板金加工とは?基礎から工程・技術まで徹底解説
板金加工は、金属の薄板を切断・穴あけ・曲げ・溶接・組立などの技術を駆使して、立体的な製品や部品を作り上げる重要な製造プロセスです。
自動車、家電、建築、産業機械、医療機器など、さまざまな分野で幅広く活用されています。
その最大の特徴は、1枚の板材から多様な形状を創出できる点にあります。
試作から量産まで対応可能で、特に多品種少量生産に強みを持っています。
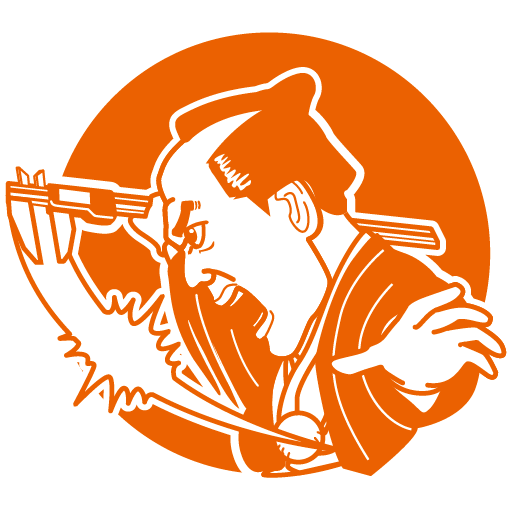
板金加工とは
板金加工とは、金属の薄板を切断・穴あけ・曲げ・溶接・組立などを行い、立体的な製品や部品を製作する加工技術の総称です。
一般的には6mm以下の金属板を対象とし、自動車、家電、建築、産業機械、医療機器など、さまざまな分野で利用されています。
板金加工の最大の特徴は、1枚の板材から多様な形状を創出できる点にあります。
そのため、試作から量産まで幅広いニーズに対応でき、特に多品種少量生産に強みがあります。
主要な使用材料とその特徴
板金加工で使用される金属材料には、それぞれ異なる特性があり、用途に応じて最適な材料選定が重要です。
以下に代表的な板金材料とその特徴を紹介します。
【SPCC(冷間圧延鋼板)】
SPCCは一般的な鉄鋼板で、加工性が良く、価格も安価なため、多くの工業製品で使用されています。
表面は比較的滑らかで、プレス加工や曲げ加工に適しています。
防錆のために表面処理(メッキや塗装)を施して使用されることが多いです。
【SECC(電気亜鉛メッキ鋼板)】
SECCはSPCCの表面に電気亜鉛メッキを施した材料で、防錆性に優れています。
筐体や配電盤など、見た目や耐久性が求められる場面で多く使われます。
【SUS304(オーステナイト系ステンレス鋼)】
SUS304は耐食性、加工性、溶接性に優れたステンレス鋼で、最も一般的なステンレス材料です。
食品加工機械、医療機器、建築部材など幅広い用途があります。
硬くてばね戻りが大きいため、曲げ加工には熟練のノウハウが求められます。
【A5052(アルミニウム合金)】
A5052は軽量かつ耐食性に優れたアルミ合金で、特に輸送機器や電子機器の筐体などに使用されます。
導電性や熱伝導性も高く、冷却部品などにも向いています。
ただし、溶接や表面処理には注意が必要で、仕上がりを美しく保つには適切な加工条件の設定が欠かせません。
【銅・真鍮】
銅や真鍮は導電性や装飾性が高く、電気部品やデザイン部材などに使われます。
柔らかいため加工しやすいですが、酸化しやすいため表面保護が求められます。
以上のように、板金加工では目的やコスト、仕上がりの美観などを総合的に判断し、最適な材料を選定することが製品品質を左右する重要なポイントです。
板金加工の主な工程
切断加工(レーザー・タレパン)
板金加工における最初の工程として、金属板を所定の形状に切断する「切断加工」があります。
使用される主な機械にはレーザー加工機とタレットパンチプレス(通称タレパン)があります。
レーザー加工は高出力のレーザー光線で金属を瞬時に溶融・蒸発させて切断する方法で、非接触で高精度な加工が可能です。
ファイバーレーザーやCO2レーザーが主流で、特にファイバーレーザーはステンレスやアルミニウムなどの反射率が高い材料にも強く、加工速度が速いという特長があります。
一方、タレパンは金型を使って穴あけや打ち抜き加工を行う機械で、一定の形状を繰り返し加工するのに適しています。
丸穴、角穴、長穴、スリットなどを高速で打ち抜くことが可能で、加工パターンを組み合わせることで複雑な形状も実現できます。
また、タレパンではバーリングやタップ加工も同時に行えるため、工程の集約化が図れます。
切断後の加工面には「バリ」と呼ばれる微細な突起が生じることが多く、これを除去する「デバリング(バリ取り)」工程も重要です。
バリを放置すると、後工程でのトラブルや製品の品質低下につながるため、グラインダーやバレル研磨機を使って丁寧に仕上げる必要があります。
また、近年では切断と同時にバリを最小限に抑えるレーザー機も登場しており、加工精度と効率の向上が進んでいます。
切断工程は板金加工の精度と品質を決定づける重要なプロセスです。
そのため、使用する設備の性能や材料特性を的確に把握し、最適な加工条件を選定することが求められます。
曲げ加工(ベンディング)
切断された板材に立体的な形状を与えるのが「曲げ加工(ベンディング)」です。
専用のベンダー機(プレスブレーキ)を使用して、金型(パンチとダイ)の間に金属板を挟み、圧力をかけて所定の角度に曲げます。
曲げ加工は、製品の構造や強度に直接関わるため、非常に重要かつ繊細な工程といえます。
曲げには「V曲げ」「Z曲げ」「R曲げ」などの種類があり、形状や使用用途に応じて適切な加工方法を選びます。
ベンディングの際には「ばね戻り」と呼ばれる材料の弾性変形によって、狙った角度より戻ってしまう現象が発生します。
そのため、ばね戻りを考慮した角度で曲げることが必要で、これは素材や板厚によって異なるため、経験や試作による補正が必要です。
また、複数の曲げを連続して行う「順曲げ」や、複雑な形状を段階的に形成する「多段曲げ」などもあり、製品図面に基づいた加工順序の最適化が求められます。
最近ではNCベンダーの普及により、曲げ角度や位置を自動制御することで、作業者の技量に左右されずに高精度な曲げ加工が可能となっています。
曲げ工程では材料の特性や曲げ形状、金型の選定など多くの要素が複雑に絡み合います。
そのため、事前のシミュレーションや試作を通じて問題点を洗い出し、量産時には安定した品質を確保することが重要です。
板金加工に使われる機械・設備
レーザー加工機
レーザー加工機は、高エネルギーのレーザー光を金属板に照射して切断・穴あけ・彫刻などを行う装置です。
CO2レーザーやファイバーレーザーなどの種類があり、用途や加工対象によって使い分けられます。
特にファイバーレーザーは薄板の高速切断に適しており、近年主流となりつつあります。
レーザー加工の最大の特徴は、非接触で加工できるため、刃の摩耗がなく常に高精度な加工が可能な点です。
極めて細いビーム径での加工ができ、複雑で繊細な形状も美しく仕上げられます。
また、切断面が滑らかでバリが少ないため、後処理の工数削減にも貢献します。
CADデータとの連携により、柔軟なデザイン変更にも対応でき、少量多品種の生産にも適しています。
NCベンダー
NCベンダーは、金属板を所定の角度に曲げるための装置で、数値制御(NC)によって精密な曲げ加工を自動で行うことができます。
主に曲げ型と押し型を用いて、板材を一定の力で押し込むことで成形し、複数の曲げ角度や形状を一度のプログラムで実現できるのが特徴です。
NCベンダーのメリットは、高精度かつ安定した曲げ品質に加え、作業者の熟練度に依存しない再現性の高さです。
複雑な曲げ形状にも対応でき、製品設計の自由度を大きく広げます。
さらに、CADデータと連携した自動制御により、段取りや試し加工の時間を短縮し、生産効率を向上させることが可能です。
タレットパンチプレス
タレットパンチプレスは、金属板に穴を開けたり、切り抜きを行う加工機で、多くの金型(パンチとダイ)をタレットと呼ばれる円盤に取り付け、回転させて目的の形状を素早く加工できます。
様々な形状の金型を瞬時に切り替えながら加工できるため、多品種少量生産や複雑なデザインへの対応に優れています。
主にアルミや鉄などの薄板に対して使用され、四角穴や丸穴、スリットなどを高速で連続して加工可能です。
加えて、タレパンは簡易的な成形加工や刻印にも対応できるため、工程の一部を一台でまかなえる点がメリットです。
CADデータをもとに自動制御で加工を行えるため、高精度で再現性の高い加工が実現できます。
スポット溶接機
スポット溶接機は、金属板同士を接合するための代表的な溶接装置で、特に自動車や家電製品の製造において多用されています。
2枚の金属板を重ね合わせ、電極で挟んで強力な電流を一瞬流すことで接点にジュール熱を発生させ、局所的に金属を溶かして接合します。
この溶接方法は非常に短時間で接合が完了するため、生産効率が高く、大量生産に適しています。
さらに、追加の溶接材料が不要で、接合部分の歪みも少ないという特徴があります。
機械の操作も比較的簡単で、オートメーション化にも対応しやすく、安定した品質で接合が行える点も魅力です。
スポット溶接機は、シンプルながらも効率的で、板金加工の中でも基本的かつ重要な機械の一つです。
ファイバーレーザー溶接機
ファイバーレーザー溶接機は、高出力のレーザー光を用いて金属を溶融・接合する装置で、板金加工における高精度な溶接を実現します。
レーザー光は光ファイバーを通じて照射され、接合部に集中したエネルギーを与えることで、極小の範囲を効率的に加熱・溶接します。
これにより、歪みの少ない美しい仕上がりを得られるため、外観品質が重要な製品や精密機器の製造に最適です。
ファイバーレーザーは非接触加工のため、電極やトーチの摩耗がなく、メンテナンスが少ないのもメリットです。
また、異種金属の接合や微細なスポット溶接にも対応可能で、アルミや銅といった難加工材にも有効です。省エネ性に優れ、長寿命で安定した性能を持つことから、次世代の板金加工現場における主要設備として注目されています。
板金加工における設計と図面
設計図面の役割と注意点
板金加工において、設計図面は現場との橋渡しを担う極めて重要な情報源です。
設計者が意図した形状、寸法、公差、材料の指定、加工順序など、すべての情報が図面に盛り込まれているため、図面の精度は製品の品質に直結します。
たとえば、曲げや穴あけの位置に曖昧さがあると、現場での解釈にバラつきが生じ、加工ミスや再加工の原因となります。
図面には、三面図、展開図、断面図、詳細図などが含まれ、複雑な製品であればあるほど、これらを適切に使い分けることが求められます。
また、曲げ指示には曲げ角度や内Rを明記し、素材の厚みによって異なる曲げ補正量(ベンドアロワンス)を考慮した寸法設計が不可欠です。
さらに、図面には製品の使用環境や組立方法も考慮されるべきです。
たとえば、屋外で使用される製品であれば、腐食対策としての表面処理指示(塗装、メッキなど)を忘れてはなりません。
設計図面の明確さと精度は、スムーズな製造プロセス、コスト削減、品質安定に大きくかかわるため、単なる指示書ではなく、製造の羅針盤としての役割を果たすのです。
板金設計の基本ルール
板金加工における設計は、製品の品質や生産効率に直結する非常に重要な工程です。
板金設計の基本的なルールには、曲げR(半径)の最小値を確保すること、穴や切り欠きの配置に十分な間隔をとること、曲げ方向と繊維方向の関係を考慮することなどがあります。
これらは板材の破損や変形を防ぎ、加工精度の向上や加工コストの削減に大きく関係します。
設計段階では、使用する材料の特性や板厚、加工方法などを踏まえたうえで、製品の形状を最適化する必要があります。
特に、曲げ工程では「スプリングバック」と呼ばれる現象(曲げた後に若干戻る)を考慮して角度を設定することが求められます。
また、加工工程を簡略化するための設計(DFM:Design for Manufacturability)も重視され、例えば溶接の必要性を減らすための一体成形設計などが取り入れられます。
CADによる3D設計の導入が進んでおり、設計段階で干渉チェックや組み立てシミュレーションを行うことが可能になりました。
これにより、試作回数を減らしながらも高品質な製品設計が実現可能です。
正確な板金設計と図面は、現場の加工精度や生産スピードに直結するため、非常に重要な役割を担っています。
板金加工の最新技術と今後の展望
次世代素材と加工技術の進化
近年、板金加工に用いられる材料の種類は大きく広がりつつあり、軽量かつ高強度な次世代素材の登場が注目を集めています。
特に、自動車や航空機、医療分野では、従来の鉄やアルミに加え、マグネシウム合金やチタン合金、CFRP(炭素繊維強化プラスチック)などの使用が増加しています。
これらの素材は軽量化と強度向上の両立を実現できる一方で、加工性に課題があるため、加工技術の進化が不可欠です。
最新のレーザー技術やハイブリッド加工(機械加工と放電加工の融合)などが導入され、これまで困難だった複雑形状の加工や難削材の加工が実現可能となっています。
また、超高出力ファイバーレーザーや自動調整可能なツールを搭載したNC機器により、より一層の高精度・高速化が進んでいます。
加えて、リサイクル性の高い材料や、環境負荷の少ない表面処理技術の導入も、持続可能な製造を支える重要な要素として位置付けられています。
このように、材料と加工技術の進化は表裏一体であり、新素材に対応する技術の開発が、板金加工の競争力強化に直結しています。今後も、環境対応や多様化するニーズに応えるためのイノベーションが求められるでしょう。
スマートファクトリーと自動化の進展
近年、板金加工の分野でもスマートファクトリー化の波が広がっており、IoTやAI、ロボット技術を活用した自動化が加速しています。
これにより、加工精度の向上、生産効率の大幅な改善、そして人手不足の解消が期待されています。
具体的には、NC機械やレーザー加工機の自動搬送、ロボットアームによる部品の自動脱着、自動検査装置の導入などが挙げられます。
さらに、これらの機器はネットワークで接続され、リアルタイムで生産状況や不良情報を監視・解析できるようになっています。
これにより、トラブルの早期発見や予知保全が可能となり、ダウンタイムの削減や品質向上に直結します。
加えて、クラウド型の製造管理システムと連携させることで、工程全体の最適化が図られています。
将来的には、AIによる最適加工条件の自動提案や、ビッグデータ解析による生産スケジューリングの最適化なども期待されています。
板金加工業界においてもDX(デジタルトランスフォーメーション)は不可避の流れとなっており、いかに早く対応し、独自の強みと融合させるかが今後の競争力を左右する鍵となるでしょう。
板金加工の見積り依頼ならアスクへ
試作品や小ロットの加工も大歓迎!
特に手のひらサイズの部品製作を得意としています。
アスクなら、試作品のお見積もりが最短1時間で可能!!
お気軽にお問い合わせください。
試作全国対応!
簡単・最短1時間お見積り
所有設備:レーザー加工機、ブレーキプレス、ハイドロリック・ユニバーサル・プレス、メカ式シャーリング
対応可能サイズ:□3mm~□500mm t0.01mm~t6mm
対応数量:単品から小ロットが得意です。
対応材質:鉄(SPCC・SECC)・ステンレス・アルミ系・銅系などお任せください。※詳しくはお問い合わせください
他、ブログ記事もご覧ください♪
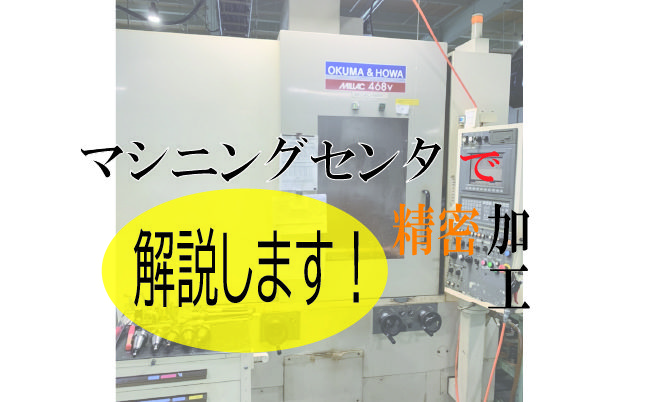
動画の投稿もしておりますので良ければご覧ください♪