い
PVDでは難しい化合物(Si₃N₄、SiO₂、TiC、Al₂O₃など)やセラミック膜の形成が可能。
・膜質の選択性
反応条件に応じて、非晶質膜、結晶膜、多結晶膜など様々な構造を制御できる。
● 課題と注意点
・高温処理の必要性
特に熱CVDでは高温加熱が必要となるため、樹脂基材や熱に弱い構造体には不向き。
・副生成物の処理
反応時に発生する有害なガス(フッ化水素、塩化水素など)への対策が必要。
・プロセスの複雑性
気体反応を制御するためには高度な設備とプロセス制御技術が求められる。
CVDは、PVDでは困難な材料を成膜できることから、半導体や光デバイス、セラミックコーティング、バリア膜など、より専門性の高い用途に幅広く利用されています。
特に、ナノスケールの均一性や化学的安定性が求められる分野で、その真価が発揮される技術です。
スパッタリングとの違いと使い分け
スパッタリングは蒸着処理の一種であり、ターゲット材料にイオンを衝突させて原子や分子を弾き飛ばし、その飛散した物質を基材に付着させて薄膜を形成する技術です。
物理的気相成長(PVD)プロセスの代表的な方法の一つで、真空蒸着(熱蒸着)とは異なるメカニズムで膜を形成します。
ここではスパッタリングと蒸着(特に真空蒸着)との違い、及び用途や特長に基づいた使い分けを解説します。
● スパッタリングの特徴
・膜の均一性と密着性の高さ
スパッタリングでは、プラズマ状態のイオンがターゲットに衝突し、原子を弾き飛ばすため、基材表面に向かう粒子はエネルギーを持っていることが多いです。
このため、蒸着よりも基材への密着性が高く、膜の密度や硬度も向上しやすい特徴があります。
・多様な材料への対応
金属だけでなく、酸化物、窒化物、合金、セラミックなど幅広い材料の薄膜を形成できます。
また、複数のターゲットを使い分けて合金膜を作ることも可能です。
・膜厚の均一性に優れる
基材が回転しながら処理されることが多く、複雑な形状でも比較的均一な膜厚を得やすいです。
● 真空蒸着(熱蒸着)との違い
特徴 | 真空蒸着(熱蒸着) | スパッタリング |
---|---|---|
膜形成のメカニズム | 加熱による材料の蒸発と凝縮 | イオン衝突によるターゲットからの原子放出 |
膜の密着性・硬度 | 比較的弱い(密着性に課題あり) | 高い(エネルギー付与により密着性向上) |
処理温度 | 基材を高温にしない場合が多い | プラズマによる基材加熱あり(だが制御可能) |
膜質・膜の種類 | 主に純金属膜や単純酸化物 | 酸化物、窒化物、合金膜など多様な材料対応 |
凹凸形状のカバー力 | 直進性が強くシャドーイング起こりやすい | プラズマ拡散効果で凹凸も比較的均一に覆う |
装置の複雑さ・コスト | 装置構造は比較的単純 | 複雑で高価な装置が多い |
● 使い分けのポイント
・装飾用途や光学コーティング
薄膜の光沢や均一性を重視する場合は、真空蒸着が多く用いられます。
装飾品や鏡面加工されたレンズのコーティングで活躍します。
・耐摩耗性や硬質膜形成が必要な場合
スパッタリングは硬質で密着性の高い膜が得られるため、工具コーティングや機械部品の耐摩耗膜形成に適しています。
・複雑形状の基材への対応
基材の形状が複雑な場合は、プラズマの拡散効果を持つスパッタリングが有利です。
均一な膜厚を確保しやすいです。
・膜材の種類や機能性の要求
酸化物や窒化物膜など機能性膜の形成はスパッタリングが適していることが多いですが、単純な金属膜の迅速な形成には真空蒸着が簡便です。
● まとめ
スパッタリングは、真空蒸着よりも密着性や膜の機能性に優れ、多様な材料に対応できる一方で、装置が高価で複雑です。
真空蒸着は装置が比較的シンプルでコストが抑えられ、装飾的・光学的用途に適しています。
用途や必要な膜の特性に応じて、これらを使い分けることが蒸着処理の効果的な活用に繋がります。
蒸着処理のメリット・デメリット
高機能性コーティングの利点
蒸着処理の最大の魅力は、「高機能性を備えた薄膜」を極めて精密に形成できる点にあります。
これは他の多くの表面処理法(メッキ・塗装・焼き付けなど)と比較しても突出しており、現代の先端技術分野において蒸着が不可欠とされる理由のひとつです。
まず、蒸着によって形成される膜は、数ナノメートル(nm)から数マイクロメートル(μm)の極薄膜でありながら、次のような高機能性を実現できます。
・高い光学特性:反射防止膜、反射膜、干渉膜など、光の波長レベルで厚さを制御することで、精密な光学性能を持たせることが可能。光学レンズやディスプレイ、センサーなどで利用される。
・高硬度・耐摩耗性:蒸着処理で得られる膜は非常に硬く、耐摩耗性に優れる。工具や摺動部品、金型などにも活用されている。
・高密度・バリア性:蒸着膜は密度が高く、ガスや水分の透過を防ぐバリア膜として機能する。食品包装や医療用パッケージ、半導体の封止材に用いられる。
・導電性・絶縁性の制御:金属蒸着によって配線や電極を形成できる一方で、酸化膜や窒化膜で絶縁層を構成することも可能。電子部品やMEMSデバイスに不可欠な技術。
さらに、蒸着は真空中で行われるため、化学的不純物が混入しにくく、高純度な膜形成が可能です。
これにより、半導体や光学機器などの高度な機能が要求される製品において、性能の安定性や長寿命化が期待できます。
また、複数の材料を交互に蒸着して多層膜を形成することも可能で、特定の波長のみを透過・反射させるような複雑な光学フィルターも製造できます。
ナノレベルの精密設計と、それを実現する成膜技術として、蒸着は極めて優れています。
このように、蒸着処理は「見た目の装飾」や「表面保護」の枠を超えて、電子機能・光学機能・機械的強度などを付加する、高付加価値の技術です。
特に半導体、通信、バイオ、宇宙航空などの先端産業では、蒸着なしには製造が成り立たないほど重要なプロセスとなっています。
コスト・設備面の課題
高機能性が得られる一方で、蒸着処理にはコストと設備面での課題も多く存在します。
これが蒸着を導入するかどうかの判断材料として大きな意味を持ちます。
まず最大の課題は、専用の高価な真空装置が必要だという点です。
蒸着は真空中で行うため、処理装置には高性能な真空ポンプ(ロータリーポンプやターボ分子ポンプなど)や、加熱機構、ガス供給系、排気系、制御ソフトウェアなどが必要になります。
これにより、初期投資額は数百万円〜数千万円にのぼることもあり、中小規模の事業者にとっては大きな負担です。
さらに、以下のような運用面の課題もあります。
・処理時間が長い:真空引き、加熱、成膜、冷却、排気といった工程に時間を要し、サイクルタイムが長くなりやすい。
・大量生産への不向き:連続処理や大面積処理には不向きなことが多く、量産性よりも高付加価値・少量生産に適している。
・基材サイズの制約:チャンバーの大きさによって加工可能な部品サイズが限定されるため、大型製品への適用には限界がある。
・メンテナンスとランニングコスト:真空装置は定期的なメンテナンスが不可欠であり、特に蒸着源や真空ポンプの寿命管理には注意が必要。また、使用する原料(貴金属・セラミック材料等)も高価なものが多く、ランニングコストも無視できません。
加えて、プロセス管理の難しさも課題の一つです。
蒸着処理は膜厚、成膜速度、真空度、温度など多くのパラメータに依存し、製品ごとの最適条件を確立するまでに時間とコストがかかることがあります。
したがって、蒸着技術は設備投資と管理負荷の高い技術であるという側面を持ちつつ、それを上回る価値(高機能性、信頼性、性能)を必要とする場面で活用されるのが一般的です。
価格競争の厳しい量産品には不向きで、付加価値が求められる高機能製品に特化するのが理想的な適用スタイルといえるでしょう。
他の処理法(メッキ・塗装)との比較
蒸着処理は、メッキや塗装といった他の代表的な表面処理法と比べて、特性や用途に明確な違いがあります。
以下に、蒸着とそれらの処理法を比較し、それぞれの長所・短所を整理します。
■ 蒸着 vs メッキ(電気メッキ・無電解メッキ)
比較項目 | 蒸着 | メッキ |
---|---|---|
形成方法 | 真空中で蒸発させた材料を凝縮 | 電解反応(電気)または化学還元反応 |
膜厚 | 数nm〜数μmの極薄膜 | 数μm〜数百μmまで形成可能 |
密着性 | 表面処理次第で剥がれやすいことも | 化学的結合による密着性が強い |
特性 | 高機能性膜(光学・電子・耐熱など) | 耐食性・装飾性が中心 |
対応形状 | 平面・微細構造に強いがシャドーあり | 複雑形状や内面にも均一な被覆が可能 |
コスト | 高額(設備・運用) | 比較的低コストで大量生産向き |
メッキは耐食性・装飾性を目的とした比較的汎用的な処理方法であり、大量生産に適しています。
一方で、蒸着は機能性膜や精密構造への適用に特化した高度な技術です。
■ 蒸着 vs 塗装(液体塗装・粉体塗装)
比較項目 | 蒸着 | 塗装 |
---|---|---|
被膜構造 | 原子・分子レベルの精密な無機薄膜 | 有機樹脂ベースの厚膜 |
耐熱性 | 高温環境にも対応可能 | 樹脂によっては低耐熱 |
精密性 | ナノレベルで膜厚制御可能 | 目視レベルの膜厚制御 |
色彩表現 | 金属光沢・干渉色など限定的 | 幅広いカラー・質感表現が可能 |
量産適性 | 少量高機能製品に向く | 大量生産・低コストに優れる |
塗装はコストが安く、色彩表現や意匠性に富む反面、膜の厚みが不均一になりやすく、耐摩耗性・耐熱性に劣ります。
蒸着は薄くても高機能な膜が得られるため、性能重視の用途に向いています。
■ 総括
蒸着は、メッキや塗装と比べて「機能性」「精密性」「純度」「膜構造制御」において群を抜いていますが、その分「コスト」「設備」「量産性」で不利です。
そのため、コスト重視ならメッキ・塗装、性能重視なら蒸着といった使い分けが実践されています。
用途や予算に応じて、最適な処理法を選択することが重要です。
蒸着のある部品加工の見積り依頼ならアスクへ
試作品や小ロットの加工も大歓迎!
特に手のひらサイズの部品製作を得意としています。
アスクなら、試作品のお見積もりが最短1時間で可能!!
お気軽にお問い合わせください。
試作全国対応!
簡単・最短1時間お見積り
他、ブログ記事もご覧ください♪
動画の投稿もしておりますので良ければご覧ください♪