半導体とは何か?製造業とのかかわりについて
本日は当社受注の約2割ほどにもなる半導体業界について記事を書いていきたいと思います。
半導体とは?半導体の歴史って?を調べてみると、今後も注目の業界だなと思いました。
それではご覧ください♪
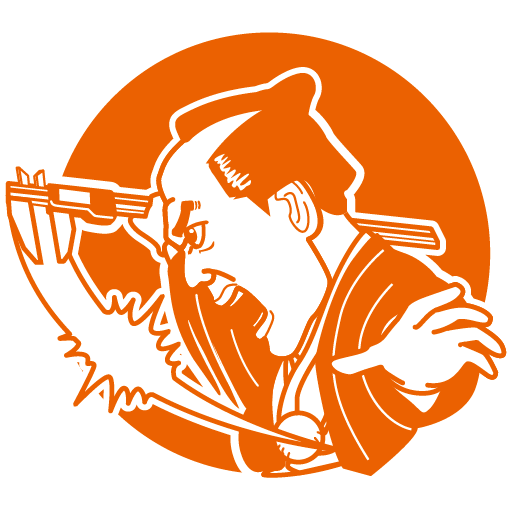
半導体とは
半導体とは、「導体(電気を通す物質)」と「絶縁体(電気を通さない物質)」の中間的な性質を持つ材料のことを指します。
代表的な半導体材料はシリコン(Si)であり、現代のエレクトロニクス産業の中核を担う存在です。
この「中間的な性質」というのは、特定の条件(温度や光、電圧の変化、不純物の添加など)によって、絶縁体のようにも導体のようにも振る舞うという特異な性質を指します。
半導体のこのような性質は、物質のバンド構造によって説明されます。
物質の内部では、電子は「価電子帯」と「伝導帯」という2つのエネルギー帯に分かれて存在します。
絶縁体では、この2つの帯の間に大きなエネルギーギャップ(バンドギャップ)があり、常温では電子が価電子帯から伝導帯に飛び移ることができず、電気が流れません。
一方、導体(たとえば銅など)では、このバンドギャップがほとんどなく、電子が自由に移動できるため、電気がよく流れます。
半導体ではこのギャップが小さく、例えばシリコンでは約1.1eV程度です。
このため、外部からわずかなエネルギー(熱や光)を与えるだけで電子が伝導帯に移動し、電流が流れる状態になります。
さらに、半導体に微量の不純物を加えることで、電子の数を増減させ、電気の流れを制御できるようになります。
この技術を「ドーピング」と呼び、「n型半導体(電子が多い)」や「p型半導体(正孔=電子の欠損が多い)」といった種類を作り分けることが可能です。
こうした制御性の高さが、トランジスタやダイオード、太陽電池などの電子部品に活かされています。
特にトランジスタは、スイッチのように電気をON/OFFできる部品であり、デジタル回路の根幹を成す存在です。
集積回路(IC)やマイクロプロセッサは、数千万から数十億個ものトランジスタを微細なチップ内に集約して構成されています。
また、近年ではガリウム(Ga)やヒ化ガリウム(GaAs)、炭化ケイ素(SiC)、窒化ガリウム(GaN)といった化合物半導体も注目されています。
これらは高耐圧・高周波特性に優れ、次世代通信やパワーエレクトロニクス、宇宙産業などの分野での活用が進められています。
このように、半導体はその独自の性質によって「電気を自在に制御できる素材」として発展を遂げ、現代の電子社会の礎となっています。
半導体の主な用途
半導体は、私たちの生活や社会のインフラに深く根ざした「電子の司令塔」とも言える存在です。
その応用範囲は非常に広く、スマートフォンやパソコンといった身近な電子機器はもちろん、自動車、家電、医療機器、インフラ、産業ロボット、通信設備など、ほぼあらゆる分野で欠かせないものとなっています。
以下、それぞれの用途について具体的に紹介していきます。
スマートフォン・パソコン
スマートフォンやパソコンのような情報端末には、数十億個ものトランジスタを搭載したプロセッサ(CPU、GPU、AIチップなど)が組み込まれています。
これらのチップは、膨大な情報を高速かつ正確に処理するための心臓部であり、演算処理・記憶・表示制御・通信機能などすべてを担っています。
また、記憶装置(メモリ)やフラッシュストレージ、Wi-FiやBluetoothといった無線通信モジュールなど、半導体デバイスの集合体によって構成されています。
自動車(特にEV・自動運転)
近年の自動車は「走る電子機器」とも言われるほど、半導体の依存度が高まっています。
とくに電気自動車(EV)では、バッテリー管理、電力変換(インバータ)、充電制御といった分野で高耐圧・高効率なパワー半導体(SiCやGaNなど)が活躍します。
また、自動運転支援(ADAS)ではセンサーからの膨大な情報をリアルタイムで処理するために、高性能なAI半導体や映像処理チップ(ISP)が不可欠です。
家電・IoT機器
エアコン、冷蔵庫、洗濯機などの白物家電にも、半導体が数多く搭載されています。
センサーで温度や湿度を検知し、モーターやヒーターを効率よく制御するための制御用マイコン(MCU)、電源を制御する電力用ICなどが組み込まれており、省エネ性能や使い勝手の向上を実現しています。
また、スマート家電やIoT機器では、通信モジュール(Wi-Fi/Bluetooth/ZigBeeなど)を介してインターネットと接続するため、さらに多くの半導体が使われています。
産業機械・ロボット・インフラ
製造業の工場や建設現場でも、半導体は重要な役割を果たしています。
たとえば産業用ロボットでは、動作制御やセンサー情報処理、画像認識などの機能が必要で、それを支えるのが半導体デバイスです。
電力インフラでは、変電所や送電網の監視・制御に必要なマイコンや通信IC、電力制御ICが活躍します。
医療機器
MRI、CT、超音波診断装置などの高度な医療機器にも、半導体技術が欠かせません。
画像処理用の高性能プロセッサや、信号の増幅・変換に用いるアナログIC、またセンサーデバイスなどが患者の状態を正確に把握し、診断精度の向上に貢献しています。
最近では、ウェアラブルデバイスや遠隔医療の普及により、超小型・低消費電力な半導体の需要も拡大しています。
通信インフラ(5G/6G)
携帯電話基地局やデータセンターといった通信インフラでは、非常に高速かつ安定した通信を実現するための半導体チップが活躍しています。
特に5G/6Gでは、高周波数帯に対応するため、従来よりも性能の高いRFIC(高周波IC)や高速AD/DAコンバータが不可欠です。
これらの技術革新により、大容量・低遅延・多接続といった通信性能が可能となり、未来のスマート社会を支えています。
このように、半導体の応用分野は非常に広範で、私たちの生活や社会の根幹を支えるインフラと言える存在です。
テクノロジーが進化すればするほど、半導体の重要性もますます高まっていくことでしょう。
半導体の歴史
半導体の技術的進化において、最も重要な転換点となったのが「トランジスタの発明」と「IC(集積回路)の登場」です。
これらの発明は、現代のコンピュータやスマートフォン、インターネットといったテクノロジー社会の基盤を形作りました。
この章では、それぞれの誕生背景と技術的なインパクト、そして社会的な影響について詳しく解説します。
トランジスタの誕生
1947年、アメリカのベル研究所において、ジョン・バーディーン、ウォルター・ブラッテン、ウィリアム・ショックレーの3人によって、世界初のトランジスタが開発されました。
それまでの電子機器には「真空管」が使われており、スイッチや信号増幅などの役割を担っていましたが、大きくて脆く、消費電力も多かったのが難点でした。
これに対してトランジスタは、固体の半導体材料(当初はゲルマニウム)を使って同じ機能を果たすことができ、小型・省電力・高信頼性という点で画期的でした。
さらに製造コストも安く、耐久性もあるため、1950年代からラジオや電話機、軍事機器などに急速に普及していきます。
トランジスタは、簡単に言えば「電流の流れを電圧で制御できるスイッチ・増幅器」です。
基本的な構造は3つの端子(エミッタ、ベース、コレクタ)からなり、ベース電圧の変化によって、エミッタ-コレクタ間の電流を制御します。
最初に開発されたのは「点接触型トランジスタ」ですが、やがて「バイポーラ接合型トランジスタ(BJT)」、そして「MOS型トランジスタ(MOSFET)」へと進化していきました。
MOSFETは現在の集積回路やマイクロプロセッサの中核をなすデバイスで、微細加工や集積性に優れており、現代半導体の主流技術となっています。
IC(集積回路)の登場
トランジスタの次に訪れた技術革新が、1958年にテキサス・インスツルメンツのジャック・キルビーによって開発された「集積回路(IC)」です。
また、ほぼ同時期にフェアチャイルドセミコンダクターのロバート・ノイスも、独自に平面プロセス技術を用いたICを開発しました。
ICは、複数のトランジスタや抵抗、コンデンサなどを1枚の半導体チップ上にまとめて形成することで、部品点数を飛躍的に減らし、小型化・高性能化・高信頼性を実現しました。
これにより、電卓、電子時計、家電、コンピュータなどの電子機器は劇的に進化していきます。
技術の進化とムーアの法則
ICの誕生以降、半導体産業は「より小さく、より速く、より安く」を目指して進化を続けてきました。
1965年、インテル創業者のひとりであるゴードン・ムーアは、「ICに集積されるトランジスタの数は18〜24ヶ月ごとに2倍になる」という予測を立て、これが「ムーアの法則」として知られるようになります。
実際に、1970年代には1チップに数千個だったトランジスタ数は、2020年代には100億個を超える規模に達し、処理能力や電力効率、機能の向上が急速に進みました。
社会へのインパクト
トランジスタとICの登場は、単なる電子技術の進化にとどまらず、産業構造や社会の在り方そのものを変革しました。
大型で高価だったコンピュータが小型化され、企業から家庭へと普及し、インターネットと結びつくことでグローバル社会が形成されました。
また、これらの技術革新は通信、医療、交通、エンターテインメント、教育などあらゆる分野の変革を促しました。
半導体と加工技術
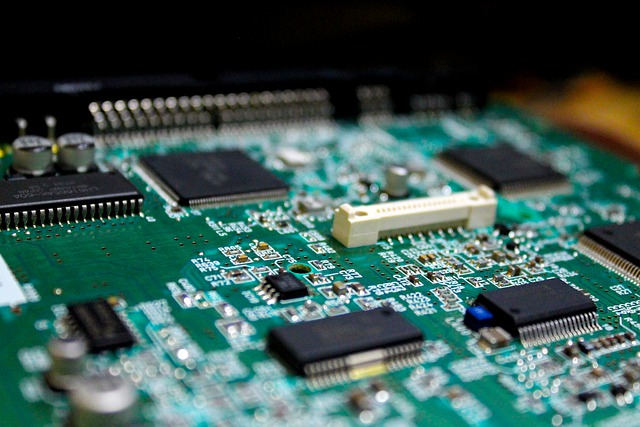
半導体製造工程では、単に回路パターンを描くだけではなく、材料を削ったり、逆に積層していく工程が必要不可欠です。
これを担っているのが、「エッチング(Etching)」と「成膜(Deposition)」という2つの加工技術です。
エッチングは不要な部分を削り取る工程、成膜は必要な材料をウェーハ表面に薄く均一に積層する工程です。
どちらもナノレベルの精度が要求され、半導体の機能や信頼性を左右します。
1.エッチングとは
エッチングは、レジストで保護されていない領域の材料を除去する工程です。
これは、フォトリソグラフィで描かれたパターンを、実際の材料構造に変えるために不可欠な加工です。
■ ウェットエッチングとドライエッチング
・ウェットエッチング
液体薬品を使って材料を溶かす方法。
例:フッ酸を使って酸化膜を除去
特徴:安価で簡便だが、選択性・微細化には限界がある。
・ドライエッチング
プラズマやイオンを使って、気相で材料を反応・除去する方法。
特徴:微細加工に適しており、現在の主流。エッチング形状の制御性が高い。
■ 異方性エッチングと等方性エッチング
・異方性エッチング:垂直方向に強くエッチング(深く・まっすぐ削れる)
・等方性エッチング:全方向に同じ速度で削れる(丸みを帯びる)
微細な垂直構造を形成するには、異方性エッチングが不可欠です。
最先端では反応性イオンエッチング(RIE)などが用いられます。
2.成膜とは
成膜は、材料の薄膜をウェーハ上に均一に堆積させる工程です。
これにより、配線層、絶縁層、ゲート酸化膜などが形成されます。
■ 主な成膜方法
・CVD(化学気相成長法)
ガスを基板上で化学反応させて膜を作る
熱CVD、プラズマCVD、LPCVDなどがある
高速かつ高密度な膜形成が可能
・PVD(物理気相成長法)
金属を蒸発・スパッタして物理的に堆積
スパッタリングが代表的
薄膜形成の均一性が高い
・ALD(原子層堆積)
材料を原子層単位で一層ずつ積み重ねる
極薄で均一な膜が必要な用途に最適(ゲート絶縁膜など)
■ 成膜に求められる性能
・膜厚の均一性:ウェーハ全体で同じ厚さになる必要がある
・密着性:基板にしっかりと張り付いていること
・ピンホールの少なさ:膜に微小な穴がないこと
3.エッチングと成膜の関係
これらは単独では機能しません。
「成膜 → リソグラフィ → エッチング → 成膜…」というように、何層にもわたって繰り返し使用されます。
例:メタル配線層の形成
絶縁膜をCVDで成膜
フォトリソで配線パターンを描く
RIEで絶縁膜をエッチング
金属をスパッタリングで成膜
CMP(化学機械研磨)で表面を平坦化
このように、エッチングと成膜はペアで活躍する「縁の下の力持ち」といえる存在です。
4.微細化にともなう技術進化
微細化が進むほど、成膜やエッチングにも高い精度が求められます。
・成膜ではナノメートル単位の膜厚制御が重要に
・エッチングでは選択性と形状制御の両立が課題に
・材料面でも、従来のSiO₂やAlに代わる新材料が次々と導入(例:ハフニウム酸化物、銅など)
特に3D構造(FinFET、GAAFETなど)が増える現在では、複雑な立体構造に対する均一な成膜・エッチングがカギとなっています。
エッチングと成膜は、半導体製造の中で材料そのものを形作る「彫刻と積層」の技術です。
微細なパターンを正確に削り、必要な材料を均一に積み重ねることが、チップ性能や信頼性の土台を築いています。
これらの工程は表には見えにくいものの、まさにナノスケールの「工芸品」を生み出す技術であり、最先端の科学と職人技が融合したものと言えるでしょう。
半導体と製造現場の関係性
現代の製造業では、あらゆるモノづくりの現場で「半導体」が欠かせない存在となっています。
この節では、製造装置の制御、品質管理、IoT化などにおいて半導体がどのように活躍しているのかを解説します。
製造業と聞くと、金属加工や組立工程など、比較的“アナログ”な現場を思い浮かべるかもしれません。
しかし近年では、スマートファクトリー化の進展により、半導体が多くの領域で活用されるようになりました。
以下は、製造現場において半導体が果たしている主な役割です。
1.自動化・省人化に不可欠な「頭脳」
産業用ロボットや自動搬送装置、CNC工作機械などは、マイコン、FPGA、センサーICなどを組み込むことで高度な制御を実現しています。
・例:CNC旋盤は、内蔵されたプロセッサが軸制御・工具交換・加工精度の補正を自動化 ・例:AGV(無人搬送車)は、距離センサーやカメラからの情報をリアルタイムに処理
このように、機械に“判断力”を与えるのが半導体の役割です。
2.計測・モニタリングによる品質保証
製品の品質を安定化させるには、「見える化」が欠かせません。
温度、湿度、振動、電流値などをリアルタイムで監視することで、異常の早期発見や、工程のフィードバック制御が可能となります。
これに貢献しているのが、以下のような半導体デバイスです。
・センサIC(温度、圧力、加速度など)
・ADコンバータ・DAコンバータ(アナログ⇔デジタル変換)
・通信IC(データの有線・無線送信)
結果として、製造品質の安定化やトレーサビリティの確保につながります。
3.IoT・スマートファクトリーの実現
近年のトレンドとして、製造設備がネットワークで接続され、中央で一括管理される「スマートファクトリー」が加速しています。
これは、各設備に組み込まれたセンサーデバイスやマイコン、通信ICが、クラウドとつながってデータを送受信することで成り立っています。
・生産状況の遠隔モニタリング
・AIによる稼働最適化
・異常発生時のアラート通知
これらすべてに、半導体が欠かせません。
言い換えれば、「製造現場のデジタル化の根幹にあるのが半導体」なのです。
製造装置そのものも半導体製品
実は、金属加工機、プレス機、射出成形機などの製造装置にも多くの半導体が使われています。
・パワー半導体:モーターやアクチュエーターの高効率制御
・マイコン:装置の状態監視やユーザーインターフェース制御
・メモリ:加工条件や履歴データの記録
つまり、製造現場は「半導体でできた装置」によって動かされているといっても過言ではありません。
半導体製造現場の特徴と課題
半導体製造現場は、一般的な製造業とは異なる独自の特徴を持っています。
同時に、技術革新の激しさや高精度要求に起因する課題も多く存在します。
ここでは、半導体製造現場ならではの特徴と、直面している課題について詳しく解説します。
1.半導体製造現場の特徴
まずは、他の製造業と比べたときの半導体製造現場の独自性を見ていきましょう。
■超クリーン環境が必須
半導体製造では、ナノメートル(10億分の1メートル)レベルの微細構造を扱います。
そのため、空気中のわずかな塵(ダスト)1粒すら、製品不良の原因になります。
・クリーンルームクラス:ISOクラス1〜5(通常の空気の数千分の1の清浄度)
・作業者も全身を覆うクリーンスーツを着用
・製造装置も、外気と完全に遮断された密閉構造
このような徹底したクリーン管理が基本です。
■24時間365日稼働
半導体製造装置は、停止や再起動に膨大な時間とコストがかかります。
そのため、24時間365日ノンストップ稼働が基本です。
・シフト制で作業員を配置
・定期メンテナンスも極力ラインを止めずに実施
・生産ロス最小化のため、稼働率99%以上を目指す現場も
この過酷な稼働体制が、現場スタッフの高いプロフェッショナリズムを育んでいます。
■超微細加工と超高精度制御
10nm、5nmといった極微細プロセスでは、人間の目や感覚では到底確認できない領域を扱います。
・リソグラフィー(露光技術):EUV(極端紫外線)リソグラフィーを使用
・成膜技術:原子層単位で制御するALD(Atomic Layer Deposition)
・計測技術:原子間力顕微鏡(AFM)による表面検査
すべてが極限レベルの精度と再現性を要求されるため、装置も作業者も異常なほどの精密さを求められます。
■多品種・短納期化への対応
従来は大量生産が主流でしたが、近年はカスタム仕様や少量多品種の要望が増加しています。
・車載向け:高信頼・高耐久
・スマートフォン向け:小型・高集積
・IoTデバイス向け:超低消費電力
これにより、製造ラインの柔軟な切り替えや、工程間のリードタイム短縮が求められています。
2.半導体製造現場の課題
■装置・材料コストの高騰
EUV露光装置1台で数百億円、先端材料も1kg数百万円といった高額な設備・資材が必要になります。
・設備投資リスクの増大
・製品価格に対するコスト回収期間の長期化
このため、ROI(投資回収率)を厳しく管理する必要があります。
■技術進歩のスピードに追いつく難しさ
2〜3年ごとに新世代プロセスが登場するため、常に最新技術へのキャッチアップが求められます。
・新技術導入の教育・研修コスト
・技術者不足によるリソース逼迫
現場では、日々の改善活動だけでなく、未来技術への準備も並行して進める必要があります。
■環境負荷とサステナビリティ
半導体製造は、大量の電力・水・薬品を消費する産業でもあります。
・工場全体の電力使用量は都市レベル
・水リサイクルシステムの導入が必須
・温室効果ガス(GHG)排出規制への対応
こうした環境負荷を低減しながら、生産性を落とさずに製造を続ける取り組みが求められています。
■地政学リスクへの脆弱性
半導体は、国際的なサプライチェーンに大きく依存しています。
地政学的リスク(例:輸出規制、紛争、災害)によって、原材料や部材の供給が途絶する可能性も常に存在します。
これに備えて、
・サプライチェーン多元化
・在庫管理の最適化
・地域生産化(オンショアリング)
といったリスクヘッジ策が急務です。
半導体とDX
デジタル化が進む現代において、「半導体」と「DX(デジタルトランスフォーメーション)」は切っても切れない関係にあります。
ここでは、半導体がDXをどう支えているのか、そしてDXが半導体産業にもたらす影響について解説します。
1.半導体がDXを支える存在である理由
現代のDX推進には、「データの取得」「データの処理」「データの活用」という三つのフェーズがあります。
それぞれのフェーズで半導体が重要な役割を果たしています。
■データの取得:センサーとエッジデバイス
工場、物流、医療、農業、オフィスビルなど、あらゆる場所に設置されているセンサー。
これらは、温度、湿度、圧力、画像、音声など、リアルタイムで情報を収集します。
・センサーIC
・MEMSデバイス(微小電気機械システム)
これらデータを収集する最前線にあるのが、半導体製品です。
■データの処理:AIチップと高性能プロセッサ
取得した膨大なデータを、リアルタイムで処理するためには、強力な演算能力が必要です。
・GPU(グラフィックス・プロセッサ)
・TPU(Tensor Processing Unit:AI専用チップ)
・FPGA(プログラマブル半導体)
これらの演算デバイスも、すべて半導体技術の賜物です。
特に、ディープラーニング(深層学習)には大量の演算が必要であり、AI時代の到来によって高性能半導体の需要が爆発的に増加しています。
■データの活用:通信インフラとストレージ
データをネットワークでやり取りし、クラウドやオンプレミスのサーバーに保存するにも、半導体が不可欠です。
・通信チップ(5G/6Gモデム、Wi-Fi、Bluetooth)
・データセンター向けDRAM、SSD、HDDコントローラーIC
IoT社会、スマートシティ、コネクテッドカーといった新たなDX領域の広がりにより、通信・記憶用半導体の重要性も高まっています。
2.DXが半導体産業にもたらす変革
DXの進展は、半導体産業そのものにも大きな影響を及ぼしています。
ここでは、DXによる主な変化を紹介します。
■設計開発のデジタル化(EDAツールの進化)
従来、半導体設計は非常に手間のかかる作業でしたが、近年ではEDA(Electronic Design Automation)ツールの進化によって大幅に効率化されています。
・論理設計からレイアウト設計までを自動化
・シミュレーションによる不良率低減
・AIを活用した設計最適化
結果として、設計期間の短縮、開発コストの削減、製品リリースの高速化が実現しています。
■スマートファブ(スマート工場)の実現
半導体工場(ファブ)自体も、DXによって進化を遂げています。
・IoTセンサーで装置稼働状況を常時モニタリング
・生産データをクラウド管理し、AI解析で歩留まり向上
・自律型ロボットによるウエハ搬送の最適化
これにより、「止まらない工場、ムダのない工場、自己進化する工場」が現実のものとなりつつあります。
■サプライチェーンマネジメントの高度化
世界規模で半導体サプライチェーンが複雑化する中、デジタル技術を活用してリスク管理を高度化しています。
・在庫・物流のリアルタイムトラッキング
・AIによる需要予測と生産計画の自動立案
・ブロックチェーンによるトレーサビリティ向上
これにより、不測の事態にも迅速に対応できる体制が整えられつつあります。
3.未来に向けた展望
今後、DXの波はさらに加速し、半導体業界にも次のような変化が訪れるでしょう。
・量子コンピュータ向けデバイスの実用化
・ニューロモーフィックチップ(脳型コンピュータ)の普及
・超低消費電力・自己修復型半導体の研究開発
つまり、DXが進めば進むほど、半導体技術もまた進化を求められるのです。
半導体製品の部品加工の見積り依頼ならアスクへ
試作品や小ロットの加工も大歓迎!
特に手のひらサイズの部品製作を得意としています。
アスクなら、試作品のお見積もりが最短1時間で可能!!
お気軽にお問い合わせください。
試作全国対応!
簡単・最短1時間お見積り
他、ブログ記事もご覧ください♪
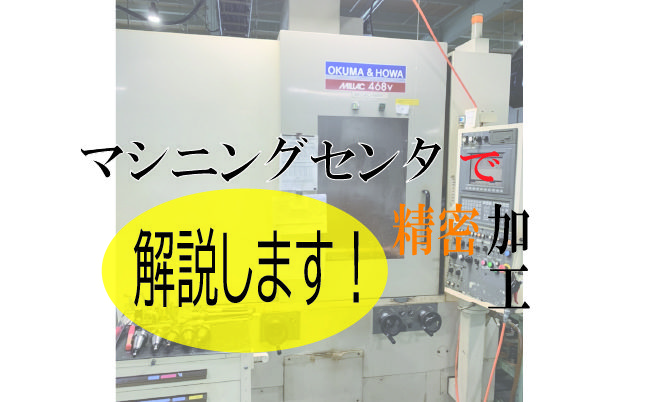
動画の投稿もしておりますので良ければご覧ください♪