旋盤加工の基礎知識:製造業における重要な役割とは?
旋盤加工は、金属や樹脂などの素材を回転させながら切削工具で削ることで、円筒形や円錐形、ねじ山などの精密な形状を作り出す加工方法です。
この技術は、機械部品や自動車部品、医療機器など、さまざまな製品の製造に欠かせない要素となっています。
旋盤加工の特徴は、その高い精度と多様な形状の加工が可能な点にあります。
また、近年ではCNC(コンピュータ数値制御)旋盤の導入により、より複雑な形状の加工や高効率な生産が実現されています。
本記事では、旋盤加工の基本的な仕組みから、使用される工具や加工方法、さらには最新の技術動向に至るまで、幅広く解説していきます。
製造業に従事する方々や、旋盤加工に興味のある方々にとって、実践的かつ有益な情報を提供することを目指しています。
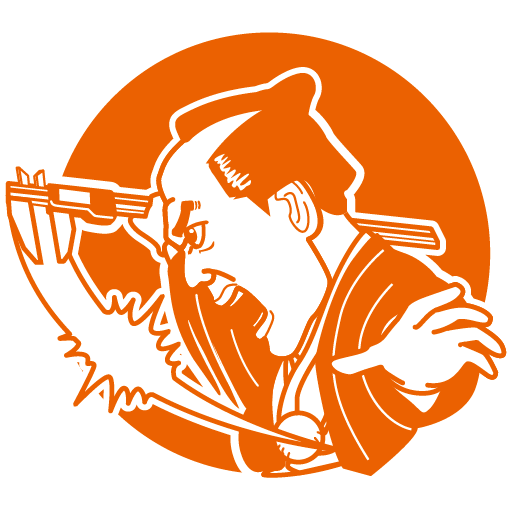
旋盤加工とは
旋盤加工とは、工作物(ワーク)を回転させ、固定した刃物(バイト)で削る加工方法を指します。
工作機械の中でも最も基本的な加工法の一つであり、金属、プラスチック、木材など幅広い素材に対応可能です。
円筒形や円錐形といった回転対称形状の部品を高精度で製作できる点が大きな特徴です。
旋盤加工は、古くは手動の機械で行われていましたが、現在ではNC旋盤(数値制御旋盤)やCNC旋盤が主流となっており、複雑な形状や微細な加工も自動制御で行えるようになっています。
これにより、量産性や再現性が飛躍的に向上し、自動車部品、航空機部品、医療機器など精密性を要求される分野で活躍しています。
また、旋盤加工では「外径削り」「内径加工」「ネジ切り」「端面加工」など、さまざまな加工が可能であり、一台の機械で多彩な加工を行える点も魅力です。
加工前の素材は丸棒やパイプ状のものが主で、素材の選定も重要な要素となります。
精密加工の基礎としても位置づけられる旋盤加工は、製造業の根幹を支える存在であり、初学者が最初に学ぶ機械加工でもあります。
そのため、加工理論や操作方法の理解は非常に重要であり、技能検定などを通して知識と技術の習得が奨励されています。
旋盤の種類と用途
汎用旋盤とNC旋盤の違い
旋盤にはいくつかの種類がありますが、代表的なのが「汎用旋盤」と「NC旋盤」です。
汎用旋盤は、作業者が手動で操作する昔ながらのタイプで、操作レバーやダイヤルを用いて加工を進めます。
一方のNC旋盤(Numerical Control Lathe)は、コンピュータによって動作が制御される旋盤で、あらかじめ入力されたプログラムに従って自動的に加工を行います。
汎用旋盤のメリットは、細かな微調整が手動でできることや、少量多品種の加工に向いている点です。
試作や修理など、柔軟性が求められる作業に適しています。
ただし、作業の品質はオペレーターの腕に依存するため、熟練した技術が必要になります。
一方、NC旋盤は大量生産に強く、寸法精度や再現性が高いのが特徴です。
プログラムを保存すれば、同じ加工を何度でも高精度に繰り返すことが可能です。
また、人為的なミスが減り、作業効率も大幅に向上します。
複雑な形状の加工にも対応しやすく、現在では製造業の多くがNC旋盤を導入しています。
ただし、NC旋盤にはプログラミングの知識が必要であり、初期の設定には時間がかかる場合があります。
そのため、作業内容や生産規模に応じて、汎用旋盤とNC旋盤を使い分けることが重要です。
CNC旋盤の特徴とメリット
CNC旋盤(Computerized Numerical Control Lathe)は、NC旋盤の進化形で、より高度な制御を可能にした旋盤です。
コンピュータ制御によって多軸制御や複合加工を行える点が大きな魅力で、現在では先進的な製造業を中心に広く使用されています。
CNC旋盤の最大のメリットは、自動化と高精度の両立にあります。
工具の交換や補正も自動で行え、連続運転による大量生産が可能になります。
これにより、人件費の削減や生産効率の向上が期待でき、24時間稼働による無人運転も実現できます。
また、CNC旋盤は複雑な形状を精密に加工する能力に長けています。
たとえば、外径・内径の同時加工や、斜めの切削など、従来の旋盤では難しかった作業も可能になります。
CAD/CAMとの連携により、図面から直接加工プログラムを生成することも可能で、開発スピードが格段にアップします。
一方で、CNC旋盤の導入には高額な設備投資が必要です。
また、操作には専門的な知識と技能が求められるため、教育や訓練も重要です。
それでも、高い品質と効率を両立できる点から、航空・自動車・医療分野などでは欠かせない存在となっています。
用途に応じた旋盤の選び方
旋盤を選ぶ際には、用途や生産規模、求められる精度などをしっかり見極めることが重要です。
たとえば、少量の試作やメンテナンスを主に行う場合は、汎用旋盤の方がコストパフォーマンスが高く、柔軟性にも優れています。
操作が視覚的でわかりやすいため、教育用途としても向いています。
一方、同じ製品を大量に、かつ高精度で加工する必要がある場合は、NC旋盤やCNC旋盤が圧倒的に有利です。
寸法精度や加工時間のばらつきが少なく、品質管理もしやすいため、量産ラインでは標準装備となっています。
さらに、複合加工を伴う部品や多様な素材を扱う場合は、CNC旋盤のようなマルチ機能機が適しています。
ミーリング(フライス加工)や穴あけなど、旋盤以外の工程も一体化できる「複合旋盤」も存在し、加工工程を大幅に短縮することができます。
コスト面や保守体制、作業者のスキルレベルも考慮しながら、必要な機能や性能を備えた旋盤を選定することが、生産性や品質向上への第一歩となります。
主な加工方法
外径・内径加工
旋盤加工の基本中の基本といえるのが「外径加工」と「内径加工」です。
外径加工は、ワーク(素材)の外周を削って所定の直径に仕上げる加工で、最も一般的な旋盤の用途です。
たとえば、シャフトやピンといった棒状部品の表面を滑らかにしたり、特定のサイズに成形したりする際に用いられます。
内径加工は、素材に穴を開けたり、すでに空いている穴を広げたりする加工です。
ドリルで下穴を開けた後にバイトで仕上げることで、滑らかで寸法精度の高い穴を作ることができます。
これは、ベアリングやスリーブ、ブッシュなど内径を持つ部品の製作に不可欠です。
これらの加工では、「切削条件」の設定が非常に重要です。
回転数、送り速度、切込み量といったパラメータを適切に設定することで、加工精度や表面粗さが大きく変わってきます。
また、使用するバイトの種類や形状も、加工対象の材質や形状に応じて選定する必要があります。
さらに、内径加工は外径に比べて工具の剛性や排屑(はいせつ:削りカスの排出)が難しいため、加工条件の調整や冷却液の使用など、より繊細な配慮が求められます。
端面加工・突っ切り加工
端面加工とは、ワークの断面(端面)をバイトで削る加工で、ワークの長さを整える目的で行います。
これにより、部品の両端が平らになり、正確な寸法を確保できます。
また、端面の平面度や垂直度は、部品の組み立て精度にも影響するため非常に重要です。
端面加工では、バイトの先端がワークの中心に向かって進むため、中心付近では切削速度がゼロに近づきます。
このため、中心部分の仕上がりが荒くなりやすく、切削条件や工具の先端形状を工夫する必要があります。
また、回転数を上げすぎると摩耗が早く進みやすいため、適切な回転数の設定が重要です。
一方、突っ切り加工は、ワークを旋盤で切断するための加工です。
細い突っ切りバイトを使用し、ワークの外径から中心方向へ進めていきます。
完成した部品を素材から分離させる重要な工程であり、寸法精度だけでなく、切断面の品質にも配慮する必要があります。
突っ切り加工はバイトに大きな負荷がかかるため、工具の摩耗や破損が発生しやすい工程でもあります。
また、突っ切った瞬間に部品が飛んだり落下したりする危険もあるため、安全対策としてチャックにストッパーを設けたり、部品を保持する工夫も必要です。
ネジ切り・テーパ加工
ネジ切り加工は、回転するワークに対してバイトを送りながら切り込み、ネジ山を形成する工程です。
外ネジと内ネジの両方に対応可能で、精密なネジ山の加工には旋盤が最適とされています。
特に、特殊ピッチや非標準ネジを必要とする部品には、旋盤加工によるネジ切りが欠かせません。
ネジ切り加工では、送り速度と回転速度が同期する必要があります。
このため、機械側で「リードスクリュー」と呼ばれる送りネジと主軸の回転が連動する構造になっています。
NC旋盤では、この同期制御が数値的に行われるため、非常に高精度なネジ加工が可能です。
また、バイトの形状もネジ山の角度に合わせて選定する必要があり、細かいセッティングが要求される工程です。
ネジ切り中のバイトの折損を防ぐため、段階的に切り込みを入れたり、切削油を十分に使うなどの工夫も重要です。
一方、テーパ加工とは、円錐状の形状にワークを削る加工です。
テーパはシャフトの挿入や取り外しをしやすくするために用いられ、工作機械の主軸や工具ホルダーなどでも多く見られます。
汎用旋盤では「コンパウンドスライド」の角度を調整して行い、NC旋盤ではプログラムによって任意の傾斜角度で加工が可能です。
テーパ加工では、角度の微調整が製品のはめ合い精度に大きく関わるため、仕上げには慎重さが求められます。
旋盤加工で使われる工具について
バイトの種類と用途
旋盤加工において最も基本となる工具が「バイト」です。
バイトは素材を削るための刃物であり、その形状や用途に応じて多くの種類があります。
一般的なバイトには、外径加工用、内径加工用、端面加工用、ネジ切り用、突っ切り用などがあり、それぞれの加工目的に最適化された形状をしています。
たとえば、外径バイトは長方形の断面を持ち、工作物の外側を削るのに使われます。
内径バイトは長く細く、ボーリングバーとして内側を削るための設計になっています。
端面バイトは刃先が直角になるように配置されており、ワークの端面を平らに仕上げるのに最適です。
ネジ切りバイトはネジ山の角度に合わせて特殊な形状となっており、細かい精度が求められるため、専用の刃物を使用します。
突っ切りバイトは非常に細く設計されており、部品を素材から切断する際に使われます。
近年では、バイトの先端にチップを装着する「チップ交換式バイト」が主流です。
これにより、刃先が摩耗してもチップを交換するだけで済み、作業の効率化とコスト削減が可能になります。
素材や加工条件に応じて、適切なバイトを選ぶことが高精度加工の鍵を握っています。
刃物交換と工具管理の重要性
旋盤加工では、バイトの摩耗や欠けを避けるために定期的な刃物交換が欠かせません。
工具の状態が加工品質に直結するため、日常的な点検と交換タイミングの管理は非常に重要です。
摩耗した刃物を使い続けると、寸法誤差や表面粗さの悪化、振動の発生などが起こりやすくなります。
工具の寿命は、素材の硬度や切削条件、冷却液の使用状況などに大きく左右されます。
そのため、作業前に工具のチェックリストを設けたり、工具寿命の記録を残すことで、予防的な交換が可能になります。
NC旋盤やCNC旋盤では、工具番号を管理して自動で切り替える機能もあり、これにより生産効率と安定性が向上します。
また、工具を管理するには「ツールプリセッター」や「工具管理ソフト」の活用も有効です。
これにより、バイトの取り付け位置や寸法の補正値を正確に記録・再現することができます。
特に複数の作業者が旋盤を使用する場合、工具管理を標準化しておくことは品質のばらつきを防ぐうえで非常に重要です。
刃物の取り付け時には、しっかりと固定されているか、チップに異常がないかも確認する必要があります。
小さな異常が大きな加工ミスにつながることもあるため、日々の点検と丁寧な工具管理は信頼性の高い加工を支える基盤です。
超硬工具とハイス工具の違い
旋盤加工で使われる刃物素材には、主に「超硬合金(超硬)」と「ハイス(高速度鋼)」の2種類があります。
それぞれに長所と短所があり、加工内容や目的に応じて使い分けることが求められます。
超硬工具は、タングステンカーバイドなどの硬くて熱に強い素材からできており、高速切削に適しています。
耐摩耗性に優れており、硬い素材でも長時間安定した加工が可能です。
そのため、量産ラインなどでは超硬工具が多く使われています。
また、チップ交換式のバイトでは、ほとんどが超硬チップを採用しています。
一方、ハイス工具は鋼にモリブデンやコバルトを加えたもので、やや柔らかく靭性(粘り強さ)に優れています。
そのため、欠けにくく、荒加工や断続切削といった過酷な条件でも安定した性能を発揮します。
また、再研磨が可能な点も特徴で、適切に使えばコストパフォーマンスに優れています。
ただし、ハイスは超硬に比べて摩耗しやすく、加工速度もやや制限されるため、精密加工や高効率が求められる場面では超硬に軍配が上がることが多いです。
逆に、小ロットや複雑な加工ではハイスの扱いやすさが有利に働くこともあります。
このように、両者の特性を理解して適材適所で使い分けることが、コストと品質のバランスを最適化するカギとなります。
品質管理とトラブル対策
寸法精度の確保と検査方法
旋盤加工において、寸法精度の確保は非常に重要なポイントです。
ほんのわずかな誤差が、製品の機能や組み立て精度に大きな影響を及ぼすため、加工後の検査は欠かせません。
特に、回転部品や摺動部品などでは、ミクロン単位での精度管理が求められることも珍しくありません。
まず、寸法を測定する基本的な方法には、ノギス、マイクロメーター、ダイヤルゲージなどがあります。
ノギスは一般的な長さや外径・内径の測定に使われ、扱いやすさが特徴です。
より高精度が求められる場合は、マイクロメーターで千分の一ミリ単位の測定を行います。
また、真円度や振れなどの幾何公差の確認には、ダイヤルゲージや投影機を用いることもあります。
さらに、工場によっては三次元測定機を導入しているところもあり、これにより複雑な形状や寸法を一度に高精度で測定することが可能です。
検査結果は記録として残し、製品のトレーサビリティ(追跡可能性)を担保する役割も果たします。
これらの検査をルーティン化することで、寸法精度の安定化が図れると同時に、不良品の早期発見や工程改善にもつながります。
検査は「加工後」だけでなく、「加工中」や「加工前」にも行い、全体の品質管理体制を確立することが理想です。
加工不良の原因と対策
旋盤加工では、時として思わぬ不良やトラブルが発生することがあります。
不良にはいくつかのパターンがあり、それぞれ原因と対策を理解しておくことが重要です。
代表的な不良のひとつが「寸法不良」です。
これは、バイトの摩耗や工具の取り付けミス、機械の熱変位などが原因で発生します。
対策としては、定期的な工具の交換、機械のウォームアップ運転、加工後の測定・補正が挙げられます。
「表面粗さの悪化」もよくある問題です。
これは切削条件が不適切だったり、バイトの先端が欠けていたり、振動が発生している場合に起こります。
切削速度や送りの最適化、バイトの研磨、機械の剛性向上によって改善できます。
また、「ビビリ音」や「工具破損」などの異常は、材料の硬さに対して切削条件が合っていないケースや、チャッキング(固定)の不安定さが関係しています。
これらのトラブルは、素材や工具の組み合わせ、工作物の固定方法を見直すことで防げる場合があります。
トラブルを未然に防ぐためには、作業前のチェックリストや加工中の音・振動のモニタリング、定期的な保守点検が効果的です。
現場の「ちょっとした違和感」を見逃さず、日々の観察力を高めることも重要なスキルです。
トレーサビリティと記録管理
品質管理の一環として、近年ますます重要視されているのが「トレーサビリティ(追跡可能性)」の確保です。
製品がどのような工程で、どの材料・機械・工具を使って作られたのか、いつ誰が加工・検査したのかを記録として残すことで、不具合発生時の原因追跡や責任の明確化が可能になります。
たとえば、加工時には「作業指示書」や「加工記録表」に使用工具や切削条件、測定結果などを記載します。
これにより、同じ不具合が再発した場合にも迅速な対応が可能となり、工程の改善にもつながります。
NC旋盤やCNC旋盤では、使用したプログラムのバージョンや変更履歴を記録することで、より高度な管理が行えます。
さらに、測定データをデジタルで保存し、クラウド上で共有することで、他部署や顧客ともリアルタイムに情報をやりとりすることが可能です。
これにより、品質への信頼性が高まり、ビジネス面での競争力も向上します。
特に自動車や航空機、医療機器などの分野では、トレーサビリティの有無が製品採用の可否を左右することもあります。
単なる「モノづくり」から「品質を証明するモノづくり」へと移行する時代において、記録管理は旋盤加工における欠かせない要素となっています。
旋盤加工品の見積り依頼ならアスクへ
試作品や小ロットの加工も大歓迎!
特に手のひらサイズの部品製作を得意としています。
アスクなら、試作品のお見積もりが最短1時間で可能!!
お気軽にお問い合わせください。
所有設備:複合旋盤・CNC旋盤・CNC自動盤・汎用旋盤
対応可能サイズ:Φ3mm~Φ250mm
対応数量:単品から小ロットが得意です。
対応材質:鉄、SUS、アルミ、銅、真ちゅうなどの一般的な金属から、チタン、インコネル、など一部の難削材、樹脂などもお任せください。※詳しくはお問い合わせください
試作全国対応!
簡単・最短1時間お見積り
他、ブログ記事もご覧ください♪
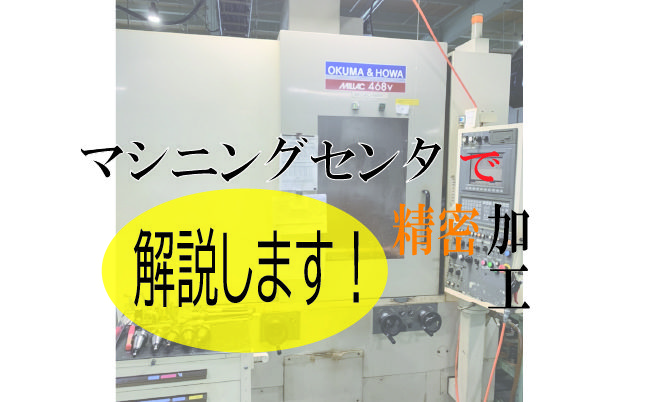
動画の投稿もしておりますので良ければご覧ください♪