必見!!溶接の種類や使い分けなど簡単解説!
こんにちわ!本日は溶接について、記事を書いていきたいと思います!
製造業に携わっている方であれば当たり前のことかもしれないですが、お付き合いください♪
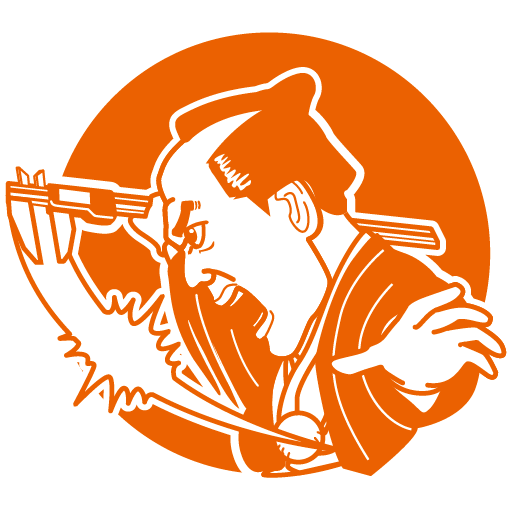
溶接とは

溶接とは、2つ以上の金属や材料を接合する技術の一種です。
単なる接着ではなく、素材同士を高温に加熱して溶かし、融合させることで一体化を図ります。
主に金属に対して使われますが、最近では樹脂やセラミックスなどへの応用も進んでいます。
溶接は、建築、造船、自動車、航空、機械製造など、あらゆる製造業で不可欠な工程です。
接合する対象や求められる強度、耐久性に応じて、様々な溶接方法が選ばれます。
作業には高温・高圧を伴うため、専門知識と高い技術力が求められます。
また、適切な手順を踏まないと、溶接部に欠陥が生じるリスクもあります。
したがって、品質管理と安全対策も非常に重要なポイントです。
溶接が使われる場面
溶接は、私たちの生活のあらゆる場面で重要な役割を担っています。
建築分野では、鉄骨構造のビルや橋梁、トンネルの建設に欠かせません。
自動車や鉄道車両の製造現場では、車体やフレームを構成する金属部材を強固に接合するために使われます。
造船業でも、巨大な船体を構成する鋼板を繋ぎ合わせるために広範囲にわたる溶接作業が行われます。
さらに、航空宇宙産業では、超軽量かつ高強度な接合を実現するために、レーザー溶接や電子ビーム溶接といった先端技術が用いられます。
最近では、家庭用製品の製造にも溶接技術が応用され、エアコンや冷蔵庫の内部配管などにも見られます。
このように、溶接は現代社会を支える基盤技術と言えるでしょう。
溶接の種類
アーク溶接
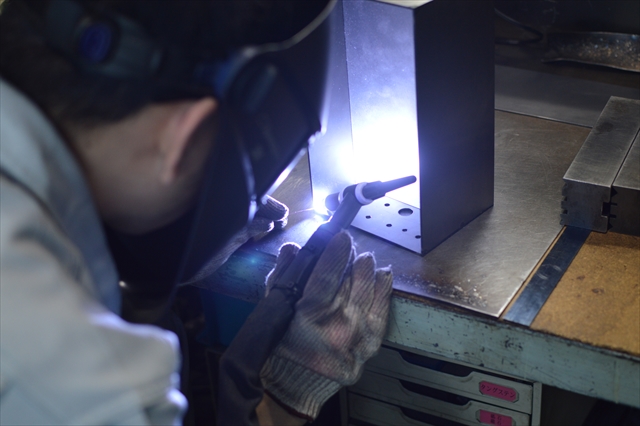
アーク溶接は、最も一般的な溶接方法の一つです。
電気を使って金属間にアーク(電気的な火花)を発生させ、その高熱によって金属を溶かして接合します。
アーク溶接には、手溶接(被覆アーク溶接)、半自動溶接(MAG溶接、MIG溶接)、TIG溶接などの種類があります。
被覆アーク溶接はシンプルな構造と操作性から、建設現場や修理作業で広く使われています。
半自動溶接はワイヤ送給機によって溶接ワイヤが自動供給されるため、作業効率が高く量産品に向いています。
TIG溶接は、高品質な仕上がりが求められる場面で活用され、ステンレス鋼やアルミニウムなどの溶接に強みを持ちます。
アーク溶接は用途や目的に応じた多様なバリエーションが存在するため、幅広い現場で重宝されています。
ガス溶接
ガス溶接は、酸素と可燃性ガス(主にアセチレン)を燃焼させ、その火炎による高温で金属を溶かして接合する方法です。
電源を必要としないため、屋外や電源の確保が難しい場所で活躍します。
特に、薄板の溶接や細かい加工に向いており、自動車板金や美術工芸品の製作にも利用されています。
また、ガス溶接は熱の加減を目視で確認しながら操作できるため、繊細な作業に適しています。
ただし、電気溶接に比べると熱効率が低く、厚板の溶接には向かない点がデメリットです。
さらに、ガスの取り扱いには細心の注意が必要であり、爆発や火災を防ぐための安全対策も重要になります。
近年ではガス切断や加熱作業の方が使用頻度が高くなり、溶接自体は一部の用途に限定されつつあります。
レーザー溶接
レーザー溶接は、高出力のレーザー光を利用して金属を溶かし接合する最先端の溶接技術です。
非常に狭い範囲に高エネルギーを集中できるため、精密で高速な溶接が可能です。
特に、電子部品、自動車部品、医療機器など、精密さとクリーンな仕上がりが求められる分野で活躍しています。
レーザー溶接の特徴は、熱影響が小さく、歪みが非常に少ない点にあります。
また、深い溶け込みを得られるため、強度の高い接合が可能です。
ただし、装置自体が高価であり、初期投資が大きい点が課題となります。
また、金属の反射率や厚みなどによってレーザーの適用条件が変わるため、事前の綿密な設計と検討が必要です。
近年ではファイバーレーザーの普及により、コストダウンと適用範囲の拡大が進んでいます。
抵抗溶接
抵抗溶接は、金属同士を接触させ、そこに大電流を流して接触部分に発生する抵抗熱によって溶接する方法です。
主な種類に、スポット溶接、シーム溶接、プロジェクション溶接などがあります。
特にスポット溶接は、自動車の車体製造において最も一般的に使用されている溶接法で、短時間で大量に接合できるため、生産効率に優れています。
抵抗溶接のメリットは、加熱が局所的であり、作業速度が速く、比較的自動化しやすい点です。
一方で、厚板や異種材料同士の溶接には向いていないという制約もあります。
また、適正な電流や加圧条件を設定しないと、溶接部に欠陥が生じるリスクがあるため、プロセス管理が重要です。
近年では、電動車や軽量化素材の普及に伴い、抵抗溶接技術の改良も進められています。
溶接に使われる材料と機材
溶接材料(金属・溶加材)
溶接に使用される材料は、主に接合する金属の種類と、それに応じた溶加材(溶接棒や溶接ワイヤなど)からなります。
金属の種類としては、鉄鋼、ステンレス鋼、アルミニウム、銅、チタンなどが多く、溶接する際はこれらの金属の融点や熱膨張などの特性に適した溶接方法と材料を選択する必要があります。
例えば、鉄鋼の場合はアーク溶接やガス溶接が一般的に使われますが、ステンレス鋼やアルミニウムではTIG溶接が最も適しています。
溶加材は、溶接金属の補充材として使用され、溶接部に強度を持たせるために重要な役割を果たします。
溶加材の種類としては、溶接棒、ワイヤ、コアワイヤ(内蔵されたフラックスが特徴)などがあり、それぞれに特徴があります。
例えば、被覆アーク溶接で使用される溶接棒は、棒の表面にフラックス(保護剤)が塗布されており、溶接中に発生する酸化物やスパークから溶接部を保護します。
一方で、MIG溶接やMAG溶接で使用される溶接ワイヤは、溶接時に連続的に供給され、効率的な作業が可能となります。
溶加材の選定は、溶接後の強度や耐食性、耐熱性を決定づけるため、金属の組み合わせや溶接条件に基づいて慎重に選ばれるべきです。
溶接材料の品質も、最終的な溶接部の品質に大きな影響を与えるため、信頼性の高い製品を使用することが求められます。
溶接機とその特徴
溶接を行うためには、適切な溶接機を選定する必要があります。
溶接機の種類は、使用する溶接方法によって大きく異なり、それぞれに特徴があります。
例えば、アーク溶接を行うためには、直流アーク溶接機(DC機)や交流アーク溶接機(AC機)が使われます。
直流アーク溶接機は、安定したアークを維持しやすいため、溶接ビードの品質が高く、溶接しやすいのが特徴です。
一方、交流アーク溶接機は、比較的安価であり、重い金属の溶接にも対応できるため、工場で広く使用されています。
また、TIG溶接やMIG溶接には、専用の溶接機が必要です。
TIG溶接機は、精密な溶接が要求されるため、細かな操作ができる機能が搭載されています。
MIG溶接機は、自動化が進んでおり、連続的なワイヤ供給が可能であるため、大量生産にも対応できます。
MIG溶接機は、一般的に手動と自動の両方で使用され、溶接速度が速いという利点があります。
さらに、近年では、インバータ技術を搭載した溶接機が登場し、従来の機械よりも軽量で高効率、さらにエネルギー消費の削減にも寄与しています。
インバータ溶接機は、安定したアークを維持でき、精密な溶接が可能であるため、特に自動車や航空機の製造現場などでも利用されています。
溶接機の選定は、作業の効率性や品質を左右するため、作業環境や求められる溶接条件に最適な機種を選ぶことが重要です。
近年の溶接技術の進化
自動溶接とロボット溶接
近年、溶接技術の進化により、自動化が進んでいます。
特に、ロボット溶接は、製造業において大きな革新をもたらしました。
ロボット溶接は、溶接作業を完全に自動化することができるため、作業の精度や生産性が飛躍的に向上します。
従来の手作業に比べて、高速かつ安定した品質を維持でき、作業者の負担軽減や人為的ミスの削減が実現しました。
ロボット溶接のメリットの一つは、繰り返し作業を安定的に行える点です。
これにより、大量生産が必要な自動車業界や家電製品の製造ラインでは、作業効率が大幅に向上しました。
また、ロボット溶接は、危険を伴う作業環境でも使用することができるため、安全性の向上にも寄与しています。
特に有害ガスや高温環境下での作業をロボットに任せることで、作業者が危険に晒されることを防ぎます。
さらに、自動化溶接機では、溶接パラメータ(電流、電圧、速度など)の最適化がリアルタイムで行われ、より精密な制御が可能になります。
これにより、製品の品質が均一に保たれるとともに、溶接の効率も向上します。
自動化技術の進展は、溶接の精度を向上させるだけでなく、より複雑な形状や難易度の高い作業を効率的にこなすための重要な手段となっています。
新素材対応の溶接技術
新たな材料の開発とその利用の拡大に伴い、溶接技術も進化しています。
特に、軽量化や強度向上を求められる現代の製造業では、従来の金属に加えて、新素材への対応が求められています。
例えば、アルミニウムやチタンといった軽量金属は、航空宇宙や自動車業界で頻繁に使用されており、これらの溶接には専用の技術が必要です。
アルミニウムは、溶接時に酸化皮膜が強く形成されやすく、従来の溶接方法では適切な接合が難しい場合があります。
そこで、TIG溶接やレーザー溶接が活躍しています。
TIG溶接は、精密な温度管理が可能で、アルミニウムのような高融点の金属に対して安定した溶接ができます。
また、レーザー溶接は、熱影響を最小限に抑えることができるため、薄いアルミニウム板を扱う際に有効です。
さらに、チタン合金は非常に高い強度と耐腐食性を持つため、航空機や医療機器に使用されています。
チタンは高温で酸化しやすく、そのため特殊なアーガス雰囲気下での溶接が必要です。
この点を解決するために、ガスシールド溶接技術や、進化したTIG溶接が使用され、より高い品質での溶接が実現されています。
また、炭素繊維強化プラスチック(CFRP)やセラミックなどの新素材に対しては、溶接ではなく、接着や接合技術が多く用いられますが、これらの新素材を溶接するための特殊技術も研究されており、今後の技術進化に期待がかかります。
新素材に対応した溶接技術は、産業の多様化に伴い、今後ますます重要になっていくことでしょう。
これにより、溶接業界は、より精密で強靭な製品の製造を支える役割を果たしていきます。
溶接のある部品の見積り依頼ならアスクへ
試作品や小ロットの加工も大歓迎!
特に手のひらサイズの部品製作を得意としています。
アスクなら、試作品のお見積もりが最短1時間で可能!!
お気軽にお問い合わせください。
試作全国対応!
簡単・最短1時間お見積り
ブログ記事も投稿しておりますので是非ご覧ください♪
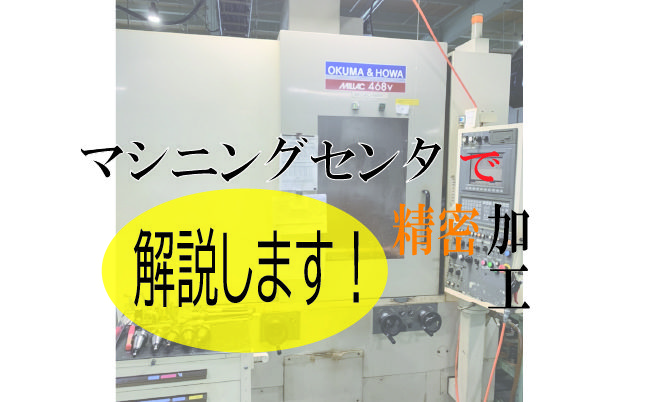
他の動画ご覧ください♪